Keep Manufacturing Production Running During the Pandemic’s E-Commerce Boost
A version of this article was originally published in engineering.com.
The holiday season is approaching and bringing an end to a year like no other. The SARS-CoV-2 virus has cost thousands of lives and been a major disruption in many ways. Unlike previous years, 2020 is seeing an unprecedented boost in e-commerce because of lockdowns resulting from the ongoing COVID-19 pandemic.
The situation has left manufacturing workers at high risk in terms of safety. With COVID-19 cases already on the rise, there is a greater likelihood for workers to catch the virus during colder weather when faced with increased workloads during the e-commerce surge.
Connected Worker® by Parsable offers technology that can help keep manufacturing workers safe while ensuring efficiency amidst a landscape of changing demands. The digital transformation tool serves to streamline processes, enforce social distancing, and reduce errors through improvements in training and protocols.
Engineering.com had the opportunity to speak with Jaime Urquidi, Regional Vice President and CPG Lead at Parsable, about how the app could be used to create a safe work environment. Urquidi has over 20 years of experience in helping companies implement large-scale operational improvements, and has held various leadership positions at Coca-Cola, Procter & Gamble, Mars, Unilever and Walmart.
Engineering.com: Could you give us a company profile of Parsable, including its history and which industries it serves?
Jaime Urquidi: Parsable was founded seven years ago under the idea of keeping workers safe. One of the founders was very cognizant of worker safety. He was aware that in the oil business – in offshore oil rigs, for instance – anything that a person didn’t do correctly could have huge implications. Even when you had tighter standards, accidents still happened.
They started exploring how workers received instructions and executed their tasks under these conditions. I’m stressing execution because it is the key aspect upon which Parsable is built.
After visiting an oil rig for a couple of months, the founders gained an understanding of how the operators would work in their environment. Then they began creating an app, which initially started with a Google Glass application. However, at the time, the founders learned that the technology was not fit for that environment as it was not mature enough and lacked system stability.
They veered into a mobile app platform with a back end and a front end. You would execute the work on the app, and then on the back end – on the web-based part of the platform – you would design, define and measure work.
From there, we started evolving and we now serve four specific verticals. Our main vertical is consumer packaged goods (CPG). We have paper and packaging, which is another industry that’s highly interrelated with CPG because a lot of them are suppliers for CPG companies. We also have our foot in oil and gas, of course, because that’s where we started. We deal with auto and aero industries as well.
What role does Parsable play in reducing human error and ensuring worker safety?
In safety, every second counts. Every time people are working, they’re either making a right decision or a not-so-good one. When different, not-so-perfect decisions add up, they increase risk until an accident happens. That’s where processes and safety management systems come in, to help people do their work correctly every time and keep the probability of an accident as low as possible.
At Parsable, we’re empowering workers with modern digital tools by delivering them the best instructions possible in the easiest way for them to execute.
Using our platform, workers know what to do, and then we track how they’re doing it by using time stamps and author stamps to monitor their work execution.
We can then start observing trends on unsafe behaviors such as skipping steps when carrying out different procedures, for convenience’s sake. With those things, if you don’t have clear data with enough granularity, it’s very hard to draw conclusions and actually change your procedures to fit the work. That’s where Parsable does its magic, because we provide organizations with that level of granularity so they can understand where their lack of process adherence is coming from. Is it coming from the process itself? Is it coming from the system? Or is it coming from the people? And then you can manage that, instead of blaming it on the operator, which is the easiest and probably not the fairest thing to do.
What issues are stemming from an e-commerce surge during the pandemic?
One of the biggest challenges in supply chain is that logistics bear a high cost. The more granular and specific you get in logistics, the higher the cost. For example, when you’re transporting a lot of widgets in a train, it’s very convenient and cost-effective. But when you’re traveling with one sweatshirt that needs to go to a specific address, the cost of that unit increases.
These factors pressure the cost and revenue of different companies. Part of the challenge we had in Walmart Mexico, for instance, was how to logistically make e-commerce as profitable and effective as brick-and-mortar with the economies of scale.
Now with the current situation in the world, with COVID-19 putting everybody in lockdown, it has changed the way people buy things and has accelerated e-commerce. Companies are trying to leverage their brick-and-mortar supply chains for making stores with 33higher reach to consumption points, and then using their stores as distribution centers. There are a lot of different variables at play, with the lack of brick-and-mortar or capacity within the warehousing and distribution centers, and with the constraints on logistics and the availability of transportation to serve this complex supply chain.
