In Executing Industry 4.0, Machines are Easy… It’s the Humans that are Hard
The Parsable team just returned from presenting and demoing our Mobile Collaboration and Workflow solution at the McKinsey launch of a Digital Capability Center in Chicago. This new center offers members the opportunity to learn state-of-the-art digital manufacturing by interacting with a factory that uses the absolute latest digital technology. The Chicago center is 1 of 4 around the world and has a short history compared to others.
Some have counted out US manufacturing, but this event made it clear that there is a ton going on in the US and underscored that now is the time for a significant capability renewal. As one attendee told me, “Europe was forced to move to more automated processes some time ago, as labor is relatively expensive.” The US approach of resting on some of our manufacturing laurels made complete business sense in an era where labor was relatively cheap. This metric is clearly now changing.
Another countervailing force is also leading us to Industry 4.0. As societies become more affluent, they desire a wider degree of goods and services. If this desire was plotted on a bell curve, Cuba would just be entering that curve, China would just be reaching the first quartile, and the US and Europe might be somewhere in the third quartile, with very demanding consumers ever hungry for unique products. For years, economists and industry prognosticators have talked about the opportunity to serve the long tail – smaller and smaller segments of people with unique needs. With rare exception, this remained just hot air as the costs of doing so were prohibitive. Today with cost of computing power going through the floor, big data now a widely adopted approach, and automation refinements including automated LASER cutting and 3D printing (just to name two manufacturing advances), it now looks economically viable to serve the long tail and invent new business models to serve that desire. Automation is clearly impacting the retail end of virtually every business as juggernauts like Amazon begin experimenting with pharmaceutical delivery, wine sales, apparel manufacturing, and yes: grocery stores. The higher margin potential of serving the long tail may be the only way some traditional retailers survive. For manufacturing, this means wrestling with way more complexity. If you want to serve those who serve the long tail or serve the long tail directly, agility and the ability to change on a dime, will be required to meet fickle and ever-changing market demand.
While clearly humans working in commodity manufacturing today have a high potential of being automated away, making a larger variety of products for the long tail will not only require smart humans, it will require more of them. Why more you might ask? Well the pesky reality of manufacturing is that there is a real cost to changeovers. The more complex machines we field to produce a wider variety of goods, the more these machines need to be configured and the more opportunity there will be for these machines to break. We recently toured 15 CPG companies and almost every one of them wanted to murder their marketing departments as the number of line changeovers to create more variety in their offerings was killing them. The companies were, of course, all under strict controls to reduce labor costs, at the same time then needed a new class of worker to keep up with the complexity.
So now we seem to have an impossible equation: the rising cost of humans and the requirement for more sophisticated automation. Even if there were higher margins to be found, adjusting the two biggest expense lines at the same time could mean certain disaster for many companies.
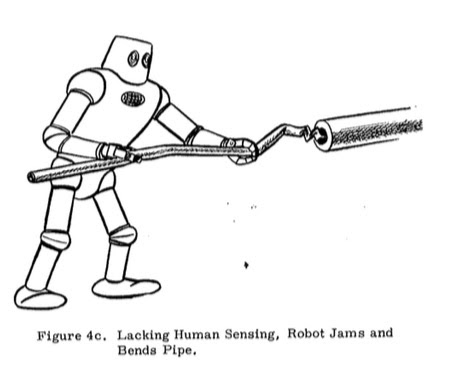
Something that everyone’s heard someone say at some point in their careers is,“The boss is coming, look busy.” Hopefully you haven’t heard that of late.
If we think about what the mantra needs to be for companies in the modern era of manufacturing, we are going to have to win more hearts and minds to make it:
“Industry 4.0 is coming, BE efficient.”
Clearly the fittest will survive, and by “fit,” we mean those who can systematically make machines AND humans more efficient.
Arguably since the Industrial Revolution, manufacturing, in general, has been on a mission to get rid of us pesky humans. We visited one consumer products company that had just 75 humans operating a 360,000 thousand square foot factory that ran 24/7. In most industries, we are now at the bare minimums to operate in current conditions let alone in a more complex long tail state. So why then is automating for a long tail world so anxiety-producing for so many industrial leaders? I would postulate that this is because working efficiently with humans is the complexity we’ve struggled with most. Robots, at least today, don’t ask why they should do something. They don’t need to be taught how, and they implicitly know when they should perform certain tasks because it is part of the machine code that feeds them. Humans…not so much. We want to understand the context of our work. We want to develop mastery, but yet we can forget the basics. And we only know when we are needed when somebody tells us so. We are complex, but we are also quite necessary in an Industry 4.0 World. Companies need our dexterity, our reason, our judgement, and our empathy to build the factories of the future, and it’s quite possible they need more of us than less of us. They need us to program sensitive machines, facilitate rapid changeovers, and address error conditions that haven’t even been conceived of yet.
So what is a manufacturer to do? If we revisit that impossible reality of rising plant and human cost, things might look pretty bleak. At Parsable, we’ve been thinking about this challenge for a long time. We believe it is possible to get incredible efficiency out of us humans and we’ve developed and have been deploying an approach to do just that. In the world that is becoming our reality right now, things get dramatically more complex. No one is going to remember what happened in that training course last week and “referring to the manual” will not only be impractical, but those manuals may be cost prohibitive to create in a constantly changing environment with infinite permutations.
Our Mobile Collaboration and Workflow platform is designed to allow human teams to perform at their level best in work environments with complex machines and operating practices. We do this by helping companies take static procedures and work instructions and make them dynamic work processes by putting just the right instruction into the hands of the right worker at the right time using the mobile tools people already know how to use. People now know in real time, what to do, when to do it, and how to do it, and if they have questions or challenges, they can communicate with each other in real time. And by executing these processes digitally, everything can be measured, analyzed, and perfected including the collaboration of humans and machines.
One thing from the manufacturing world will continue to be true in a more complex future: Machines will run until they break, and in general, they break because of variability in human work processes. Oops, forgot to do preventative maintenance. Crap, that servo was reassembled incorrectly. What if you could nearly eliminate variability in human interactions in the work environment and take on significantly more complexity?
Parsable can reduce the significant burden in moving to a digital Industry 4.0 world and future-proof your organization as you become significantly more complex.
As one senior leader at the McKinsey event commented, “You can’t plug a whole bunch of wires into machines and say you have a digital factory.” The humans have to be at the center of your strategy and they need to be efficient – now and tomorrow.