Manufacturing in the Virtual Age: Exploring XR and AR
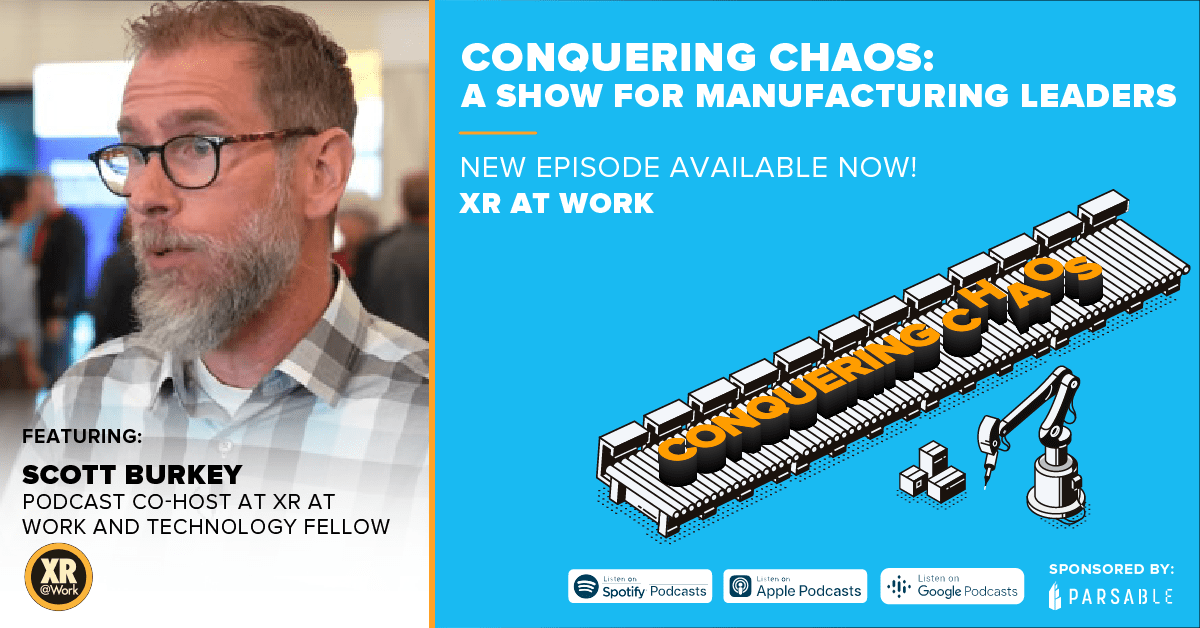
We’re living in a time of innovation. With Industry 4.0 and Digital Transformation on the horizon, new, emerging technologies are taking the industry by storm. Close to the top of that list is Extended Reality. But how much of it is hype and how much is (actual) reality?
In this episode of Conquering Chaos, we delve into the ways in which these technologies are improving the lives of frontline workers and the efficiencies of manufacturers..
We’re joined by fellow podcast host and technology fellow for a global manufacturing company, Scott Burkey. We speak with Scott about how these technologies are being used to improve worker training and implementation. From training simulations to remote troubleshooting, virtual and augmented realities are transforming the experience of frontline workers. We also discuss the potential for these technologies to revolutionize the entire manufacturing process, from design to production to maintenance and more.
Join as we discuss:
- The reality of XR including AR VR, and MR
- The immediate impact on the lives of frontline workers
- How to tap into tribal knowledge with tenured workers to train the next generation
- How extended realities are connecting workers
___________________________________________________________________________________
Experiencing disruption on the frontline? We can help. Request a demo today.

___________________________________________________________________________________
Check out the episode transcript below:
Josh: Welcome back to Conquering Chaos, the show where manufacturing leaders share what they’re doing to improve their operations and how they’re doing it. In this episode, we’re taking a deep dive into extended reality, what it is, and how you can use it to make an impact in manufacturing.
Our guest is Scott Burkey, podcast co-host of XR at Work and a technology fellow at a global manufacturing company. In his role, he brings modern digital technologies to the front lines of manufacturing, spending tons of time working with and learning from frontline workers. If you’re curious about extended reality and what you can do with it in manufacturing, this episode is the one for you. On to the show.
Josh: Scott, welcome to the show. Thanks so much for being here.
Scott: I’m excited. Thanks for having me, buddy.
Josh: I’m glad you were willing to hop on. One, you are one of the few podcast hosts that we’ve also been able to have on our podcast. It’s always exciting to talk to someone who has a podcast, especially within the industries that we’re seeking to serve, manufacturing industry, like industrial organizations as well. Not only that but it’s been great just getting to know you. It was the Smart Manufacturing Food & Beverage conference that you and I were able to connect and start to have conversations and talk with each other. I’ve really enjoyed each conversation so I’m excited to have you here today.
Scott: Thanks. I’m excited about it too. I think how we met each other and our initial conversations were certainly exciting on my side as well. It’s always nice to meet someone else from a home state of Texas and someone I can chew the fat with and just hang out. I’m enjoying our relationship so far, so I’ll try and keep it that way for you as well.
Josh: I promise not to ask any tough questions or argue with you in this. [laughs]
Scott: All right. [laughs]
Josh: No, but I’m excited to talk with you and I know that our audience will be excited to hear from you. You’re a passionate and knowledgeable guy about a subject that I’m also excited by. You’re extremely thoughtful and perceptive. I know that I’m about to learn a couple of things from you.
In this episode today, we’re going to be digging in deep on extended reality, also known as XR, and the impact manufacturers can make on their operations with it. Before we do that, I’d love to get into your background first so that everyone knows why you’re more than qualified to speak to this topic. Right now you are a technology fellow at a global manufacturing company, but that’s not where you started. Tell us about your path. Tell us about how you went from the Marine Corps to where you are now.
Scott: Sure. When I came out of the Marine Corps back in the early ’90s, actually, I was a chef. I worked in restaurants and country clubs, and I hated it. I really hated it. I thought I was going to be a TV celebrity chef and make all this money and be famous. I wasn’t really that good. I’m all right, I can hook something up in the kitchen, but I wasn’t that level good.
I had an opportunity after yet another restaurant closed I was a chef at, and that industry is just terrible, the turnover and just the swirl that happens. I had an opportunity to get out of that and go to work for CNN back in the mid-’90s. Being here in Atlanta, CNN was a big employer. Ted Turner’s a famous guy in Atlanta. I had an opportunity to go to work on CNN and work on cnn.com.
My first job in technology was, I think I probably made $300 a week. Back in my day, that was a lot of money, but $300 a week. All I did, Josh, was I went onto the old– We used to have message boards before Reddit was even a thing. We had message boards and chat rooms, and I would scrub posts on the message board for profanity, and so I would delete cuss words off of CNN’s website. Being a Marine, I know how to identify profanity for sure so it was [laughs] an easy thing for me to spot and laugh at and then remove.
Then I would go into the old IRC chat rooms and moderate chat rooms. We’d have celebrities in and I would kick you out or silence you if you were chatting inappropriate things to celebrities in the chat rooms. It was a pretty fun deal, started off there.
