Paperless Manufacturing: The Hidden ROI
It shouldn’t come as a surprise that the role of paper in our daily lives is rapidly diminishing. However, many manufacturers still use pen and paper to record what’s happening on the shop floor. According to a Parsable study released in March 2021, 79% of factory workers still rely on paper-based documentation and checklists to track work and communicate with their team.
Failing to adopt paperless manufacturing is problematic for a number of reasons, but primarily because it leads to waste, it’s costly, and the data collected often isn’t timely or accurate because it’s prone to human error.
On top of that, manual paper reporting isn’t lean. It’s a workaround that was implemented because the technology needed to support the ideal transfer of information between people and systems wasn’t available at the time. And if you don’t equip your team with the right tools, you can’t be surprised when you fail – fail to increase throughput, pass audits and recruit the next generation of workers.
Chances are you’ve got frontline workers on your factory floor writing down information on pieces of paper, every hour or maybe at the end of every shift. This data is then transferred to a whiteboard or production board and then entered into a spreadsheet, like Excel. An operations or plant manager likely performs calculations in the spreadsheet, creating a report that is distributed to certain team members. This is a very manual, time-ridden process and is riddled with the potential for error.
What if that entire process didn’t take up an extra time? What if there was a way to transfer information between people and systems on the frontlines?
When you look at the dynamic nature of manufacturing operations and all the stakeholders involved that need to collaborate and share information successfully, the benefits of a paperless environment extend beyond the shop floor. As manufacturers continually look at ways to cut costs and operate more efficiently, the easy answer to that is: going paperless.
You can eliminate a portion of your overhead costs, enhance productivity and help out the environment. Going paperless may seem like a daunting task, but it’s easier to implement than you think.
Paperwork Isn’t Just Painful – It’s Costly
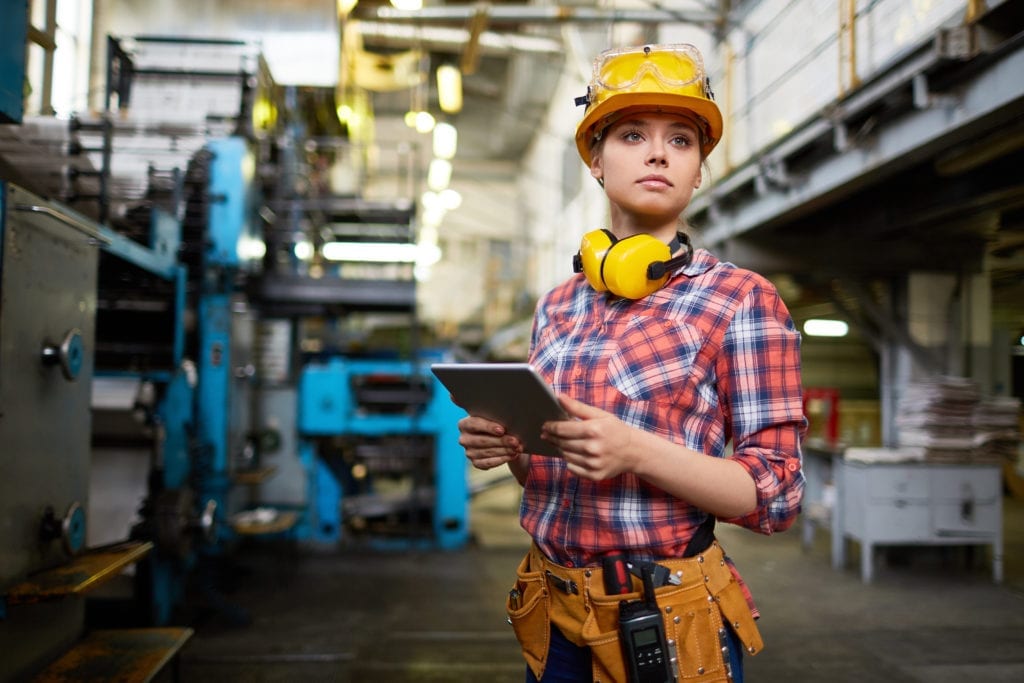
Paperwork isn’t just an inconvenience; it’s actually pretty costly. And, when you examine the impact of using paper as your main way of transferring information from person-to-person or person-to-system, you’ll find there are a lot of inefficiencies:
- Lost Information – If you write something down on paper, it still doesn’t exist until it’s input into your system of record. What if that sheet of paper gets lost, someone accidentally throws it away or something gets spilled on it? The information collected is effectively useless.
