Supply Jane & Fifo: Getting Younger Generations Interested in Supply Chain
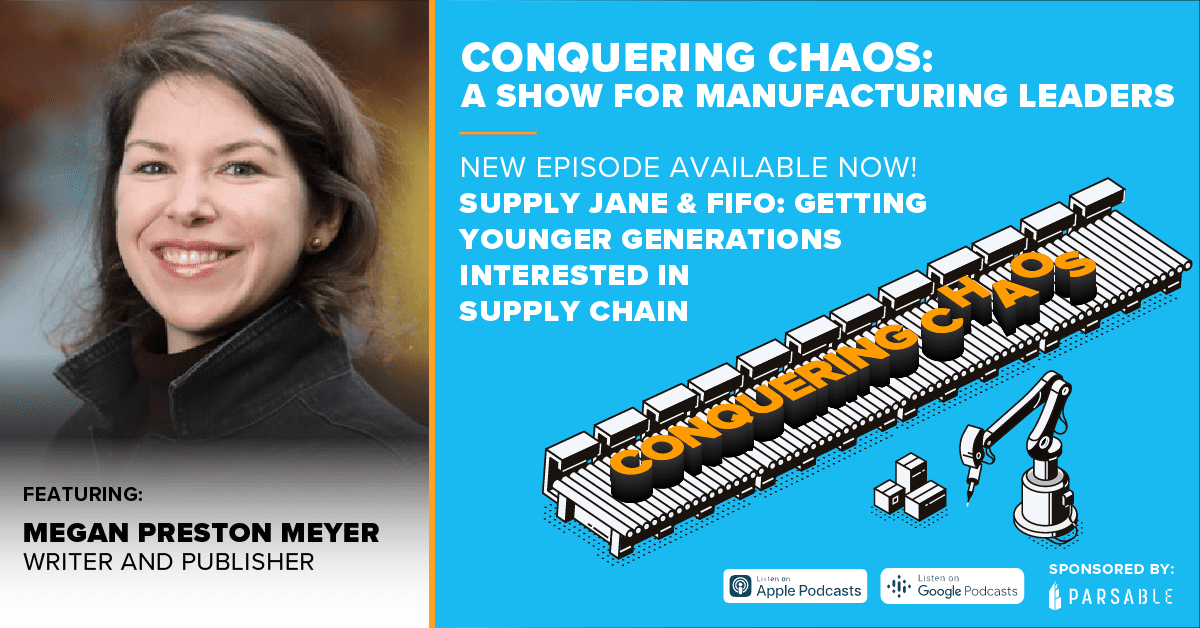
Data is essential to the supply chain process, but it’s not everything.
It’s a tool to be leveraged by the people who ultimately make the decisions. After all, data without business context is meaningless, or even worse, misleading.
Megan Preston Meyer, writer, and publisher at Preston Meyer Publishing, is an expert in supply chain analytics and a proponent of finding the right balance between data and insight.
She’s also a key player in attracting the next generation to manufacturing.
How is she doing it? A children’s book series that follows the adventures of Supply Jane and her dog FIFO.
In this episode, we discuss:
- The role of analytics in the supply chain
- What many people working in supply chain get wrong
- Best practices for dealing with data
- How a story can attract younger generations to supply chain careers
Check out the full episode below:
[00:00:02] Josh Santo: Welcome to Conquering Chaos: The Show for Manufacturing Leaders. In each episode, we’re connecting you to the manufacturing leaders of today who are driving the innovations needed to future-proof the operations of tomorrow. If you feel like your time is spent fighting fires and trying to control the everyday chaos, this show is the show for you. My name is Josh Santo, I’ll be your host.
[music]
Hey, all. It’s Josh. Before we get into this episode, I wanted to put this into your ear. If you like the types of these conversations we’re having, you’ll enjoy the content that we share through our mailing list. Go to parsable.com/podcast, scroll to the bottom of the page, and sign up to get more insightful content delivered directly into your inbox. Okay, onto the show.