Then someone took the time, and this is a big theme with me, Josh, in my career, is that someone took the time to sit next to me and say, “Hey, let me show you how to write HTML. Let me show you how to build a webpage. We need people to help us with building web pages on this website.” I learned how to do HTML, CSS, and JavaScript. I started building sections of cnn.com out early on, building webpages, and really fell in love with it. I was off to the races.
I was a web developer working on sometimes very large web properties for a living for many years. I built websites for big companies, Coca-Cola, CNN, some other ones, and really had a lot of fun building websites.
Moved into mobile apps. Of course, we know that phones have taken over the world, and the progression there was to move from building web-based applications in a browser to building mobile applications. I moved from websites to mobile apps, I got to work on some, what we call streaming apps, managed our build-out and delivery of apps for TV stations like TBS and TNT, to Roku, Amazon Fire TV, Apple TV, that sort of thing. Really, it’s about putting data and content into different screens, in a browser, on a mobile device, in an app, or to your set-top box, to your TV. Enjoyed that for many years.
What happened really in probably about 2016, 2017, was yet another screen came out, which was the virtual reality headset. They asked me to take and start pushing live television content into VR. I said, “Okay, well, I’ve done browsers, I’ve done mobile apps, I’ve done streaming apps, we can figure this out.”
At the time, my employer Turner Broadcasting managed all the NBA’s digital properties. I worked with the group. We put live NBA games into virtual reality. You could watch NBA on TNT, Thursday night games in a VR headset in your living room, if you’re so inclined to do so. Of course, you can still do that now, but I don’t know about you, Josh, but I’ve got a nice big flat screen in my basement and comfy couch, and I enjoy watching the game that way, but there’s a lot of people, super fans, that love watching NBA games in a virtual reality headset, and more power to them.
We built apps for a lot of the VR headsets, built an application experience for Magic Leap back in probably 2018, and started falling in love, really, with just the thought of being able to do more immersive content and consume content in 360 in a virtual reality headset.
The last thing that happened there, to get me where I’m at now, is that I had an opportunity, I got a call from a recruiter with a big global manufacturing company in Atlanta. They said, “Hey, we’ve got 300 factories around the world and we’re manufacturing consumer products. We want to have someone start to put augmented and virtual reality into our factories, and you’re like the only person we could find in Atlanta that has a technology background and some experience in AR/VR.”
A lot of my friends told me I was nuts. They’re like, “Man, why would you leave the NBA to go to work for a manufacturing company?” No, I don’t see Shaq or Charles in the studio every week in manufacturing, but what I have is I have this huge greenfield playground opportunity to go use XR in a meaningful way to impact frontline workers around the world that are essential to our economy, to our lives. It’s been really rewarding. I put new technology into old factories in a lot of case.
I shared this story with you before, this analogy, which is that my son was asking me, my son’s 18, he was asking me about my job. He’s into cars. He’s a car guy. I said, “Well, what I do, son, is a lot of times it’s like you think about we’ve got a friend, John. John’s got this real old truck.” I said, “Take a look at this real old 1923 Ford truck. One thing it does not have in it is technology. It’s too old. They didn’t have technology back in the 1920s. What I do is I put a new head unit or Bose surround sound stereo system and touchscreen into very old vehicles, very old factories.”
He got it right, that I put cutting-edge immersive technology into old environments that we have in manufacturing. Listen, I’m having a blast. I’ve moved through technology in the last 25 to 27 years and had a lot of fun doing it. Now I sit in a position where I get to do really cool stuff in a really neat industry. I’m very blessed to be where I’m at.
Josh: It sounds like a great experience, both current day as well as your path to get there. You went from cooking up grub to cooking up code, with that code exploring and evolving as the technology evolved. You’ve mentioned going from websites to apps, to streaming apps, that call out of bringing these live television events, these sporting events to VR. I’m actually a huge fan of that. I, like you, consume most of my content on my TV as well, but there is an experience to be had in VR.
I first experienced that, oh, a couple of years ago is when I got an Oculus Quest 2. At the time it was Oculus Quest. Now it’s Meta. Putting that headset on, and even just opening up Netflix, because when you open up Netflix in virtual reality, you’re not just opening up an app. All of a sudden you are on a couch in a cabin. It’s nighttime. There’s a roaring fireplace. You look out the window and there’s snow everywhere. The only thing that’s missing is the smell really of what it would like to be in that environment. Then you’ve got a big screen in front of you, which you can watch it, and that’s just Netflix.
The sporting events like you broke down, I personally believe that is the future of sporting events because now it’s taking as much as you can, that experience of being there and putting you there, either front row seats that you couldn’t find elsewhere, or if you’re like me, you couldn’t afford.
Scott: You can’t afford. Right [crosstalk].
Josh: I cannot afford that. My goodness. It’s not just that, but the potential for as wearable technology matures and that starts to become more and more part of, let’s say athletes’ uniforms or athletic equipment, now what if you’re able to experience the game as the quarterback in the football game is experiencing the game? I think there’s just so much potential. Really cool that you got to do that.
Now, like you mentioned, you’re now in manufacturing and you’ve been there for the past couple of years. It sounds like based off what you’ve shared, you’ve really discovered a passion and a purpose for bringing this type of technology so that it is productively impacting– Productively is maybe the wrong word, but just impacting in a positive way frontline workers. I’d love to hear just a little bit more about that. What about that are you finding to be so fulfilling in your work?
Scott: Oh, yes, man. I can remember the day that I was– Early on. I started where I’m at about four years ago. I remember just a few months in, I was in a factory in North Carolina, and talking to one of the guys. I’m in corporate, of course, but I never want to be the guy that just passes down direction to factories from the ivory tower, so to speak, or from the home office or from my home office. I spent a lot of time out in the factories, Josh.
I remember I was out in the factory talking this guy. A pallet would come down– Actually, a robot would drop a pallet off on what we call a shrink wrapper. They put shrink wrap around a pallet of boxes. We call them cartons. His job was to check and make sure that all the cartons on that pallet were the same product before it got shrink-wrapped and shipped out.
I was talking to this guy super nice, and I’m like, “Hey, how tough is this job?” He’s like, “It’s not super tough, but it’s a little taxing.” I said, “What are you most worried about with this job? Is it getting hurt? Is it safety issues?” He says, “No. What I have to do now, Scott, is when a pallet comes up, I have a number.” I think it was an eight-digit number. He says, “I’ve got a number on a piece of paper on a clipboard, and I’ve got to take that number and I’ve got to go make sure that every box on that pallet–” Typically, there’s 14 to 20-something cartons on a pallet. He says, “I’ve got to memorize that number and I’ve got to walk that pallet, and I’ve got to make sure that all the numbers are the same. I’m deathly afraid that I’m going to make a mistake.”
If I were to give you an eight-digit number, Josh, and then say, “Hey, hold that in memory, and then now walk this pallet and make sure all these boxes have that same number on it,” your mind starts to play tricks on you and it gets polarized, confusing. He says, “I’m deathly afraid that I’m going to make a mistake, ship something out. We’re going to have what’s called a recall, meaning our customer or in-consumer has an allergic reaction because they got the wrong product and they have a peanut allergy. Now there’s a recall, there’s a pushback, and we get sued.”