What challenges is the manufacturing world facing in terms of safety during COVID-19?
There are restrictions on social distancing regarding the availability of people and keeping them safe. If you have somebody that gets sick, you need to lock down, sanitize everything, and stop your operation for a number of hours.
Another significant challenge for distribution chains is the rotation of operators within this environment. Companies are trying to put systems in place that enable them to ramp up the workers that they do get. Operators must learn quickly and work as efficiently as possible while staying safe.
Companies are using Parsable to assign workers to different areas in order to comply with social distancing. Parsable is also being utilized to enable communication when doing distant shift handovers amidst staggered entry and departure times, where personal interaction is missing.
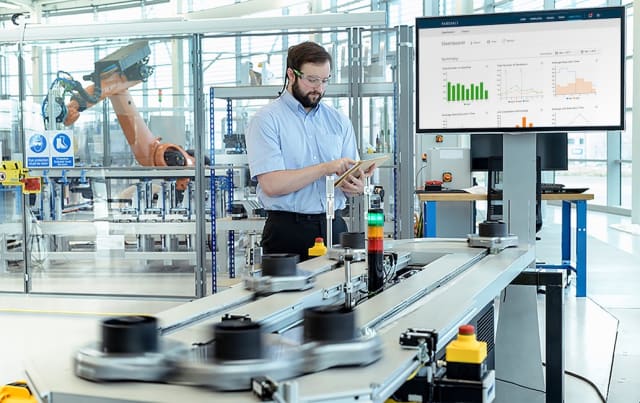
Connected Worker can help alleviate the variables that are in control of operations in order to cope with the surge in e-commerce demand.
How can Parsable help in the drive for efficiency?
Digital tools like Connected Worker enable organizations to conduct better, faster training as opposed to receiving instructions by reading manuals.
Picture a cell phone that has all your instructions, where you’re looking at quick start videos that tell you step-by-step how to carry out a procedure. First of all, it’s more entertaining; people tend to be visual and learn better by watching videos. Paper is dead – it has limited capabilities.
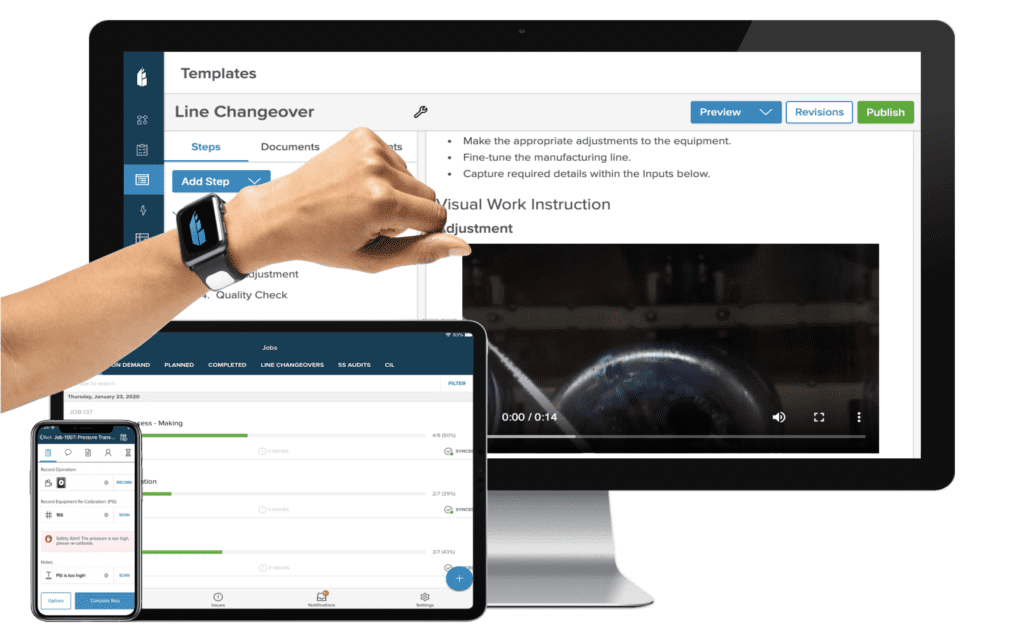
Furthermore, through Connected Worker Platforms, an update to the system can be deployed immediately throughout the organization so that everybody has the latest and greatest. We’re starting to shrink continuous improvement cycles, and changes can be implemented faster.
