Leader Standard Work (LSW): What it is and How to Implement It
For a leader to grow, they must understand their core duties in detail. To obtain a clear vision of all duties, companies develop strong systems that lock in managerial routines.
Managers and supervisors can better understand their roles and boost performance is by implementing Leader Standard Work (LSW). Below, we’ll explain LSW and how it enables leaders to flourish.
- What is Leader Standard Work?
- Importance of Leader Standard Work (LSW)
- Leader Standard Work at Every Level
- How to Standardize Frontline Leaders’ Work
- Operator vs. Leader Standard Work
- Benefits of Standardizing Managers’ Work
- The Connection Between LSW and Daily Management Systems (DMS)
- Connected Worker for Sustaining Management Standards
What is Leader Standard Work?
In practice, LSW outlines a team leader’s daily, weekly, and monthly tasks. These tasks include things like:
- Performance reviews
- Shift handovers and schedule changes
- Key performance indicators (KPIs) reviews
- Gemba walks
- Healthy, safety, and compliance audits
These leadership tasks vary depending on an organization’s nature and the leader’s title and job description. However, the goal of LSW is to set a consistent schedule for driving continuous improvement.
Leader Standard Work (LSW) Components
Breaking it down, LSW consists of four core components:
- Routine schedules outlining daily, weekly, and monthly tasks
- Developing managerial skills
- Finding new tools for more efficient and effective management
- Hierarchies of accountability
Importance of Leader Standard Work (LSW)
Instituting LSW is critical to organizational success, long and short-term. Done correctly, it yields many benefits.
Standardization
Every managerial task must have a written and defined standard. Standardized tasks establish consistency, allowing leaders to perform their best, as well as when they do their jobs correctly.
Leadership
Standardized work promotes healthy leadership skills. For example, manufacturing floor managers should build schedules for training new staff members. These schedules allow for improved training over time, resulting in safer and more productive employees.
Active Management
Active management is inseparable from continuous improvement, and LSW establishes proactivity as a core tenet. An example of this is scheduling daily or weekly Gemba Walks to analyze and gain information from frontline workers.
Cultivating Improvement and Problem Solving
Cultures of continuous improvement are a modern business concept that starts from the top down. Holding team leaders accountable for their duties benefits everyone.
LSW also promotes problem-solving because it promotes organizational awareness and allows channels for improving existing methodologies. When duties are clear, it’s easier to identify areas for improvement and opportunities to enhance productivity.

Leader Standard Work at Every Level
The LSW processes and routines involve all management and leadership roles, not just those at the top.
Leader Standard Work (LSW) for Different Levels
Of course, LSW schedules look different depending on where a leader falls within an organization’s hierarchical structure. For example, C-suite executives have a much lower percentage of standardized work as opposed to team leads.
How to Standardize Frontline Leaders’ Work
Building an approach to LSW takes more than outlining responsibilities. Companies should take a step-by-step structure to roll out LSW successfully.
1. Standardize Management Practices
Calculate the percentage of standardized work for team members based on the hierarchical level. To calculate, outline all essential standardized responsibilities, including:
- Daily checkups (Gemba Walks)
- Audits and inspections
- Visual management and KPI monitoring
- Meetings and follow-ups
- Procedural and safety training
2. Equip Team Leaders and Directors with Management Tools
Connected Worker® digital software simplifies the creation of effective LSW procedures, reducing administrative burdens and enabling leaders to manage their responsibilities easily.
3. Establish Daily, Weekly, and Monthly Routines with an LSW Calendar
Creating a detailed calendar provides leaders with a visual management tool, ensuring full awareness of responsibilities.
4. Establish Objectives and Performance Indicators
Without goalposts, management can’t track the effectiveness of current procedures. As such, KPI monitoring is essential to LSW, especially when segmented into departmental and hierarchical duties.
5. Promoting Optimal Management Behaviors
Good management boils down to how leaders handle human connections, and standardized workflows must support that. LSW must include time for routine 1:1 meetings and group-wide discussions covering team objectives and goals.
Operator vs. Leader Standard Work
Producing an effective LSW resulting in process improvements hinges on finding the line between operator work and leader work.
Operator standard work deals with specific procedures that fall under criteria like 5S and meeting performance targets.
Leaders focus on continuous improvement by envisioning ways to enhance productivity, safety, and profits. They use methods like Gemba Walks, scheduling, shift changes, and monitoring meetings and reviews to manage effectively.