He says, “I’m afraid of losing my job because I can’t memorize a number, check it against 20 instances of it correctly, and then do that several hundred times a day.” This poor guy has to memorize hundreds of numbers and check it on thousands and tens of thousands of boxes, and it gets to be confusing.
He says, “Dude, I got three kids at home and a wife. I don’t want to lose my job because of that.” That light bulb went off for me, Josh. It was like, “Hey, what if you had a camera you wore on your head that allowed you to scan those numbers, and it either gave you a green check mark or a red X if the pallet matched out or not, and it takes all of that memorization off of you and puts it onto the computer.”
You’d have thought that I had just given the guy a million dollars, man. It was like this big light bulb moment. It’s not so much that I had given him something cool, but I had taken away this fear that he had, potentially going to take away this fear of his that he was going to lose his job because he couldn’t do some superhuman memorization Jedi mind trick 1,000 times a day.
That was the moment where I said, “You know what? This is going to be a really cool job because I want to be able to have an impact in a positive way on not just how people do their job, but how they feed their families, man, and how they provide for their wife and kids or their husband and children.”
We put that solution in place, helped that guy out. That solution’s still in place today. That was the big moment for me where I was like, “All right, forget pro basketball. This is it. This is what I want to do, frankly, for the rest of my career.” Of course, at 78 years old, I don’t have long time left, but I’ve got a few years left in my career and I could do this forever, man. That human element, Josh, that to me is like I’d do this for free. I’m glad they pay me for it, but I would do it for free because it’s just so cool to be able to work with these guys one-on-one.
Josh: That’s such a great story. One of the biggest reasons I love it, not just because I think you did a great job of really articulating that, when you’re impacting an individual’s life, you’re impacting others’ lives as well. I love that you called that out. Really, where my mind went while you were talking about this, some of the questions I had was, my goodness, how long has this guy been having to do that and the people that were doing it before him? Was that just one line? Are there other people on multiple lines going through that same experience?
Then you start to multiply that at different factories and across different companies because you know that no one’s really figured this out and solved this problem. All of this technology is still in the emerging state, in the early adoption side of things. I love that you brought it up because when you first hear it, it sounds very tiny. We’re talking about solving a problem of just somebody checking numbers on boxes.
I think sometimes people get caught up on these big changes that have to happen in order to justify the use of technology or bringing in technology, but what you just broke down, not only is it impacting that individual, it’s taken a fear off of them. Now, I’m probably not going to be as stressed as an individual. That stress isn’t going to carry over to when I come home, in whatever ways it manifests.
Not only that, but that’s going to open up the opportunity to be more engaged, to be an employee that ultimately doesn’t leave because he’s so stressed out because of this fear, because of these unrealistic expectations that have been placed on him. There’s an impact there of solving that problem for that individual, but there’s also a productivity gain.
The act of checking numbers, the act of that individual spending so much time doing this, I understand it’s the best way that was available at the time to mitigate this risk. I get that, but let’s agree that that is a non-value-added activity. That is an inefficient use of time from a productivity perspective. I bring that out because there’s definitely a soft impact that cannot be overlooked, and 100%, a hard impact that can’t be overlooked. That was such a great story. I appreciate you sharing that.
Scott: It’s interesting because you bring this up, Josh. I have fallen prey to this thinking in the past that I hear a lot of men and women suffer from, which is this notion of, “Man, I’m going to go in and we’re going to do lights-out manufacturing. It’s going to be robots everywhere and XR. We’re going to do away with humans in factories.”
It’s like, “No, we’re not. Come on.” If you can just go impact little small things, it does have such a cascading effect because one number being missed causes sometimes a lawsuit. Someone gets hurt, someone goes to a hospital because you mixed products up and they ate something they weren’t supposed to eat because we manufacture a lot of food packaging.
I asked, what’s the typical payout we have on, we call a recall? It’s a ton of money. It’s a lot of money that we have to pay. It could be solved by a tablet, a head-mounted device, heck, a barcode scanner. It doesn’t have to be XR, just whatever’s going to give that worker better accuracy and more confidence and keep the mental fatigue from setting in. It has a lot of impact, soft and hard. You’re right.
Josh: I completely agree with you on that idea of lights-out manufacturing. It’s certainly doable for certain factories and certain industries because it has been done to a degree. People are still required. Sure, maybe long enough on the timeline, this’ll be something that happens. We’re talking about maybe when you’re actually 78 years old, because [laughs] you are nowhere near 78 right now. Maybe on that timeline, but the here and now, it’s really about focusing on what you can do today.
Your focus, a lot of that centers around XR, but not everyone knows what exactly XR is. I’d love for you to take it very basic for us. How do you define XR?
Scott: XR is an umbrella term for all of the Rs. Now, you get into more acronyms, AR, VR, MR. Augmented reality is taking virtual objects and putting them in your field of view in your first world, in your first reality. We think Pokémon GO, we think Snapchat filters, we think anything that shows up on a screen that you’re looking at or looking through and that thing that shows up as virtual. Some sort of animation that shows up on top of a screen or a lens you’re looking at or through. That’s augmented reality.
Virtual reality, of course, is a totally immersive environment. You are no longer looking at your physical environment. When you’re in a VR headset, you don’t see outside that headset typically. There’s exceptions, but a totally immersive virtual reality application is virtual reality.
When you look at augmented reality that you’re either wearing or holding, virtual reality that you’re wearing, those two things together, we just call this XR. We could get into mixed reality as well and what that means. XR is just the umbrella term for anything other than what we’re all doing right now, which is looking at our offices, or bedrooms in first world. XR is just an umbrella term for that. It means we’re extending people’s reality beyond what they typically see and interact with.
Josh: XR, extended reality, consisting of augmented reality, virtual reality, and mixed reality. To be honest, I’m not 100% sure of what the difference is between mixed reality and augmented reality. Would you mind just breaking that down for me?
Scott: Absolutely. The way I look at mixed reality, and I talk to a lot of people about this, there’s a couple of different camps. Typically, what I would tell you because you’re asking me, I’m on the show today, so I get to answer this, my perspective on mixed reality is we start to do two things with augmented reality. If I’ve got a tablet, I’m looking through it at my bedroom or my office. Augmented reality would be a penguin standing on the floor in my bedroom. That’s AR.
Now, if that penguin walks over and climbs into a drawer of a desk and shuts the drawer and you can no longer see it, that’s mixed reality. We’re starting to take a virtual object and it’s starting to interact with my first world. There’s obfuscation. The penguin can walk behind the bed. The penguin can jump up on a table, climb inside of a box and you can’t see it any longer. That’s one aspect of mixed reality.
Another aspect would be if that penguin was wearing, let’s just say, a necklace, and on the necklace, it showed you what that penguin’s heartbeat is. I’m using a real sophomoric example here, aren’t I? When that penguin walks over to your TV, it can turn on your TV or it can turn it off. It can turn the volume up and down. It starts to interact with things in your physical space.
