What is Operational Excellence in Manufacturing?
Operational excellence is a business management method that focuses on creating a culture of continuous improvement. It does so by fostering employee investment in the success of the business. The approach aims to keep employees and management aware of the flow of value from production to the customer.
When employees comprehend their role in the organization, it helps them swiftly recognize and solve problems with minimal disruption. Operational excellence creates a customer-centric mentality that encourages continuous improvement to drive operational agility, long-term efficiency, and sustainable growth.
- Industries That Benefit from Operational Excellence
- Principles of Operational Excellence
- Methodologies of Operational Excellence
- Applying Operational Excellence
- Advantages of Implementing Operational Excellence
- Advanced Tech and Operational Excellence
- Connected Worker and Operational Excellence
Operational Excellence and Continuous Improvement for Changing Market Conditions
In today’s ever-changing global economy, complex business management requires continuous improvement. Businesses must still focus on return on investment (ROI) and improved efficiency. However, competitive advantages depend on flexibility and resiliency in the face of market shifts, new technology, and evolving conditions.
Operational excellence creates a competitive advantage by creating a company culture of continuous improvement. This allows complex business environments to thrive and grow by encouraging problem-solving and overall process improvement.
Industries That Benefit From Operational Excellence
Operational excellence can benefit any industry, from product manufacturing to retail sales. Some industries have already established a standard of operational excellence, including:
- Construction: Operational excellence keeps construction projects on task and within budget by optimizing efficiency, promoting worker safety, and minimizing overhead.
- Technology: Information technology companies utilize operational excellence to ensure efficient development and optimize workflow.
- Healthcare: Operational excellence focuses the customer experience, enabling healthcare workers to decrease patient wait times and enhance health outcomes.
- Manufacturing: Manufacturers incorporate operational excellence to improve productivity in manufacturing operations while cutting down on waste, reducing downtime, and minimizing overhead.
- Retailers: Focusing on customers while striving for operational excellence helps retailers improve product quality by making supply lines more efficient and standardizing internal operations.
Understanding the Principals of Operational Excellence
The concept of operational excellence focuses on enhancing product quality and the customer experience. The Shingo Model is the basis, which established the following ten core principles of operational excellence:
- Respect each individual
- Lead with humility
- Seek perfection
- Encourage scientific thinking
- Focus on process improvement
- Ensure quality at the source
- Improve the flow of value
- Think systemically
- Create constancy of purpose
- Create value for the customer
The principles of the Shingo model aim to make it easier for value to flow from the organization to the customer. By communicating purpose, you create a culture focused on systemic process improvement. Your organization ensures that each team member knows their role and acts in line with the organization’s goals and principles.
Established Methodologies for Operational Excellence
The Shingo Model of operational excellence serves as the fundamental basis for many of the principles. However, many companies have adapted the method to apply to their fields and industries. Other operational excellence methodologies include:
Lean Manufacturing: Prioritizes efficiency by maximizing employee productivity and reducing waste
Six Sigma: Focuses on process standardization to eliminate errors and reduce defects
Kaizen: Methodically and gradually approaches change through employee involvement in continuous improvement
Scientific Learning: Uses an evidence-based approach that incorporates trial and error, observation, and iterative process improvement
Okapi: Uses specific, measurable, achievable, relevant, and timely (SMART) key performance indicators to foster sustainable improvement
Hoshin: Aims all parts of the organization toward meeting specific business objectives
The flexibility of operational excellence lets each company modify its approach to suit its business needs. There is no one right way to achieve operational excellence. Rather, the goal should be to improve every aspect of your organization from an operational standpoint.
Applying Operational Excellence to Your Organization
Implementing operational excellence requires a workforce that continually improves processes. This means establishing clear goals and expectations while understanding that the process is fluid.
Operational excellence is not a fixed state; it’s a constant process of review that motivates employees and leaders to continually improve.
Reviewing your key performance indicators (KPIs) in operational, workforce, and financial aspects can help in determining metrics and defining future goals. While every company’s solution will be different, operational excellence should always focus on delivering value to the customer and facilitating open communication.
Focus on Delivering Value to the Customer
The primary goal of operational excellence is optimizing the customer experience. From an operational standpoint, this means creating high-quality products promptly and at a competitive price.