Welcome one, welcome all. I know that I always say this to you, but we’ve got a great show lined up for you today and just in time for the holidays. Our next guest is an experienced supply chain and operations analyst who’s accomplished quite a bit during her career. From optimizing the use of brewing and by-products to mapping complex inbound supply chains across different continents, she’s helped companies like SABMiller tackle supply chain opportunities that reduced waste, unlocked millions in value, and helped drive sustainability.
While her career has spanned multiple industries, she now focuses on the stories that data doesn’t tell as an author, speaker, and communications consultant. By doing so, she helps companies become more authentic and engaging in their communication, collects corporate jargon, and writes children books about supply chain and operations management. Please welcome to the show, Megan Preston Meyer. Megan, thank you so much for being with us today.
[00:02:04] Megan Preston Meyer: Thank you, Josh, I’m really excited to be here.
[00:02:06] Josh: Now, for those of you listening to the show, I am in Austin, Texas, but Megan, you’re not. Megan, where are you located?
[00:02:13] Megan: I am in Zug, Switzerland, so quite ways away, in fact.
[00:02:19] Josh: Zug, Switzerland. I always imagine Switzerland to be beautiful. I’ve been once, but not to this particular area. Tell me, is it living it up to what I am imagining?
[00:02:28] Megan: Well, I can’t tell what you’re imagining, but I suspect it does. One thing right now, it’s just the end of November as we’re recording this, and we got our first snowfall which you probably don’t have in Texas quite yet, but it’s gorgeous.
I actually grew up in Northern Minnesota, and I like to say the landscape is really similar, except for Switzerland has these mountains that Minnesota doesn’t have, but the flora, the fauna, the lakes, the forest, it all looks pretty similar. I actually feel quite at home over here.
[00:03:04] Josh: That’s great. It sounds exactly like what I was imagining in my head, so what a perfect description, the thought of Switzerland is Minnesota except in Europe. Just kidding. I just think-
[00:03:17] Megan: I’ll call up the tourism board and see if we can get the slogan switched.
[00:03:19] Josh: Yes, new tagline. Yes, exactly. You heard it here first, everyone. Megan, talk to us about how your day-to-day looks like. We love to start off the conversation just by getting to know our speakers a little bit more and what their day-to-day looks like.
[00:03:34] Megan: One of the things I love about my- as you heard for my bio, my new role as an author, et cetera, is that no, I don’t have a “day-to-day”. Every day looks different. For instance, yesterday I spent most of my morning- I’m working on a parody or an homage to ‘Twas the Night Before Christmas, but supply chain themed. I finished the poem and then handed out the layout and some graphics to the freelancer that I work with. We can hopefully get that polished into a book before Christmas time.
That’s one thing that I would’ve never imagined myself doing two years ago at this time. I do freelance work. Recently I was working on a white paper for a client and talking about the benefits of digitized work instructions, something completely different. I prepare for different podcasts or things like this, conversations with people from all kinds of different industries, different positions, and try and also do some of my own writing. I’m working on a novel as well. Really very, very– I never- I should probably plan better, but I never really know what my day is going to look like until I sit down at my desk and get started.
[00:05:01] Josh: I love the supply version of The Night Before Christmas and I would love to see that myself. Please keep us up to date with the status of that and when it’s going to be available because I love the holidays and I love that you’re bringing this unique idea too, which we’re going to talk about a little bit more. Of course, digitized work instructions, I can talk a lot about that, but we’re not here to dig into that.
In fact, actually, I’d like to start our conversation by digging into your background. You worked as a supply chain analyst and you worked a lot with analytics. Supply chain is very relevant right now, it always is, to be honest, but in particular, it’s causing a lot of concern and frustration for both manufacturers as well as consumers, it’s a fairly timely conversation. Before we get deep into that, your background, you were on your way to a Ph.D. in operations management, is that right?
[00:05:58] Megan: That is right, yes. I have 2.25 degrees and 1.25 of those are in operations management. I did my MBA focused on operations and then I fell in love with the subject matter so much so that I decided to jump basically straight into a Ph.D., got about a quarter of the way through, and then realized that I liked practicing much more than I liked teaching. I didn’t want to be a professor, so I decided to leave academia and get back into the real world. That’s how I ended up on the path that I was on/am on now. It’s been jagged, but there’s a red thread.