The way we equate that to manufacturing is, mixed reality is when I can take and get information about a machine that’s in my factory, I can get that information from the machine to the cloud down to my device in real-time. I can look at a machine through a tablet in AR and I can see runtime, temperature, that sort of thing about the machine because that data’s being pushed from that first-world object to the cloud down to my tablet or head-mounted device. That’s where we start to get into mixed reality. We start to mix all the above, so to speak. It’s next-level stuff, man. [chuckles]
Josh: I know. Sign me up. I love that idea. Just to make sure that I’m interpreting it all correctly, really, when we’re talking about augmented reality, that’s bringing the digital world into our periphery, basically, something that we can see, but we’re still existing in our environment. Virtual reality, you’re existing and experiencing the virtual environment. Mixed reality is when the virtual environment has a tangible impact on the physical reality that you are in. It’s not just a view or interactions purely happening in the digital side. It’s that digital interaction is affecting the physical interaction as well.
Scott: That’s right. That virtual object can impact your first world and it can also be impacted by your first world.
Josh: I just have to do this. [makes noise] That is my mind being this blown.
Scott: It’s nuts, man.
Josh: That is crazy. Now, that gets me excited. I feel I want to see it, I want to try it, I want to use it.
Scott: Sure.
Josh: That is very much the buzz, the feeling of buzz, the feeling of hype. There’s a lot of that tied around extended reality. You have practical, actual experience of bringing extended reality solutions into manufacturing environments, and not just one or two, but factories across the world. The buzz surrounding extended reality, how much of that is hype?
Scott: A lot of it, man. There’s so much hype going on out there. It’s maddening for people like myself who are responsible for helping that poor guy with his pallet.
The hype, you can’t stop it. We can’t help it, right? It’s certainly out there. We’ve all seen Marvel movies, we’ve seen Jarvis and, the glasses that Spider-Man wears, and there’s all this cool stuff that’s out there. There’s YouTube videos, and there are things that get our stakeholders hyped up. I end up being the one to try to readjust them onto reality, not just the reality of what we can do, but the reality of what we should do. Could I put someone in a suit that talks to them and has AR overlays on the screen and they walk around? Yes, we could. Money solves that problem. Should we? No, we shouldn’t.
I get asked this a lot. Internal stakeholders, Josh, will say to me, I’ll be speaking at internal meeting, or I’ll just be on stage somewhere and somebody’ll say, “Mr. Burkey, what do you think about the metaverse? I saw this on YouTube and I saw this on a movie, and I saw this on the internet, shouldn’t we be doing this?”
What I say time and time again– and I try to be professional with it, Josh, but what I say time and time again is, especially if I’m talking to an internal stakeholder, that say, “You know what? We have work instructions in our factories written in Sharpie on a piece of cardboard duct taped to the wall.” That’s how we train our factory workers.
I think we need to fix some of this before we start worrying about Ready Player One happening inside of our factories. There’s enough low-hanging fruit and immediate value that XR can bring that that’s where I’m focusing on, is how to get people more productive, keep machines running, keep everyone safe at the end of the day. That’s my concern.
It’s not about the cool stuff that we could do, because there’s a metric crap ton of things we could do. Let’s look at what we should do and what can have an immediate impact on the efficiency and productivity and safety of our frontline workers. That’s where I live.
I get it. We have executives that go to software companies, customer experience, showrooms in different big cities, and they get all hyped up and they come back and go, “Burkey, we need this in our factories.”
It’s like, guess what? There’s a big difference between that customer experience lab you were in in Boston or New York, and what actually happens at our plants out in rural South Dakota. There’s a big difference there in internet connectivity and lighting and no ambient noise level and that sort of thing. You can’t take this hype and go try to copy and paste it down into industrial environments all the time. It doesn’t work, and we need to live in reality.
I battle a lot of that, but I’ll tell you this, I wanted to make sure that I use this phrase at least once in our conversation today. The tech is the easy part. It’s the human side of this that really separates the amateurs from the pros, in my opinion, Josh. If you don’t take a very pragmatic, realistic, simplistic, humanistic approach to the use of technology in industrial environments, you’re going to be in trouble because this isn’t fantasy land that these folks are working in out there.
It’s real, dangerous, loud, hot, dirty environments. We need to take a pragmatic approach. We need to always be asking questions and understanding what it’s like to be a deskless worker and a factory, and we need to meet their needs, not try to copy and paste the metaverse into their job. It doesn’t work that way.
With that, I will drop the mic and walk off stage.
Josh: [laughs]
Scott: Thank you. [laughs]
Josh: There’s so much–
Scott: You got me started
Josh: I’m glad I did. There’s so much to unpack there [crosstalk].
Scott: I’ve got an opinion.
Josh: Good. That is what outlets this are for. What I love is that your opinion is coming from a place of education, and by that, it’s not just your technical background, but it’s your experience too of actually doing this and finding the things that solve the problem. Far too often, I’ve seen this as well, and to be honest, one of the reasons I’m not a huge fan of the current state of smart glasses, which maybe we could we’ll get into, but it’s that idea of it demos well in a conference room. It absolutely does, and like you called out, it’s a totally different environment.
It’s great to be hyped up and excited about the potential that this technology can bring, but when exploring extended reality, you still have to live and make decisions in actual reality.
Now, some of the things you described with that idea of hype, I had some questions come to mind.
As I was listening, some of the questions I– Well, really it’s one question, and the answer’s probably a little bit of all of this, but when we say it’s more hype than reality, is that due to– I heard a little bit about expectations of the people seeking to use the technology or excited about the technology, and I heard some things, really, about, is the industry or is our specific company ready for the technology? Then I had some questions. Is it marketing where this technology is being hyped up, but the technology itself, the maturity of technology isn’t actually ready for prime time? What’s been your experience?
Scott: I have a very strong set of thoughts on this, Josh. People will ask me a lot, is augmented and virtual reality, is it ready for manufacturing? Is manufacturing ready for XR? I can emphatically say absolutely on both accounts, and I’ll tell you why.
If you look at the consumer metaverse, is that ready for manufacturing? No. Is manufacturing ready for that? No, it doesn’t make any sense. If you start to come back off of that some, we talk about the industrial metaverse, we talk about remote collaboration or remote expert calls, and we talk about spatial-guided workflows. We start to see in this industrial metaverse, in this industrial ecosystem of technology, there’s absolutely–
I don’t care who you are. I talk to a lot of people all the time in manufacturing, oil and gas, healthcare, hospitality. They ask me, “What should I start with?” I can emphatically tell you that if we sit and look at your environment and you think about your company, look at your problems, really try to understand where the needs lie, I will guarantee you there is some particular aspect of extended reality technology that could be deployed in your shop, and it would have a positive impact on recruiting, training, retention, OEE, overall equipment efficiency, reduction in unplanned downtime, reduction in time to repair. Absolutely.
There is something, if we take all the stuff that could happen and your problem, we can find something and you can find something, but you’re going to have to get real, and you’re going to have to be willing to try some things and start small.
