What is Clean in Place (CIP) and Best Practices
Manufacturing and processing pharmaceutical, food, and beverage products requires highly effective cleaning solutions. Cleaning in place offers an efficient way to support clean processing methods consistent with strict industry standards.
Clean-in-place (CIP) systems quickly and thoroughly clean processing equipment without requiring the removal of components. Businesses that incorporate CIP solutions enjoy numerous benefits, including reduced downtime, increased production, and enhanced product safety.
- What is Clean-in-Place in Manufacturing?
- Functional Goals of CIP
- Essential Design Tips and Considerations
- Develop a Successful CIP With Connected Worker Software
What is Clean-in-Place in Manufacturing?
In manufacturing operations, CIP is a series of cleaning cycles specifically engineered to optimize cleaning efficiency. Rather than disassembling and cleaning process piping and components by hand, users can utilize automated CIP systems.
Companies that process or manufacture consumable products must meet stringent standards governed by the Food and Drug Administration (FDA) and US Department of Agriculture (USDA). Automated clean-in-place processes allow you to ensure efficient cleaning while meeting even the strictest industry standards.
Industries That Utilize CIP
The efficiency of CIP systems makes them beneficial for numerous industries, including:
- Food processing and manufacturing
- Dairy processing
- Beverage production
- Breweries and other fermentation facilities
- Pharmaceutical manufacturing
Each industry uses different types of equipment to process materials and products. Tailor CIP cycles to meet your facility’s specific needs.
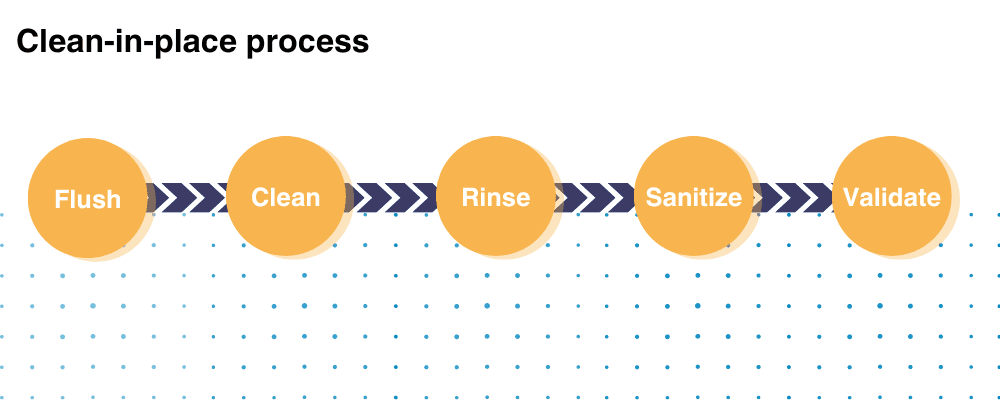
Functional Goals of CIP
CIP aims to establish clean, hygienic operations with the utmost efficiency. The functional goals of CIP are as follows.
Effective and Uniform Equipment Cleaning
Automated clean-in-place methods ensure consistent, repeatable cleaning. CIP systems also reduce the potential for human error. This ensures better quality products that consistently meet industry standards.
Prevention of Product Cross-Contamination
CIP solutions help manufacturers prevent cross-contamination from cleaning chemicals. They also help avoid cross-contamination with allergens, raw foods, and drug ingredients.
By controlling the risk of cross-contamination, you enhance consumer safety, align with legal and regulatory requirements, and bolster your brand’s reputation for excellence.
Improved Safety and Productivity
CIP systems require less hands-on cleaning from workers, which reduces potential exposure to dangerous cleaning chemicals. Automated cleaning processes require fewer workers, allowing you to assign them to other tasks on the production line.
Additionally, automated CIP systems are simply faster than manual cleaning. Workers who might otherwise have spent hours cleaning between batches can move from one batch to the next more quickly.
Reduced Downtime and Lower Overhead
Automated clean-in-place equipment handles cleaning more quickly, with no disassembly necessary. This reduces downtime for cleaning, maintenance, and repairs. CIP is also more energy-efficient and uses less water and cleaning chemicals than manual cleaning.
Since every facility has different requirements, manual cleaning methods can be extremely expensive and time-consuming. By automating clean-in-place systems, you can ensure cleaning consistency, thoroughness, and accuracy while reducing operating overhead.
