The Missing Data That Prevents Companies From Creating the Factory of the Future
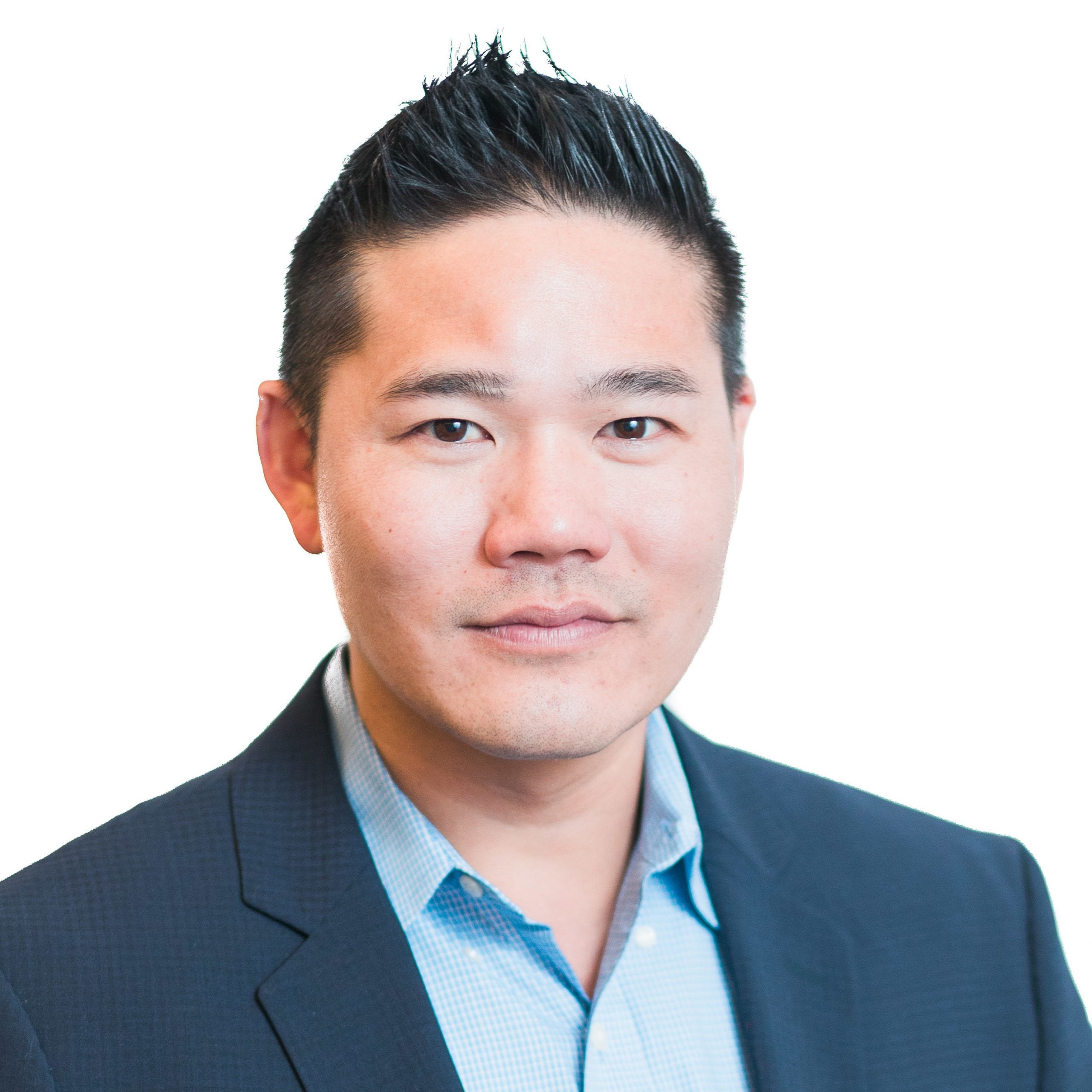
Featuring:
Ben Cheng, VP of Solutions and Partnerships at Parsable
In the industrial world, the prospect of a complete lights-out operation – with high levels of automation and line speeds in place – has been on the horizon for some time. But the reality is that even in highly automated environments, human oversight and intervention will remain very necessary.
In a new 20-minute “Data in Depth” podcast, Parsable’s own vice president of solutions and partnerships, Ben Cheng, chats with Mountain Point president and co-founder, Andrew Rieser, about why humans will always have a place on the operational frontlines, and how data – if done right – can unlock new levels of productivity, quality and safety.
There was no disagreement that creating this new “factory of the future” will take more than analyzing data from equipment, systems and processes; it’ll take a deep understanding of the tacit, human knowledge sourced from the generations of work performed before.
The discussion covered three main themes:
A Pragmatic Approach to Industry 4.0
Despite all the conversations around the factory of the future and going lights out, the reality is that manufacturers need to break down what digital transformation actually means to their organizations, and be pragmatic about what they can realistically take on and secure quick ROI.
For example, the concept of an intelligent, enterprise-class Internet of Things (IoT) ecosystem that can accurately predict downtime is great, but getting there, in reality, takes a long time. Another approach – one that’s much easier to deploy and has a faster time to value – might be to optimize human-led procedures on the frontlines by digitizing their previously paper-based processes in order to increase uptime.
‘O’ and ‘X’ Data
Much of the investment in digital transformation today is in collecting operational data, aka “O” data. (Look no further than the Salesforce acquisition of Tableau for $15.3 billion and Google’s acquisition of Looker for $2.6 billion.) There are lots of data sources out there within manufacturing that provide operational data telling us what is happening on the factory floor or out in the field, from enterprise resource planning (ERP) systems, to IoT, to product lifecycle management (PLM) solutions.
What “O” data doesn’t give us are those insights into why or how the “what” was achieved.
Experiential data, or “X” data, gives us the why and how behind performance. Examples of “X” data can be employees’ personal, institutional knowledge, whose deep work experiences inform and shape a specific procedure or step order, ultimately resulting in the “O” data you see. Unfortunately, “X” data is often not captured nor digitized, resulting in unreliable “O” data as well as huge data gaps in your operations.
Why ‘X’ Data is Important to Industrial Companies
Imagine not only understanding the operational performance of your workforce – like when a job starts and ends, or the size of a batch – but seeing multimedia verification of batch quality per worker with detailed metadata about the work performed, such as micro step duration with notes as to why they performed steps out of order or maneuvered equipment a specific way.
Additionally, with a continual shift in worker demographics where Baby Boomers and Generation Xers are retiring out, companies are also facing a loss in tacit knowledge because their retiring workforce is taking their years of experience with them.
“X” data is how leadership can capture that tacit knowledge to inform standard operating procedures and best practices to train the new millennial workforce, allowing organizations to also ultimately cut costs by hiring for potential instead of experience.
Now, with your “O” data and “X” data working together, your factory of the future becomes much more achievable. By knowing what happened, how it happened and why, you can make better-informed business decisions to improve productivity, quality and safety across the entire value chain.
For more detailed insights on how the right approach to data can transform your operations, listen to the full 20-minute “Data in Depth” podcast.