10 Stats about Digital Transformation that Every Plant Manager Should be Wrestling with Now
1. Peer Adoption
Industry 4.0 is coming, whether you’re ready or not. It’s your decision whether you want to be left in that 23% in five years.
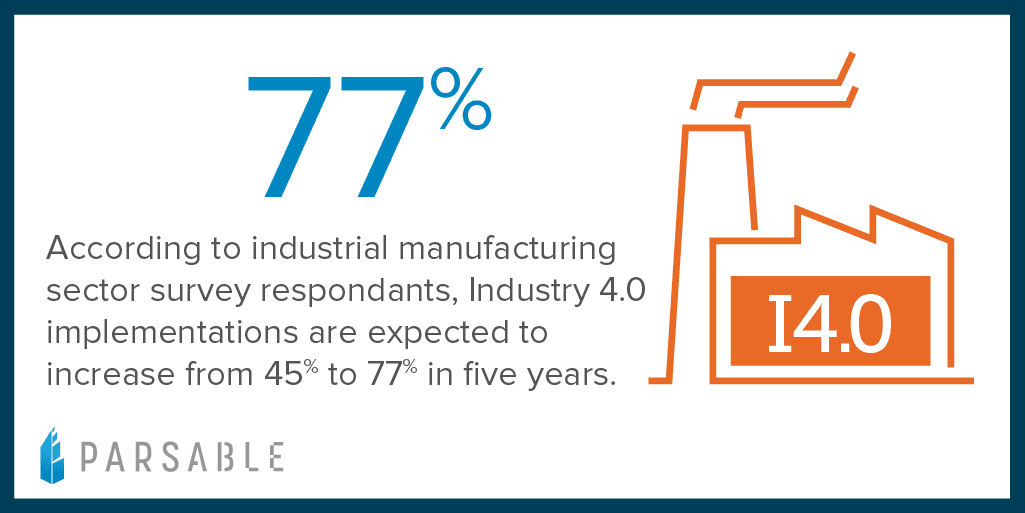
2. Savings
Between making up for lost time and error costs, billions of dollars can be saved by implementing Industry 4.0. Don’t let this opportunity fall through the cracks.
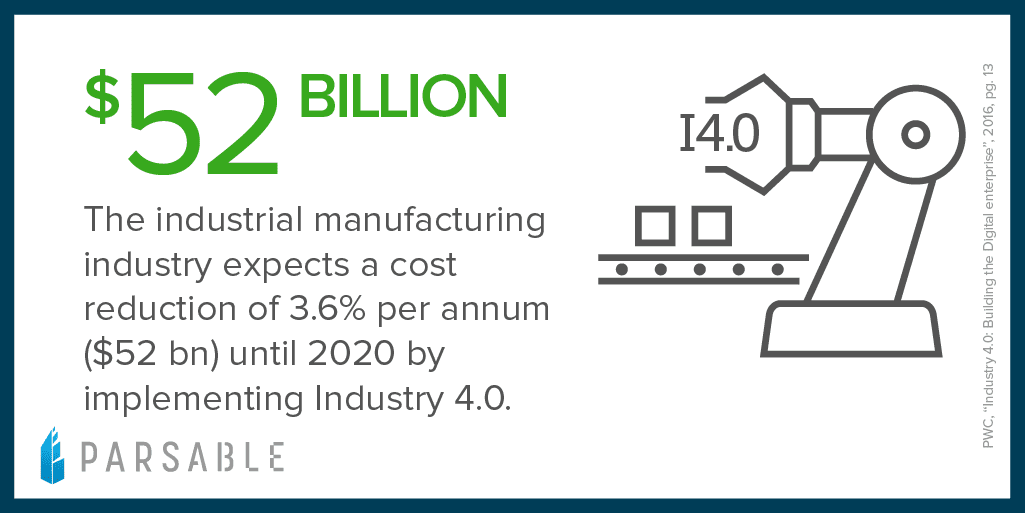