I’ve seen over the years and recently a lot, Josh, where a small-ish company with three plants, there’s an opportunity for XR to impact their operations and their revenues and their training and their safety. Of course, and I work for a company that has 300 plants, and we absolutely have 100 times that opportunity. It doesn’t matter what you’re doing. There’s probably something there that’s going to have a positive impact for you.
Now, listen, I’ll say this and I’ll leave you on this thought on this topic, Josh, but it’s not always XR. I don’t always come out of a factory after a couple of days and go start ordering devices, ship in, and go start training people on how to use a HoloLens 2 or start building a virtual reality application. Sometimes the answer for their problem, it’s not best solved by XR. I’m not in the business of selling technology into factories for my employer. I’m in the business as it were of trying to sort out whether or not this is an XR problem to solve or not. If it’s not, there are other people that can help you with refining that process or doing a better job with whatever your problem is. If it’s XR, I’m your man. We’re going to take a very pragmatic, simple approach.
I want to do what’s best for the company. Anyone in my shoes that’s listening to this today, that’s maybe thinking about dipping their toe in the water and XR and manufacturing in particular, I would say start small, be realistic. Have your ears to the ground of what’s needed in your facilities. Just block out all the noise and hype. Don’t be trying to do stuff because it’s cool. Do stuff that’s going to have an impact and give that guy confidence that he can do his job without losing it and being unemployed. That’s where you want to be. If you get it down to a very humanistic approach, all that hype and everything, it’s fun to look at. It’s like candy. You can’t survive off candy three meals a day, you got to have some meat.
Josh: My takeaway from what you said is that XR is ready to be used in manufacturing, and manufacturing is ready to use XR, which is a great takeaway for everyone listening. It really comes down to, like you said, what are the problems that need to be solved? Not only can they be solved by XR, but are you going to get the most value out of them by doing it this way? Because essentially, what you’re describing, Scott, is not pursuing tech for the sake of tech, because that’s going to set everyone up for failure.
That reminds me of an example, I was working with a very large consulting firm, and they were talking me through, this was on behalf of– first of all, we were talking about how we could work together. They were talking to me through the idea that they had to solve this, I’m going to describe it as a logistics problem a particular company was having. The ultimate issue that they were looking to solve for was the fact that when these trucks would arrive and drop off these containers, they couldn’t find the containers after they got dropped off because there wasn’t really any system of organization to it.
What they were wanting to explore with technology is, could we set up video cameras so that as the truck is pulling up, it reads the license plate and the number on the container and then there’s geotagging and different things so that you always know where it is? My question to them was like, “What if we painted lines on the ground and numbered them and people told them to go park in that spot?” They were like, “Well, that is an alternative.” That was just such a great moment of we were like over solutioning it.
[chuckles]
Scott: Imagine that.
Josh: Just bring a system to tell them where to park. I think that just echoes that idea of like, we can make things super cool and fancy, but really too complicated to really provide the value that’s needed, but it comes back down to understanding what the problem is that needs to be solved and identifying the best way to solve that problem. I’d love to hear from you, Scott, what are the most common obstacles that you see manufacturers facing that they can overcome with XR?
Scott: There’s a couple of things that I see happening a lot in manufacturing. I would imagine that a lot of industrial enterprise organizations are seeing this. I’ll give you a three for thought. Number one thing that I see that XR has had a positive impact is this whole notion of, and your light bulb’s going to go off when I say this because everyone knows it. It’s this tribal knowledge that exists in the heads of an aging workforce. That’s a huge issue when you have 30% of your workforce is over the age of 60.
They’ve had stuff in their head for 30, 40 years and they’re about to retire, or they’re going to go fishing and never come back or they’re going to have health concerns, health issues and maybe they’re not even the right person to be training younger workers. Now we have all this tribal knowledge that’s super valuable in the heads of veteran workers. That’s the number one thing that keeps us up at night, as it were, that we have started using XR to help solve.
Here’s another thing that we’ve used XR to help solve, which is a lot of companies have poor standards for how to do things, how to do procedures or processes. If I need to lock out a machine, it’s 17 steps to do it. I’ve to get it memorized or I don’t. If I have it memorized, great. Is that our training method now is to just teach everyone to memorize it? What a spiral downward that is.
If it’s not memorized, giving people the ability to reference information in a portable way on the factory floor that gives them no more or no less than the reference information they need at the time and place they need it, that’s what XR is doing. That’s how we’re deploying it. Here’s how you do it the right way so that nobody gets hurt. Taking our training standards and making sure that everyone’s on the same page and that it’s in a way that everyone, and I mean everyone, can consume and digest and refer to on a device that’s easy to use, easy to operate, that is another big thing.
You’ve got tribal knowledge that’s stuck in people’s heads. How do we get that out? How do we then take this and standardize this and make this accessible and easy to digest and access by a distributed workforce? Then really, all this speaks to, we’re trying to train Gen Z workers like workers were trained back in the 1960s or ’70s or ’80s. What we end up with a lot in manufacturing right now is we end up with crabby old Joe who knows how to do everything, that doesn’t write anything down.
He’s about to retire. He tries to tell the new folks how to do it. They can’t memorize it. They’re afraid to ask questions at 3:00 in the morning when Joe’s sleeping and they’re on the floor and the machine goes down. So they just try to figure it out themselves and somebody gets hurt, or the machine gets broken. This is a breakdown. This is what’s happened for years, from what I’ve seen.
I don’t come from a manufacturing background, Josh, but I’ve seen this in the last four years where that happens time and time again. I’m 21 years old, 22 years old, it’s 3:00 in the morning. I don’t know how to fix this machine. I’m afraid to call crabby old Joe and wake him up because he’s going to yell at me or I’m going to be seen as incompetent. Man, if I don’t get this machine back up and running, the supervisor in the morning’s going to have an issue because we didn’t hit our production goal on the overnight shift, so I’m just going to wing it.
Winging it is not the thing you should be doing when you’re repairing a multimillion-dollar dangerous piece of equipment at 3:00 in the morning in South Dakota. That’s how people get hurt. This whole notion of knowledge transfer and training effectively for a younger, different workforce in Gen Z, that’s the job number one of what we’re doing in XR in my role right now. That’s a lot. I’m sorry to throw up all over you all with that.
Josh: By no means was it a lot. In fact, I think it could probably be its own potential episode where we spend an hour, two hours, three hours talking about each individual one of those, especially with the stories that you had. This is just a recap. Tribal knowledge, poor standards with really essentially internalizing knowledge. Then the approach to training. All of those being difficulties that are experienced day in and day out within manufacturing that XR could be something to solve, and I completely agree.
One of our recent episodes we explored this idea of really, and I think this is kind of echoing what you said is there are silos preventing people from accessing the information they need when they need it so that they can make the right decision or take the right action. Not only do they need to be able to access that information, they need to be able to consume that information.
Like you said, sometimes that information is siloed into the heads of the guy that’s sleeping at 3:00 a.m. That’s a silo. That’s something that’s preventing people from getting the information they need right when they need it. Sometimes that information is stored in another system and, like you called out earlier, without an on-the-go digital way of interacting with that system, now you’re siloed. Now you don’t get the benefit of that information because you’re nowhere near a place where you can actually tap into it and consume it.