Digital tools can help you analyze business trends and establish areas of improvement. By adopting real-time data collection, you can measure your organization’s performance and discover ways to add more value for your customers.
Clearly Communicate Business Goals Internally
Employee buy-in is a critical aspect of operational excellence. Provide clear, actionable goals and expectations to ensure employees actively engage in continuous improvement.
Instead of trying to correct issues by focusing on employee performance, operational excellence pays attention to the processes themselves. This aligns employees and leadership in pursuit of a common goal.
Use mobile technology like Parsable Connected Worker® to keep everyone connected, informed, and focused on continuous improvement.
Advantages of Implementing Operational Excellence
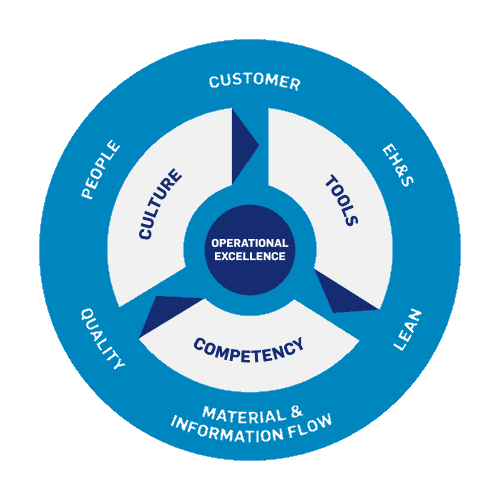
Operational excellence encourages your company to look at its internal operations for areas of improvement. A critical approach that encourages continuous change can lead to numerous benefits, including:
- Reduced overhead: Operational excellence helps you reduce operating costs and increase revenue by streamlining internal operations and reducing inventory.
- Enhanced workflow efficiency: Digital process management tools let you identify and rapidly address bottlenecks, overproduction, waste, and other roadblocks to efficiency.
- Operational standardization: Standardized operational requirements help employees meet expectations and contribute to overall accountability.
- Improved worker collaboration: When employees know how they fit into the bigger picture, they make better choices that help the whole company.
Advanced Technology Facilitates Operational Excellence
Digital technology is a critical component of a successful operational excellence strategy. To streamline operations, you must first be able to identify areas of improvement. The latest business management technology can facilitate a smooth transition to operational excellence and foster continuous improvement.
Business Process Automation
Often, mundane tasks require time and effort from employees whose skills can be better applied elsewhere. Business automation programs can help with repetitive activities like billing, invoicing, report preparation, and analyzing data.
Business process management tools can also help you compile and sort information to draw actionable conclusions. Using this information, you can map each step of the process and create a more efficient workflow.
IT Operations Automation
Information technology (IT) operations manage critical digital infrastructure that keeps your organization running. IT teams can use optimization technology to automate numerous tasks.
IT management systems allow workers to monitor the full stack of applications in use by your organization. IT workers can make adjustments to improve how applications work, making them more efficient, while lowering the risk of expensive periods of downtime.
Integration
Communication between every part of the organization is crucial when establishing operational excellence in your organization. Digital integration technology ensures that your organization can rapidly share critical information.
Integration tools allow secure sharing of information between apps and devices, making sure all parts of your organization have the most up-to-date information. With immediate access to accurate information, leadership and workers can make informed business decisions.
Integration makes your organization more flexible and resilient. When faced with market shifts, supply chain disruptions, and other challenges, your company can stay ahead of the competition.
Connected Worker® and Operational Excellence
Parsable’s state-of-the-art Connected Worker® technology provides the digital support you need to move from inconvenient paper forms to a mobile-first approach. Parsable lets you connect your workers and leadership to share goals and operational data and drive operational excellence.
Also, you can make and change procedures and training info to keep your employees updated on the newest organizational changes. With Parsable, your organization gets the tools to get immediate insights and easily adjust operations to match new needs
Contact Parsable today to request a demo and see how our Connected Worker® technology can enhance your operational excellence.
Ready to revolutionize your operational workflows? Experience the power of Parsable’s Connected Worker® software firsthand. Schedule a demo today and discover how our solution can streamline your operations by digitizing your frontline.