Standardized Work: What It Is and How to Implement it
Standardized work is a series of specific steps and procedures to make manufacturing processes safer and more efficient. Standardized work is a core concept in lean manufacturing that minimizes waste, boosts productivity, and helps maintain high quality.
- Elements of standardized work
- Benefits of standardized work
- 6 Steps to implement standardized work
- Connected worker solutions and standardized work
Three Elements of Standardized Work
Standardizing work processes involves more than just creating a uniform work procedure. Lean manufacturing requirements for standardized work include the following three elements of standardized work.
Takt Time
Takt time is the time in which a manufacturer must create a product to meet customer demand. You can calculate takt time by dividing production time by consumer demand. Production time refers to the amount of working time available to complete a product.
Work Sequence
Once you establish the takt time it takes to meet customer demand, you define the work sequence. Your work sequence is a list of steps your workers must take to complete the required product within takt time. List each step in the order it needs completion.
Standard Inventory
Standard inventory, also known as in-process stock, tracks the materials required for manufacturing steps. The standardized work combination table illustrates how takt time, work sequence, and standard inventory impact your work cycle.
By implementing these three elements, you can determine the minimum staffing and other resources needed to increase efficiency.
Benefits of Standardized Work
Standardizing your manufacturing process brings consistency to products, keeps employees content, and fosters ongoing process improvement.
Reduce Product Variation
Standardized processes guarantee uniform manufacturing for every product. Product quality is consistent, and the cost of manufacturing is predictable. You can better predict operating costs and outcomes, which leads to more efficient overall operations and greater customer satisfaction.
Help Employees
With standardized workflows, your employees can complete their work more efficiently. Understanding expectations reduces stress for workers.
In addition, employee training is much easier with a fully standardized work process. All employees get identical instructions and requirements, helping them seamlessly integrate into the workflow.
Continuous Improvement
Standardized work fosters a culture of continuous improvement and problem solving. Creating standardized workflows requires you to repeatedly identify and eliminate ineffective processes throughout the manufacturing process.
Clear calculations and consistent documentation necessary for standardized work allow you to track progress and problem solve. Over time, you learn to recognize areas of improvement so you can further enhance your lean manufacturing operations.
6 Steps To Implement Standardized Work
When you are ready to apply standardized work to your lean manufacturing operations, take these six steps.
Gather Current Operating Data
The first step in calculating your Takt time, work sequence, and inventory is gathering details about your existing operations. Platforms such as Parsable assist in collecting frontline operating data to help you accurately pinpoint your business needs
Pinpoint Areas of Improvement
Analyze your operating data to establish areas of improvement. Consider any aspect of production that costs your operation or fails to add value. Lean manufacturing typically tries to eliminate the following wastes:
- Excess production
- Excess processing
- Unnecessary movement
- Product defects
- Excess production inventory
- Downtime, delays, and waiting time
Use a process capacity sheet to determine the operating capacity of each piece of equipment in your production line. You can use this data to identify and reduce delays and bottlenecks.
Determine the Most Efficient Way to Run Your Operations
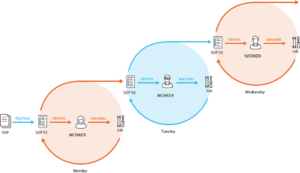
Consider how you can address the areas of least efficiency. After conducting a thorough review, adjust your operations to address the above issues. For example, you may change the way an employee performs tasks or shift equipment to streamline operations.
Digital software helps analyze processes in real-time, allowing for quick adjustments to each manufacturing step for more efficient workflows.
Document, Document, Document
Use digital tools to document your manufacturing instructions and make them accessible to workers. As your processes improve, you can update your standardized work chart without needing to print multiple paper forms, reports, and procedures repeatedly.
In addition, interactive digital work instructions ensure that workers perform each step of the process in order as required. This helps to support your standardization, even as the workflow evolves.
Update Training Programs
Keep your training programs up to date with digital manufacturing instructions. Instead of printing bulky manuals for every class, train both new and existing employees using computers and mobile devices.
Create a Culture of Continuous Improvement
Standardized workflows are a process rather than a goal. Digital programs ease continuous improvement. As you implement standardized work, you should plan to review processes regularly.
Digital tools help you watch processes, gather important operations data, and easily update your standard operating procedures (SOPs).
Standardization of processes makes it easier to notice issues and identify the source. A flexible culture of continuous improvement supports increased efficiency and helps you build a more sustainable operation.
Using the latest connected worker technology, you can also keep workers and leadership on the same page. That means your changes and improvements are in effect immediately without potentially costly delays.
Connected Worker Solutions and Standardized Work
Gather the data you need to create an effective standardized workflow with Parsable’s Connected Worker®. We offer the digital tools you need to transform and optimize your industrial processes. Using the latest digital technology, we empower frontline workers while increasing productivity, employee safety, and product quality.
Using our connected worker solutions, you can quickly and easily establish standardized work processes. Do away with cumbersome paper forms with digital data tracking, efficiency calculations, procedural updates, and training materials.
Get in touch with Parsable today to schedule a demo and discover how our real-time data tracking and insights can assist you in building a successful standardized work strategy.
Ready to revolutionize your operational workflows? Experience the power of Parsable’s Connected Worker® software firsthand. Schedule a demo today and discover how our solution can streamline your operations by digitizing your frontline.