Meet the Next Gen of Manufacturers: Tu Cao
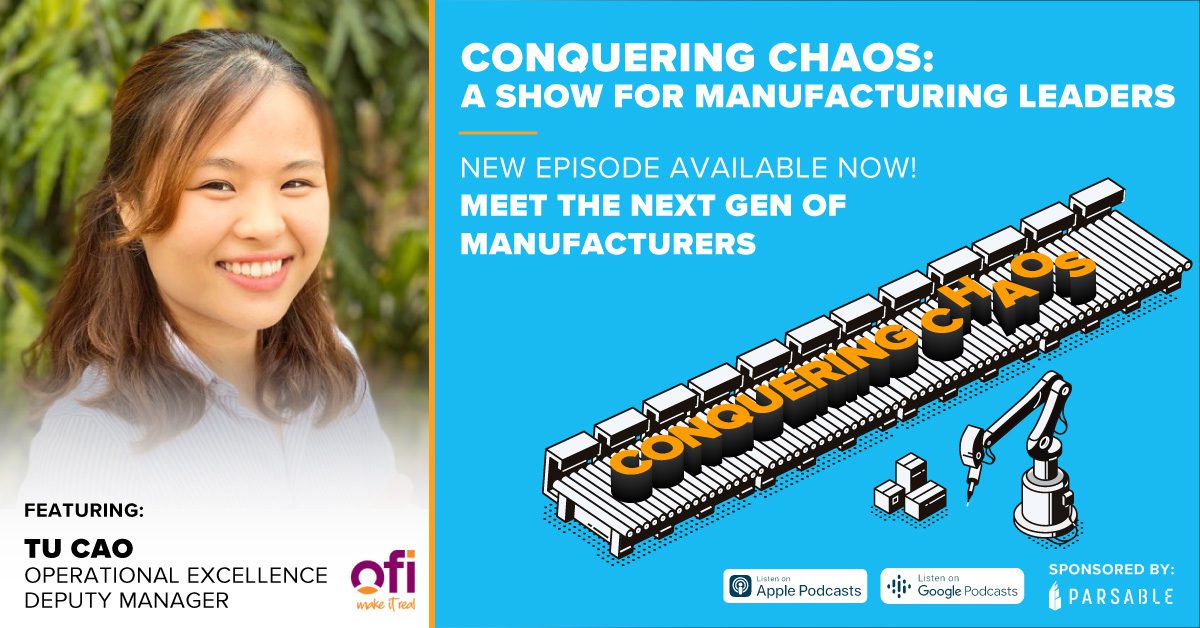
It’s no secret that manufacturing and industrial organizations are struggling to recruit and retain millennials and Gen Z workers.
As an aging workforce nears retirement, it has become an urgent issue with companies scrambling to fill these positions.
So, the million-dollar question is: How can we attract the next generation to manufacturing?
To answer it, we’re talking to Tu Cao, Operational Excellence Deputy Manager at ofi, a global leader in food and beverage ingredients. She’s a member of this new generation, and in this episode, she shares what piqued her interest in manufacturing and what the industry needs to understand in order to bring in a younger workforce.
Topics covered:
- How to get more kids interested in becoming builders
- Misperceptions about working in manufacturing
- Advice for anyone interested in pursuing a manufacturing career
- Advice for companies looking to attract young workers
______________________________________________________________________________________________________________
Are you ready to start your digital transformation journey? Request a demo today.

______________________________________________________________________________________________________________
Check out the full episode below:
[00:00:00] Tu Cao: If the leaders want to recruit and retain young workers, they should delegate jobs to the young and give them ownership.
[00:00:15] Josh Santo: Welcome to Conquering Chaos, this show for manufacturing leaders. In each episode, we’re connecting you to the manufacturing leaders of today who are driving the innovations needed to future-proof the operations of tomorrow. If you feel like your time is spent fighting fires and trying to control the everyday chaos, this show is the show for you. My name is Josh Santo. I’ll be your host. Hey, y’all. It’s Josh. Before we get into this episode, I wanted to put this into your ear. If you like the types of conversations we’re having, you’ll enjoy the content that we share through our mailing list. Go to parsable.com/podcast. Scroll to the bottom of the page and sign up to get more insightful content delivered directly to your inbox. Okay. Onto the show.