One thing that often happens is that even if there’s an improvement to a system, it’s hard for people to change their ways. So another benefit of using Parsable is to monitor if operators are executing updated procedures, to confirm that you’re making updates stick. These changes and capabilities start getting embedded into organizations.
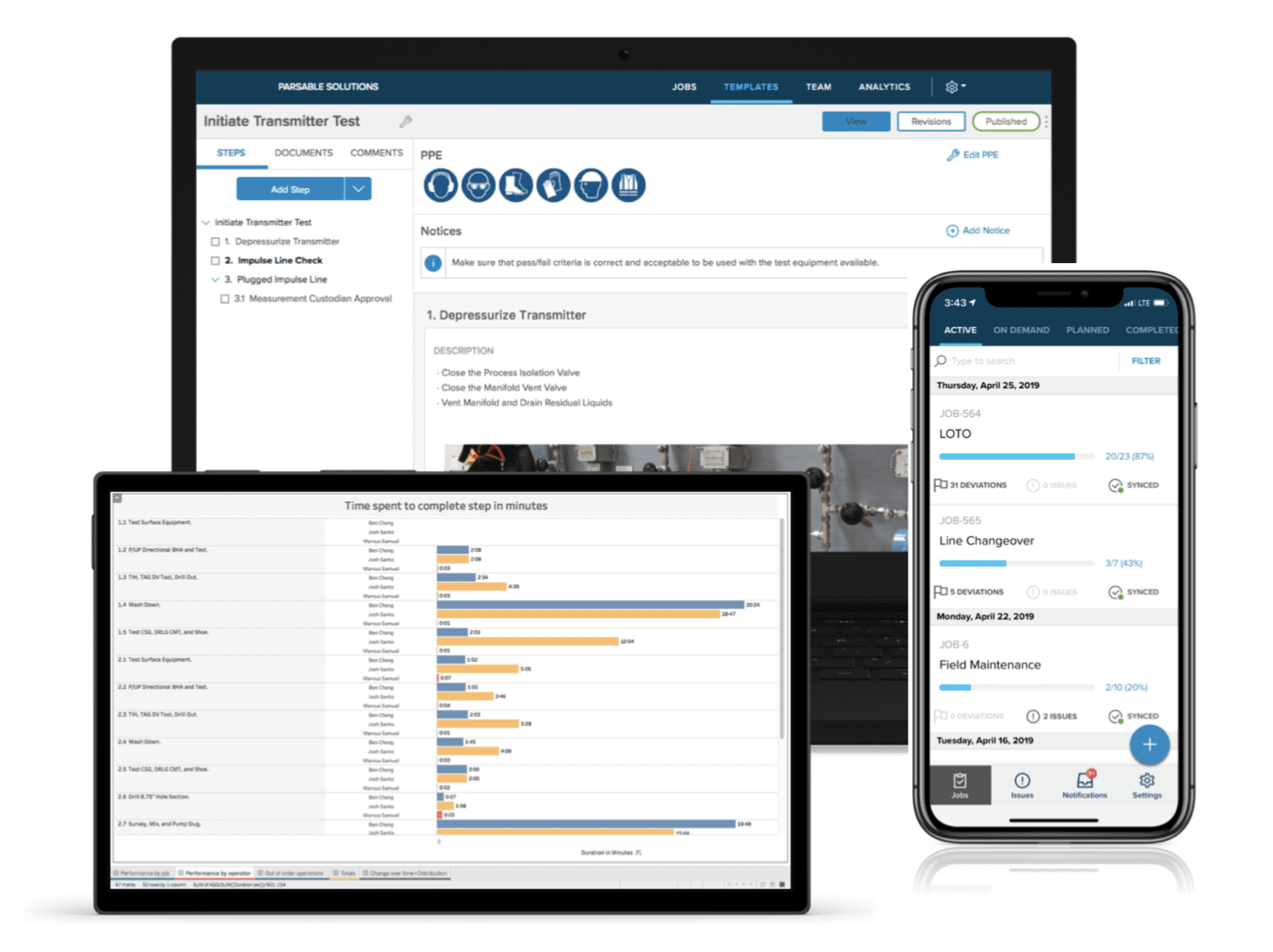
Operators themselves can track their performance and optimize efficiency, without needing their boss to tell them what to do. Most people go into work wanting to do the best job possible, and Parsable helps workers gain ownership of their own process and eliminate waste that comes from inconsistencies, non-compliance, non-conformances or errors.
