How Global CPG Manufacturers Like Grupo Bimbo and Coca-Cola Use Data to Increase Productivity
According to a study conducted by the Manufacturing Leadership Council and discussed in West Monroe’s 2022 Manufacturing Report, CPG manufacturing companies expect their data volume to surge by more than 500% over the next two years. These seemingly limitless data points can be overwhelming unless you have a strategy and the right technologies to turn that data into actionable intelligence.
Solutions like connected worker software are increasingly being used by CPG manufacturers to not only gather data on how work is performed on the factory floor, but to automatically sync that data to business intelligence and analytics tools. The end result? Manufacturing best practices at scale, a more paperless manufacturing environment and more efficient output.
Coca-Cola Europacific Partners Germany, which employs 7,000 people, uses connected worker software to help their frontline workers collaborate more effectively and, by doing so, take their operations and logistics to the next level of productivity.
Similarly, Grupo Bimbo uses connected worker software to achieve the next level of worker occupational safety by implementing digital standard operating procedures (SOPs) and scaling best practices across multiple sites and languages.
CPG manufacturers need to be both offensively and defensively positioned in a rapidly changing supply chain and consumer environment. And data and connected worker technology are at the core of both strategies.
The CPG Manufacturing Landscape: Disruption Meets Optimism
The COVID-19 pandemic has fundamentally shifted expectations and manufacturing best practices around workplace flexibility, employee safety, health and wellness. Coming out of the past few years since 2020, CPG manufacturers have a heightened awareness that disruption and change can happen overnight. Through the pandemic and beyond, the industry has had to navigate higher wages, fuel costs, a talent shortage, sluggish supply chains and material shortages, and accelerated digital expectations by customers and employees.
Recent data shows that for 62% of manufacturers and distributors, hiring is a top challenge. Demographic trends and changing work force preferences are the forces driving this. The Baby Boomer generation is retiring, but they’re not being replaced at the necessary rates by younger workers. This is at least partly due to misperceptions around what manufacturing jobs are like – in a Parsable survey of 1,000 18- to 24-year-olds, 30% were concerned it would be a “low-skilled, manual job” – and the lack of familiarity around what skills are needed to qualify for these roles.
Yet for most organizations, including CPG manufacturers, their people are the most critical asset. As Dr. Fabrizio Salvador, professor of operations management at IE Business School, explains in a Parsable “Conquering Chaos” podcast episode, “people analytics is about understanding what is needed to empower and enable them because they are who will ultimately be bringing the value to your organization.”
Despite all these challenges, research from “The 2022 Outlook: The Future of the Manufacturing Industry” found that the sector is mainly optimistic: 70% of respondents expect organic growth, and 51% intend to introduce new products or services.
Connected worker software can help CPG manufacturers to achieve these growth goals despite increasing external pressures. It enables the optimal use of data across the business, improving staffing and organizational culture in addition to operational measures like productivity, safety and sustainability.
Maximizing Productivity Requires a People-first, Connected Worker Mindset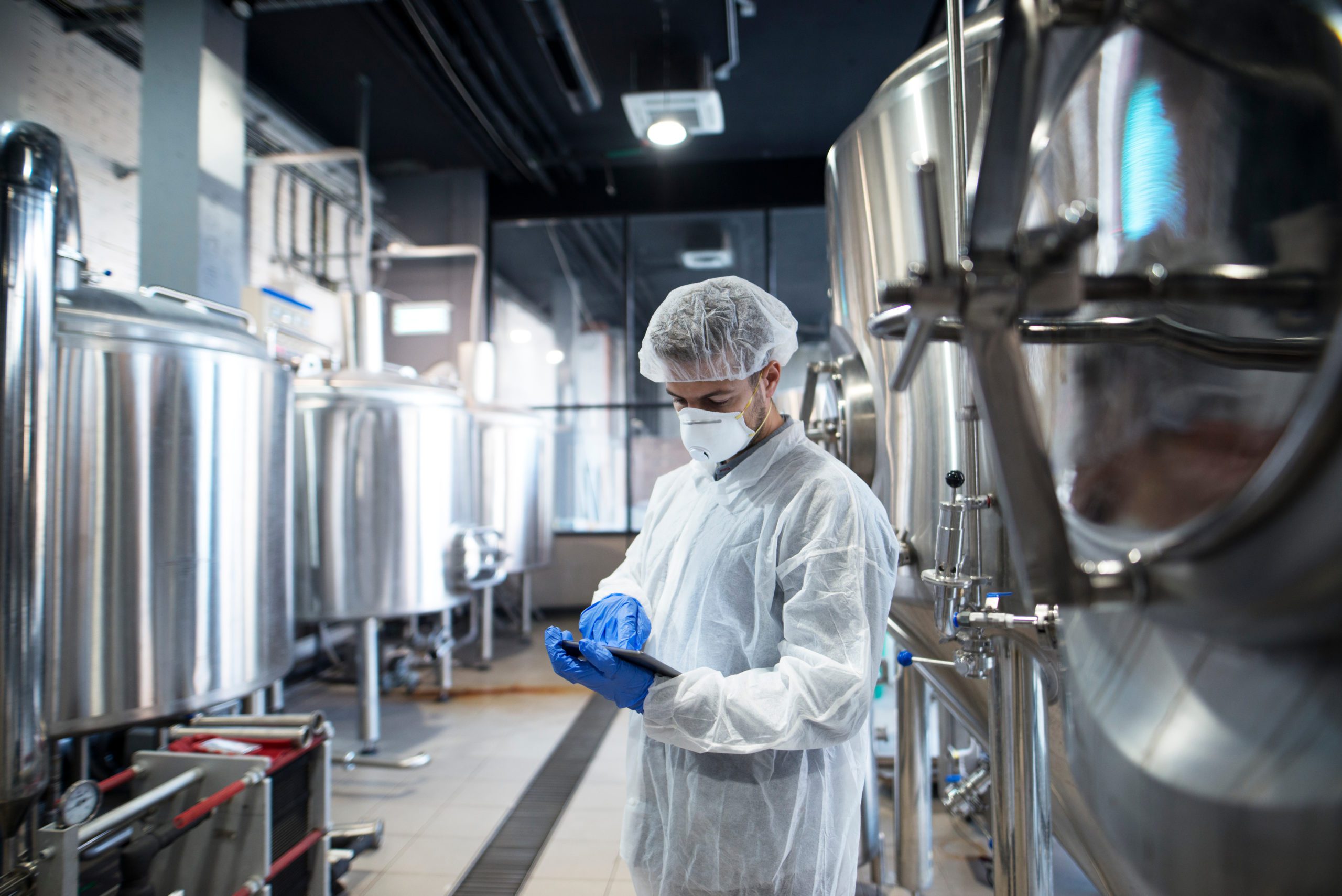
“For the CPG manufacturing sector, connected worker platforms unlock capabilities that represent their offensive and defensive productivity strategy,” says Jaime Urquidi, regional vice president, Americas, and CPG industry lead at Parsable. Urquidi has more than 25 years of experience managing CPG manufacturing facilities at Unilever, Coca-Cola and Procter & Gamble.