3. Culture
Digital transformation is not a tiny change, it is an entire change to a company’s infrastructure, but it can begin with relatively easy steps (hint: Parsable)
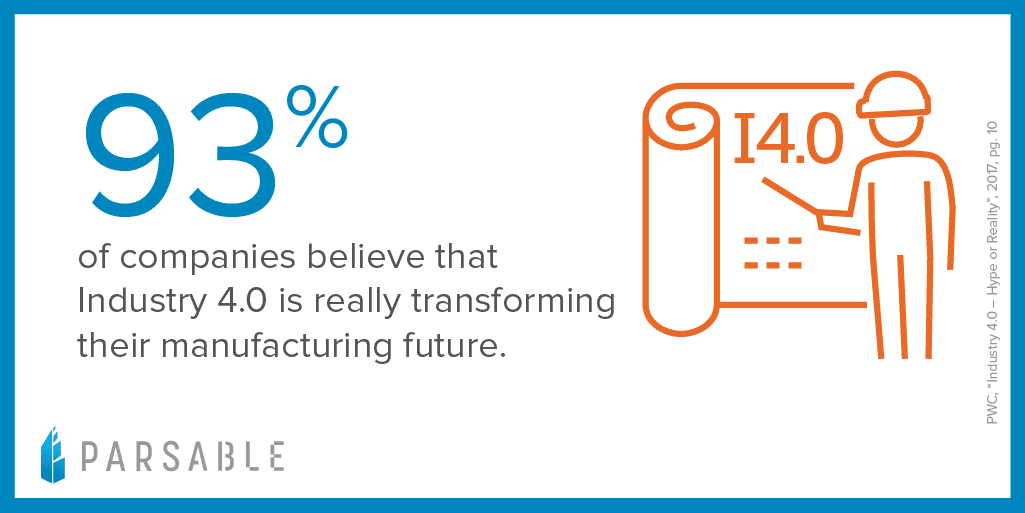
4. Innovation
How are you supposed to innovate without digital transformation? Figuring out those opportunities to digitize is the key to innovation.
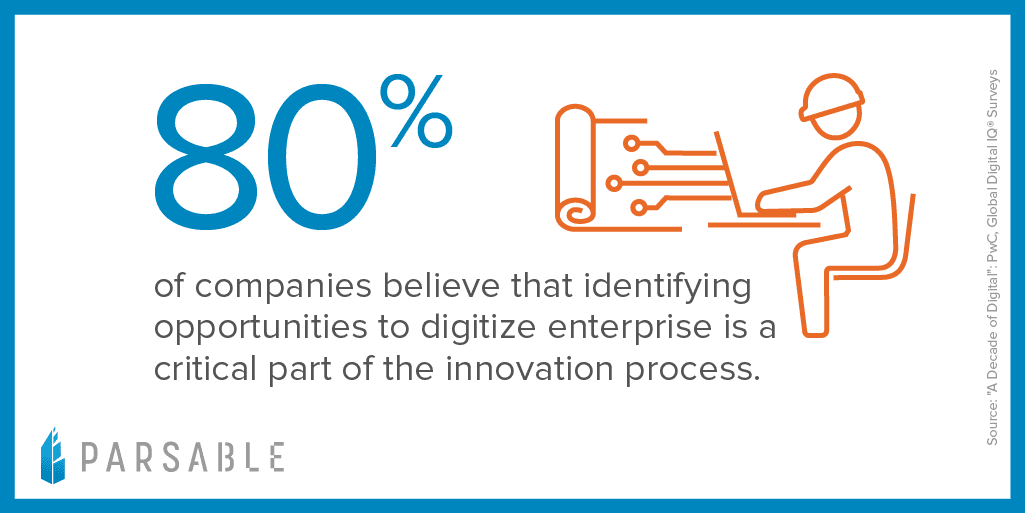
5. Quality
Industry 4.0 precision can catch little details that could reduce product quality.