- Decreased Accountability – Manufacturers often run into the issue of pencil whipping when using paper – it’s when someone documents that a task or work was completed when in actuality it wasn’t. Without the right digital tools in place to get the visibility needed to understand accountability or lack thereof, pencil whipping will continue to occur.
- Increased Miscommunication – Say a frontline worker raises an issue and due to other inefficiencies in the workflow, and that information gets lost. Perhaps there’s a severe wait time. Or, it might be the case that no one follows up with the person that raised the issue. They’re then less likely to flag problems in the future knowing their voice wasn’t heard. What kind of impact does that have on worker morale?
- Inefficient Processes – The workflows that paper-based procedures, forms, audits, checklists and inspections rely on have a lot of gaps and opportunities for breakdown. And there are a lot of manual processes to support that. Tasks are often completed in isolation and siloed from subsequent activities that need to occur. Ultimately, from a lean manufacturing perspective, this leads to waste, whether that’s excess motion, transport, wait times or more.
- Irrelevant Data – When you record information on paper, you’re not actually capturing data. It takes a lot of effort to turn that information documented on paper and put it into a system record for reporting. The shelf life of data is relatively short, and its value can expire before you even do something with it.
- Wasted Time – What’s it like to have too much paperwork? Aggregating all the forms, checklists, audits and inspections that are created and performed is a painstaking process. But, then you’ll have to take that information, enter it into an Excel spreadsheet and be able to create a report or dashboard. How long does all this take? And think of all the time wasted along the way.
These inefficiencies aren’t just inconvenient; they negatively impact your manufacturing operations. Time is wasted on slow, manual paper-based processes. As a result, this directly impacts the time it takes to solve defects, hazards and issues. It increases risk – risk of unplanned stoppages, unplanned downtime, safety incidents and quality defects.
Using paper impacts your overall operations, impacting throughput, first pass yield (FPY), uptime, lost time frequency rate (LTFR) and much more. Learn how to achieve visibility, traceability and accountability in manufacturing.
The ROI on Paperless Manufacturing
What are the benefits and savings you can expect from a paperless factory, as you eliminate redundancies, waste and time to market? Each of the areas below can’t be accomplished due to inherent inefficiencies, which ultimately affects your bottom line.
Keep reading to find out how going paperless is beneficial to your manufacturing operations.
Faster Reporting Means Faster Response
Connected worker technology connects frontline workers to the people, information, systems and machines to improve productivity, quality and safety. It allows for a deeper layer of insights that informs next steps within a work process, identifies patterns and predicts outcomes – ultimately driving continuous improvement.
One of the keys to your success as a plant or operations manager is fully understanding the manufacturing data that’s collected. In a paperless environment, collecting and analyzing data are a lot easier. With connected work, you can improve reporting and get the data you need to analyze trends. Your team captures critical data points as they complete their work, which empowers you (as a manager) to react much faster to safety, quality and performance trends. You’ll have less delays between when an issue, like unplanned downtime of a machine (check our these interesting stats on downtime), is reported and when it’s handled.
By automating the handoff of data and information from the frontline to business critical systems and management dashboards, you spend less time on compiling reports and more time improving operations. This will help you make sure at the end of the day that you’re producing at an optimal level, your team is safe, and the quality of your product meets the required specifications.