All right, welcome to the show. This episode is going to be a special episode. This marks our first conversation about what we’re focusing on the next generation of manufacturing. Now, we’re not talking about technology. Necessarily, we’re talking about people. The next generation of the workforce. This episode is bringing to life the voice of one of those individuals in manufacturing. One of those that we want to highlight is the voice out because as we all know, within this industry, we are struggling to attract and retain a younger workforce. It’s important to hear from that younger workforce and those individuals who choose a career in manufacturing.
With us today is Tu Cao. She’s the deputy manager of the operational excellence department in Cafe Outspan Vietnam producing soluble coffee. Her factory is a branch of Olam Food Ingredients, also known as ofi which is a global leader offering naturally good food and beverage ingredients and solutions. She’s worked for ofi for three years, starting as a graduated engineering trainee. She has been a coordinator of several digital projects focused on improving product quality, overall standardization, as well as energy and yield optimization. She’s done a lot in her brief career. She’s here today to talk with us about her experiences and what drew her into manufacturing. Welcome to the show, Tu. How are you doing today?
[00:02:36] Tu: Hey, Josh. There’s most of the excitement here and I’m privileged today to chat with you on the podcast about millennials and Gen Z in manufacturing.
[00:02:45] Josh: We’re happy to have you. Now, before we get a little bit into why you chose to get into manufacturing, I’d like to hear a little bit about what your day-to-day looks like within your role.
[00:02:59] Tu: As I shared with you, I’m working from home. I will tell you about a routine a month ago when I say work in a factory. I live in Ho Chi Minh city and a factory is located in a neighboring province. After communing with the factory by bus, the first thing I do is make a traditional approved coffee. I’m fun of it because the strong taste gives me the energy to confront a whole day. After that, I check my to-do list and depending on the phase of the project, I may do data analysis or explore more potential functions in the project platforms. Later, I chair the operational review being held inside the production area and I use the light as time for Gemba walk. I can observe the actual work process, engage with coaches and then gain knowledge about the machine operation and so on.
[00:03:58] Josh: When you go through that operational review and you’re looking to observe the work process, engage with employees, gain that knowledge, what is your goal in doing that?
[00:04:12] Tu: My goal is that first I’m still young in the factory just three years and the factory is a high technology. At this time I’m still gaining more knowledge about an operation because my background is not engineering and moreover because I carry out continuous improvement projects. I need to understand the work process and improve them and also understand the obstacle that the team is facing.
[00:04:40] Josh: I want to talk about your interest in manufacturing. It’s not a secret that manufacturing and industrial organizations are struggling to recruit and retain both millennials as well as Gen Z but it’s particularly concerning right now due to the aging workforce. You’ve got people retiring and an inability to bring people in to fill these jobs. The last number I heard is and this is a US number is the expectation that around 2.9 million jobs are expected to go unfulfilled by 2030. It’s a situation that people are struggling to address right now. That’s part of the purpose of this episode is to talk to the members of the next generation to understand what actually drives those interests so that we can highlight those voices to other people and share those stories so that people can see whatever misperceptions they might have about the manufacturing industry, there are some real positive and fun and exciting opportunities there. I’d like to hear from you Tu, what inspired you to pursue manufacturing?
[00:05:53] Tu: Let me share with you a bit about my childhood hobbies. Back in the years when I was in high school, I’m a fan of physics as a natural science is learning how the universe behaves. Moreover, I can use the lights as an application to my daily life. For example, I installed LED lights for my toys. When I come to the university, I opted for the course of industrial management in a technical university because I can study modules of engineer science and management. Hilariously, while studying, I felt overwhelmed with manufacturing subjects, such as maintenance or quality management and this led to feelings of self-doubt. After graduating, I decided to apply for an office job in demand and supply planning. The tasks are just making weekly plans and proceeding with purchase orders in SAP day in, day out. For up to three months, I failed at this boring job, which completely crushed my spirit. I decided to pursue a more vigorous career. Then I applied for several training programs in multinational food companies and luckily I engaged with Olam.
