What Is First Time Quality (FTQ)? Benefits and Tips
Product defects can result in downtime, waste, and diminished customer satisfaction, severely eroding the profit margins of any production process. However, many continuous improvement processes, metrics, and principles help eliminate defects. One of these principles is a concept known as first time quality (FTQ).
Below, learn the definition of first time quality, its benefits, how it improves quality management over time, and three simple steps to improve your company’s FTQ.
- First Time Quality in Manufacturing
- What Is Total Quality Management?
- Benefits of FTQ
- Tips for Cultivating First Time Quality
- First Time Quality and Connected Worker® Software
First Time Quality in Manufacturing
First time quality is a metric that tracks how successful manufacturing companies are at reducing the ratio of defective products coming off the production line.
Say you operate a canned food company. If your production run yields 1,000 canned goods per hour, but an average of 50 fail to meet quality standards, your FTQ is 95%. To understand why 5% of your products are defective requires familiarity with the concept of total quality management.
What Is Total Quality Management?
Total quality management evaluates the production process as a system of parts that work holistically. By examining each part of the process individually, owners and production managers can identify specific root causes of inefficiency and waste. Once they have identified the weak parts of the production process, companies can implement solutions to improve the quality and quantity of the output and boost customer satisfaction.
Benefits of FTQ
Although FTQ is only one element of total quality management, learning to improve it yields significant benefits.
It Helps To Idenity Areas in Need of Improvement
Viewing defective materials and products as an inevitability is a colossal mistake. Companies should analyze even small fractions of waste and defects for improvement opportunities. FTQ is a valuable tool that breaks down the production process and pinpoints specific causes of waste, such as a machine settings issue or inadequately trained employees.
It Leads to Faster Resolution
FTQ is all about gradual improvement. At first, identifying and solving production problems might take a long time. However, as managers develop and implement routine processes, like periodic machine maintenance, and create proper documentation around those processes, they intuitively discover solutions to problems more quickly.
It Can Measure Process Efficiency
To increase profit margins, it is crucial to understand how much time and money go into each product. FTQ analysis paints a clear picture of how many items you have to sell versus how many go to waste, and it offers insights into opportunities for improvement. Additionally, FTQ analysis enables companies to calculate precisely how much they spend on materials and labor.
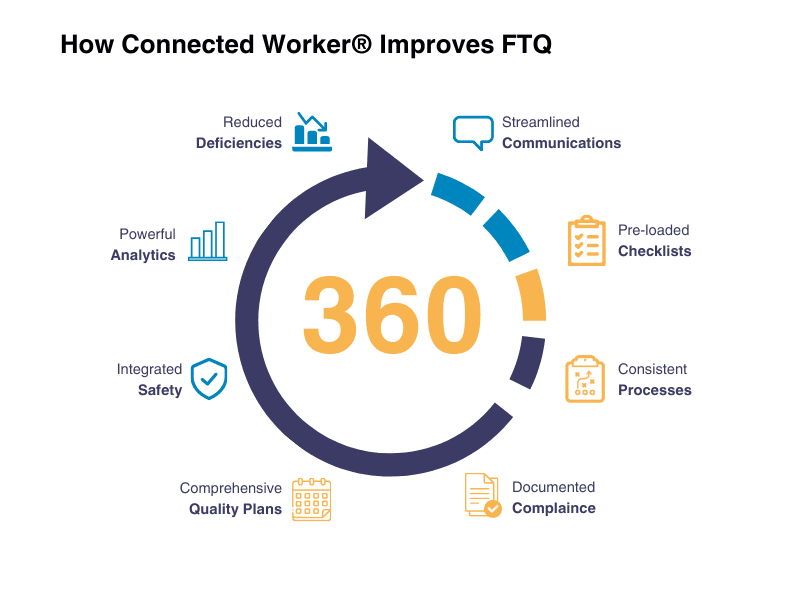
Tips for Cultivating First Time Quality
Measuring FTQ at multiple stages provides the clearest vision of your production run’s efficiency. Below are a few steps to ensure you’re improving quality in a way that will result in a higher FTQ metric over time.
Step 1: Inspect Materials
Using faulty materials dooms production processes from the beginning.
Avoiding defective materials begins with a thorough inspection of all raw materials and a rigorous cross-check of quality standards with your suppliers. Examining every batch of raw goods upon delivery and identifying any issues before you begin production gives you the opportunity to change suppliers or negotiate different quality standards.
Step 2: Practice Machine and Equipment Upkeep
Each machine, employee, and processing stage represents a point at which products can fall below the quality standard. Routinely scheduled inspections for all machinery involved in production (even new or high-tech equipment) is critical to lowering downtime and stoppages and increasing FTQ.
Step 3: Implement Process Documentation
Ensuring alignment with the philosophy of continuous improvement involves documenting each process. For example, by recording FTQ variability under different personnel, you may discover the FTQ rate could significantly improve if certain employees receive additional training.
First Time Quality and Connected Worker® Software
Investing in software that tracks and reports critical FTQ-specific data points is one of the best ways to consistently improve quality standards.
Connected Worker® is a comprehensive platform that digitizes processes across operations, including managing IoT equipment sensors, which records operations data necessary for raising FTQ.
Our technology allows manufacturers to digitize their processes and visualize the data in, in real-time, in a central location. This helps increase productivity, reduce waste reduction, and enhances safety and quality.
Parsable enables your front-line workers with the tools and peace of mind to get their jobs done safely and efficiently.
Ready to revolutionize your operational workflows? Experience the power of Parsable’s Connected Worker® software firsthand and discover how our solution can streamline your operations by digitizing your frontline.