What is Quality 4.0 and How It Improves Manufacturing
Data is everywhere and allows manufacturing companies to improve production processes dramatically. The issue, however, is this: Manufacturing companies struggle to implement tools to harvest and process it.
With the right datasets, companies can glean revolutionary insights to enhance efficiency, production time, safety, and customer satisfaction. But too often, businesses fail to use the emerging tools offered by data companies for critical analysis.
This is why Quality 4.0 exists, as it’s a strategic way to leverage modern capabilities. In this explanation, we will discuss the concept of Quality 4.0 strategy. This strategy utilizes new technologies to promote innovation and enhance productivity.
- What is Quality 4.0?
- The Evolution of Quality 4.0
- Establishing and Implementing Quality 4.0 Principles
- Quality 4.0 Enabled by Industry 4.0
- Quality 4.0 and Connected Workforce Software
- Quality 4.0 Value Propositions
- ASQ and BCG Quality 4.0 Study
What is Quality 4.0?
At a basic level, Quality 4.0 is a digital transformation process. It’s a mindset that encourages manufacturing companies to shed antiquated data collection methods by introducing more capable technology. Done correctly, the result of implementation is a strong culture of quality and continuous improvement.
The Evolution of Quality 4.0
The story of Quality 4.0 is long and winding. Even the name “Quality 4.0” implies the existence of Quality 1.0-3.0.
So, what came before? Experts outline the genealogy of these quality processes in separate phases, which are:
- Quality 1.0 (Prior to 1890): Manufacturing relied on water and steam power via crude machines. Here, we measured quality through physical inspection, and we prioritized production volume over quality.
- Quality 2.0 (1891-1940): Manufacturing processes adopted electrically powered machines, allowing companies to scale production. During this phase, quality improvements were connected to the quantity of production. Additionally, we implemented measures to guarantee product quality and safety.
- Quality 3.0 (1941-1995): A period defined by computer-powered machines and a decline in human labor, instead using information technology to instigate efficiency. In this phase, quality moved from sheer production to an emphasis on customer satisfaction and an organized approach to standardized processes.
That’s the past, which brings us to Quality 4.0. Quality 4.0 is evolving. Key principles include automating processes and using AI for machine learning.
At this point, quality is judged based on how well companies use digital quality management systems to build processes that can identify needs, self-regulate tasks, and solve errors independently and in real time. Human involvement in Quality 4.0 remains a core element, but now, human value comes via the ability to design and optimize production systems.
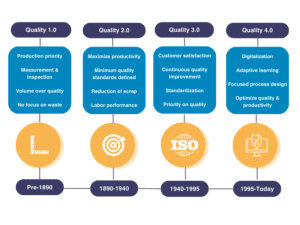
Establishing and Implementing Quality 4.0 Principles
It’s difficult to tell precisely where Quality 4.0 might end and the next phase will begin. But for now, the future of quality processes remains in the 4.0 phase.
Here are some of the core tenets of implementing Quality 4.0.
People
Yes, Quality 4.0 incorporates more technology than any prior stage. However, people remain at the center.
Now, providing people with the best tools for managing quality is imperative to success. As a result, a core Quality 4.0 principle is proper education and training so humans continue discovering disruptive ways to use 4.0 tech to increase productivity and quality.
Process
Automation began with physical manufacturing processes. Now, Quality 4.0 seeks to automate digital operations via cutting-edge digital solutions like chatbots, generative AI, and machine learning.
Technology
An advanced knowledge of the latest technologies is a critical piece to the Quality 4.0 puzzle. With technological advancement speeding up each year, Quality 4.0 relies on finding better, more effective ways to gather data. After processing raw data, management must incorporate findings to adjust and optimize manufacturing processes.
Remember, available tools evolve constantly. But as things stand, some of the necessary Quality 4.0 tools for manufacturing companies to understand include:
- Reality AR and Virtual Reality VR
- Augmented Reality AR
- Cloud Computing
- Big Data Infrastructure
- IoT Sensors and Platforms
- Language Processing and Chatbots
Quality 4.0 Enabled by Industry 4.0
Under the umbrella of Quality 4.0 is Industry 4.0.