Really, I love that we have our different ways of putting it, but there’s just this idea of, it’s about making sure that people get the information they need when they need it in the way that they can consume it. That is ultimately what’s going to help solve some of these things that you talked about. Tribal knowledge, the poor standards, the inefficient way of moving onto training.
Now, knowing that these are problems, let’s talk about the impact of it. What have you seen the impact be if left unchecked?
Scott: Left unchecked, you start to have valuable knowledge walk out of your factory never to return. Tribal knowledge. Turnover kills companies. Turnover is a terrible thing. Even if someone gives two weeks’ notice and leaves, you can’t get all of that knowledge out of them in two weeks. Turnover, it’s a natural thing, but it’s also been accelerated in the last couple of years where we don’t just have veteran workers leaving, we’ve got people three days on the job going, all right, forget this, I’m out of here. When people leave your company, they’ve been there 30 years, or they’ve been there three days, it has a negative impact on your business in some way, shape or form, hard or soft. It has a negative impact on morale, a negative impact on your training budget, on the time it takes.
We see a lot of this. I just learned about this recently, Josh, that a lot of people in manufacturing will tell you that training new employees, it’s not just the time to train them, but training them on the machine, what they make during training is not a usable product. It tends to be, the first 100 times they run it, it’s garbage. It goes in the trash or gets recycled. There’s a lot of waste that happens during training, hard, tangible waste of goods and materials. When people walk out of your factories, it has a negative impact on a lot of things because they take that knowledge, and you have to go recreate that.
I’ll tell you a big thing that happens if you don’t do these things, again, it doesn’t have to be XR but do something. The big thing that people like to talk about, but people don’t want to really dig in a lot of times is on safety. People get hurt in ruggedized industrial environments all the time due to lack of proper training and support. They’re afraid to ask for help. They don’t know how to reference the information, so they do my favorite phrase there, they wing it. Winging it gets people hurt. There’s a loss of throughput. There’s a loss of productivity. There’s people that just get hurt when they’re guessing how to do stuff. There’s a soft cost that you’re going to experience, that you’re probably already experiencing in manufacturing if you’re not effectively training new workers. That is recruiting and retention.
I learned this from the Conquering Chaos podcast. You did an episode a while back, Josh, where you talked about all these people in a manufacturing survey that said, I need technology and I’m not getting exposure to it, and I’m thinking about leaving because of that. I want to work somewhere as a 21-year-old in 2023. I need, and I demand, and I expect technology to be involved in my training and support in some way, shape or fashion. If it’s not, even if they don’t tell you they’re thinking about leaving–
I’ve got four Gen Z kids and they don’t know how to operate a three-ring binder. They don’t know how to pinch and zoom those grainy pictures on a piece of paper. They don’t do well with crabby old Joe. They got crabby old dad, and so they delight in technology. Recruiting and retention suffers with Gen Z workers and millennial workers if we’re not using technology. It’s kind of table stakes anymore. There’s a lot of gloom and doom there in that, Josh, but there’s nowhere to go but up by putting some digital solutions in place to help with the training and retention and support of your younger workers.
Josh: Absolutely. The episode that you referenced was when my colleague, Jaime, and I went through our annual state of the connected manufacturing frontline worker to really understand what are frontline workers’ perspectives on the use of technology. What’s the reality that they’re working with? How do they use it? Do they have access? et cetera.
We asked a ton of different questions to over, I want to say over 1,400 different frontline individuals in manufacturing, specifically in various age groups.
The finding that you’re referring to was that over half of workers between the ages of, I might get this number wrong, 18 to, I want to say, either 45 or 54. I know that’s a big gap, but it was somewhere in that range. Over half of them cited that technology would be a motivator for considering moving to a different employer. That has ramifications within the industry. The workforce is already a tough topic for manufacturers to deal with, and to know that by embracing and utilizing technology, that’s going to provide a competitive advantage in the sense of recruiting people and retaining people. That’s a big deal to think about, especially with the future goals.
Another finding from that particular survey was that over 80% still rely on paper to access work instructions and track and log the work that they’re doing. Really what they’re saying is like, most of the work that I do that I have to either consume information about or report information on, I have to use this paper and what I would really like to do is use something else.
I think that was such a great thing to call out, and I appreciate you referencing. It’s always great to talk with people who listen to this show as well. Thank you.
Scott: Oh, yes. That was a great episode and a great study. Thanks for doing that. Would you do another one every year, please?
Josh: Yes.
Scott: We would all appreciate that. [laughs]
Josh: Oh, yes. We’d love to. I think the more that we can really tap into, what do people actually think and feel? I think a lot of times, and you alluded to this, sometimes decisions are made about what’s best for people without actually knowing what people want or are experiencing or need. That’s the old way of doing things because now with all the different technologies, not just the technologies for frontline workers, but all of the technologies make it easier to access the information you need to make the best decision possible.
The episode that came out before this one, we talked with an individual, well, the CEO of a company called WorkStep, and their technology focuses on really just a pulse check on the frontline. What are your people thinking, feeling, experiencing? et cetera. Using those data points, management will be better able to predict what is going to be a driver of turnover, and then work to prevent that.
They released anonymized data of their findings, and what they found was, while technology was absolutely on that list, tools in particular was on that list, it wasn’t as highly rated as the more human elements. The top-rated things were; I want to feel heard, I want career growth, I want to know that I’m valued. I want to be paid in a way that I think I deserve to be paid. All very individual, I’m a human, I need to be taken care of, and I’ve got people that I need to take care of, or I’ve got a life that I want to live outside of work, and I need to be able to do that, and I need to stay safe. I think it’s interesting. I love that you brought it up. Technology is certainly a factor, but back to the point that you made earlier, it’s really about focusing on doing what’s best for the people.
Scott: Absolutely. I love when we have doughnuts in the break room, but doughnuts in the break room cannot be the only way my employer tries to motivate and retain me, you know?
Josh: Yes.
Scott: Unfortunately, it’s a lazy thing that a lot of people do. I love doughnuts. I’m guessing maybe you do too, Josh. Who doesn’t, right?
Josh: Oh, man. Can you tell?
Scott: I didn’t say anything, but if that’s what you’re trying to do instead of having actual conversations with your people and meeting their needs in a way that’s going to have a positive impact on their health and wellness and security and confidence, you’re just being lazy. That’s a cheap way out.
Josh: Look, I have no idea if technology will solve that as well. Maybe instead of having to have conversations with your people, artificial characters in the metaverse will check in and provide coaching using artificial intelligence. I don’t know, maybe that’s the future. [laughs]
Scott: Maybe.
Josh: Well, look, I know that one of the things I really wanted to hear from you and give you an opportunity to talk about was, you’ve done a lot of work in manufacturing with XR. I love that you’re not just studying the technology in an ivory tower, you’re going to different factories, you’re listening to and learning from people in all different roles within manufacturing operations. I’d love to hear from you, what are some of the innovations or implementations of XR in manufacturing that you are most proud of?
