The Factory of the Future: Focus on the Frontline
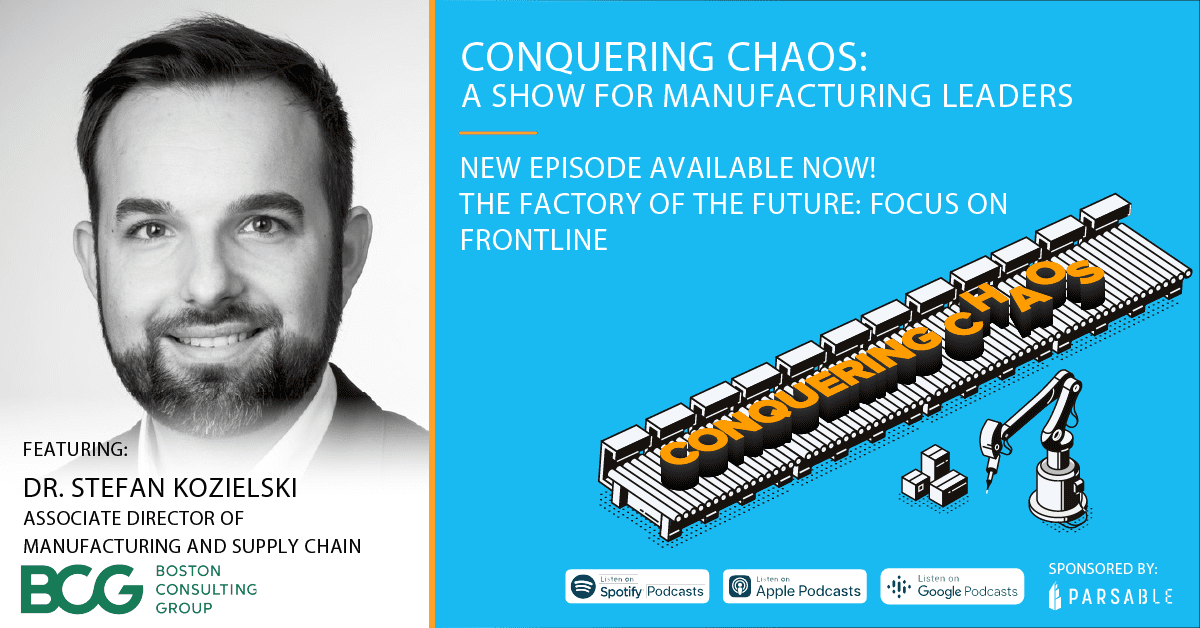
In today’s episode, we speak to Dr. Stefan Kozielski, Associate Director Of Manufacturing and Supply Chain At Boston Consulting Group, about his experience advising manufacturing leaders and what manufacturers need to do to get started on a people-focused journey to the factory of the future?
Join us as we discuss:
- A Realistic Approach to Digital Transformation
- Leadership & Psychological Safety
- Making a Focus On People in the Future
___________________________________________________________________________
Are you ready to start your digital transformation journey? Request a demo today.

________________________________________________________________________________________________
Check out the full episode below:
[00:00:00] Josh Santo: Welcome to Conquering Chaos, the show for manufacturing leaders. In each episode, we are connecting you to the manufacturing leaders of today who are driving the innovations needed to future-proof the operations of tomorrow. If you feel like your time is spent fighting fires and trying to control the everyday chaos, this show is the show for you. My name is Josh Santo. I’ll be your host.
Welcome one, welcome all to another episode of Conquering Chaos. Today’s guest is a very experienced leader in manufacturing and supply chain, as well as digital transformation and strategy. Now, what makes him such an experienced leader? Well, I’d point to his tenure in leading organizations within manufacturing and supply chain companies like Tyson Group, Henkel, and DHL.
In fact, in his most recent manufacturing role as the plant director of one of Henkel’s biggest consumer goods production sites, his site was recognized as a Fourth Industrial Revolution lighthouse by the World Economic Forum in McKinsey, as well as Factory of the Year by Kearney. How’s that for experience? Now, he brings the lessons he’s learned to other manufacturing and supply chain leaders in his role as an associate director of manufacturing and supply chain at Boston Consulting Group. Please welcome to the show, Dr. Stefan Kozielski. Stefan, thanks for being here today.
[00:01:27] Dr. Stefan Kozielski: Josh, thanks for the invite, and very happy to be here.
