What is Kaizen (Continuous Improvement)?
The history of Kaizen, or Kaizen Blitz, is well-documented. The inventor of Kaizen, Masaaki Imai, was a managerial theorist and consultant on the Toyota production system. In 1986, he wrote a book titled “Kaizen: The Key to Japan’s Competitive Success.” His book outlined his examination of manufacturing processes over a decades-long career.
The word Kaizen breaks down into two parts: the first, “Kai,” translates to “change.” The second part, “Zen,” translates to “for the better.” Put them together, “change for the better.”
Below we’ll take a deep dive into Imai’s concept of Kaizen. We will discuss how it changed the business world and led to lean manufacturing and continuous improvement practices.
- The Core of Kaizen (5 principles)
- Benefits of Kaizen in Lean Manufacturing?
- Just-in-Time Inventory Strategy
- The 5 S’s Elements of Kaizen?
- Example of Kaizen
- Connected Worker for Continuous Improvement in Lean Manufacturing
The Core of Kaizen (5 principles)
Kaizen consists of five core principles. Together, these five specific areas empower organizations to implement impactful solutions that elevate productivity and customer satisfaction.
- Know your customer: Before selling to them. Identify their needs and problems to make your product more valuable to them.
- Let it flow: Pursue the elimination of waste, waste being anything that fails to add value
- Gemba focus means going to where the action happens, like factory floors, to understand the real situation. Managers should be present with frontline workers.
- Be transparent: Keep performance data out in the open for all to view key areas for improvement
- Empower people: Organize teams for success, providing clear goals for improving productivity, safety, and quality
Kaizen operates as an action plan and a philosophical approach. The plan focuses on improving organization by optimizing floor layouts to reduce errors, downtime, and rework.
As a philosophy, Kaizen focuses on employee involvement. The philosophy suggests that employees play a vital role in the success of the company. Kaizen sees employees as important to overall success, not just cogs in a machine. Their actions and performance are key to achieving institutional goals.
What Are Some Benefits of Kaizen in Lean Manufacturing?
A successful Kaizen process delivers a handful of benefits to institutional success, including:
- Better cost control: Kaizen cuts costs by reducing waste, without hurting morale like pay cuts or layoffs do.
- Reduce Waste: The goal of Kaizen is 100% efficiency, meaning processes that bring down waste in materials and time.
- Strengthens Communication: Kaizen aims to breakdown silos and increase transparency and accountability, encouraging employees to help identify areas of improvement
- Better quality control: Kaizen uses data analysis to find problems early, improving quality and making customers happier.
Just-in-Time Inventory Strategy
Introducing a just-in-time inventory is one of the specific types of Kaizen that eliminates waste dramatically.
It begins with stream mapping, which analyzes the flows of materials from beginning to end. The maps serve as a visual guide, illustrating each stage of a product’s lifecycle. From there, managers can optimize the process by introducing a just-in-time inventory if applicable.
A just-in-time inventory aligns orders of raw materials with suppliers and production schedules. The outcome is a flow of materials that come when needed, reducing the need for extra storage space.
Advantages of just-in-time inventory are less waste, strong supplier relationships, and quicker production.
What Are the 5 S’s Elements of Kaizen?
Kaizen is about identifying and solving problems that lead to continuous improvement. However, this requires standardization of practices. So, with any Kaizen initiative, management must follow these five steps:
- Sort: Organize tools, parts, and materials into two groups: needed and not needed; get rid of anything not needed.
- Straighten: Get everything ready before starting production to avoid mistakes or delays. Organize parts, materials, and workers for efficiency.
- Shine: Clean and inspect all equipment and workstations to reduce errors and malfunctions.
- Standardize: Create written guidelines and procedures for each stage of the process, including steps, responsibilities, and communication hierarchies
- Sustain: Repeat the first four steps to maintain peak product quality and efficient workflows.
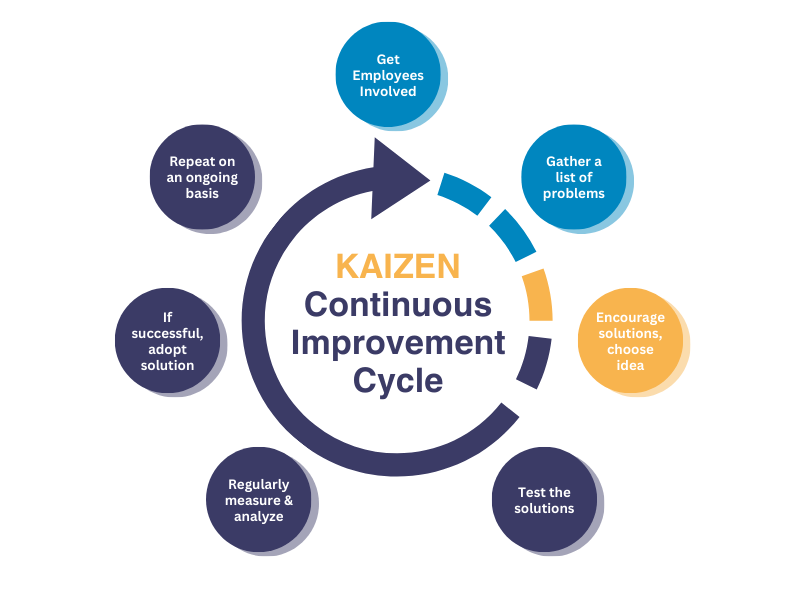
What Is an Example of Kaizen?
A prime example of a Kaizen event would be a company looking to reduce product completion times.
For example, say a car manufacturer wants to improve the speed at which they build and ship one of their cars. TheKaizen process would look something like this:
- Set goals by defining KPIs at each stage, such as reducing process cycle time or inventory stockouts
- Study current processes to find inefficiencies, like broken equipment or departments with lots of downtime.
- Strategize and implement improvements, such as scheduling routine employee training or creating just-in-time inventory schedules
- Check progress every day, see if changes work, and report results to make sure they fix problems and meet goals.
- Standardize all practices that work, creating written and visual guides for new workflows
- If the changes don’t work, begin again with new information in mind
A standard way to practice Kaizen is by following the process of plan, do, check, and act (PCDA). In essence, PCDA incorporates the scientific method into every Kaizen event. It works as follows:
- Plan: Establish goals and what’s necessary to reach them
- Do: Put change into motion
- Check: Evaluate performance results of the new changes
- Act: Standardize changes or begin again, depending on the outcome
Connected Worker for Continuous Improvement in Lean Manufacturing
A significant challenge in Kaizen is ensuring consistent workflows and effectively communicating changes for continuous improvement.
Leveraging a connected worker solution is a modern method for digitizing frontlines, breaking down communication silos, and standardizing procedures from a central location.
Parsable’s Connected Worker® software is among the most effective tools for locking in the principles of Kaizen. Our software empowers managers with a comprehensive suite of features and applications for managing safety, quality, and production insights.
Tools like Connected Worker® can help solve problems and improve processes when using Kaizen in manufacturing.
Want to learn more about operational excellence? Read more about the approach that encompasses all of the solutions you’ll need to maximize efficiency, improve worker safety and create a higher standard of production quality.