Scott: We’ve done a couple of things in the last couple of years that I’ve been surprised by, and we’ve done a good job at. I’m proud of it not because it’s cool, but because it’s having a positive impact, again, on our frontline workers. You know what a 360 tour of a house looks like? You see this on Zillow where you walk through a home and you can stop and look around and click through and look 360. They went and just shot the inside of that house with a 360 camera and stitch the images together. We started doing that in our factories during COVID and it gave us a way to show customers and other employees the inside of our factories without them having to travel and without them having to come into a sealed-off environment during COVID.
We started doing 360 walkthroughs of factories and somebody had the idea, I wish it was mine, it wasn’t, but it doesn’t matter, it’s a good idea. The idea was, “Hey, what if we just did a 360 of a machine, one machine on one line, and instead of having little pop-ups on top of the machine at different points that tell you what the different parts are, what if you could click on those and you could get more information and you could dig deeper and you could see a video of what is happening on the inside of the machine? Or you could start to get images, pictures, documents, text.” We started doing that.
We started doing what we call 360 training experiences for a particular machine. Any given machine that we have at one of our factories, I guarantee you it’s in somewhere between 5 and 50 other factories because we buy a lot of the same machine. Then we started taking and say, okay, so what if we took that 360 training experience, and when someone’s looking at it on a tablet, in the break room, on a laptop, in an office, or out on a handheld on the floor, what if we asked them questions and we tested to see if they’re really retaining this knowledge, if they’re really learning anything?
We started doing little quizzes and little certifications, little mini-tests in the experience. Lo and behold, we started to be able to see what’s working, what’s not. We started to see how effective or ineffective these experiences are based on how they performed, the user performed during the pop quiz at the end of the tour. That’s something that’s really simple. Arguably it’s not even XR. It’s a 360, it’s cool, but it’s not virtual or augmented reality so much, but it brings value.
It’s portable, it’s using real photogrammetry of our factories. It’s meeting the needs of consistent standardized training on important things for our younger workers in a way that’s scalable and distributable across multiple factories. It’s a way for us to assess and determine whether or not they learn what they’re supposed to learn. That’s something that is like– it’s kind of old hat, I think maybe in XR. I see a lot of companies, a lot of my buddies that run XR for different manufacturer companies do this. It’s pretty standard now in the world that I live in, maybe not across all of manufacturing, but it’s super impactful and I’m proud of that.
I think your question was, what are we proud of? I’m proud of that because it’s having an impact, a positive impact. It doesn’t cost a million dollars to make. A 360 camera and some software run you less than a grand and you can go do 100 factories with that same camera and that same software. That’s something I’m proud of, is that positive impact we’ve had and the, AHA, light bulb moments that we have with our workers when they look at that.
Because now you can see what’s going on in other factories and you can train your people in a way that doesn’t require crabby old Joe yelling at them and them memorizing stuff or them carrying around a piece of paper in their pocket that they might lose. That’s something I’m proud that we’ve done, my team and the team, my employer, has done.
Josh: That’s such a great example. I think it ties back a couple of points that you made earlier in the conversation. One, coming back down to, what is the problem that we’re solving? Two, you’re really establishing, what’s the best way to solve this problem. I’m sure you could have found a way more complicated and fancy way of approaching that.
To your point, you were really looking at almost that common idea in software development of, what is the minimally viable product to solve this particular problem. Like you said, you found something that can not only solve this problem at this local level, but this issue is certainly faced in other areas of the business, other factories, et cetera. It can be easily taken over there. I think that story really emphasizes some of the points and the lessons that you’ve shared already today and I love to see it.
I also love one of the phrases that you used, and I don’t even know if you caught it, but it’s this question of what if? In my opinion, that is the most powerful question to ask. What if blank? What if we did this differently? Just starting there opens up the opportunities to really make an impact. That’s something that I also picked up on from what you shared, that idea of what if. I would love to make sure that everyone listening really embraces the power of what if.
Scott: Because you brought this up, Josh. What if we don’t? We know what if we don’t capture that tribal knowledge from our veteran workers and put it in a digital format for our 21-year-olds? I can tell you what if we don’t do it. The veterans are going to retire, the young people are making stuff up and we’re running around pulling our hair out trying to figure out how to do it when Joe is already retired. I’ll tell you what if.
People will say, well, what if we try this and it doesn’t work? Or, well, what if we do this and what if our internet goes? Well, anything we do is going to be better than what we’re doing now because it’s tik-tok. Our veteran workers are retiring. People are leaving to go to work down the street at a new factory that has technology embedded in it from day one. I’ll tell you what if. What if we don’t try and we just keep getting the same results we’re getting, but it actually starts diminishing?
I like to use the carrot instead of the stick, but sometimes the stick, unfortunately, pain is a great motivator and I hope that those listening remember that it’s always better to get in front of this stuff than to try and put things in place after you have 55% turnover in a factory.
Josh: You’re absolutely right, that pain is the motivator and there’s plenty of studies out there to show that the fear, the pain, the loss, that is what really drives change to happen, more so than the optimism, what the future could look like. I think you have to have a good balance of both. I think you called it out. What if we don’t? What if we do? What if it doesn’t work? What if it does? Those are all flip sides of the coin.
Really, you’re going to have to choose which problems do you want to have. Do you want to have the problems of figuring out how to make it work? Or do you want to have the problems of not having done anything, and so you’re guaranteed to have those impacts we talked about earlier?
Now, we’ve covered a lot in this and I really want to, just as a final topic, hear from you people who are interested in exploring XR, what do you recommend they do? By that I’m meaning, what’s kind of a process that they can think through or follow through to find an opportunity to implement this technology and what are some of the constraints that they should be aware of as they go?
Scott: I talked to a lot of, I say a lot, maybe a couple of months new folks who are in some manufacturing company or some industrial environment. They’re with some company and they’re thinking about– they’ve either been told, “Hey, you need to go put this VR stuff into our factory,” or they’re considering, how could they go start to explore the use of this technology in their company.
I always tell people a couple of pieces of advice is number one, you’ve got to surround yourself with people who will risk your anger and tell you where you’re wrong. Here’s what I mean by that. Software companies and XR vendors, present company excluded, Josh, are happy to tell you why you need their solution. Now you’re smarter than that. I know you are. I’ve known you for a while.
Early on, starting off right in XR, I got my education almost solely from vendors, from headset manufacturers, from software companies. Now, I had some good people that gave me good, solid advice and I had some that wanted to trade me my cow for their magic beans. I had different types of experiences with headset and software vendors. What I would say to answer that is you’ve got to surround yourself with people that are going to shoot you straight, both inside your company and outside your company.
Isn’t it funny that we go back to the humanistic side of this? It always comes back to that, Josh. I would encourage everyone to get your information from others who have gone through what you’re about to go through that can tell you where all the forks in the road are at, where all the quicksands’ at, where some of the pitfalls are at, and they can be a buddy and help you. They have no vested interest in selling you anything, they’re interest is in seeing you succeed and being helpful.