[00:01:31] Josh: I was really excited to connect with you. I was just mentioning to Stefan before the show started, conversations with people like Stefan or what the show is all about. People who have a strong opinion based on their experience in the industry. He’s walked the walk. He’s talked the talk. He’s here to share some of his lessons today. We’re going to start with the same question we start with all of our guests. Stefan, what’s your day-to-day look like in your role?
[00:01:59] Dr. Kozielski: Currently, couldn’t fit more into the title also of your podcast. It’s about conquering chaos, so working with many clients, being able to be on-site again on the shop floor working with the people, connecting with the people, and driving factories and their transformation forward. That’s what I’m currently doing in different dimensions, so big strategic directions, ESGs, sustainability topics, performance topics, efficiency topics, and people development. All the different elements of what we would call driving a transformation towards a factory of the future.
[00:02:44] Josh: Factory of the future. That’s a key topic. We were talking before the show, Stefan is on the road pretty frequently visiting different sites at different levels and stages of maturity with different strategies. He’s seen a lot and he’s met with a lot of people. This is going to be a great conversation. As you mentioned, that focus is on the factory of the future.
Well, let’s take a second to talk about that. Technology is evolving at a rapid pace. With these new innovations, finding the right strategy to bring different advancements together will unlock new opportunities to improve safety, quality, and efficiency while making new business models possible, which leads to additional streams of revenue. Those are the core ideas driving digital transformation in Industry 4.0.
Now, related to these ideas are the concepts of smart manufacturing, the smart factory, the factory of the future, and other various terms to essentially describe kind of the same concept. Now, a frequently-debated component of that, lights-out factories and robots replacing people comes up pretty consistently as well. We’re going to talk with Stefan today about the future of work in manufacturing and what factories of the future will actually look like. Stefan, let’s start with the basics. What is the factory of the future and how does that differ from what’s in place today?
[00:04:11] Dr. Kozielski: I would like to point out three things about the factory of the future. Some are new and some are actually quite simple. Starting with one of them, which is a factory is still about productivity and getting an outcome, right? With all the topics that you mentioned, digitalization use cases, lights-out factories, smart factories, et cetera, we tend to forget that. In the end, the overall objective is to be productive and to produce something to have an outcome, a transformation.
What the factor of the future is actually doing is we are having a productivity revolution. While traveling around and working with clients and visiting factories, I’m still seeing that we are sometimes tremendously underutilizing our assets strategically because we hold buffer for peak production, et cetera, so a supply chain question to solve because of poor efficiency. A production line at 60% OPI or OEE is still 40% idle, right?
There are factors that help us in driving a productivity revolution, and not only by the alt views of measuring productivity but in a more sustainable and holistic view. It’s about the financial outcome, the product outcome, but it’s also the sustainability and the wealth and share for society and people, which is actually from the three pillars, the second one. The factory of the future is still about people. We are often talking it’s about technology and what technology is enabling us. That’s fully true.
In my view and in our view, the factory of the future is bionic. It has components of human functions and human enablement. It has a clear people focus. It’s a workplace for people. Then as the third pillar comes technology. When both come together, technology enables us to do the productivity revolution that I mentioned. At the same time, in a usable way, creating an even better workplace for the people working in such a factory. When these three things come together, I am talking about a factory-of-the-future transformation.
[00:06:51] Josh: I love the way that you broke that down. Just to summarize what I heard, there are three tenets there. It’s the productivity, it’s the people, and it’s the tech. It’s all coming together. The tech is supporting the people. The people support productivity. I like how you positioned it that the factory of the future or smart factory, whatever you want to call it, is ultimately a productivity solution because those are where the problems lie today.
There’s an opportunity to be more efficient with the assets that are in place, whether those are machines, whether those are the people operating the machines. Technology should be that enabler that helps support the path to the highest levels of productivity that are achievable with the current state of things because there are always constraints, right? It’s always going to evolve and get better.
It’s a constantly moving boundary, so I love that. I think that that’s a great way of conceptualizing it. Now, I imagine our listeners, others I’ve spoken with, there are some frequent misunderstandings that come up. I’d love to hear from you, Stefan. When you think about the conversations you’re having with manufacturing leaders, what are they often getting wrong about the concept of the factory of the future?
[00:08:12] Dr. Kozielski: First of all, we don’t put the user experience of our people in the factory and our operators at the heart of the technology transformation. I’ve seen manufacturing plants and manufacturing lines with multiple Industry 4.0 use cases deployed, be it advanced analytics, predictive maintenance tools, et cetera. The frontline people had to lock in into three different systems.
