Total Productive Maintenance (TPM) – Definition and Benefits
Manufacturing success hinges on consistency and productivity. Downtimes, delays, and product defects can completely erode profit margins and cost industrial manufacturers up to $50 billion annually. As a result, the responsibility falls on maintenance managers to discover and institute production processes that promote continuous improvement.
Below, we’ll explain how inventors improved maintenance activities through Total Productive Maintenance (TPM) to reduce downtime, product flaws, and stoppage.
- What is TPM Maintenance
- Defining the TPM Pillars
- OEE and the Six Big Losses
- TPM Examples
- Incorporating Additional TPM Activities
- TPM Maintenance and Connected Worker Software
What Is TPM?
TPM maintenance is a Japanese philosophy that focuses on improving equipment management and strives to achieve perfect production.
At its core, TPM emphasizes proactive thinking while including every team member in the production process. This helps identify and eliminate losses through root cause analysis. From there, perform reactive and preventative maintenance to create a working environment with higher productivity, uptime, and efficiency.
Defining the Traditional TPM Pillars
TPM maintenance is a philosophy at its core. However, it’s also a structured approach built on the 5S foundation. This outlines strictly ordered processes concerning the maintenance and handling of all relevant manufacturing equipment.
Understanding the 5S Foundation
Below are the five “S’s” included in the 5S foundation:
- Sort: Identify all needed equipment in the production process and eliminate any excess pieces
- Straighten: Reorganize remaining equipment to optimize productivity and improve equipment operation
- Shine: Thoroughly clean all equipment and work areas before instituting changes
- Standardize: Form strict standards about how to carry out the above three points
- Sustain: Ensure adherence to all standards by conducting routine inspections
The Eight TPM Pillars
Perched atop the 5S foundation are eight TPM pillars. Together, these frameworks support development, allowing organizations to enhance a proactive approach. The TPM pillars are:
- Autonomous maintenance
- Planned maintenance activity
- Quality maintenance
- Focused improvement
- Early equipment management
- Training and education
- Safety, health, and environment
- TPM in administration
- Incorporating
OEE and the Six Big Losses
Overall Equipment Effectiveness (OEE) is a calculation of manufacturing productivity, assigning it a numeric value to track and improve upon.
Introduction to OEE
TPM aims for 100% OEE, representing flawless production with no part defects, no downtime, and maximum production speed. OEE consists of three factors, each addressing a different style of productivity loss:
- Availability: Addresses complete stops in production, both planned and unplanned
- Performance: Addresses slow cycles and small stops
- Quality: Addresses part production to eliminate product defects
Benefits of Automated OEE Tracking
Although OEE tracking can be manual, using automation tools greatly boosts accuracy, tracks patterns, and shows real-time results.
Creating a “Best of the Best” OEE Goal
Setting goals to improve OEE, which requires tracking the “Best of the Best” OEE score, is essential. Managers must track daily metrics for availability, performance, and quality to get this score. Finally, multiplying the best results across each category will produce a target OEE score.
Understanding the Six Big Losses
Improving the OEE score hinges on eliminating six score losses, which include:
- Unplanned stops resulting in availability loss
- Setup and adjustments resulting in availability loss
- Small stops (typically less than five minutes) resulting in performance loss
- Slow-running equipment resulting in performance loss
- Production defects resulting in quality loss
- Reduced yield resulting in quality loss
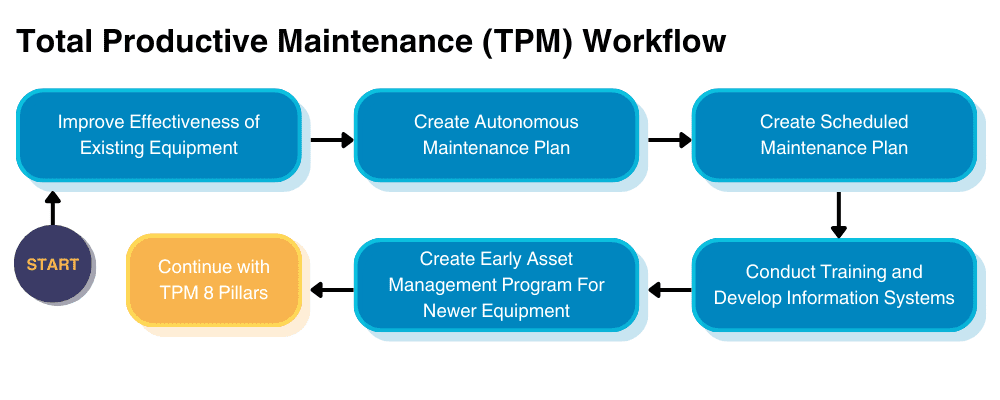
TPM Example
We’ve established the core concepts behind TPM. Now let’s see how it plays out in practice.
Step One – Identify Pilot Area
First, find what equipment you’ll include in the TPM program. This requires asking three questions:
- Which equipment is the easiest to improve?
- Which equipment is subject to bottlenecks?
- Which equipment causes the most problems?
Step #2 – Restore Equipment to Prime Operating Condition
After choosing the equipment, clean and repair it to ensure it can achieve 100% OEE. Then, maintenance management must create an automated maintenance program to implement recurring tasks and proper training for everyone involved.
Step #2 – Begin Measuring OEE
Measure vital metrics either manually or through automation to comprehensively track performance across the six big losses. Before making any adjustments, track metrics for at least two weeks to get a clear picture.
Step #4 – Identify Major Losses
After collecting enough data, identify the key areas of loss. Then, form a team to organize and define the leading causes. From there, develop the most effective solutions.
Step #5 – Roll Out Proactive Maintenance Techniques
Once the response team defines solutions, introduce the new maintenance techniques. Define maintenance intervals to reduce stop time and form a feedback system to determine the effectiveness of maintenance procedures.
Ideally, maintenance teams should conduct monthly audits to review all log entries and adjust maintenance tactics.
Incorporating Additional TPM Activities
Businesses must build a TPM roadmap to uniquely fit their needs. As such, consider introducing additional TPM activities as you eliminate losses in productivity.
Below are four additional TPM activities that go beyond the basic TPM approach. Introduce these while identifying further areas for improvement:
- Quality maintenance
- Early equipment management
- Safety, health, and environmental measures
- TPM in administration as opposed to just in operational workflows
Sustainable Improvement
Locking in continuous improvement takes more than reactive measures. To achieve long-term success, it is important to think long-term. To achieve long-term success, it is important to think ahead.
One way to do this is by using the 5S foundation and eight pillars of TPM improvement. These tools can help set expectations, assign responsibilities, enhance work environments, and offer growth opportunities for maintenance teams. Identifying and rewarding behavior to be replicated is crucial.
However, to keep up with the fast-paced nature of modern manufacturing, implementing TPM demands modern solutions.
TPM Maintenance and Connected Worker Solutions
Routine maintenance requires solutions that allow maintenance teams to set plans, track data, and adjust schedules in a centralized way. Therefore, digitizing work instructions is critical for unlocking growth and efficiency. Parsable’s Connected Worker® is a mobile-first solution that connects frontline workers to boost productivity, enhance safety, and improve the quality of work and output.
Take a digital tour of our Connected Worker® software and discover how it improves reaction times and compliance visibility to gain insight across your organization.
Ready to revolutionize your operational workflows? Experience the power of Parsable’s Connected Worker® software firsthand. Schedule a demo today and discover how our solution can streamline your operations by digitizing your frontline.