These Six People are Critical to a Successful Connected Worker Implementation
At Parsable, we’re strong believers in the power of people. Nowhere are people more important than in the implementation of Connected Worker® by Parsable. When planning a deployment with Parsable, in order for your roll out to be as successful as possible, you’ll want to make sure all your ducks are in a row.
It’s important to have a clear plan in place outlining your objectives, the resources required, an understanding of timelines and who’s responsible. This is especially important for the initial deployment and your first set procedures that you want to digitize – in order to set you up for success and establish a solid baseline for a larger global roll out.
Before you deploy Parsable or any connected worker solution, it’s absolutely critical that you have the right team on board to help with the roll out.
Once you’ve identified the core team of people that’ll help get this project off the ground and continue to keep it running smoothly, you can set expectations. You’ll want to clearly define what, how, when and why as it relates to your deployment. This means helping each person on your team understand what is their role in this project, what are they responsible for, why is this new technology beneficial for your company and how will this project be deployed and when.
In this post, we’ll share how Parsable simplifies governance at scale within your manufacturing operations.
Who Are Your Key Stakeholders?
One of the key elements of an implementation with Parsable is the overall organizational structure and governance our customers put in place. We’ve seen customers rapidly scale to over 100 locations across a number of countries in their digitization journey – moving away from outdated paper-based procedures and adopting digital work instructions to realize quick time to value.
As we reflected on some of the most successful companies that drove change, we saw a clear model emerging. The companies that scaled most effectively, established a particular governance model that we call the Center of Excellence (COE). It consists of six essential people or groups that form a centralized process organization. You need a core team, across different levels of your organization, in order for your roll out to be successful. It’s their responsibility to stay informed, making sure the project keeps moving forward in the right direction, ensuring consistency across sites and establishing credibility along the way.
The COE team consists of:
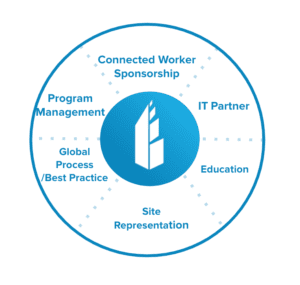
Connected Worker Sponsor:
They’re a global executive sponsor, or sponsors, who’ll drive the overall Parsable program and ensure alignment with the strategic vision for their digital initiative. They add gravitas to the implementation of your digital initiatives and the authority necessary to make the implementation successful. The global executive team will set all of the global success metrics and key performance indicators for the program. They’ll provide the overall direction for the rest of the COE to follow during the implementation.
Program Manager:
They’re a single point of contact (SPOC) who will centrally own and manage the roll out of your connected worker program. The success of the actual deployment rests with the program manager, so it’s essential to get the right person in this role. Typically they’re someone who has implemented software before and has the people skills to lead through influence, as they’ll be working across multiple functions, regions and sites.
Often, Parsable is a piece of your company’s digital program and you might have other systems you’re managing. We’ve found the most successful roll outs have a program manager that can start getting stakeholders involved and driving the software implementation. They’re really the key to moving things along and realizing your quick time to value. You need someone that can manage the entire digital program.
Global Process Owners:
They’re people who will define and manage standard processes and a best practice function where processes are non-standard. These owners are the functional heads that own all the processes and procedures across business functions such as safety, quality and production. They play a critical role, because once you’ve identified the set of use cases to transform from paper checklists and procedures to digital work instructions, they’re your go-to experts that have the knowledge and authorization to help improve these specific processes. A procedure on paper is not the same as a digital procedure. The digital format of a procedure gives you so much more flexibility and critical data points that you’re able to capture at every step.
Site Champion:
You’ll want to have someone at each individual site to champion Parsable and to help drive adoption. They work closely with the program manager, and two-way collaboration and communication will be critical to ensure things are moving forward.
Typically at a site, you might even have a mini governance structure, where you have a site champion, authors to create templates, people planning jobs and then all your users at the site level. A site champion is key to ensure the implementation goes smoothly and that change management is taking place. They could be a site manager, a continuous improvement person or a supervisor – a good champion knows everyone in the plant and is tech savvy.
Education Partner:
Another important area is education and having a central owner to help train people. Often, education gets rolled up into the global process or program management role. But, we’ve seen companies hire for an education-specific role, and they’re the ones that end up maintaining the training that goes into Connected Worker. So, once you have a large global roll out, you should have a designated person to administer the training.
IT Partner:
And finally, you’ll need an IT contact who is responsible for infrastructure, integrations and reporting. They play an important role in making sure your implementation is in line with your company’s security policies. They will help guide you to ensure you have the appropriate infrastructure in place to implement Connected Worker. You’re going to have some angry end users if your wi-fi is too slow to handle your digital initiative, whether it’s a technology solution like Parsable or an IoT sensor.
Looking at the big picture, here are a some benefits and value you can derive from having a Center of Excellence in place:
- You get centralized process organization.
- You have global process owners who can help you drive standardized procedures and best practices.
- You can ensure consistency across each of your sites.
- You can capture enterprise-level reporting, as opposed to site-by-site reporting – so you have a more holistic view of your operations.
What Does a Typical Implementation Look Like?
Think about which processes, or use cases, could be the easiest and quickest to digitize. Maybe it’s a safety walk, CIL (clean/inspect/lubricate) procedure or pre-trip truck inspection.
Digitally transforming your operations means moving dozens of procedures off paper. Because it’s not necessarily realistic to implement a full transformation in one go, tackle it in stages.
As a company, you must come together to find a common approach where you can drive visible return.
Start by identifying a couple of use cases at one site – this will become your champion site that will be used as a model for implementation at other sites. Essentially, once your champion site is up and running, other sites can follow suit and replicate the implementation process.
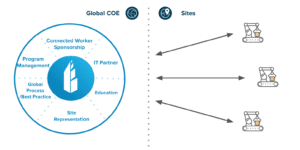
From there, you can easily scale and then iterate accordingly. Are there simple processes that are similar across multiple plants or sites? This way, once you can prove initial success at one site, you can make the case to digitize the process at multiple sites – while also capturing all the data points along the way that will enable you to continuously improve the process across plants.
The goal is to have a couple champion sites by type. For example, if you’re an agricultural manufacturer, your champion sites would be grouped by corn, wheat, soy, etc. It’s easier to group by type because the use cases and production lines are similar.
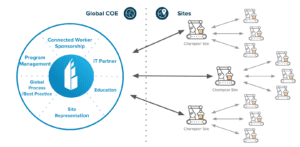
With the support of our professional services team, you can get up and running in no time. This can vary depending on the resources allocated, number of use cases and plants targeted to get up and running. But, following this strategy will help you win the war for momentum and drive long-lasting change that ensures the sustained success of your operations.