It was tremendous additional work for them. Then we often, as manufacturing leaders, think the solution is whether we need more training. We need a better user experience because technologies get deployed by the user experience and not by how much and how intense we train people, right? In today’s world and society, our frontline operators, are exposed to technology in their private life.
In their private life, they don’t accept anymore when something is hyper-complicated. Everyone has a smartphone. We use our iPads. When it’s too complicated, we simply don’t do it. In the factories, what I see in many cases, it’s still too complicated. Then comes the second misconception. That is, let’s build a lighthouse in our factory network. Let’s revolutionize our manufacturing and then we run into the same issue.
It does not scale. Then in the business environment, if it does not scale, then you run into the problem that your business case of industrialization via digital is not calculating anymore because you don’t have the underlying productivity increases that were assumed when investing in technology. In the end, the big misconception I’m often seeing is that we dramatically underestimate the importance of the operator’s user experience in this factory transformation.
[00:10:37] Josh: I love how you called that out because it really highlights the focus needed to be on the people. There are a lot of talks out there in the world about how digital transformation is a people-focused transformation, but the application of that seems to get lost. That can be seen as simply as that user experience. You highlighted, “Look, we’re bringing in multiple different tools because let’s be honest, there is no one vendor that provides everything.”
A lot of times, companies then turn to, “Well, let’s build it ourselves in order to have that comprehensive approach.” It still starts to become more about the business outcomes and the processes and the other systems in place as opposed to that focus on the people. I think what you’re highlighting is that actually leads to a productivity problem. The user experience. We try to solve that for training by saying like, “If you just know how to use it.”
Let’s be honest. Let’s say I’m being nice and saying 30 seconds to log in to a particular system. You get 30 seconds there, 30 seconds there, 30 seconds there, and they’re not talking to each other. I got to go here and this session timed out. What a pain, and so that’s such a great way of crystallizing the tech, still has to be about the people supporting productivity. There can be gaps if you’re not looking out for those things. I love how you called out, “It’s not about building a lighthouse.”
You can certainly have a proof of concept to test and make sure that this is something that works well, but you have to plan for scale. There’s a variety of different ways that that can actually come in. Actually, I would love to pick your brain on that when we’re talking about building a lighthouse. The problem with that is that it does not scale. If it doesn’t scale, then you’re not going to realize those productivity gains, which ultimately jeopardizes your business case. Why do you see these lighthouse initiatives not scaling?
[00:12:38] Dr. Kozielski: There are, I would say, two major points why they are not scaling. First, it’s about that, simply said, it takes too long to build a lighthouse because our learning journey while building the lighthouse is quite long. While we are building the lighthouse, the rest of the network is not standing still. Then you can either be fully straightforward or top-down. Top management says, “Okay, we’ll do it like this or that.”
Then you take out all the ideas you, meanwhile, had in the other places or you will realize that your transformation is what I call getting blurry and scattering because your factories are– there are so many systems, so many startups, so many cool apps. Then your overall lighthouse concept is getting blurry because not any more transferable to the other sides. Secondly, we, on the one-hand side, underestimate.
I’m coming back to the point with the user experience. The complexity we create also, afterward in the product lifecycle management of all the applications that we deploy, is eating up our plant resources. It’s the same with IT, right? When you do this transformation, you need resources that drive the backbone of the transformation. The underlying analytics platform, your cloud infrastructure, your visualization, front-end, et cetera, et cetera.
If this is fully lying within the plants and the plants are not properly organized for this, then we come into something like a vicious circle. Because as you rightfully described, Josh, people are eaten up by other processes that actually defocus them on the productivity revolution. These two points like we take too much time. I’m also a German engineer, so the concept of something being ready and perfect was 80/20.
It’s still something that we can learn. Also, failing fast is something that we can learn. Not to stick too long to something, let’s make this a lighthouse. I’m convinced this will work, why it’s not working. The other thing is all about deploying the right organizational resources and considering the complexity that we create. Because in a factory of the future, there are so many technology clusters, software-wise, but also hardware-wise.
All of them have steering systems. I have machine panels. I have potentially AGVs or AMRs that have a steering system. I have ESG analytic system, energy, gas consumption, water consumption, I have ERP flows, et cetera, et cetera. We need a clever way of integrating and organizing and deploying also the resources to be able to do that, and then we have a chance to scale.