[00:07:11] Josh: I want to dig into another thing that you said, you focused on industrial management but there were some feelings of being overwhelmed. You mentioned subjects like maintenance and quality and how that led to some self-doubt. Can you talk to us about what your thought process was and why that led to you feeling doubtful and pausing on pursuing the more vigorous career?
[00:07:43] Tu: It was the term when I was in my second year in university. The motto was manufacturing management and at the time I need to solve some production maths. It’s called light balance. The teacher gave that in class. There are some steps and each step has its own capacity. As a student, I need to calculate the balance light to prevent a bottleneck. At that time the math was a bit complicated and I could not balance the light because there are a lot of variables for me and not okay some maths is, let me remember, this is maintenance meantime to repair. Actually, in the working environment, we have a lot of tones to calculate that KPI but when I was in university, I need to calculate by myself and I was struggling to calculate that one. I felt overwhelmed.
[00:08:48] Josh: I can understand that. I think we see that with a lot of topics in general, not just with manufacturing. There’s very much a focus on. You as a student need to understand this equation or this function or this process. I absolutely agree. You need to know the why behind it and the principles that make it work. As you mentioned, there are tools out there that make this much easier and much quicker to process and understand. It’s interesting to hear that while there may be some difficulties in some complicated topics, we’re at a point in how factories are run where a lot of these, what used to be manual activities are supported by tools which I think is an important topic to make sure people are aware of. Let’s talk a little bit about your first role as young manufacturing professional.
[00:09:51] Tu: When I joined Olam in the trainee program, I rotated in different units, such as edible nuts, spices, and soluble coffee to learn processes and then carried out improvement projects. After four months, I was the SI of fixed position in the soluble coffee factory which is the one I’m working, Cafe Outspan Vietnam. Working as a process improvement assistant, my first eight months were mainly learning the operation of sophisticated machines. While doing simple tasks such as writing standard operation procedures, I obtained a lot of knowledge that I still use today. My most memorable task is the optimization of DSL consumption in the roster. At that time, I deeply studied the flow of materials and heat to find opportunities to improve energy usage. That time was valuable as I can be involved in almost every department ranging from production engineer to quality control, even though the tasks are minor, but I had built a firm base for my current career.
[00:11:06] Josh: Hey, we’re going to take a real quick break to hear from our sponsors. Stay tuned for more Conquering Chaos.
[00:11:12] Rob: Hey listeners, it’s Rob. I’m one of the producers on Conquering Chaos. I’m right here with you for every episode, working behind the scenes to make sure everything is just right for your listening experience. Whether you’re a new listener, binging content to help you conquer the everyday chaos, or a dedicated fan tuning in for each new episode, there’s one thing to always keep in mind. Information is useless unless you use it. Obvious, right? It’s so easy to learn, forget, and then miss out on the opportunity to make real improvements in day-to-day activities.
Well, the folks at Pasarble have an opportunity for you to learn, experience, and make real improvements to those same day-to-day activities. Get rid of paper on the factory floor. It’s the quickest and easiest way to make a measurable impact on safety, quality, and production. Think about it. Paper-based checklists forms and SOPs isolate workers from getting the information they need when they need it which leads to a number of inherent inefficiencies that you probably accept as a part of your own everyday chaos.
As a result, you can’t respond quickly to problems. You struggle to standardize the completion of critical tasks and you miss out on new continuous improvement opportunities. Parsable is proven to help across a number of different functions, including autonomous maintenance, line changeovers, in-process quality checks, and more which has helped industry-leading manufacturers reduce unplanned downtime, increase OEE, improve throughput, and more. See for yourself how easy it is to bring a connected digital experience to your frontline workers by using Pasarble risk-free for 30 days. Check the show notes for the link. All right. Back to the show.
