Grupo Bimbo: Achieving Next Level Occupational Safety Performance
COMPANY BACKGROUND
Grupo Bimbo S.A.B. de C.V. is a global Mexico-based CPG company and the largest bakery in the world, with approximately $15.6 billion in revenue and a presence in more than 30 countries.
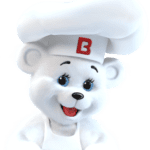
“Building a sustainable, highly productive and deeply humane company” is at the heart of its people and global company philosophy.
- Associate well-being drove the need to standardize the safety program across its Bimbo QSR business of 20 plants in 10 countries.
- Parsable was part of a holistic upgrade of Bimbo QSR’s occupational safety program.
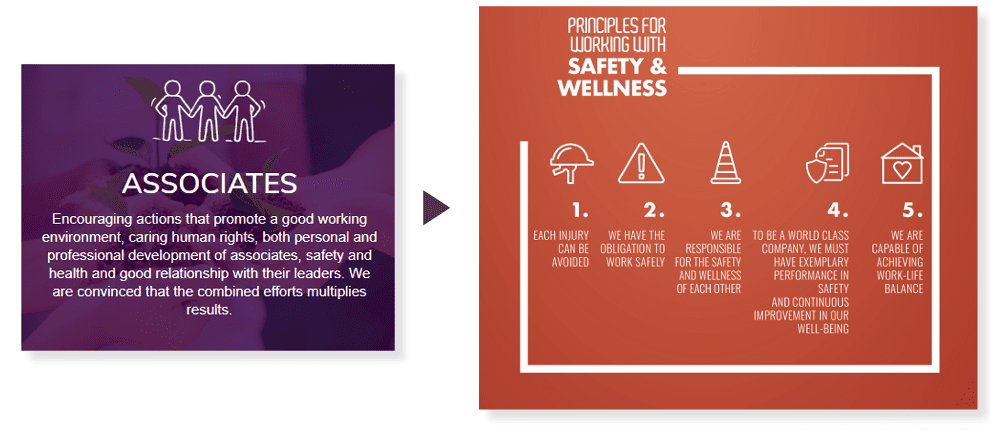
THE CHALLENGE OF STANDARDIZING SAFETY
Didier Moleres, VP of Global Operations, Gerardo Gordillo, Global Director of Human Resources, and Luz Alanis, Corporate Operations Manager, faced a lack of standardization across key components of Bimbo QSR’s safety program:
- Safety Incident Investigations used to identify potential hazards and the corrective actions necessary.
- Safety Observations used to identify and provide valuable feedback on the possible presence of unsafe actions or conditions in a work area.
- Good Safety Processes used to guide the collection and analysis of safety data across plants.
The team saw the opportunity to improve safety performance by implementing digital and standardized operational procedures across these components. Didier was familiar with Parsable Connected Worker® as it was already being used successfully in the Manufacturing side of the Bimbo QSR business in a project led by Luz Alanis, and wanted to put this technology to work for safety.
“An important part of our sustainability strategy is ‘Caring for Our People,’ and Parsable is one of the tools that helps us achieve better safety performance while supporting a good working environment.”
— Gerardo Gordillo, Global Director of HR
FROM CONCEPT TO IMPLEMENTATION IN 8 WEEKS
Faced with the need to implement a standardized safety program in a multilingual environment, Grupo Bimbo QSR conducted virtual workshops with native language speakers across 10 countries to ensure accurate translation of specific safety terminology in the new digital procedures.
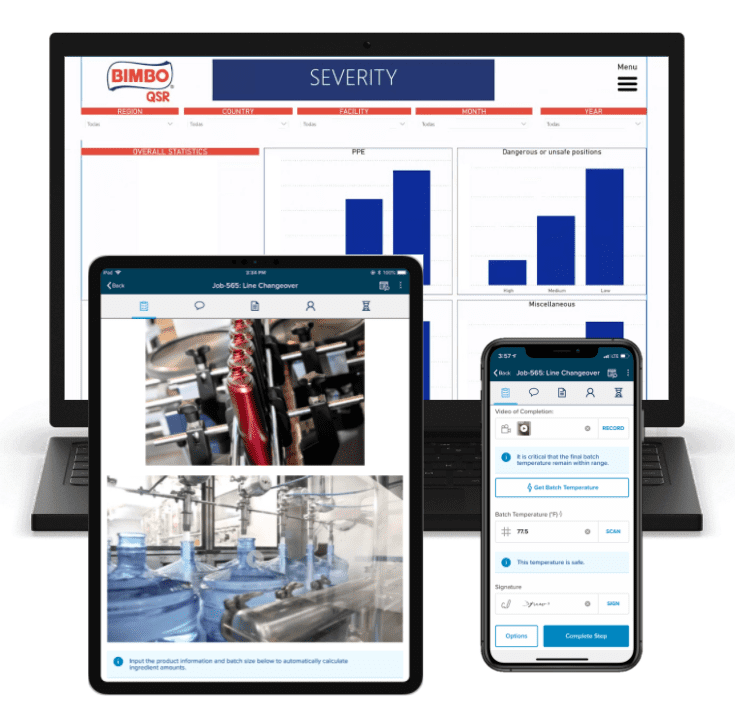
Best practices SOPs for conducting both Safety Incident Investigations and Safety Observations were standardized and digitized in Parsable, then distributed to bakeries around the world in 8 languages and within 8 weeks.
Data captured by associates on the bakery floor using Parsable-powered dashboards provided leadership with real-time visibility into safety performance at enterprise-wide, regional, and facility-specific levels.
“Digitizing safety program components using Parsable and analyzing the resulting data has enabled us to make changes proactively before workplace incidents happen.”
— Didier Moleres, VP of Global Operations
THE BENEFITS OF CONNECTED WORKERS AND DIGITIZED DATA
Better, More Efficient Safety Incident Investigation
Grupo Bimbo QSR used Parsable not only to support Safety Incident Investigations, but also for root cause analysis and action plan development and tracking.
- Embedded deadlines for associates to report an incident (24 hours), complete the investigation (72 hours), and complete the action plan, using a traffic light color system to track early, overdue, and late closures.
- Listed manufacturing location options in Parsable in the order found in the manufacturing process sequence to reduce the time spent scrolling through options.
More Value from Safety Observations
Grupo Bimbo QSR used Parsable to roll out the standardized Safety Observations procedure across the business, helping to:
- Better utilize data collected to distinguish between business-wide gaps or facility-specific issues.
- Unlock the power of safety observations in different safety categories sorted by region, county, facility, month, year.
Improved Safety Performance
Bimbo QSR’s improved safety performance is ultimately due to a number of factors supported by Parsable, including:
- Standardization of good safety processes.
- Collection and analysis of relevant data.
- Robust system of root cause analyses and completion of corrective actions.