Conagra Brands Improves Quality & Reduces Downtime With Connected Work
THE CHALLENGE
Paper-based work instructions hinder collaboration and do not capture the complexities of various standard operating procedures. Conagra Brands wanted to improve operations at its plants by using a digital, mobile-first approach for its frontline employees to execute work, seek real-time help, access information quickly and collect actionable and accurate data.
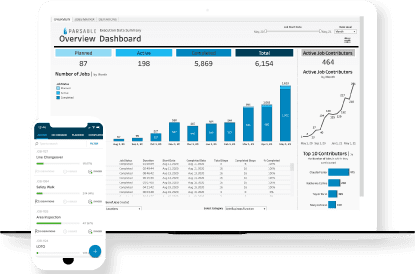
The ACCENTURE + PARSABLE SOLUTION
As part of the Connected Shop Floor initiative, Parsable is the Connected Worker for Operations solution at Conagra Brands’ brand-new, $300-million production facility in Waseca, Minn., with four more sites planned.
Minimal IT Support
- Low-code/no-code platform
- Enterprise interoperability (SAP, etc.)
Quick to Implement
- Clearly defined use cases
- Professional services
Fast to Deploy
- Digitized templates in hours
- Familiar end user experience
Parsable is being used to perform CIL and centerline processes in many areas of the factory, including:
Quality
Enzyme testing
Air cleaning
Size grader
Production
Machine inspections
Clean in place
Vision system
Receiving
Truck/hopper inspections
Conveyor inspections
Sorter/scalper inspections
Shipping
Tote filling
Tote sealing
Tote X-ray
“Before, you would have to leave the floor, go to the shop, log in, etc. With this, if you have it on you, by the time it would have taken you to walk there, you’d already have it done.”
– Corbin P., Maintenance Lead
VALUE DELIVERED
Reduction in downtime
through timely, complete checks/audits performed by digitally connected employees
Empowered associates
who now have the digital tools and skills needed to autonomously run their processes
Reduction in errors
with automated quality triggers, reduced manual inspection, and rapid issue traceability
Improved data quality
resulting in more accurate data for better visualizations, reporting, analytics and insights