Tell us about Parsable’s key features.
Apart from the execution of instructions, one key feature is the compliance and completeness of data.
Not all data is inputted by the operator. We have open APIs, where we can connect to a machine that records a temperature, for example. You can have a sensor or IoT device sending information into Parsable. Part of your data may be coming from your SAP or ERP. Everything ends up in the hands of the operator, and they can make decisions based on that information.
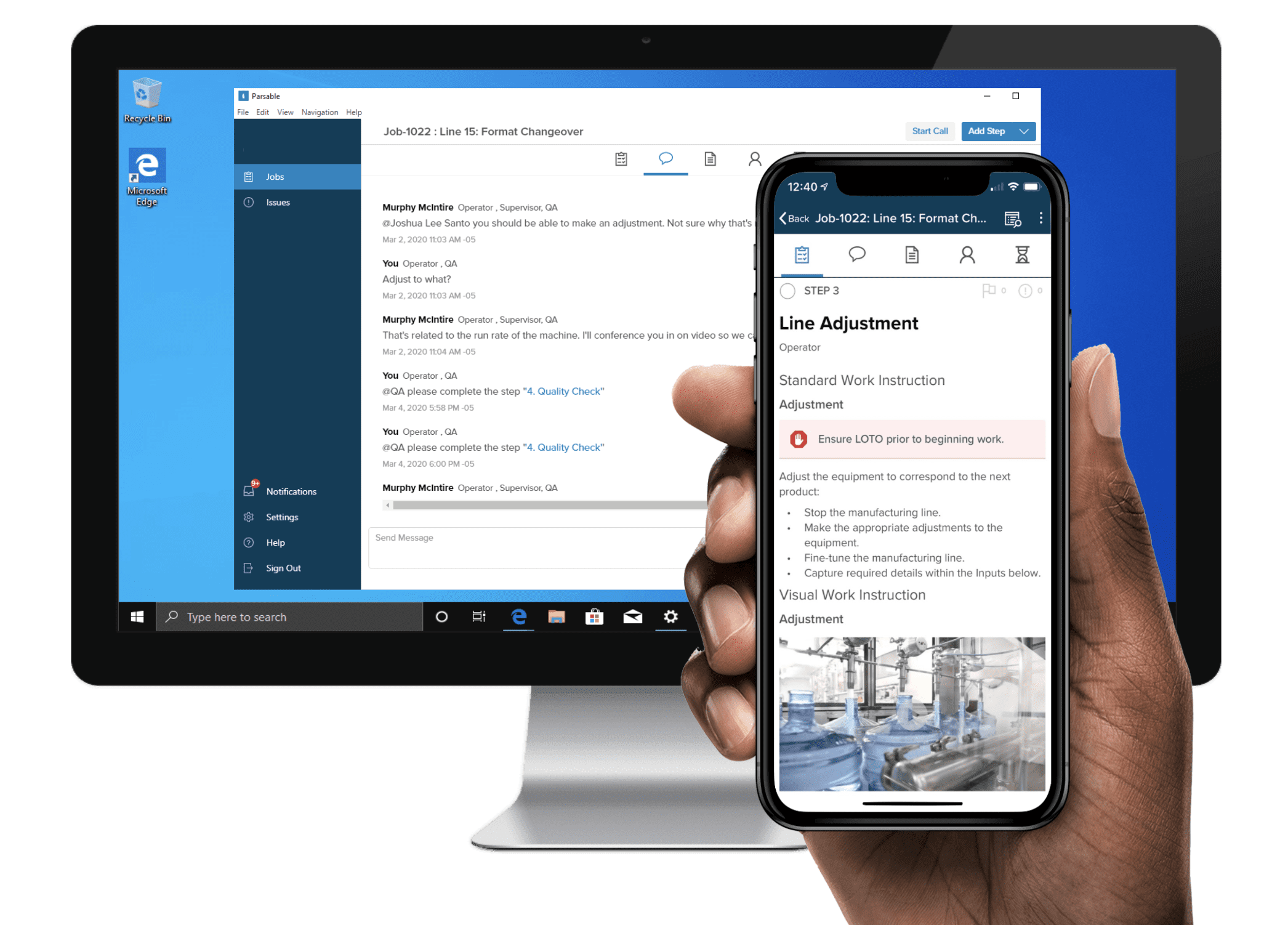
You can also have workflows around certain data points where, for instance, if you have three temperature readings that are out of spec, that can trigger a job within Parsable.