[00:16:33] Josh: The resources are such a critical part, right? Because resources mean people, they mean priority, they mean funding. That is critical, not only to set up a lighthouse but to take the successes there, and adapt them at the different sites, because that’s the other thing that we all need to face, especially when we’re talking about major, leading manufacturers who have acquired different sites or different brands that come with different sites. They’ve got totally different machines running in place and different processes, et cetera.
There’s a lack of standardization, which means you can’t just figure it out at one place, and then expect that to work at each place. It requires that ability to say, “Here’s what works, but we ultimately have to go and adapt it on a per-site basis.” That takes not only the time and the people and the resources but the prioritization, meaning we are prioritizing this over other things, including– and this might sound a little backward and, Stefan, let me know if you agree or disagree. It includes prioritizing that over productivity at first because you might see that there’s going to be a bit of a hit in the short-term in order to achieve a long-term gain.
[00:17:45] Dr. Kozielski: It’s not backward, Josh. In fact, it’s right because every one of your listeners who has deployed an advanced system or an Industry 4.0 use case has faced difficulties in the deployment phase and has created standstills during the deployment, which is quite natural. Making an MES system work over multiple machines, making a maintenance and spare parts management system work, and making more advanced analytics work.
We worked on something that we call production line health checks, where I try to get more into the space of predictability out of various machine parameters and try to make a prediction on how is the line going to perform in different scenarios, do-nothing scenarios, maintenance scenario one, two, three. Resources and, of course, the acceptance that, in the beginning, you also need the idle time on your production equipment to install factors that I see underestimated and not taken into account enough.
[00:19:08] Josh: Great points. It does come back to that idea of, “It has to be a priority.” There are going to be some trade-offs. That’s a tough conversation to have, particularly right now. When we talk about resources, manufacturers are struggling to get people in place to help out with a variety of different roles. You’ve got inflation, which is impacting the bottom line, which then impacts the money resource.
You’ve got supply chain challenges. You’re trying to produce. You got to keep up with demand and you’re struggling to do that. It’s hard to have these conversations about trade-offs, but they are essential for aligning expectations. There’s no other way about it. If digital transformation is the future, if the factory of the future is the future, you’re going to have to go through these short-term pains.
[00:20:04] Dr. Kozielski: Also here, to make it simple, yes, there is a people shortage and there is a war for talent. One of the answers in, “What are we going to do about it?” is our factories have to be a great place to work. That has many components, right? First of all, that comes with points that I don’t see, which are leadership and also psychological safety for our people. Parts of our brains are still working like an animal brains. If there is stress, there is an escape mechanism.
If you’re the operator of a production line during the night shift, there is permanent stress due to micro stops and 10 different systems to lock in additional pressure because of material shortage and potential bad leadership from the shift leader or factory manager side. People are going to flee. That is something we have to care about. Sometimes we are investing too much time to make our offices fancy. We don’t think with the same strictness and the same vision and the same passion, about how to make our factory a great place to work.
[00:21:44] Josh: Yes, I love that. We had a guest not too long ago, Jim Parker from Inline Plastics. What we talked about were the efforts that they went to understand what was going on with retention at their specific site. Why were people leaving? Why were they coming back late from breaks? What they assumed was a behavioral problem really came down to not providing what people need in order to do their work.
There are some great concepts there. Ultimately, what you brought up, leadership, and psychological safety, are critical. I’d love it if you could talk a little bit more about psychological safety and what is meant there. Is it a feeling of, “I’m safe in my work environment,” or is there more of an emotional attachment to it?
[00:22:38] Dr. Kozielski: Oh, it has both. First of all, still, the number one priority in every factory is that every person who works there is safe and can go back home to family and friends. Well, of course, ideally, in better shape than before. That’s the physical part of it, right? There’s also the psychological part of it. That is, if I’m in constant fear of losing the job or not making the performance indicators, the KPIs, then that’s harmful. That’s stressful.
That can lead also to burnout situation on the operator level, which is, by the way, also something we rarely hear about or talk about because we typically have burnout as an illness in a white-collar space. I’ve seen production lines and OEE performance at 55. The target is 80. We put the big monitoring system in place. Every day, it shows you the gap and the bright red. You have the very directive leadership pushing people towards the target.
Other than improving, you run into a vicious circle of not improving and people leaving. That has also to do with leadership setting the right target, also setting the right ambition for a factory, and then also deploying the right tools and enabling people to achieve the target and to have little successes on the journey and celebrate those successes. That’s still in this century with all the use cases and technologies and tools we can deploy at the heart of factory leadership.