“The offensive competitive advantage is that connected worker software helps improve productivity, employee engagement and effectiveness, positioning the company in a talent shortage,” he says. “It also provides the most robust defensive strategy in times of turbulence. Real-time insights help leaders make better decisions faster. They have more assurance that they have the information needed to navigate whatever comes up in the business.”
Leveraging data to maximize productivity is a continuous process for CPG manufacturers. It doesn’t have a deadline or finish line; it’s a never-ending process that should touch every corner of an organization.
Connected worker software is a way for CPG manufacturers to understand and apply their data to improve productivity, increase efficiency, drive profitability, position themselves to be competitive and agile for any disruptions that might arise, and make the most of any new opportunities that may emerge.
Coca-Cola Europacific Partners: Connected Worker Software Improves Plant Productivity and Employee Engagement
Steffen Löser, manager of processes and solutions at Coca-Cola Europacific Partners Germany, is responsible for supply chain processes, further development and standardization. The German facility and team require regular changeovers to meet their multiple production schedules. “They may have to change over three or more times a day, plus cleaning shifts,” he says.
Coca-Cola Europacific Partners Germany has approximately 7,000 employees and, as part of its “Fit for Future” strategy, continuously looks for digital solutions to both better support employees and, at the same time, strengthen the company’s competitiveness.
In 2019, Coca-Cola Europacific Partners Germany launched its initial project with Parsable’s Connected Worker®. It‘s now able to support employees directly with digital work instructions and interactive checklists, ensuring greater adherence to standard procedures.
Specifically, Coca-Cola Europacific Partners Germany uses Parsable in maintenance and quality management, warehousing, transportation, and distribution. As Löser shares, “Parsable contributes above all to the fact that our supply chain continues to function smoothly despite increasing complexity. After all, we can see how much it simplifies employees’ day-to-day work and is correspondingly well adopted.”
(Read the full success story.)
Global Bakery Grupo Bimbo Significantly Improves Worker Safety with Connected Work
Grupo Bimbo is a global Mexico-based CPG company and the largest bakery in the world. It has approximately $15.6 billion in revenue and a presence in more than 30 countries.
Grupo Bimbo wanted to improve its associates’ well-being across 20 plants in 10 countries by digitally standardizing safety procedures, specifically safety incident investigations, safety observations and good safety processes. It implemented Parsable Connected Worker® as part of a holistic upgrade of Bimbo QSR’s occupational safety program.
Data captured by bakery associates using Parsable’s mobile app provided leadership with real-time visibility into safety performance at enterprise-wide, regional and facility-specific levels. The results improved safety across operations.
“Digitizing safety program components using Parsable and analyzing the resulting data has enabled us to make changes proactively before workplace incidents happen, ” says Didier Moleres, vice president of global operations at Grupo Bimbo.
(Read the full success story.)
Connected Worker Software Improves Sustainability
By digitizing paper-based procedures and capturing data on what’s happening on the factory floor, Parsable is also helping CPG manufacturers significantly improve sustainability and energy usage.
For example, one company was able to reduce waste by 10% in three months with the use of connected worker technology and other digital tools. All waste became routinely scanned, tagged, measured, and, where possible, photographed – a prime example of the importance of capturing data and how “you can only improve what you measure.” This eventually resulted in significant financial savings over the course of the year, and the company went from being the highest producer of waste in its country of operation to “best performing” in two years.
Coca-Cola Europacific Partners also is using connected worker technology to reach its sustainability goals, a big one being its commitment to be climate neutral by 2040. Paperless manufacturing – moving work instructions off paper and into an interactive digital format – is one lever. Other effects are far more significant: For example, the start-up and shut-down checklists for the production lines help to reduce consumption of water and electricity, and to save energy in the generation of compressed air.
According to Löser, “Because we perform all checks reliably in Parsable, costs and sustainability-related issues are positively impacted.”
It’s clear that the real-time data provided by connected worker technology makes it significantly easier and faster for CPG manufacturers to identify positive and negative patterns, and implement changes across the business. And by ensuring that frontline workers and teams are part of the process, it helps create a culture of continuous improvement and optimization. Companies that embrace this approach are winning over their competition in productivity, quality, safety and sustainability.
Want to learn more about operational excellence? Read more about the approach that encompasses all of the solutions you’ll need to maximize efficiency, improve worker safety and create a higher standard of production quality.