[00:06:45] Josh: You liked the practical application as opposed to teaching and spending some time in that theoretical realm. What was is it about the practical application that really ignited this passion?
[00:06:58] Megan: I think it’s because operations, supply chain, continuous improvement, this whole world is so tangible. I started my career when I was 16, working at a Subway restaurant, and then I worked my way through high school. During my undergrad, I managed two stores, two Subways, and that’s where, in this franchise model, I really fell in love with standardization. We made the exact same sandwich that a store in California or Switzerland– We have Subways now here. We made exactly the same sandwich, following exactly the same instructions, the same process, and this tangible, standard process that could be improved upon and could be transported from place to place regardless of the operator for a normal personal term.
That really got me interested. There’s so much knowledge that is placed into the process itself, and the fact that you can convey so much information within just a set of instructions, a very simple training method, I found that really, really interesting. I also realized about this time that I wanted a career that involve wearing an apron and a visor for the rest of my life. That’s how I decided to get an MBA. Once I got to business school, I realized that I was not a finance person, wasn’t really a marketing person at that point, so focused on supply chain and operations management.
[00:08:40] Josh: Sounds like, in your experience with Subway, these principles that you discovered about what makes not just one Subway work but what makes– The Subways work together in such a way that a consumer can walk in and know, “I know I want to get this, and it’s going to be prepared this way, and it’s going to meet my expectations,” it sounds like you saw applications of those same principles in a broader perspective, right? It wasn’t just Subway that applies this. If you look at the right spots, you can see it just about everywhere we go.
[00:09:17] Megan: Absolutely, absolutely. It’s this hidden logic, these concepts that make the world go round, really. If you do things the exact same way, how many– We talk about it in more of a business sense, in operation sense, but there are so many leadership and productive books these days that talk about the power of habit, right? Doing things the same way over and over again pretty much guarantees the same results and the opportunity to improve.
Learning that from an early age, I think, really shaped the way that I look at just about everything else. If you start looking for patterns, whatever you’re looking at, you’ll usually find them. Once you can see these patterns, it opens up this whole new world, this whole new layer that I find just fascinating.
[00:10:11] Josh: I’ve certainly found, especially with my work in manufacturers or with manufacturers, I should say, and focusing on continuous improvement, how there’s principles that we learn to apply at the jobs that we do that are actually pretty great tools for outside of work activities, whether it’s a hobby or just your own household.
For example, I now always hold the rail up or downstairs, or I maintain three points on a ladder whenever I’m using a ladder, or I unplug the toaster before I do anything with it. That’s “Lockout/tag out”. There are some standard safety concepts, but also improvements. Let’s get to the root cause, let’s dig into why. The five whys. Why? Why? Why? Exactly. That’s what I’m hearing from you is, you discovered these rules that can actually make an impact in life. You mentioned you were exposed to it at a younger age. Were you exposed before college to these types of ideas and concepts? Or was it when you got into Subway that it really clicked for you?
[00:11:16] Megan: I think that was really when it started to click for me. I don’t recall before Subway ever actually noticing many of these things. I knew I wanted to work at a Subway from the time I was like 12. I’m not exactly sure where that urge came from. I’m glad I got there because it has put me on a really good trajectory.
[00:11:39] Josh: That’s great. This is going to tie into something we’re going to talk about later in the episode, but it’s that idea of exposure of our young minds to these different principles that make the world go round, not just from a business perspective, but things that you can apply within your life. Before we get there, tell us about your experience working in supply chain and how you leveraged analytics to support you throughout that time.
[00:12:02] Megan: When I started working in supply chain, it was very traditional cut-and-dry supply chain optimization. I was mapping inbound supply chains. One of my first big projects was mapping barley supply chains in Africa. One of the biggest challenges we had there was grain loss along the supply chain. I started looking into this and realizing that I needed numbers. You can’t just say, “Oh, we’re losing a lot of grain.” You have to be a little more specific.
