Silgan PFC Achieves Better Quality and Increased Efficiency at Lower Costs with Parsable
Silgan PFC Achieves Better Quality and Increased Efficiency at Lower Costs with Parsable
Silgan Plastic Food Containers (PFC) is a global leader in producing high-barrier plastic packaging for long shelf-life, ambient, microwaveable, convenience foods. Silgan PFC supplies high-quality, innovative products to some of the world’s most recognizable brands.
The Challenge
Though Silgan PFC has built itself into an industry leader with gold-standard products, there have been challenges. It was difficult to find out about and manage issues or incomplete activities. Documentation happened entirely on paper, creating a lack of transparency into who did (or didn’t do) what, when, or how that was impacting operational results. Handing over activities and responsibilities was not easy especially when someone was out of the office. When teams missed critical tasks, taking the necessary steps to address the issue was challenging. Additionally, Silgan was required to conduct one major audit and several smaller ones each year, but finding the required documentation amid an opaque paper filing system made the process difficult and time consuming.
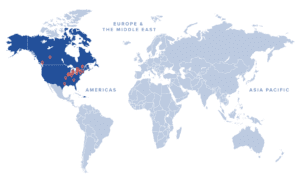
Silgan Custom Containers Plant Map
The Solution
Knowing that there was more that could be done to ensure optimal product quality, increase frontline visibility, and keep employees safe, Silgan PFC enlisted the services of Parsable. Digital Transformation was top of mind for leadership who saw it as a way to address internal needs like standardizing operations and external needs like keeping pace with competitors. As a result, Silgan implemented Parsable across quality, production, safety, maintenance, and other functional areas to tackle inefficiencies across routine processes like quality checks, line profile, preventive maintenance, forklift inspections, perimeter checks, and incoming receipt forms. As a result of working with Parsable’s product and people, Silgan was able to revolutionize how frontline work gets done through:
- Consolidation of all information into one single-source-of-truth system
- Faster, higher-quality handoffs of information between departments
- Streamlined reporting as a result of simplified audits
- Digital traceability and new levels of accountability for employees and managers
- New data points for monitoring equipment trends to make corrections as necessary
- Increased collaboration and visibility across safety, quality, production, and more.
Silgan has seen tangible improvements to business operations since partnering with Parsable. Silgan achieved a 20% reduction in audit times and a 10% increase to first-pass yield. By rapidly iterating standard preventive maintenance routines, Silgan was able to catch more errors and address redundancy, decreasing downtime and positively impacting throughput. Silgan also saved thousands of dollars in supply chain costs with enhanced accountability measures. By switching from a paper-based system to a digital single-source-of-truth system, Silgan achieved a 10% increase in labor efficiency due to quick and easy access to critical information, like records and documentation, right when needed.
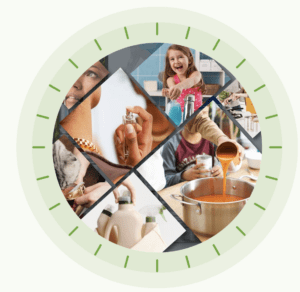
“We are always looking for more ways to use Parsable in our daily operations to make things streamlined and more efficient. The system is easy to use, even for those unfamiliar with tablets. The information is at your fingertips with customer-designed dashboards to chart critical data points for quick, daily review. It’s scalable with nearly unlimited possibilities for many jobs and use cases. Anytime an employee wants something tracked, or we want a new check implemented, we all immediately ask, ‘Can Parsable help us?’”
– Christina Stage, Plant Manager at Silgan’s Fort Smith, Arkansas
Asked if it was more than Parsable’s product that provided value to the team at Silgan, Christina highlighted the people of Parsable.
“The Parsable team has a great understanding of the industry challenges plant managers, in particular, want to solve. They’re professional, available, and willing to help find a resolution for anything new we would like the system to do for us.”
– Christina Stage, Plant Manager at Silgan’s Fort Smith, Arkansas