What is Poka-Yoke in Manufacturing?
The Japanese are notorious for their dedication to work. In fact, Tokyo tops the list of the most overworked cities in the world. Many would say workers across the globe should look toward the Japanese for inspiration around work ethic.
Apart from hard work, the Japanese have a thing or two to teach us about manufacturing. One such term is poka-yoke.
Poka yoke is a Japanese term that means mistake proofing. Shigeo Shingo developed the idea in the 1960s while working as an engineer at the Toyota Production System. According to him, poka-yoke is any mechanism that eliminates error, making it an impossible occurrence.
- Why Poka-Yoke?
- Principles of Mistake-proofing/Poka-Yoke
- Prevention vs Detection
- Poka-Yoke with Connected Worker Software
- How to Implement Poka-Yoke
Why Poka-Yoke?
In manufacturing, practitioners use poka-yoke for quality control. It ensures the manufacturing process does not result in defects, which would ultimately lead to returns and customer dissatisfaction.
Benefits of Poka-Yoke
The purpose of poka-yoke is to render a manufacturing process error-proof. It minimizes or eliminates the risk of human error to almost zero. It also saves costs incurred when mistakes occur. Some benefits of poka-yoke include:
- Lower quality control costs
- Improved customer satisfaction
- Better manufacturing efficiency
- Increased production
- Safer work environments
- Lower skill requirements
- Reduced rework
Example of Poka-Yoke in Action
We see examples of poka-yoke around us. For instance, if an elevator door remains open too long or detects overload, it triggers an alarm. Similarly, the elevator doors don’t shut unless they sense no one is in the way.
Another example is putting a car in “park and applying the brake before attempting to start the engine. The mechanism ensures that you don’t accidentally start the car in gear, preventing vehicle damage or injury to yourself.
Principles of Mistake-proofing/Poka-Yoke
There are six main principles of mistake-proofing or poka-yoke. How these principles are applied depends on the industry and process in question.
Elimination
Elimination means completely removing the possibility of an error occurring. In this approach, you redesign the process or system so that the error becomes impossible. You eliminate the error-prone step.
If the manufacturing process frequently selects the wrong part for assembly.. You can eliminate this error by only having the correct part in the assembly line.
Prevention
In prevention, you prevent the process or process step that leads to an error. For example, you cannot fill out information in most online forms unless it’s in the required format. You must give accurate contact info and ID number before proceeding to the next step on the form.
The same applies to manufacturing, too. A manufacturer may redesign their equipment or tools to make inserting a part in the wrong position physically impossible.
Replacement
In this approach, you replace an error-prone process with something that minimizes the chances of error. An everyday example is swiping a credit card instead of manually entering the numbers.
Automating labeling in packaging eliminates human error by replacing manual label placement in the process.
Facilitation
Some tasks are so complicated to perform that they can result in errors. In such instances, you can facilitate the process by providing tools or guidance to minimize the mistakes. You can apply this principle in manufacturing by employing procedures and tools to assist employees.
Detection
Detection means noticing a problem before any further processing. Software developers use code reviews to facilitate error detection before deployment. Similarly, the spell check in word processors facilitates error detection in writing.
You can use technology to detect errors in the manufacturing industry, too. For example, motion step methods (sensor-based) can detect if a part is missing or not in its correct position. The alert will prompt a corrective action before the product moves to the next step.
Mitigation
After detecting the error, mitigation occurs. You try not to let the situation get out of hand. If a part is misplaced mid-assembly, stop the machine until the issue is resolved. Doing so prevents more significant problems, like product recalls or malfunctioning machinery.
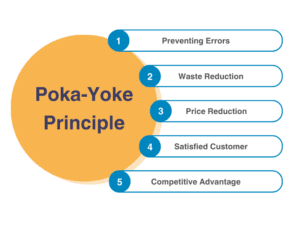
Prevention vs Detection
There are many types of poka-yoke processes, but the two most common are prevention and detection. Prevention-based poka-yokes in manufacturing act before the error occurs, while detection-based ones act after it.
A prevention-based poka-yoke system would eliminate the possibility of errors. It’s like safety bars in roller coasters, which are there to prevent falls.
In a detection-based poka-yoke system, you rely on detection to catch errors. The system stops when it finds a mistake, so you can fix it and stop more problems from happening.
Poka-Yoke with Connected Worker Software
Connected worker software, such as Parsable’s Connected Worker®, lets workers use poka-yoke processes in a digital format. Organizations can use this software to collaborate across the value chain and streamline cross-functional teamwork.
Workers can also “talk” to machines, getting real-time information from IoT devices and sensors. These systems enable remote access to safety updates and training materials, which helps eliminate defects.
How to Implement
Unless you’ve implemented poka-yoke, you can’t avoid mistakes that cost you time, money, or customer satisfaction. To start the implementation process, get the right people on board. Review your manufacturing process and identify the areas requiring improvement.
Once you have a list of possible defects or errors, you can start designing a poka-yoke process to prevent or detect them. In this step, work with a poka-yoke expert.
Next, monitor the effectiveness of your poka-yoke processes. Keep improving them over time or as your manufacturing processes change.
Ready to revolutionize your operational workflows? Experience the power of Parsable’s Connected Worker® software firsthand. Schedule a demo today and discover how our solution can streamline your operations by digitizing your frontline.