Operational Availability – What it is and How To Improve It
Operational availability, or OA, is a yardstick applied across various industries, including engineering. It measures how often a system is working compared to how often it should be working.
The OA concept focuses on a system’s uptime. It reveals the amount of time the system is up and running and ready to fulfill its designated function.
OA looks at things that could affect uptime, like breakdowns, maintenance, and repairs. It doesn’t just stop at one factor. As such, it’s an important metric for any business to keep track of.
- Calculating Operational Availability
- Do You Have Faith in Your Operational Availability?
- Identifying Causes of Instability in Operational Availability
- Improve Downtime Measurement With Connected Worker
Calculating Operational Availability
People usually express OA as a decimal between 0 and 1. People often convert this into a percentage to make it easier to grasp and understand. Knowing how OA is calculated is helpful.
To find operational availability, divide the average time between maintenance by the total of that time and average downtime. The formula looks like this:
OA = Mean Time Between Maintenance (MTBM) / (MTBM + Mean Downtime Time (MDT))
In this equation, MTBM stands for the average duration a system manages to operate as intended. This includes time without encountering a major breakdown that requires repair or other downtime. MDT is the time needed to find a problem, figure out why it happened, and fix whatever is causing the downtime.
By understanding and managing these factors correctly, you can significantly improve the reliability of each critical piece of equipment and its operational availability.
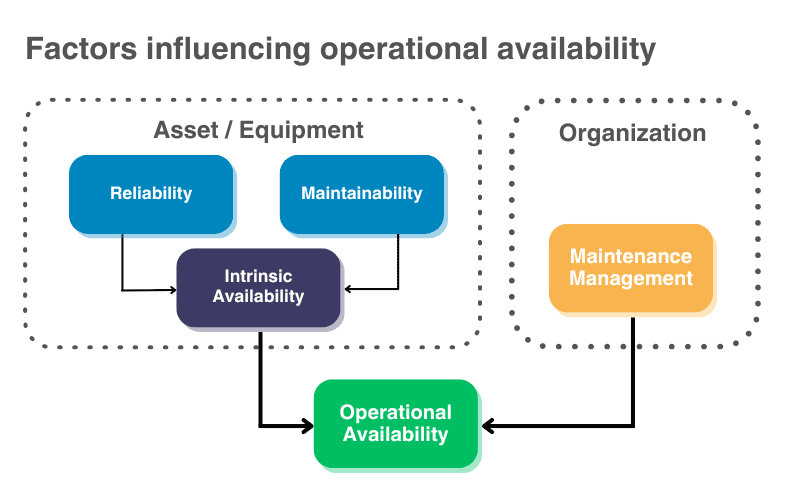
Do You Have Faith in Your Operational Availability?
Operational availability is a complex metric. Because of this, it’s normal to struggle with a few uncertainties. You might feel unclear on how all the puzzle pieces fit together. However, when you realize that OA directly relates to equipment reliability, things start falling into place.
By making sure your machines work well, you can easily create accurate and reliable data for your organization.
Considering things like logistics delays or the availability of replacement parts is important. These issues can be important for your planning and efforts to increase OA in your organization.
Availability Is Equipment Reliability
Why does equipment reliability matter? The answer is simple; a reliable piece of equipment typically results in less downtime. This also means fewer interruptions because of malfunctions, sudden breakdowns, or the frequent need for repair or maintenance.
The outcome of all this is clear. When your system works better, each piece of equipment will have more time to work as it should.
Understanding the connection between OA and equipment reliability can help you appreciate OA more. It can also guide you in taking steps to improve it.
Consider if there are enough repair technicians, parts, or other items available in case there are delays in logistics. Downtime of equipment or systems can impact overall business productivity..
Operation Availability vs. Operating Rate
For efficient and well-informed operations management, knowing the difference between operational availability and operating rate is important.
OA helps you know when your system is ready to work versus when it should be working. Overall Equipment Effectiveness (OA) measures the time your system is operational and performing its intended function effectively.
The operating rate looks at the gap between what your system is capable of and what it is actually doing. It reflects your system’s actual output efficiency.
The operating rate measures how well your system performs at full capacity. It ensures that your system is reaching its maximum potential.
While OA is about uptime, the operating rate focuses on operational efficiency. These two different and distinct components are equally important in understanding the overall performance of your systems.
Identifying Causes of Instability in Operational Availability
Finding out why OA is unstable or unreliable is crucial for making it better. Planned or unexpected downtime can significantly affect your OA.
This downtime could stem from equipment malfunction or inefficient maintenance strategies. It can also stem from logistics delay that makes replacement parts or other important maintenance components unavailable.
Understanding these factors and how they relate can help guide your OA improvement efforts.
Improve Downtime Measurement With Connected Worker
Some traditional methods for improving operational availability can include regular team meetings, employee training programs, and the manual tracking of performance metrics. While these methods have their merits, they can often be time-consuming and prone to human error.
Connected worker technologies can streamline and make these processes more efficient. A “connected worker” uses digital tools and technology to track and handle various improvement methods more efficiently.
By using technology to streamline tasks, a connected worker can easily find information, communicate instantly, and track performance effectively. Digital transformation improves efficiency, reduces errors, and creates a more productive workplace.
Parsable’s Connected Worker software helps frontline workers engage with your company’s digital tools.
Parsable’s technology helps workers collect and communicate data in real-time. This allows teams to quickly capture and analyze data at the work site. Connected Worker® helps track important metrics, plan efficiently to address issues, and improve operational availability.
Want to learn more about the future of work? Read more about the approach that encompasses all of the solutions you’ll need to maximize efficiency, improve worker safety and create a higher standard of production quality.