What is Preventative Maintenance?
Downtime, systems failure, and lapsed operations can completely wreck a business’s productivity and revenues. Reports show that unplanned downtime costs businesses over $50 billion annually.
However, businesses can employ tactics to reduce the likelihood of such vulnerabilities. For example, preventive maintenance helps leverage data and technical expertise to fix issues and stabilize operational vulnerabilities before they unravel into catastrophes. This article explains various approaches to preventive maintenance and how they are useful for lowering operational costs, growing productivity, and improving workplace safety.
- Types of Preventative Maintenance
- When is Preventative Maintenance Required
- Advantages of Preventative Maintenance
- Disadvantages Preventative Maintenance
- Examples of Preventative Maintenance
- Preventive Maintenance vs. Corrective Maintenance
- Preventive Maintenance vs. Predictive Maintenance
- Preventative Maintenance FAQs
What are the Types of Preventive Maintenance?
Preventive maintenance is a multi-pronged approach. Ultimately, choosing the right methods depends on your unique operation. But when done right, certain studies show it can yield over a 500% ROI.
There isn’t one type of maintenance that’s superior to others. Businesses must select the type that aligns with the specifics of their facilities. Then, operation managers can work alongside technicians to coordinate a preventive maintenance program. These plans must include clear work orders and accurate assessments of the company’s needs and infrastructure.
Mandatory / Non-Mandatory Tasks
When defining tasks, prioritization is key. Anyone responsible for handling preventive maintenance must consider all equipment and systems. From there, split all maintenance needs into mandatory and nonmandatory tasks.
So what’s the difference?
Preventive maintenance analyzes each piece of equipment included in facility operations. So, if equipment is vital to workflow production or involves safety, that’s a mandatory task. Here, mandatory means no excuses: You must carry out any maintenance according to schedule.
On the other hand, non-mandatory maintenance refers to any task that falls outside of the mandatory criteria. Remember, non-mandatory tasks aren’t unimportant. Rather, they can’t ever take priority over mandatory tasks. This means they may experience delays if necessary.
Pyramiding / Non-Pyramiding Tasks
Pyramiding is a strategic, time-based tactic used to create a preventive maintenance plan. Essentially, it’s a scheduling system that states that if a certain task overlaps with another maintenance task on the schedule, it will be canceled or rescheduled. On the other hand, a non-pyramiding structure keeps tasks siloed and tracked individually.
Inspection and Task-Oriented Tasks
Inspections are a crucial part of preventative maintenance, but they don’t necessarily entail maintenance all the time. Inspections are scheduled checkups on key equipment to identify maintenance needs. Then, if the inspection reveals an issue, it’s added as a formal maintenance task. These checkups must occur routinely, as they are critical for catching issues before they grow into larger problems and cause long-term damage.
Additionally, there are task-oriented preventive maintenance tasks, which are scheduled repairs or tune-ups that are built into the inspection. Creating a calendar for these smaller tasks helps ease the burden on technicians by setting expectations and workload via a planned maintenance schedule.
- The system or process is crucial to operational success
- The system or equipment poses a safety hazard to front-line workers
- The system can be rethought or fixed to help cut down on overhead expenses or boost productivity
Ultimately, there’s no mandate for preventive maintenance so long as equipment and facilities meet regulatory and legal standards. However, preventive maintenance is crucial to enhance efficiency.
Why Is it Important?
Preventive maintenance isn’t simply useful because it addresses equipment malfunctions through regular maintenance and inspections. A well-thought-out preventive maintenance program builds a philosophy of responsibility and meticulous care for all key processes. Over the long haul, this significantly reduces the likelihood of major supply chain issues, downtime, and system errors.
Advantages
The benefits of preventive maintenance are manifold, allowing businesses to lock in smoother operations, improve employee satisfaction, and tap into benefits necessary for growing and maintaining a well-oiled, profitable operation.
1. Improved Safety
In any business, safety comes first, so safety concerns can bring entire operations to a halt. However, preventive maintenance establishes oversight and accountability for all equipment and facilities. That way, you can build plans to track safety metrics, ensuring everything is up to standard.
Safety audits should be a regular habit. Using a great digital solution, such as Parsable’s Connected Worker® app, is a great way to put safety first. These solutions provide management with visibility into critical safety and compliance-related data points. It also increases collaboration between operations managers and front-line workers, so safety issues can be addressed immediately.
2. Greater Equipment Lifespan
Well-maintained equipment always outlasts neglected equipment. Preventive maintenance is a great way to improve mean time between failure (MTBF) rates and avoid breakdowns. It’s a philosophical approach that understands machines as objects requiring routine care. With a good plan and the right tools, managers can lock in maintenance predictions that address mechanical needs over a system’s entire lifespan.
3. Improved Productivity
Reducing downtime, boosting safety, and keeping equipment running efficiently all lead to one thing: Better productivity. Preventive maintenance keeps equipment running and helps you track KPIs like overall equipment effectiveness (OEE).
4. Reduced Costs
All maintenance comes with a price tag. However, emergency repairs are much more costly than preventive repairs. Preventive maintenance reduces the likelihood of emergency repairs by carefully tracking all equipment and eradicating issues before they result in large-scale disruption.
5. Reduced Energy Consumption
The US Department of Energy Conducted a study showing that preventive maintenance can reduce energy costs by up to 18%.
With the right tools, operations managers can track energy consumption across all equipment and identify areas of heavy waste. With this insight, they can quickly address issues, resulting in massive savings and more sustainable workflows.
