What is a Gemba Walk and Why is it Important?
Have you ever taken a Gemba walk? It is not the latest health trend, physically speaking. Rather, it is part of the Lean Management philosophy and is used across many industries to help businesses identify areas for continuous improvement.
It doesn’t matter if you apply the Gemba walk to a shop floor, a warehouse, or massive digital operations. Continuous improvement and recognizing inefficiency are necessary to stay afloat in the fast-paced business world.
This article explains the ins and outs of a successful Gemba walk. We’ll explain the origin, benefits, and steps to do a self-assessment for finding ways to improve continuously.
- What Is a Gemba Walk?
- 7 Steps to Follow Gemba Walk
- Gemba Walk Checklist
- Post Gemba Walk
- Practicing Gemba Walk
What Is a Gemba Walk Actually?
Gemba is a Japanese word that translates to “the real place.” It also often translates to “the place where value is created.” Taiichi Ohno, a famous engineer for Toyota, coined the term and earned the title of the father of lean manufacturing.
In short, the term Gemba signifies the place where a business creates its valuable product, also known as the front lines. For example, for an automotive company, it’s the factory floor. For a petrochemical company, it’s the oil rigs and refinery plants.
Basically, Gemba walks are a way for managers to be present in these spaces and put themselves at the scene of action. They can review their processes, analyze them, and evaluate their productivity, cost, efficiency, and safety.
Elements of a Gemba Walk
Thinking of the Gemba walk as a tool for businesses to identify and eliminate wasteful activities is essential. Three elements enter a successful Gemba walk.
1. Go and see
Be present. A simple act, but something management frequently fails at. Regular Gemba walks through “the real place” are essential to understanding the struggles workers face daily.
Some managers shy away from this, thinking a Gemba walk might make team members nervous. However, in reality, management by walking around (MBWA) is anything but ominous. It isn’t about judging workers.
Rather, it’s a way for managers to evaluate their operations objectively. From there, they have opportunities to identify ways to optimize processes and benefit their employees.
2. Ask why
Without active communication, the Gemba walk is useless. Good leaders know to listen first and then speak.
A Gemba walk relies on understanding the needs and complaints of those who work on the front lines. This involves being present, asking why certain processes are problematic, and listening to criticisms.
This step takes some digging, so managers must learn to employ various techniques. The five whys is a method for managers to understand the reasons behind problems. It involves listening and asking questions instead of giving orders.
3. Respect people
While performing a Gemba walk, it’s critical to avoid coming across as domineering or judgemental. Too often, managers can point fingers and criticize workers when in fact, it’s their own processes that stifle productivity. A Gemba walk is a team activity to improve processes and make them more productive for everyone.
7 Steps to Follow When You Go to Gemba
To ensure success, you should practice seven key steps with every Gemba walk:
- Pick a theme to focus efforts on a specific area, such as safety or productivity
- Prepare your team so everyone is comfortable and understands expectations
- Focus on the process, not on the people, because a Gemba walk is not a performance evaluation
- Be where the value stream is, because that’s where the most potential for positive change resides
- Record your observations and wait to offer solutions later
- Add an extra pair of eyes by bringing along a colleague from another department
- Follow up with all teams about any upcoming changes
Gemba Walk Checklist
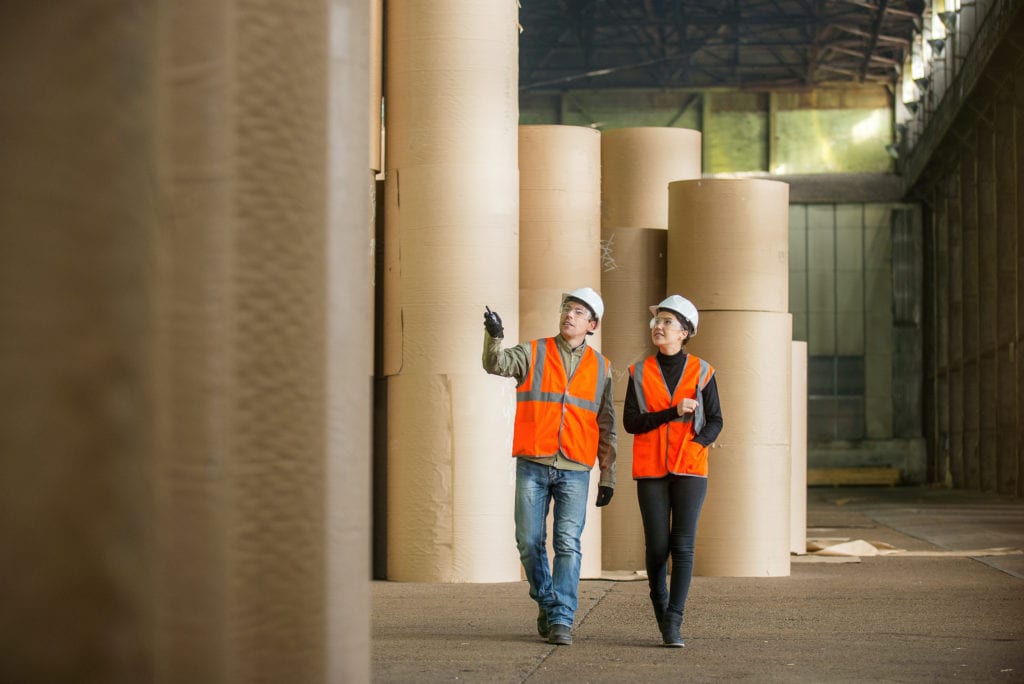
Gemba walks require forethought. This way, you can target your efforts and actually get to the heart of the issues.
Prepare a list of questions to remember as you investigate key processes. Of course, these questions will vary depending on the nature of the process, but below are a few general questions to use:
- What is the description of this work process?
- Does this work have an established process?
- Does this process further our company’s goals?
- Who is responsible for each task in the process?
- What might cause this process to fail to reach its goals?
- Do workers know how to report issues?
- What could speed up or make this process more efficient?
Post-Gemba Walk
Simply performing a Gemba walk isn’t enough on its own. After each Gemba walk, record observations and review results in a post-mortem, including these steps.
- Organize your thoughts and notes
- Analyze with care
- Incorporate worker insights
- Utilize collected data
- Diverse participation in review
- Complete the loop
- Show respect and build success
Practice the Gemba Walk Efficiently
Incorporating the Gemba walk into your management strategy is always a good idea. However, you must approach it as effectively as possible. Using the best tools is a great way to keep front-line workers satisfied, safe, and able to communicate effectively.
Did you know that 45% of frontline workers state they are considering leaving their current job for somewhere that offers a more modern, digitized work process? To ensure you’re providing frontline workers the tools they need for success, consider investing in Parsable’s Connected Worker® mobile application.
Parsable’s Connected Worker® mobile application enhances communication between front-line workers and management by allowing them to streamline collaboration and track key processes. Our app collects data from the front lines and helps with tasks like documenting processes, making checklists, and following regulations.
Learn how Connected Worker® can level up your operation’s productivity, safety, and efficiency by signing up for a free product tour today.
Ready to revolutionize your operational workflows? Experience the power of Parsable’s Connected Worker® software firsthand. Schedule a demo today and discover how our solution can streamline your operations by digitizing your frontline.