Addressing Managerial Standards and Team Performance
Managers require personal standards if they are to improve the performance of those working below them. LSW allows organizations to define clear standards for the leadership they strive to cultivate. From there, identifying which managers help or hinder team performance is much clearer.
Example of Daily Standard Work
Imagine LSW as a square on a calendar that outlines management’s daily, weekly, and monthly tasks. In practice, it would look like this:
- 8:00 AM: 1st Gemba Walk
- 10:00 AM: Health and Safety Audit
- 12:00 PM: Weekly Maintenance Meeting
- 3:00 PM: Shift Handover
- 4:00 PM: 2nd Gemba Walk
- 5:00 PM: Monthly KPI Performance Review
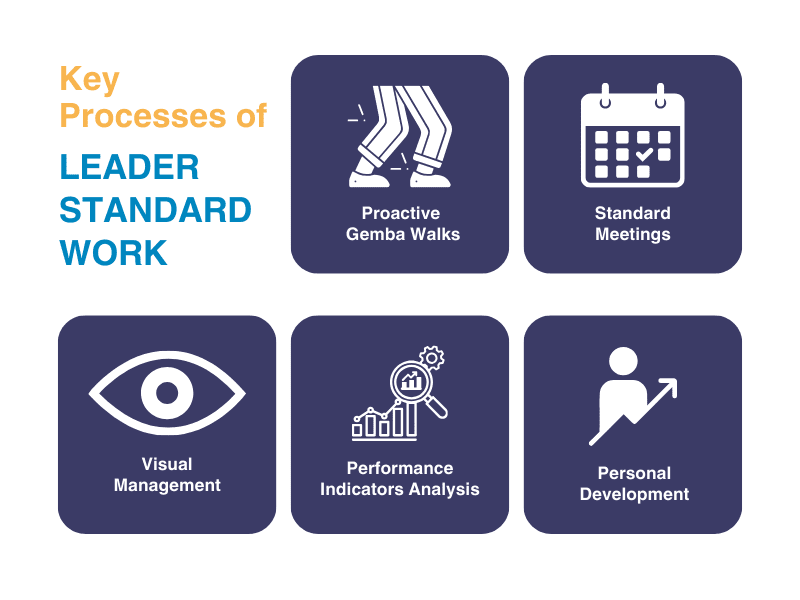
Benefits of Standardizing Managers’ Work
Standardized work is critical for improving entire processes, whether it’s for a specific department or an entire factory floor.
Alignment with Organizational Goals
LSW allows leadership to define goals, and unite around a strategy to meet them.
Cultivation of Problem-Solving Skills
A set of practices gives managers time for team-building exercises and meetings, including problem-solving skills.
Proactive Control
Routine schedules must lock in time for brainstorming ways to solve issues ahead of time, rather than taking a reactive approach.
Streamlining Employee Onboarding and Workplace Safety
Depending on the process, manufacturing onboarding spans from days to months. LSW helps build the most effective onboarding process over time, as well as train employees correctly from the beginning.
Engagement in Continuous Improvement
Strong LSW allows teams to view success and failure through the lens of a system, rather than individuals. A system-based approach creates a positive work environment. Team members can work together to improve the system instead of blaming others.
Enhanced Response Agility
Standardized work creates clear channels of communication. This speeds up problem-solving, breaks down silos, and builds a culture of transparency.
The Connection Between LSW and Daily Management Systems (DMS)
The LSW and DMS processes both exist to establish daily routines that improve over time.
Foundation of Lean Leadership Routines and Culture
Both LSW and DMS include core principles surrounding lean leadership, such as Gemba Walks, daily huddles, safety checkups, and productivity reviews.
Catalyst for Accountability and Alignment
When used together, LSW and DMS help unite teams around common goals. They also enhance understanding of organizational structures and communication channels, fostering accountability.
Enabling Leadership Traits through LSW and DMS
Standardized flows like LSW and DMS both shape how leadership develops and improves over time. Done carefully, corporations can use both systems to promote leadership traits they wish to promote in the company culture.
Connected Worker for Sustaining Management Standards
A core factor in locking in transformative LSW practices is investing in connected worker software. These tools centralize tasks and routines such as scheduling for leadership, analyzing KPIs, and managing performance. Parsable’s Connected Worker® is an excellent choice for managing LSW processes and promoting operational excellence through data-driven insights and frontline worker visibility.
Industry leaders have a glimpse into the future of manufacturing, and they see connected work as the bridge that will take them there. Read more on how Connected Worker® helps drive continuous improvement.