I’m involved in a big community of folks with, you mentioned my podcast, XR at Work, we exist solely to provide education, support, training, camaraderie, and community for others who are putting XR into industrial environments, that’s it. I don’t sell anything to anyone, we charge no money for our advice but we just get other people together who are putting XR into manufacturing, and we talk, and we meet, and we share ideas, and we share war stories, we complain about vendors, and we talk about what vendors are doing a great job. We get together and talk.
I would say, plug into a group of people, and there are a few. I don’t have the best podcast out there but I care about people and their success and I’m happy to take a call. There are other people like me that will listen to your situation, help you sort out where you need to go, how you need to start, and they’ll give you straight advice, take it or not.
That’s the number one thing I would say is, if you’re looking to put XR in place in a ruggedized environment, oil and gas manufacturing, whatever the case may be, warehousing, aerospace, automotive, you need some buddies. You need some people, men and women who are going to help you out and be there for you, and they don’t stand to do anything but benefit from just being a blessing to you. That’s the number one thing I tell people all the time.
Josh: I think that’s great advice. Essentially what you’re saying is take some time to learn, learn from people who don’t have an agenda, necessarily. I think that that is absolutely true about not just this topic but in our personal lives as well, get advice from others and the peers. Coming back down to the human element, we can’t get away from this topic enough. At the end of the day, technology is just the tool, the people are the ones responsible for using it. It’s really all about empowering people to make the best decisions and take the best action possible.
I am a big fan of your podcast, I know you said it’s not the best podcast. I would argue that it is the best podcast exploring technology, specific technology and practical uses based off practical experiences related to XR within the industry, at least I haven’t found another one. If you have another one, I would certainly review it and then I’d compare and give you a true honest critique of it.
Scott: No, thank you for that. There’s a lot of podcasts. Conquering Chaos is a great podcast, you’re going to get a little different content and perspective on Conquering Chaos than you’re going to get on XR at Work or you’re going to get off of– there’s Augmented Podcast is run by an Natan Linder and Trond Arne Undheim. Alan Smithson used to have a podcast that I started listening to years ago, that’s no longer going.
What you get is you get different perspectives but if you’re just looking to put XR into industrial environments, I’m proud of XR at Work, Dan and I love doing it. You know what? I listen to a lot of other people’s podcasts and we would love to have you someday come on to our podcast. We’d be honored to have someone like yourself, Josh, share with our audience, all seven of them, what your experiences and what your insights are. [laughs]
Josh: I’d appreciate that.
Scott: Listen, we all need to help each other out, there’s a place for all of us in this deal, it’s not a competition. What does it say? The rising waters rises all boats, or whatever, I don’t know, I don’t live by the lake, the ocean. It takes all types, we’re all in here to help each other out. If we’re not here to help each other out, well then get out of the way, man, because we need this thing to succeed. Let’s not have another stop-start on XR like we’ve had in the past.
Josh: I love it. I appreciate the compliment, I appreciate the invite, I will absolutely take you up on that. I’m a big fan of XR at Work. I was actually bingeing today, I was listening to the one about Augmented Reality Without Disrupting Manufacturing, I think it’s one of your more recent episodes. What I love is not just the fact that you and your co-host, Dane, have experience in industrial environments actually implementing XR. If I recall from one of the episodes, Dane’s got a big experience on the EHS side, if that’s correct, and I remember him sharing some perspectives about the impact XR can have on that. You’re also bringing in people from the industry who can share their own perspectives and expertise, it’s really great. I think the individual on this episode I was most recently listening to was from Boeing, I believe.
Scott: Yes, that was Dr. Brian Laughlin who is both Dane’s father as well as my mentor. I use Brian as a mentor in XR. One of the things, to my earlier point is, one of the things, I want to make sure you guys hear this, because it’s just super valuable. One of the things that Brian’s taught me is that as my mentor, he says this over and over again, “We are both the purveyors of and protectors from the same technology. The very technology that we are promoting, and selling, and implementing and putting in place, we also need to be good stewards of that power, as it were, of that influence, and we need to also be protectors from that technology with our stakeholders and our customers.”
It goes back to what you and I have been talking about for the last hour, which is, we need to do the right thing, for the right reason, in the right way for people, not just take a top-down approach and put things in place because it looks cool. Yes, we do. We have people that come into our podcast and share with us their perspectives, and I think that’s something smart that both you and I do on our podcast.
Josh: I love it. Well, look, we covered a lot of topics, we talked about XR at Work, it really tied it to this idea of you’re going to have to consume information from multiple different sources and experts and ultimately, try some things and learn on your own and combine your own– really come to your own conclusions about where XR is going to work. I love that other people can share lessons but even if you provide the most perfect plan, your environment’s going to be different, your situation’s going to be different.
The best thing you can do is hear what people are saying, experiment with it, critically think about it, keep it simple and put the people first and you’ll have a really positive experience and learn a lot of lessons along the way. Scott, other than XR at Work, how can our listeners continue the conversation with you?
Scott: I’m happy to talk to anyone. I get paid to sit around and think about and research XR all day long, so it’s a great way to make a living. Thank you for that, Josh. If anybody wants to reach out to me on LinkedIn, I’m very open on LinkedIn. We do have XR at Work on YouTube, Spotify, and Apple podcasts if you want to consume some of the episodes there. That’s X-R A-T W-O-R-K. xrawork.org is our website that we just launched last week, but, man, my web development skills are a little rusty, but there’s a website up there and it has contact information and has a tab called community and how you can get involved.
Reach out to me, LinkedIn, through the podcast. If you see me at a conference, man, I’m always up for sitting around drinking Lacroix and talking. I’m happy to engage with anyone. I spend a lot of my time trying to help others because listen, man, everything I know somebody taught me so I owe it to the world to pay it back and pay it forward, so I’m happy to engage. Reaching out to me on LinkedIn is probably the best way or xratwork.org.
Josh: For the listeners there, we will have a link in the show notes to XR at Work as well. From your convenience, once you’re done listening to this episode, you can hop right in to the latest episode by Scott and Dane. Scott, once again, thanks for joining today.
Scott: Josh, thanks, it was my pleasure and my honor. I look forward to continuing the conversation. Thanks for everything you’re doing for the industry, man, we need more people like Josh Santo, man, you’re doing terrific.
Josh: You’re too kind. It’s you that’s needed. We’re going to make a bunch of copies of you proliferate the metaverse and hook it up to ChatGPT to make sure that everyone can benefit from it.
Scott: Giddy up.
Josh: A big, big thank you to Scott for joining the show today. I’m going to say something a little controversial here but I think this is by far the best episode of Conquering Chaos. Scott shared so many important lessons. My key takeaways, tech for tech’s sake does not work, focus instead on solving real problems. Don’t focus solely on hard savings, understand the impact of the soft savings. Manufacturing is ready for XR and XR is ready for manufacturing, and of course, last but not least, put your people first. If you like what you heard today, check out XR at Work, that’s the podcast that Scott co-hosts, the link is in the show notes. Until next time, thanks for listening.
What it's REALLY like to use extended reality in manufacturing!