I opened up an Excel sheet, and I’m sure this wasn’t my first Excel sheet ever, but this is probably where I started to fall in love with it. I made a nice model and realized though, when you start providing nice models and spreadsheets, people start expecting more of that from you, which is great. You need data and you need numbers. I started using analytics much more so than I probably expected when I started in the role and in supply chain in general, and just dug into it, kept looking, learned. I got very, very good at Excel, moved into SQL which then became my weapon of choice, and never really looked back.
[00:13:29] Josh: During your time working in supply chain, were there any lessons that you learned that now knowing this lesson, you would say, “This is what people get wrong about working in supply chain or analyzing operations within the supply chain”?
[00:13:47] Megan: One thing that I can definitely say now because I was guilty of this for a long time, is that numbers only tell half the story ever and if that. You can do a great analysis, but first of all, you have to be darn sure that your analysis is correct. Second of all, even if it’s the most insightful groundbreaking discovery that anyone in the organization has ever had, if you don’t communicate that recommendation or that course of action effectively, no one’s going to listen because they don’t know what your numbers say.
We find ourselves, there’s a lot of tension that I see sometimes where people either rely too heavily on the data because they either haven’t crafted a story around it. All they can do is they look at it through one lens and say, “The numbers say X, we must do Y,” or on the other hand, if there isn’t enough data, if the data is dirty, if the data doesn’t say what we want it to say, then we just ignore it.
There definitely has to be a balance. No matter what industry, what organization, the balance between the data and the insights, it needs to be in line. You can’t rely too heavily on it- you can’t go blindly with the data. You can’t go blindly with your gut. You have to find the right balance.
[00:15:19] Josh: I’ve heard a concept similar to what you’re describing. There’s so much such a focus on data and that’s typically referred to as big data. I hear less often about this idea, but I think it applies to what you’re describing as the term thick data. The thick data is there to provide the context, the nuance, the details that really make a story come together. That’s certainly something that I found is also a must-have because you can get a ton of data points, but without the right expertise to understand what these data points are indicating, you may not accurately- the data or you may not have the context that you need to understand why this is the data that you are getting. That understanding and being able to bridge those pieces together through the arts, is certainly how you maximize what data is bringing.
[00:16:16] Megan: Absolutely. I think what you said about context is absolutely key because the sad fact of the matter is that data never gives you one right answer. In almost anything that we’re doing, there’s no objectively correct answer. The data will lead you to a very good answer in the best case, but that context and the thick data, knowing in the entire landscape that the decision you’re making has to lie in, that could skew- you could have the exact same points, do the exact same analysis, but I’m picturing a scatter plot, one little data point could throw the entire curve off and you need someone in the organization, someone who can decide, first of all, if that data point is relevant or not, do we just throw it away, or do we say, “Actually, this one data point, this outlier is the most interesting of the whole bunch, and this is where we can learn the most, and this is where we start crafting our story”? That’s also, I think, the most interesting, those little outliers, and finding the context.
[00:17:37] Josh: There are so many very in an operation, and the data’s really good at “Here are all the different pieces right. Here are the facts.” Ideally, that’s what the data is referring to. Now, you mentioned- if data is dirty, it isn’t too helpful. Let me ask you, in your experience, are there any best practices with regard to data that come to mind that manufacturers or people in supply chain should be aware of?
[00:18:11] Megan: There are lots of best practices when it comes to data, and from the technical side, or the statistical side, or the data integration or cleaning side, there are all kinds of best practices, tips, industry standards to stick to. For more of an insights best practice, I think you really need to make sure that analysts and the people they’re speaking to aren’t too far apart, aren’t too siloed because really, I like to say that data is great, we talk about data-driven organizations all the time, but really data shouldn’t drive. Data can navigate. Data absolutely deserves a spot in the front seat, but it should be in the passenger side looking at the map, helping you get to where you need to go.
A human needs to be behind the wheel. A human needs to drive and judgment is really what we should be relying on, not just blindly following the data, and an analyst or anyone who has access to the raw data needs to be able to add in that layer of insights, and to do so, they need to know the business context. They need to understand the operations. They need to know what they’re looking at. This is why black-box models and machine learning will get you pretty far, but you also need a human who’s going to be able to look at that and say, “Okay, this is great, but in our factory floor, that’s just not going to work. I know with my- call it intuition, call it judgment,” but you need that. You need business context in order to make the right decision over and above just the pure statistical ability.