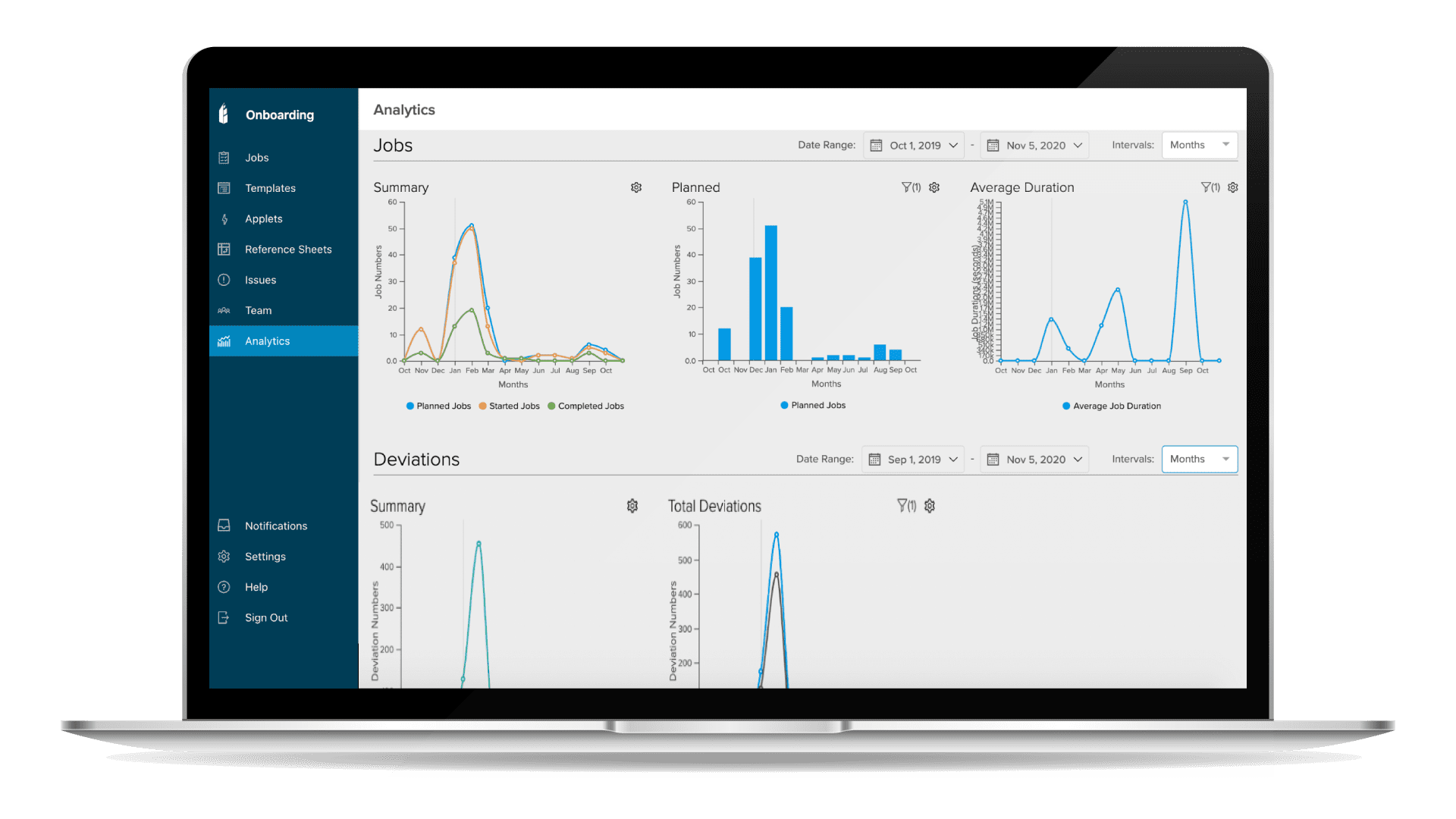
Tap Into True Cycle Times
Your true cycle time and your actual cycle time are probably different.