Preventative maintenance can additionally be embedded into the system – so that instead of people forgetting to perform maintenance, the system would give you alerts. Autonomous maintenance practices help reduce the number of breakdowns, and are also an enabler for implementing continuous improvement models such as world class manufacturing (WCM) and total productive maintenance (TPM) best practices.
As we evolve in the maturity of procedures and the ecosystem in which they’re executed, we become that single pane of glass where the operator interacts with legacy systems in the background. There are a lot of solutions for different things. There are great solutions for safety, but they just do safety. There are great solutions for training, but they just do training. With Parsable, complexity is eliminated when everything comes together, and the way that workers interact with technology is simplified.
What’s the process involved in helping your customers kick off their digital transformation efforts?
Our platform is a no-code platform, and you can author a procedure in between 10 and 20 minutes.
If a person knows how to use Word and PowerPoint, it’s super simple. You open your browser, open your job, create your template, and then start specifying the way you want the input to be sent. I can choose to have data entered as a list. I can put an announcement at one step. If the temperature is above a certain limit, I can have a warning that says something along with lines of “Watch out. This is out of specification.” I can arrange for the operator to not be able to carry out the next step until their current one is completed with evidence. I could set a requirement for them to take a barcode scan here. I could ask them to take a picture and annotate it.
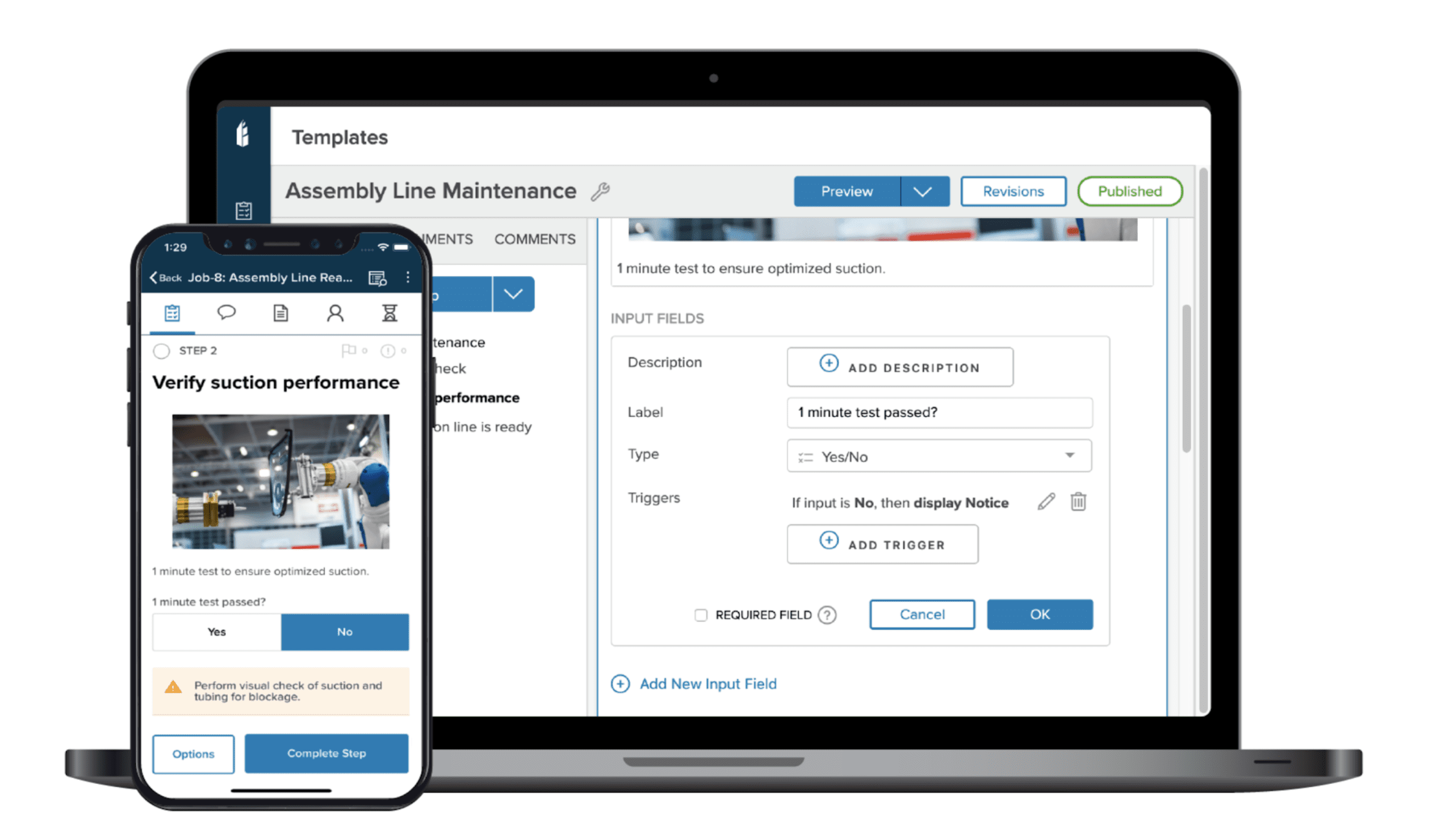
We have a very simple, straightforward platform. When we engage with a customer, we conduct a training session on authoring and execution. Within a week, they’re already executing work live and getting insight from their processes.