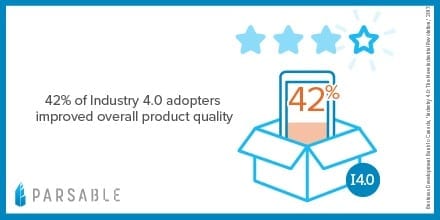
6. Productivity
Between digitizing processes and easier forms of communication, digital technology can help pinpoint certain areas that need improvement.
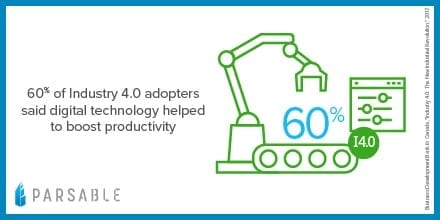
7. Downtime
That is 15.9 hours a week and 63.6 hours a month. Within those 10 minute periods, you don’t realize how much money and productive time you will be wasting in the long-run if you don’t precisely measure it (Hint: Parsable 😉 )
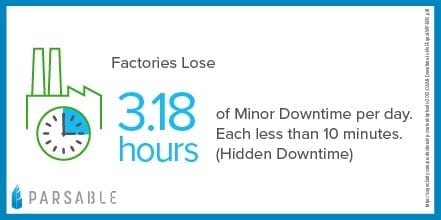
8. ROI
With all of the money and time Industry 4.0 innovation saves, the beginning investment costs can be easily paid back.
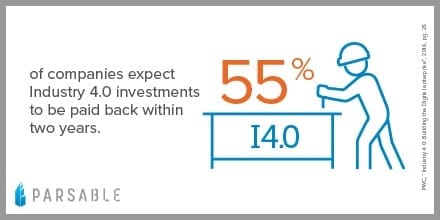
9. Failure
Industry 4.0 technology can help detect potential problems with equipment and processes so you can catch them before it’s too late.
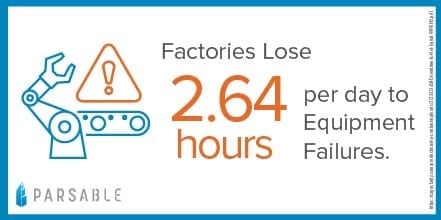
10. Results
Starting your digital transformation doesn’t have to be tedious. Find out how you can get rolling on your path to digital transformation by registering for a demo.
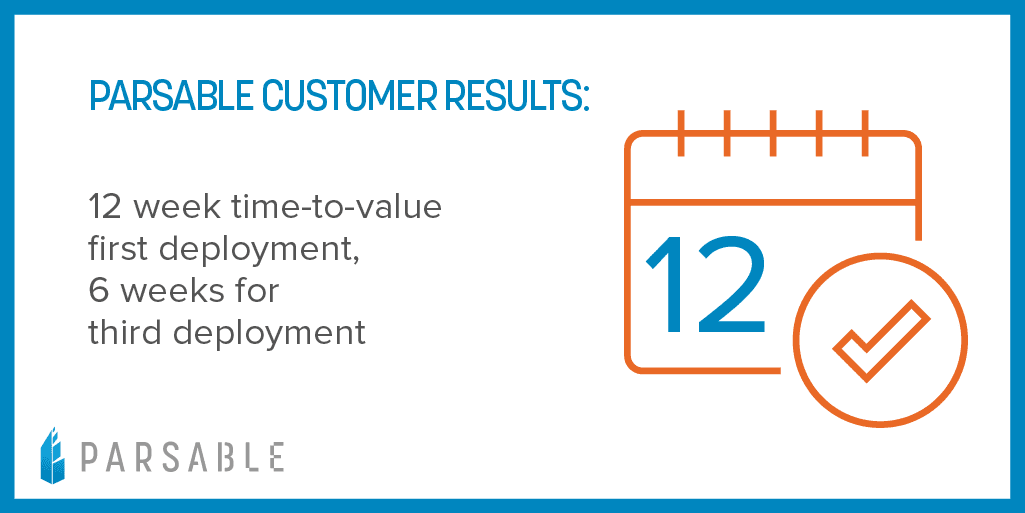