Essential Design Tips and Considerations
An ideal CIP system will consider the specific needs of your overall operation, as well as your unique equipment requirements. Take the following factors into account when designing your clean-in-place solution.
1. Clarify Your Operation’s Particular Cleaning Needs
Analyze your operation’s cleaning requirements, including:
- Equipment and components you will clean
- How often you need to clean them.
- Specific regulations or requirements for your products or equipment
Pharmaceuticals, for example, require extensive cleaning to avoid chemical or drug cross-contamination between batches. Some CIP cycles use strong chemicals, high temperatures, and UV light to decontaminate product contact surfaces. Chemical concentrations may also vary depending on your decontamination needs.
2. Account for Your Production Schedule
Your CIP system design should match your production schedule. Consider the amount of time you have to clean and engineer your system to address cleaning needs as efficiently as possible. This means reviewing the size of your system, cleaning frequency, cleaning methods, and flow rate.
You should also review which processes require cleaning between batches. Some products may be fine with a quick pre-rinse, while others will need a thorough cleaning of the entire system. Consider all these factors when integrating CIP into your production line.
3. Reduce Cross-Contamination Potential
When food, beverage, and pharmaceutical manufacturers process different products, cross-contamination is a risk. Allergens, raw food, and chemicals can contaminate products and make them dangerous for consumers. A well-planned CIP system can mitigate these risks and reduce your liability. Examine your system for potential cross-contamination risks and plan your clean-in-place strategy to avoid these pitfalls.
4. Lower Chemical and Water Usage
Incorporating automated CIP solutions helps you reduce the amount of water and chemicals you use in your cleaning processes. Some systems incorporate pressurized water, final rinse water recycling, spray devices, heat exchangers, and chemical alternatives to reduce cleaning time while optimizing disinfection processes.
Analyze your water, chemical, and energy usage while creating your new CIP plan. Address areas of waste to create a more sustainable, eco-friendly process.
5. Enhance Material Flow and Liquid Drainage
During the CIP system design phase, review the flow rates in your process piping. CIP cleaning uses water turbulence to clean process piping. Calculate your CIP system flow rates based on the amount of pressure and turbulence you require for adequate cleaning.
In addition, review your drainage capacity to ensure that your drain valves, drain hubs, and floor drains are capable of handling cleaning fluid flow. Adjust your drainage equipment as necessary to prevent flooding, backflow, and splashing during peak cleaning periods. Check your drainage pipes for dead legs where contaminants could become trapped.
6. Determine Your Available Space
Map your available space when considering the best CIP setup for your facility. You can tailor the system to meet your spatial limitations. Many users opt for a centralized CIP system. With one system, you can use a single tank for cleaning fluids and centrally operate the different circuits for each pipeline.
Sometimes, complex operations with limited space may need multiple tanks and operating centers. Choose the system that meets your spatial needs while ensuring operating efficiency.
7. Ensure CIP System Compatibility With Cleaning Requirements and Equipment Layout
Some process piping, manufacturing equipment, and even drainage systems use materials that can be incompatible with cleaning chemicals. Avoid unnecessary damage and deterioration by reviewing your system’s configuration in advance. In some cases, a CIP system installation will generate enough cost savings to justify replacing incompatible components. If your system requires harsh chemicals to meet industry standards, plan to include compatible equipment from the beginning.
Develop a Successful CIP With Connected Worker Software
Design an effective CIP process from scratch using critical frontline operations data. Parsable’s Connected Worker® platform can help you gather, track, analyze, and optimize your clean-in-place operation for the best possible efficiency and sustainability.
When designing your clean-in-place strategy, incorporate software solutions that support worker communication, training, and efficiency. Parsable’s comprehensive Connected Worker® platform provides you with digital frontline operation tools to help streamline every aspect of your manufacturing operation.
Our connected worker software solutions can help you reduce costs, increase efficiency, and enhance operational sustainability by analyzing frontline data for areas of improvement. Digitizing your frontline operations with Connected Worker® helps you identify and address potential issues in your CIP processes and other operations before they become problems.
Contact us today to schedule a demo and see how our digital solutions can standardize and optimize your work processes.
Ready to revolutionize your operational workflows? Experience the power of Parsable’s Connected Worker® software firsthand. Schedule a demo today and discover how our solution can streamline your operations by digitizing your frontline.