[music]
[00:19:57] Josh: Hey, we’re going to take a real quick break to hear from our sponsors. Stay tuned for more, Conquering Chaos.
[00:20:04] Rob: Hey, listeners, it’s Rob. I’m one of the producers in Conquering Chaos. I’m right here with you for every episode, working behind the scenes to make sure everything is just right for your listening experience. Whether you’re a new listener binging content to help you conquer the everyday chaos, or a dedicated fan tuning in for each new episode, there’s one thing to always keep in mind, information is useless unless you use it.
Obvious, right? But it’s so easy to learn, forget, and then miss out on the opportunity to make real improvements to day-to-day activities. The folks at Parsable have an opportunity for you to learn, experience, and make real improvements to those same day-to-day activities. Get rid of paper on the factory floor. It’s the quickest and easiest way to make a measurable impact on safety, quality, and production.
Think about it, paper-based checklists, forms, and SOPs isolate workers from getting the information they need when they need it, which leads to a number of inherent inefficiencies that you probably accept as a part of your own everyday chaos. As a result, you can’t respond quickly to problems. You struggle to standardize the completion of critical tasks, and you miss out on new continuous improvement opportunities.
Parsable is proven to help across a number of different functions, including autonomous maintenance, line changeovers, in-process quality checks, and more, which has helped industry-leading manufacturers reduce unplanned downtime, increase OEE, improve throughput, and more. See for yourself how easy it is to bring a connected digital experience to your frontline workers by using Parsable risk-free for 30 days. Check the show notes for the link. All right, back to the show.
[music]
[00:22:13] Josh: I love that you’re putting data in its place. Data is not something that we serve or the process serves. Data is there to be another tool that’s leveraged by the people who are ultimately making the business decisions. It could be a very powerful tool, it could also be a misleading tool. That’s why it’s important to have the appropriate context, bring in the expertise, investigate, interrogate, dispute, argue, go over, understand it, and know it.
That’s great. I want to dig into that idea that you brought up of the power of stories. I also want to tie it into some of your more recent pursuits. Just some context, one of the conversations that we have consistently on this show is about recruiting, retaining the next generation. Manufacturers are struggling with that. A lot of these conversations focused on millennials, more so now Gen Z as well.
Really focused on how do we get millennials in, but how do we get new grads, the new high school grads, new college grads, Gen Z into our doors, or into our facilities. It’s not going to be long though before we’re talking about how to recruit the “next” next generation, which is Generation Alpha. That’s the term used to describe kids born between 18 – 24.
They’re still coming up, but they’re already here. They’re already growing up. We need to keep this in mind when we’re thinking about how to appeal to these younger generations because pretty soon here, we’re not going to be targeting Gen Z for these jobs. We’re going to be trying to appeal to Generation Alpha. You talked about your own experience with- it wasn’t until college that you really started to explore and have this epiphany about, “Oh, the world works with these practices that could be shared,” and talked about it earlier. I would love for you to talk to us about how you’re helping expose these next generations to these types of roles that kids don’t often-
[00:24:09] Megan: Sure. The main way that I’m working on that is through my Supply Jane & Fifo Adventures series. There are two books in the series so far about Supply Jane, who is a plucky little, probably pre-teen heroine, and her canine companion whose name is Fifo and they have so far gone on two adventures, more are planned. In each of these adventures, they investigate and bring to light a logistics or supply chain or operations management concept that then they help out a hapless business owner to improve their processes and save the day along the way.
These characters, they’re cartoons. Supply Jane has purple hair. They are hopefully very relatable to kids. It’s not some dry textbook, like, “Let’s learn about perishable inventory management today, kids.” It’s a little bit more fun.
[00:25:17] Josh: It’s interesting that you bring up this way of teaching these concepts because it reminds me of a book that I really appreciated called The Goal, which I’m sure you’ve read it. Classic operation management–
[00:25:28] Megan: It’s my favorite.