It can be difficult to accurately gauge the true cycle for a part from initial production of the item until it’s completed. You know what your constants are – the rate at which the machines were built to produce the part or product. But there’s more to producing a part than just what the machine is doing.
There’s the setup of the different machines on the line for the run, changeover activities between one product and another, and autonomous maintenance activities that can impact output. Realizing true cycle times and producing at the ideal run rate depends on the tasks that operators, or mechanics, perform every single day. In a paper-based environment, the only way to factor this variable into your true cycle time equation is to look at the paper trail, the recorded dates and times by your team. But again, that information may not always be accurate.
With connected work, the data behind human activity is easily accessible. Every time an action is taken, a mobile app can log granular data points like who did what, when and how – which are critical for understanding the “why” of the run. The data enables you to put together comprehensive time studies for critical activities that help you uncover opportunities to improve everyday processes in impactful and sustainable ways.
This approach has enabled manufacturers to identify specific training needs based on trends in performance, opportunities to improve workflows, and common obstacles impacting performance. Previously, the only way to get insights like these was to host a workshop in which internal teams or even consultants would meticulously observe workers, noting every task and obstacle seen – not a very efficient or accurate process at all.
By understanding and factoring in the human impact on production, you will get a more accurate view into true cycle times, which further enables you to make your lean operating goals a reality.
This allows you to better estimate your expected finish dates for cycles and ultimately you can analyze areas that need improvement to help reduce overall cycle times – because you have access to all this incredible data.
Decrease in Waste
Waste in manufacturing is also known as “Muda,” which is the Japanese word that means wastefulness, uselessness and futility. It’s easy to understand by now how paper is wasteful, and reducing your paper footprint is the first step in cutting waste and adopting a more lean approach.
In addition to waste from paper, many manufacturers are faced with wasted goods on a daily basis. Companies have quality checks and systems in place to ensure the products that leave their facility meet a certain specification and that there’s consistency in quality. But, oftentimes the quality checks built into the system rely on documentation and revisions to those documents. When you’re living in a paper-based environment, mistakes happen and incorrect revisions or quality specifications get recorded. The result is waste.
In a paperless environment, you can prevent these errors from happening in the first place. Connected work helps your organization both in terms of work quality and end-product quality. And by capturing data about how work is performed on the frontlines and you can dynamically update standard operating procedures (SOPs), you’re able to proactively maintain and deploy quality initiatives across your entire manufacturing organization.
By digitizing and cueing up specific steps in an SOP, quality becomes consistent across teams and sites every time, and enables more up-to-date documentation that’s easily referenceable. This is particularly important to all team members to ensure proper training and quality assurance information is digitally accessible. Digitized SOPs can be centrally maintained, revisions to work instructions can be made on the fly, then quickly rolled out across all sites. The result: better training, higher quality results and a reduction in scrap.
Paperless Manufacturing and the Role of Connected Work
The need for a paperless environment is a big step for many manufacturers that are set in old ways – but it can’t be ignored any longer. Companies that refuse to embrace a digital environment risk falling behind. In the March Parsable study, nearly three-quarters of frontline workers (72%) expressed no concerns about using digital tools in the workplace; they want access to digital technology to best perform in their jobs, and companies that don’t close the digital gap will risk losing talent.
Why continue analyzing handwritten notes, standing in front of a whiteboard or looking at Excel spreadsheets to make sense of what’s happening on your shop floor? Getting rid of your paper trail eliminates waste, non-value added time and potential errors that constantly occur in your manufacturing operations. It provides you with the potential to improve operational excellence and tap into your most powerful asset today – human workers. They are the change agents that will drive continuous improvement and collaboration in your paperless manufacturing environment.
We have everything you need to make going digital easy. Parsable provides a simplified approach to digitizing procedures for higher productivity and operational efficiency. Take your first step today.