Now, spot onto our conversation, Josh, we have this situation. Then in this situation, we put on top, 5 to 10 additional Industry 4.0 use cases. That leads to additional stress. We have to find ways. The environment is super volatile. The world is changing frequently. How things are changing politically, and financially, it’s increasing and increasing. We should, in my opinion, consider this and rethink our factories as a place of safety, both physical and also psychological. Then people will want to work in your factory.
[00:25:33] Josh: That’s a key part, right? People will want to work in your factory. It’s not technology that’s going to drive that desire to want to work there. Ultimately, the word that I think you’re describing, Stefan, is culture. What is the culture there? The culture is set by leadership. What does leadership prioritize? How do they make people feel psychologically safe and reinforce that? Not only do we want you here, but it’s actually a positive experience for you. It takes, again, prioritizing the people. That’s a consistent theme that we’re hearing in this conversation. Would it be fair to say that the focus of the factory of the future should be placed on the people?
[00:26:20] Dr. Kozielski: Absolutely, yes. On all the people in the factory, on all the different roles that we are currently having and that we will see transform, I would say that in all factory transformations, I was lucky to participate either as the factory manager or as a consultant. The critical success factor was to get, first of all, the team starting with the leadership team and, secondly, to really incorporate all the people and all their perspectives into the program.
You can, of course, top-down, deploy something in your factory. Let’s take AGVs as an example. You replace forklifts with AGVs. What you realize when the factory teams are not owning it and when it’s not explainable in such a simple way that every person in the factory will understand it, you will fail. Because what we forget in all the discussion about technology, the heart of a factory next to the people is their routines.
The difference between a good and a not-so-good factory very often lies in the quality of the routines. The technologies that we introduce have an impact on the routines. Changing a routine, as we know from ourselves or personal habits, is not an easy thing to do. The first thing on that change journey starts with our self to understanding why we are changing the routine.
[00:28:13] Josh: When you think about those concepts that you just brought up, there’s a lot of talks right now about building resiliency. What we’re describing here, is the focus on people, the factory of the future, how does that lead to a resilient factory?
[music]
[00:28:32] Josh: Hey, we’re going to take a real quick break to hear from our sponsors. Stay tuned for more Conquering Chaos.
[00:28:38] Rob: Hey, listeners, it’s Rob. I’m one of the producers of Conquering Chaos. I’m right here with you for every episode, working behind the scenes to make sure everything is just right for your listening experience. Whether you’re a new listener, binging content to help you conquer the everyday chaos, or a dedicated fan tuning in for each new episode, there’s one thing to always keep in mind.
Information is useless unless you use it. Obvious, right? It’s so easy to learn, forget, and then miss out on the opportunity to make real improvements to day-to-day activities. Well, the folks at Parsable have an opportunity for you to learn, experience, and make real improvements to those same day-to-day activities. Get rid of paper on the factory floor. It’s the quickest and easiest way to make a measurable impact on safety, quality, and production.
Think about it. Paper-based checklists, forms, and SOPs isolate workers from getting the information they need when they need it, which leads to a number of inherent inefficiencies that you probably accept as a part of your own everyday chaos. As a result, you can’t respond quickly to problems. You struggle to standardize the completion of critical tasks and you miss out on new continuous improvement opportunities.
Parsable is proven to help across a number of different functions, including autonomous maintenance, line changeovers, in-process quality checks, and more, which has helped industry-leading manufacturers reduce unplanned downtime, increase OEE, improve throughput, and more. See for yourself how easy it is to bring a connected digital experience to your frontline workers by using Parsable risk-free for 30 days. Check the show notes for the link. All right, back to the show.
[music]
[00:30:48] Dr. Kozielski: I don’t want to say it’s the same thing, but it goes hand in hand. Why is that? Think about potential drivers of resilience for your manufacturing site or for your factory. You can go through all the levers and you can say, “Well, I think it’s resilient when I can have a machine breakdown and my output is still not harmed.” This means I need double assets. Let’s be more resilient towards material and material supply.
You will discover that part of the answer is to have somewhere in the supply chain and the system more stock or you will change to another supplier, who is more potential than not in a low-cost country. You will increase the cost. The only driver of resilience and the only factor, at least one of the most powerful ones who drive resilience, is the people, their routines, and how they work together in the organization with the right leadership principles in place, Josh, as you call it, with the right culture in place, and also with the right degree of autonomy in place.