[00:25:29] Josh: Theory of constraints, and how it’s not dry like, “This is what the theory of constraints is.” It tells the story of a plant manager in charge of a struggling plant, the lessons that he goes through with his team, and the practical applications they put in place to not only meet the demands of their facility but exceed them. That helped me contextualize these lessons as an adult. I can certainly see the power of story and introducing these concepts and ideas to children.
[00:26:05] Megan: Absolutely, and I will say, I remember very clearly, I read The Goal during my first year of MBA school. I remember thinking, “This is incredible. I love this book. It’s a novel, it’s interesting. It’s not just a textbook,” and I remember thinking, “I want to write a book like this someday.” I don’t know that Supply Jane Clears the Way is quite to The Goal level, but I’m pretty proud of it.
It was definitely, definitely inspired by The Goal. What you said, Josh, about The Goal helping you to conceptualize some of these ideas, of course, the book is set in a novel setting, and it does talk about plant optimization, but one of the most evocative scenes in the book was when the scouts go camping, and they have to- this is complete- this does not take part or take place in a factory at all, but they’re walking up a hiking trail, and one kid keeps falling behind.
They finally realize it’s because he has so much weight in his backpack. Sorry, spoiler alert, probably shouldn’t have said that but then he’s the bottleneck, they realize that, and then they clear the bottleneck. They make sure that he’s okay, and then the entire Scout troop can speed up. It’s exactly the same content, but it’s a completely different setting, and it helps you just to understand it that much better.
[00:27:35] Josh: Well, absolutely. After reading The Goal, I could not sit in traffic without thinking about the same principles and ideas. Every time, I would think, who’s the Herbie of the group? Who’s the Herbie on the road right now? When we think about this idea, with these types of stories, how do you get kids interested in these types of careers?
[00:27:59] Megan: One thing, it’s giving kids the words to describe things that they’ve probably already noticed. For instance, we were talking earlier about this hidden logic, these rules that make the world work. Kids have noticed these. If we’re talking about First In, First Out, or inventory, stock rotation, kids can go to the grocery store and see expiration dates on the gallon of milk, and hopefully, they’re not reaching to the very back to grab the freshest milk because that will mess up a lot of planning.
These concepts are- they’re common sense, but they’re not common knowledge. By making them more- bringing them to the forefront, helping kids to see some of these concepts, and use them, identify them in other situations in their life, they can start to say, “Hey, I really like this. I like making sure that I’m using up the leftovers in the fridge before I start eating something new,” or, “I really like this concept of clearing the bottleneck and making sure that everything is going smoothly and finding the place where things slow down and then focusing my efforts there.”
The quicker we can get kids the language to start articulating these ideas, the sooner they can start thinking about, “Hey, I’m really good at this. Maybe I want to do this when I grow up.”
[00:29:24] Josh: That’s an interesting point, this idea of, “Maybe I’d want to do this when I grow up,” because if we think about what we’re exposed to– If you’d have asked me what I wanted to be when I was a kid, I would say a superhero. I don’t have any superpowers yet, I’m still working on that. The other options that kids are exposed to; firefighters, police, doctors, lawyers, these are common jobs that are talked about, and they’re great jobs, don’t get me wrong. People should absolutely grow up and think, “Oh, I would want to do that,” but I think what it highlights is that there’s no representation of some of these critical jobs to making the world go around. In fact, most of our listeners have these critical jobs, which was highlighted and spotlighted throughout the pandemic, and it helped bring exposure to these ideas and the importance of these roles, but people don’t grow up thinking, “I want to work in supply chain,” as a kid. I think it sounds like you’ve discovered some of that for yourself.
[00:30:27] Megan: Yes. One of the things you just mentioned, you said you think of firefighters and policemen and doctors and lawyers, and for kids, a lot of that is because if you go to the jobs and careers section of the children’s library or the Amazon category, children’s jobs and careers book, which I’m very familiar with, there’s a lot of books about firemen and policemen and doctors because they’re easy to draw. They’re easy to visually represent. A fireman has a uniform, a policeman has a uniform, a doctor has a stethoscope, and you can’t– It’s much more difficult to draw a cartoon that at first glance says, “Oh, this guy’s a procurement manager. This guy’s a demand planner,” so I think that some of it is just– We need to make things more vivid, more visually sticky so that kids can picture what somebody who works in supply chain or manufacturing looks like.