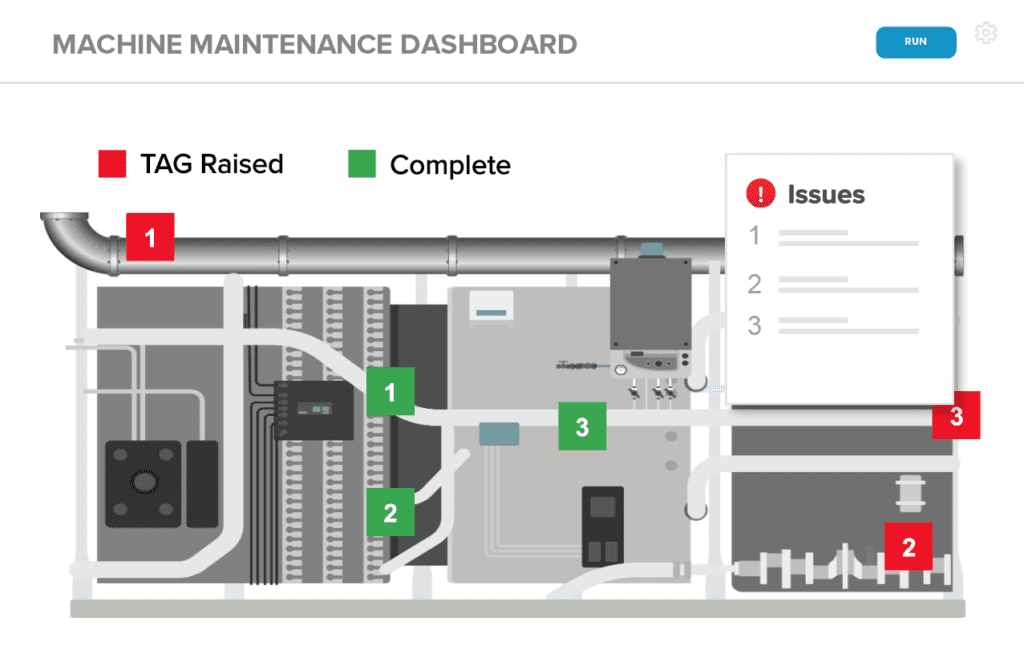
Disadvantages
Preventive maintenance offers many benefits. But when considering how to approach it for your workflow, it’s critical to weigh the disadvantages as well.
1. Budget Constraints
Although preventive maintenance reduces costs over the long term, building a plan and carrying out maintenance tasks requires upfront investment. This can be a struggle for organizations working on shoestring budgets.
2. Additional Resources Required
On top of financial investment, preventive maintenance demands a significant amount of expertise and personnel to perform inspections, hire technicians, and carry out maintenance tasks.
3. Time-Consuming
One of the primary reasons organizations fail to institute proper preventive maintenance is the time it takes to scour an entire operation to account for all equipment and identify which tasks are mandatory. Scheduling, asset intervention, and organizing personnel also take time.
4. Organizational Difficulties
Kicking off a preventive maintenance program from the ground up is no small task. It requires energy, labor, and money, all of which drain on organizational efficiency. Ultimately, this shouldn’t prevent organizations from adopting preventive maintenance, but it’s a major effort that requires many assets and technicians to do it right.
Examples of Preventive Maintenance
Whether you work in industrial manufacturing or SaaS, preventive maintenance is useful across many industries.
Manufacturing
Manufacturing relies heavily on successful preventive maintenance. For example, preventive maintenance can be used on systems like conveyor belts or rollbars to perform routine tasks like lubrication, bearing replacement, and addressing general wear and tear. Likewise, in the transportation of goods, routine oil, brake, and safety checks are necessary to avoid supply chain breakdowns.
Software
Every day, software maintenance becomes a larger threat. Cybercriminals are constantly looking to exploit dilapidated digital infrastructure to run attacks and steal data. This demands preventive maintenance for software systems, networks, and security, such as identifying weak code and issuing patches before hackers discover entry points.
What Is the Difference Between Preventive Maintenance and Corrective Maintenance?
Preventive maintenance focuses on planning ahead and creating schedules that consider where existing equipment may fail. Corrective maintenance deals with issues as they arise, meaning it involves waiting for equipment to break down or malfunction.
What Is the Difference Between Preventive Maintenance and Predictive Maintenance?
When comparing preventive maintenance vs predictive maintenance, it’s important to understand that they pursue the same goals: To lower costs and increase productivity. However, predictive maintenance incorporates tools that leverage machine learning to help determine ideal schedules for maintenance. Preventive maintenance plans maintenance tasks through human observations, expertise, OEM manuals, and other means.
Related Frequently Asked Questions (FAQs)
What Is Corrective Maintenance?
Corrective maintenance applies to systems or tools that are already broken. Here, the goal is to identify issues and restore equipment as soon as possible. This is also known as reactive maintenance.
What Is Predictive Maintenance?
Predictive maintenance employs advanced analytics, data assets, and artificial intelligence to estimate when a piece of equipment is likely to break down. Predictive maintenance aims to reduce the risk of unforeseen breakdown, which boosts productivity by eliminating downtime.
What Is the Difference Between Corrective, Preventive, and Predictive Maintenance?
Corrective maintenance strictly deals with issues after they’ve occurred, meaning it reacts to an existing problem. Conversely, preventive and predictive maintenance seek to solve issues ahead of time by performing routine maintenance before any breakdowns. However, preventive and predictive maintenance differ in how they’re carried out. Preventive maintenance involves building a schedule based on observation or adhering to resources like the original equipment manufacturer (OEM) manual.
Ready to revolutionize your operational workflows? Experience the power of Parsable’s Connected Worker® software firsthand. Schedule a demo today and discover how our solution can streamline your operations by digitizing your frontline.