Let’s take an example from sports. The soccer team where the soccer player, once he has the ball, needs to look to the coach to ask for permission to play the ball or to ask him what to do with the ball will never win. We have to bring this same concept into our factories that we make the rules of the game, of the system clear, but we give people a great place to work and room for their own autonomy driving the system forward. That for me is resilience.
[00:32:54] Josh: I really appreciate how thorough and specific that example was. The focus is on people, routines, and how they work together. Then to your point, that level of autonomy, the goal should be to empower the people who are doing the work to make decisions that are best in line with the goals of the production. Technology is certainly an enabler there. I love the focus on the quality of routines and having that be a centerpiece.
There are routines everywhere. Sometimes your routines may be a bit chaotic, but your reaction to the fires that pop up in the day-to-day over time becomes your routine. Really examining, do we have the right routines in place? If the answer is no, that’s got to change. If the answer is yes, then it’s, “How do we ensure that the people are able to successfully do these routines consistently?”
Whether that means they need to have access to knowledge and one-point lessons to understand how to perform aspects of that routine, or that could be, “How do we ensure the handoff of information between a person and another person in a different department, but they have to work together because that’s part of the routine?” or maybe it’s even a handoff of information from the person to the system and the system then triggers an automated action.
That idea of resiliency, being focused on people, routines, and how they work together is such a great way to crystallize it. That gets us to this idea that people are critical. We’ve been saying that on this. That’s consistently the theme that we’re having here. Frontline workers in particular are a critical part of a manufacturer’s future. We’ve talked about, conceptually, what a factory of the future looks like. We’ve talked about how that isn’t what we see today. Let’s spend a little time in the future now. Let’s talk, Stefan, about, what does the future of manufacturing actually look like for people in the factory?
[00:35:11] Dr. Kozielski: Josh, as we already pointed out, for me, the factory of the future, first of all, is really a great place to work for the people, a place we like to go through, and a place where we can be productive and create something new without harming our environment and where people are safe from a physical and also psychological perspective. Then from the work that we are doing and how people are working together, we completely underestimate how dramatically and how drastic the change really will be because the keyword for me here is “bionic.”
Now, we’ve talked a lot about people, but we should not underestimate how big of an impact the technology side will have on the way we are manufacturing. This can be in the manufacturing processes. We see a huge development in more generative manufacturing, technologies like 3D printing, and additive manufacturing. This is somehow old-school to be a blunt way of doing things– I take a big block of something and then I build it out towards I’m building up something from scratch. That will have a dramatic impact.
The way how we are able to capture and work with data will make a tremendous difference. Again, simple example. I don’t see any paper or handwriting in any of the factories of the future. Potentially, it’s not even on a screen. Potentially, it’s not even in our intelligent glasses. Potentially, it’s implanted somewhere. You have a little lens on, so there are all kinds of really futuristic things we can think about to interact with data.
In the end, that interaction with data brings two things. Number one, for the people in the factory, it helps them make better decisions. Secondly, as you mentioned, with the right steering systems and algorithm then in place, it allows the machinery and robotic part of the factory, in the end, you could say, to set, optimize, and operate themselves. The job of the operator, I’m going to the machine. I push the button.
It’s going to change dramatically. There is an automation revolution still going on. The number of automated systems we’re going to see in the factories will dramatically, dramatically, dramatically increase. We need that because, as we said, we have people shortages and we will continue to have people shortages. In order to cope with this gap, we need a productivity increase.
We need to take out some of the jobs that potentially don’t make a factory a nice place to work. These three things coming together. First of all, it’s a great place to work for people. Then combined with the data piece, interaction with data, better decisions, self-optimizing systems, and then the technology, 3D printing, and automation revolution, that will, I think, be the drivers for the factory of the future in the coming years.
[00:39:27] Josh: I love spending some time about what these advances in technology are ultimately going to lead to. That’s really that question of, how do people work? One of the ways that we’ve envisioned it here at Parsable is almost this– I guess the best way to describe this example is almost like a doctor-patient relationship between the human and the machine where you as the person, you’re the doctor in this case.
You’re the expert on how this machine should run. If not, you know how to get the information. That information is quickly accessible and the machine does let you know, “Hey, Doctor, it hurts here. I’m not able to do X, Y, and Z. I can’t change the temperature to the setting that it needs to be,” or whatever the case is. Then the human is able to successfully almost have a conversation with that machine.