I think we should have a Halloween costume test. We need to figure out if a kid came and said, “Hey, mommy, I want to be you for Halloween,” how do we represent that? If you work in manufacturing, maybe you work in a clean manufacturing facility, so you’re wearing a little white suit. Maybe you’ve got a hard hat on. Maybe you’re wearing a polo shirt because you work from home. We need to make it easier for kids to visualize careers in these fields, and then once they can visualize it, articulate what they want to be, we should have no problem getting the next generation into manufacturing and supply chain careers.
[00:32:24] Josh: I think you brought up also an interesting point of enabling parents to share their stories and tying the impact of what the parents do and the value that they’re bringing on the consumer’s life and the world at large and helping kids put that into perspective so that they could say, “Well, when I grow up, I want to be just like mom or just like dad,” that’s a big benefit to stories like these.
[00:32:52] Megan: Yes, I think so too, and I hope that these books do spark those conversations and help- even if mom or dad doesn’t do exactly what Supply Jane and Fifo do in the book, they can at least start to build the parallels and say, “Just like Supply Jane helped out Uncle Manny, when I go to work, I help about my boss or I help out our suppliers or I help out our customers by moving things upstream, downstream.” You don’t really move things upstream, probably downstream. To start giving the shared language and to help make these concepts a little bit more accessible to not only- hopefully, but there’ll also be a nice useful, meaningful conversation, and then hopefully, the kid will at the end of the bedtime story go to sleep, that would be my ideal use case for the books.
[00:33:54] Josh: Yes, and look, data shows that the roles, the careers that parents have does play a pretty big impact in a child’s future career, I would say, interests. One of the data points that we asked them is where they got their perception of manufacturing and whether it was positive or negative. It was- about 50% were like, “My family, my parents specifically.” We can’t undersell the importance of the family being able to clearly explain, “Here’s what I do, here’s the impact,” in a way that can resonate and appeal to kids.
Your response- your work is Supply Jane and Fifo, the dog, they’ve already got a few adventures, you mentioned a few of them, they’re tackling problems within a dragon food factory, and with a dragon egg distributor as well. I’m sure there’s more on the way. You mentioned a couple of the ideas and concepts that kids get to learn through the stories of Supply Jane and Fifo, the dog. Can you talk a little bit deeper about some specific supply chain and operations examples that kids will be exposed to terminology impact process?
[00:35:18] Megan: Well, yes, as you said, the newest book, Supply Jane Clears the Way, takes place in a dragon food factory. The illustrations are fair- well, I don’t want to say accurate, but they show very clearly an assembly process, a factory, so it’ll start to help kids- this would be a great opportunity for somebody who worked with a similar setup to say, “This looks kind of like when I go to work all day. This is what it looks like,” and maybe read the book and then bring your kid into the shop floor sometime and say, “Does this look similar? Does it look different? Let’s do a compare and contrast.”
That’s one thing. I try to be- I made sure that we were very clear with the illustrations, that they should be as realistic as possible. One of the things, I work with an amazing illustrator. Her name is Anita, give her a little shout out here, and she’s incredible. One of the original sketches came back. There was a scene in the loading dock and there was the safety tape on the dock, and there was a cart that had two of the wheels over the safety tape. I sent it back and I said, “Anita, we cannot have a cart like this. We have to imagine the impact we have on the next generation here because I’m sure that this will be when Gen Alpha starts going into the workforce, they will all cite my books, just like we’re citing The Goal as major influences.” I wanted to be responsible and make sure that we were illustrating proper warehouse safety practices.
[00:37:06] Josh: Yes, you have to be a good example and a true example. You had mentioned bottlenecks, you mentioned the ideas of First In, First Out, and I think also there’s an idea with spotlighting, these types of roles and principles in this way brings an element of importance to it, an element of prestige to these types of roles as well.
I think when you and I were talking earlier, one of the things you had mentioned is that people don’t really grow up and say like, “Well, I want to be a procurement manager and work there.” In a lot of these roles, we tend to fall into these things, and you had asked a good question at that time, which is, “What if that wasn’t the case?” I think that that’s such a compelling idea in the prestige that’s spotlighting it in any children’s book and other media forms as well, is something that could really help change perceptions of these roles because the industry is certainly struggling with perceptions.
