Global Dairy Manufacturer improves Quality and Safety with insights from Parsable
COMPANY BACKGROUND
As one of the largest dairy manufacturers in the world, this company produces a variety of products including milk, juice, cream, cheese, yogurt and butter. A billion-dollar company with close to 38,000 employees, this leading manufacturer has plants and distribution centers throughout the U.S., Mexico, Brazil and Central America.

THE CHALLENGE
The company is on a mission to create the world’s best dairy products. As a fast-growing CPG brand, it faced hurdles in scaling its operations to meet the growing demand. Outdated procedures and processes led to inconsistent data capture, impacting operational productivity, quality and employee safety.
This company’s largest site produces different types of drinkable yogurts. For every batch of finished product, samples are sent to the quality lab for microbiology and physico-chemical testing. All lab results were recorded on paper and created large binders of data, which were then manually entered into SAP every 24 hours, leaving room for human
error. The data reporting process took anywhere from seven to 30 days to uncover trends or identify if the production line was complying with quality standards – way too long for a dairy product.
Another challenge the company faced was that a single safety inspector would walk around a production facility to conduct safety rounds and create Safety Behavior Observations (SBOs). These reports were filled out in an inconsistent manner and would sometimes get lost. The lack of reliable SBO data resulted in considerable safety insurance premium costs.
THE SOLUTION
• Instead of relying on a 6-inch binder and paper-based reporting, the team has digitized its quality analysis using Parsable.
• Workers are able to open the application on a mobile device and begin capturing data in real-time.
• With Parsable, data went from being processed and put into dashboards in seven to 30 days, to synchronized data every 24 hours with no data recapture.
• Safety checks have been transformed from static paperbased procedures into digital, interactive processes.
• If a worker identifies an unsafe condition or bad safety practice, they can receive in-the-moment training within the app-based work instructions, and identify improvements to make the operation safer.
THE RESULTS
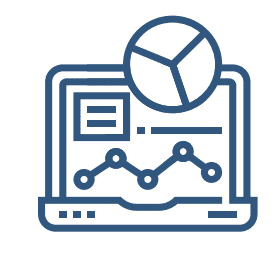
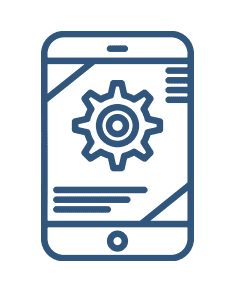
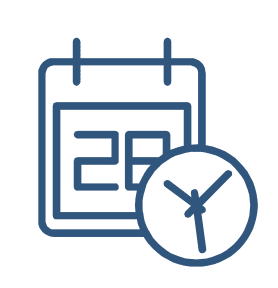