“Okay, I took this action. How are you feeling now?” “Oh, this is the case.” Well, based on historical data as well as our routines and our procedures and expertise, all of this coming together, I can then make the best decision to help you right here at that moment. That’s one of the visions that we, here at Parsable, see for how workers can be connected to those different assets, including machines in the future.
[00:40:51] Dr. Kozielski: Josh, think about it. We and also the workers of the factories, the people, accept that in our home, potentially, we do voice recognition, and shopping via voice. We steer the housing systems via voice. Well, we have, as I said, our mobile phone. We have all kinds of applications. Then, normally, you would imagine, I have a technological advantage in the factories. Over the last years, that has completely turned around. The operators rather, in some of the factories, have a technological advantage in their private and social life, how they are connected, and how they’re using social networks. The factories need to keep up with that.
[00:41:53] Josh: I think that’s such a great point that you can look around your own life as a consumer in today’s day and age and extrapolate some of those things, some of the ways that you live your life, and take that and say, “Well, how can we apply this to our working lives?” To your point, there are enough systems in place right now where you can set it up to where you walk into your front door and the music starts playing. Maybe the lights dim down, whatever the case is.
I’ve got a friend who’s got a Ford F-150. At the end of each week, he gets an email that says a little bit of information about the usage. It’s almost like he’s having a conversation with his truck, right? Imagine if those same types of experiences were available in the factory, the machines reporting out like, “Hey, this is what happened,” everything and taking that data and being able to optimize with it. I’m a big fan of voice recognition. I would love to see that take off within manufacturing. Issuing commands, and having conversations, I think, is such an exciting idea.
[00:43:08] Dr. Kozielski: Yes, and it scales without 5 to 10 to 20 pieces of training and certifications. I don’t know if you have a voice steering system certificate and you were trained in using the system. I’m exaggerating, but that’s what I’m talking about when creating a factory of the future and scaling it. We are sometimes making it too complicated.
[00:43:39] Josh: Yes, I love that. The more you can focus on this idea of work like how you live, you lower the barrier of entry there because, to your point, you don’t have to spend a ton of time upskilling people because these are habits that are already there. You don’t train anyone to walk in a factory or you don’t train on having conversations or connecting with different people. That are things, for the most part, that people do in their day-to-day lives.
Just conceptualizing this example of the more it’s like the way you live, the easier it is. I hope that rambling makes sense at all. I want to talk about an action plan. It’s great to cover concepts, but we want to make sure that everyone listening has an action plan. Something that they can walk away with this information and do something about it. Change is tough, but a good plan can help. However, Stefan, as you mentioned, leadership is going to make the biggest difference. Talk to us about, what should manufacturers do to get started on this people-focused journey to the factory of the future?
[00:44:59] Dr. Kozielski: First of all, before starting on the people side, as a factory manager, thoroughly review your processes systems and what you have in place and make a complexity assessment. Find the over-complications and try to get rid of them. How to do that, spend time at the frontline. Nobody hinders the factory manager to spend a minimum of 30% of his time on the shop floor.
Potentially, if more, why not take the time to run one shift together with the operators at the machine to get the– we talked about user experience, so get information from the shop floor and talk to the people. One of the most, I would say, rewarding and also powerful measures while working in one of my factories was that we had a business breakfast with 10 selected operators every Monday.
Just a cup of coffee for 30 minutes outside of standard work like a conversation. What’s working? What’s not working? How can we get to a better situation? How can we make this an even better place to work and offer support where we often speak about what we need to change as leaders and the concept of servant leadership and putting people first? Then we stumble over the first step, which is making time and having a conversation.
Then as a site manager, get your team and your organizational structure right and make a thorough audit, which also not only people, but also roles you require to make your factory a factory of the future and then see if your organization is structured in the right way and if your people are on the right job, and then have a look at your transformation program. Is the ambition rightly set? Are the tools in place and deployed to reach the targets? Are your people, first of all, empowered with the right autonomy to do so?
The example regarding the soccer player, do they have the right playing concept and guidelines to do so? Then, in the end, make a thorough assessment either for your plant or for your plant network. What are Industry 4.0 use cases or technologies where you see the potential to truly transform? Not to make an incremental step, but to truly transform the way how the plant can perform. Then try it out as fast as possible in a place where it’s easiest to try it out and then fail super fast.
[00:48:39] Josh: Fail super fast. Who would you say is responsible for this type of initiative? I heard you mentioned the factory manager. Should this come from the factory manager? Is this above the factory manager? What are your thoughts there?