One of our customers was the world’s biggest bakery. In a week and a half, they created a safety observation process in 12 languages, all on their own, after a little bit of initial guidance from us.
From your experience, how has COVID-19 affected manufacturing in 2020? Has Parsable been able to use the opportunity to help many businesses?
It’s been an interesting year for everybody. I think we’re all still adapting.
First of all, we manufacture products to address market needs, but customer requirements have changed since we went into lockdown. For instance, an ex-colleague of mine who runs a very large bubble gum factory in Mexico was telling me that people don’t eat that much gum anymore because they’re at home. The company is under a lot of cost pressures because of having lost 30 percent of its volume. He’s thinking of using Parsable to increase his productivity and reduce his waste so he can go back to his costs before the volume plummeted.
Another example is the beer industry that has lost all its on-premises revenue – the beer they used to sell during concerts and sports events. People are drinking the same amount of beer, perhaps even more. But the margin that you make as a company from the beer that you sell in Walmart, versus the beer that you sell at an event, is way higher. So there’s a lot of cost pressure and profit pressure in these companies, and they’re starting to use Parsable as a way to become more efficient while having the same resources.
Then there’s the beauty company that’s found a way to put sanitizer into shampoo bottles. Time is of the essence, so how does Parsable help you through all that uncertainty, and do it fast? Simply buying and setting up a new machine for bottling hand sanitizer is almost out of the question because it’s super expensive. After you get away from COVID, you won’t need that much hand sanitizer anymore – but you never know. So then, what is the most cost-effective and time-effective way to change?
First off, you can change your procedures and processes. You can either adapt them, or create new procedures quickly. You can ramp up your people. With digital tools, you can deliver information to the front lines effectively, while ensuring safety and quality.
When you put a data point on a sheet of paper, it dies and it takes a lot of time and effort to revive it. With Parsable, you keep it alive and send it wherever it’s needed. The time-to-value from the actual generation of the data point to the decision-making gets streamlined. The concepts of simplicity, data availability and flexibility have been resonating with our customers. This has been very good for us, and has accelerated the adoption of Parsable.
In your opinion, what’s the future of connected worker platforms?
When working with prospective clients, I always tell them to picture the guys from Microsoft who were selling Excel 30 or 40 years ago. You’d be sitting at a desk with a big calculator, and a sales guy would come in saying, “Hey, you need Excel. It’s a super calculator!” People would say, “No I don’t need that – I can do my pluses and minuses here.” The salesperson would say, “You can be more efficient.”
Now, your computer better have Excel or Google Sheets. It’s considered basic for getting things done. That’s where I see connected work going – as something that’s just part of the everyday, because we’re changing people’s approach to work.
Lawrence Whittle, the CEO of Parsable, always talks about how industries and workers have been underserved by technology. I totally relate to that. You currently live in a digital world, with your Instagram, Snapchat, cell phone and so on. Then you go into the plant and you’re back to 1960 where you’re working in binders.
Times are changing. We’re now bringing these two worlds together to make manufacturing sexy from that technology perspective. That’s why the Connected Worker market that we have at Parsable is so big and so promising. I think it’s time to help the vast majority of people with technology to do their work in a better way.