[00:38:09] Megan: No, and you’re exactly right. I’ve talked to so– So many of my colleagues said, “Yes, I just landed here. I certainly didn’t set out with a nice clear-cut career path that would get me into this supply chain position, but once–” By and large, once everyone’s there, they love it, so why not? Why don’t we try and get kids to enter into this career path more intentionally? The quicker and earlier that we can get kids interested, get kids thinking about this sort of thing, it’s not like anybody wastes a lot of time wavering, but if we’re getting kids interested, if they decide on this particular career path earlier on, they can be much more intentional about it.
They can start looking for different opportunities, different angles that they can come at it from, and it doesn’t have to– I think some of the prestige element that we talk about these days is that we tend to view these sorts of jobs as, eight to five, you go to work, you come home, you don’t really think about it at all, between your clocking out and clocking back in.
We’re also talking about the generation that is growing up with Instagram, with TikTok, with all kinds of social media, so why not? We’ve got influencers for everything else. Why don’t we have manufacturing influencers or why don’t we have more? I’m sure there are some. Why don’t we have supply chain influencers? The quicker that you decide on one of these career paths, the quicker you can build more holistic– It doesn’t have to just be “clock in and clock out”. It can be much more integrated.
[00:40:06] Josh: I think when we look also at the number one concern for Gen Z, typically, from a world view perspective, is climate change and sustainability. We’re seeing a lot more engagement in, “What are the activities or careers that I can pursue that help makes a difference here?” I can only imagine that Gen Alpha is also going to share that maybe even more so, and by exposing kids to these ideas, then they have a tangible way of going, “Here is a cause that I care about. Here’s a way that I can actually impact and make a change to and contribute to this cause that I care about so passionately.”
That’s another thing that I see there as far as why we should engage and tell these stories and tie to the importance and equip parents to be able to talk with their kids about it in a way that can appeal to kids. I’m certainly excited about those opportunities.
[00:40:59] Megan: Absolutely. Again, it’s a much more or applied way to when you have these concerns about sustainability, you can think about them. You can talk about them, you can read about them, but at the end of the day, you need to go and do something about them. If your career is moving goods around the world, any little tiny change you can make there will have huge ramifications. It’s a great way to put that into practice.
[00:41:28] Josh: Absolutely. How can listeners learn more about the adventures of the Supply Jane and Fifo? Oh, we got a surprise guest.
[00:41:35] Megan: Yes. My cat is- she’s ready to tell everybody. What she was saying, if I’m may interpret, was that you can find more at www.supply-jane.com, and that’s got all the information on the books. They’re also available in the US on Amazon.
[00:41:57] Josh: Wow. You are a pro at interpreting what cats are saying. That was really well put. I couldn’t believe that she was wanting to answer so quickly. Well, just in time for the holidays, check out Supply Jane and Fifo and their adventures throughout the supply chain. Check the show notes for a link and bring a unique adventure to your kid this holiday season. Megan, thank you so much for joining us today.
[00:42:24] Megan: Thank you, Josh. This was so much fun. Thank you.
[00:42:27] Walt: Hey, all. It’s Walt here. I’m another producer for Conquering Chaos. Before you go, if you’re not ready to try Parsable to help you get rid of paper, why not watch a quick video instead? Check the show notes for a link to a demonstration Josh put together to show frontline workers what it’s like to use a dynamic digital experience to get work done. In it, Josh shows you how using a modern-day app enables you to connect to people, information systems, and machines, just like the apps you use in your personal lives. Take a look and let us know what you think.
[00:43:06] Josh: That’s the show. Thank you so so much for joining us today. Conquering Chaos is brought to you by a Parsable. If you’re a fan of these conversations, subscribe to the show and leave us a rating on Apple Podcasts. Just tap the number of stars you think the show deserves. As always, feel free to share what’s top of mind for you and who you think we should talk to next. Until then, talk soon. Take care, stay safe, and bye-bye.
Listen to find out how you can get younger generations interested in Supply Chain