[00:48:51] Dr. Kozielski: Both. The responsibility and the parts of the vision and to drive the plant-forward always has to come from the plant manager. It’s always a part of it. From my experience, it works best when there is a consolidation area or a consolidation piece above the plant manager, a function that is giving top-down strategy, and also priorities and production strategy for all the plants in the network. Then if you really want to transform, combine both top-down and bottom-up approaches.
As an example, if you want to advance in technology, you will require some capex. For some of the capex, you assign a top-down on strategic priorities. Some parts of the capex should be completely bottom-up. Either on budget, the plant manager can spend on his own decision together with the team where you make something like an RFP. We are looking for the best concept in using advanced analytics to improve OEE of our production line, and then your plans can apply to the budget.
[00:50:17] Josh: Got it. I can certainly appreciate that because there has to be that local leadership involved, and then the local leadership needs that central support. Especially when we start thinking about some of these initiatives, it’s going to cost money, money that’s beyond just what is in a typical factory manager or plant manager’s budget. Really important call-out. It’s both local leadership is required as well as central leadership is required. Then on that point, how critical is the business case for these conversations, especially for just getting started? Our listeners, how do you recommend they make a business case?
[00:51:04] Dr. Kozielski: Typically, in the industrial environment, you will need something of a payback time, let’s say, between two years. Sometimes three years if you do something really innovative. Also, potentially, you see cases where you have five years’ payback time, but technology changes so fast that that’s most likely too long. Drivers in your business case, to make these investments fly, are typically on the productivity and efficiency side of your plant budget.
The degree of underutilization, for example, comes from lower OEE. Try to calculate in a way, “Okay, what does a line standstill at full cost really cost me? What is the real cost of not using the asset at 100%?” and then approach it that way. Don’t go too much into all the details immediately in the beginning. Make a rough overall calculation. Also, there are some cases that require, you could say, initial money on the table because there is no business case for one factory. If you install the structure for 10 or 20 factories, you will have a case.
Don’t see it only from the view of one factory, but see it also from the view of the network to make it a business case. Then I can tell you from experience for good use cases, there is always a business case. The need to change also goes beyond the financials in many cases from other aspects that you caught. We have a shortage of human labor in some areas of the world. We have sustainability pressure. We have to reduce dramatically our emissions. We have to become carbon-neutral, et cetera, et cetera, especially in the combination of, you could say, digital technologies driving sustainability improvements are fantastic opportunities and fantastic business cases to make.
[00:53:34] Josh: Great. Well, I think we’ve covered a lot of great topics in this conversation today from exploring, what does a factory of the future really look like? What is the secret to the factory of the future? Reminder, it’s the people that are supported by tech in order to drive productivity gains. We talked about, what does that factory of the future look like, how that differs from today, and what you can do to get started on building towards the factory of the future? A lot of great topics there. Stefan, how can our listeners continue the conversation with you?
[00:54:08] Dr. Kozielski: First of all, you will find me on LinkedIn. Just drop me a note. I’ll definitely reply, and then we can have a conversation. You will definitely also find the one or the other article or podcast or presentation, either from me directly or from us as the ops team of Boston Consulting Group, and looking forward to it, looking forward to the conversation, and looking forward to transforming more and more factories and deploying the concept of the factory of the future as we just discussed.
[00:54:52] Josh: How can your team at Boston Consulting Group help?
[00:54:56] Dr. Kozielski: First of all, we can support all phases of such a transformation program, be it for the total network or be it for a single factory. We can, together, design such a program. We can run analytics. We can, together, define concepts. We can also deploy the use cases. On the other extreme, we can also deliver full-factory transformation with our teams. Enable together with your teams, the factory transformation drive, to track the factory transformation on the ground. BCG is typically not seen or perceived as specialized in operations. In fact, that’s not true. We fully are.
[00:55:46] Josh: Well, great. I really appreciate your time, Stefan. Thanks so much for joining us today.
[00:55:51] Dr. Kozielski: Thanks, Josh, for the opportunity. It was really a pleasure to talk to you.
[00:55:55] Josh: You too. That’s the show. Thank you so, so much for joining us today. Conquering Chaos is brought to you by Parsable. If you’re a fan of these conversations, subscribe to the show and leave us a rating on Apple Podcasts. Just tap the number of stars you think the show deserves. As always, feel free to share what’s top of mind for you and who you think we should talk to next. Until then, talk soon. Take care, stay safe, and bye-bye.
Listen to find out how you can focus on the frontline.