Industry 4.0 explains how the core pillars and emerging tech in Quality 4.0 apply to manufacturing companies. When done correctly, the application lowers costs, eliminates waste, raises productivity, secures compliance, and satisfies customers.
Data
It’s said that striking the right data is the modern equivalent of striking oil.
The analogy may be comparing apples and oranges. However, it’s true data is vital when attempting to enshrine continuous improvement into existing workflows.
Industry 4.0 tracks data in real time to suggest and even automate quality improvements. Manufacturing companies accomplish this by using technology like IoT sensors, connected workforce management tools, and machine learning recommendation systems.
Analytics
Without insightful analytics, data collection is pointless.
For one, robust analytics enhances the capacity to solve existing issues. However, it grants the capacity to predict future needs, such as machine maintenance or supply chain issues. From there, managers can change production processes to eliminate vulnerabilities and lower downtime, product shortages, or safety concerns.
Connectivity
Collaboration and speedy communication are critical to modern production lines. Quality 4.0 tools, like cloud computing, open-source software, and AI-powered assistants, boosts connectivity, allowing employees and managers to communicate more effectively and issue real time feedback.
Scalability
A good Quality 4.0 tool is one that’s simple to scale. Digitized production management allows management to connect sources and centralize data and communication management, allowing conditions to scale much easier when necessary.
Management Systems
Prior to Quality 4.0, digital management relied on manual data entry and updates. Modern digital quality management systems allow manufacturing companies to automate key tasks like data processing, communication and security alerts, text analysis, and threat detection.
Compliance
Manufacturing companies must adhere to quality and safety standards, as well as growing environmental regulations. Quality 4.0 tools track data on key processes to monitor conditions and visualize patterns to understand when products or processes fall out of compliance.
Quality 4.0 and Connected Workforce Software
Connect worker software is a crucial tool to emerge from the Quality 4.0 era. A high-quality connected worker software offers a robust set of tools that centralize new tech and amplify the benefits of adopting Quality 4.0. For example, Parsable’s Connected Worker® is a sleek mobile app that connects users with IoT-enabled equipment to access critical, real-time data to influence strategic change.
Quality 4.0 Value Propositions
Manufacturers have been notoriously tardy when it comes to adopting the latest tech. It’s understandable, given that manufacturers use highly complicated processes and a vast machinery network. Introducing new tools is a genuine challenge.
However, the quality 4.0 value proposition touches on many vital factors critical to successful modern manufacturing processes:
- Supporting and prioritizing human intelligence over human labor
- Accelerating decision making
- Higher levels of transparency and compliance
- Greater ability to adapt and scale
- Successfully locating areas for continuous improvement and Kaizen principles
ASQ and BCG Quality 4.0 Study
Although Quality 4.0 offers a remarkable value proposition, many manufacturing companies fail to implement quality activities via modern tech.
For example, a study conducted by the Boston Consulting Group (BCG) and ASQ in 2018 took input from manufacturing managers, which produced the following insights:
- Only 16% of companies involved in the survey have incorporated Quality 4.0 tools and initiatives
- Of the companies surveyed, 63% haven’t developed a strategy to use Quality 4.0 initiatives
Start Fast, Design for Scale
Maybe you’re thinking, “Okay, Quality 4.0 sounds enticing. But how do I begin?”
The ASQ-BCG study concluded that businesses should “start fast and design for scale” when beginning to work toward an effective Quality 4.0 approach.
The statement means immediately identifying Quality 4.0 opportunity zones, such as enhancing cross-team collaboration. Starting on a smaller scale, introduce solutions and analyze data continuously to ensure your chosen solutions support productivity and continuous improvement. After identifying tools that provide a solid return on investment, roll out larger-scale changes that influence the entire manufacturing process.
One of the first steps in implementing Quality 4.0 is through a top-notch workforce management tool.
For example, Parsable’s Connected Worker® software offers a comprehensive suite of tools. Incorporating advanced communication, analytics, and compliance technology. After its near-seamless integration, manufacturers have everything necessary to connect Quality 4.0 infrastructure and launch their manufacturing processes into the future.
Ready to revolutionize your operational workflows? Experience the power of Parsable’s Connected Worker® software firsthand. Schedule a demo today and discover how our solution can streamline your operations by digitizing your frontline.