[00:13:23] Josh: When we talk about the difficulties manufacturing’s having with bringing in the next generation of workers, some of the research that’s gone out, particularly from the Manufacturing Institute, their research has found that there’s a perception among the younger generation that manufacturing is dangerous or behind the times or the fact that there’s not much emphasis on vocational education or apprenticeship is leading to the skills gap. Even if people are interested, do they have the skills that are needed where they set up with the foundation to successfully enter the industry?
Then there’s also a mismatch between where younger people want to live and where manufacturing factories are located. There’s a preference of the younger generation to be around the bigger cities. Whereas some of these factories are oftentimes in small towns, rural areas, or places that don’t have the same type of appeal that the younger generations looking for. I’m curious to hear about your perspective. Before joining manufacturing, what were your perceptions about it? Did you want to work in manufacturing?
[00:14:47] Tu: Yes, I’ve shared that. Four years ago, I did not plan to work in this field at all. At that time I underestimated myself by raising the question that, what can a fresh student do in a factory? I have no engineering background and I turned back to my degree. I call that, I can apply for an office job and still have a successful career. However, it was not as my expectation. I changed my direction and fortunately, I saw a couple of recruitment posts on the page of my school. I gave myself a try.
[00:15:26] Josh: Let’s talk about you’re now in manufacturing but it’s still pretty common for people in our generation, in your generation to not be as interested in a manufacturing career. Why do you think that is? How come people that, you know aren’t getting more involved in manufacturing? What are your thoughts?
[00:15:49] Tu: People in my generation, such as students in my school generally are not interested in factory jobs. The main reason I heard from them is the nature of work. People imagine that when a person works in a factory, they need to work too many places to assemble engines, take samples or supervise the task of subordinates and it sounds fatiguing. The second reason is the location of the factory. As you shared that normally they are in the outskirts of the city or in suburbs. The long route along with traffic congestion probably exhaust some people physically and mentally.
The last one is that technical students generally adopt new knowledge quickly hence up to graduating, they can enroll in various shops. Some of my friends in a score of electronic and electrical now working in software companies. They are capable as they have learned the language of C plus, plus and they are good at maths. They can learn other languages. Others choose to work in industrial services which they can work in the office and they just travel to factories of customers sometimes.
[00:17:02] Josh: I think you raised up a good point about the newer generation being very technically minded, being very digital-first. There are a significant amount of opportunities in a variety of different industries for individuals who are seeking something like that. One of the things I think about is the big tech companies that are out there, they do a really good job of recruiting people. Some of that has to do with the fact that what they’re working on is the latest and greatest technology that people all over the world, businesses all over the world use. That ties to that preference for the younger generation to be connected to a bigger impact. The work that you do is affecting millions of people. That’s something that really appeals to individuals which one of the things we need to do is make sure that that’s understood about manufacturing.
The goods that are produced are the goods that millions of people rely on every day. I think that this also ties in to some of those perceptions about manufacturing being behind the times because that is a perception, regardless of whether or not it’s true. When you have someone who prefers to work in a more technical and advanced environment looking to work in software or learn the different software languages to build different products or to automate certain tasks, you can see why there’s a preference to move to a different type of industry, as opposed to manufacturing. Another common perception is that manufacturing is dangerous. You’ve worked in manufacturing firsthand. Do you think manufacturing is dangerous?
[00:18:50] Tu: I have to share that in terms of work-related disease, every occupation has its own risk. Office clerks possibly face vision problems due to continuous exposures or blue rays from an electronic screen. I’ve heard that you’re facing this one, right?
[00:19:06] Josh: That’s right.
[00:19:07] Tu: People sitting or standing for a long time may suffer from orthopedic disorders and basically negative impacts are invisible and they are recognized up for a long period. By contrast, the factory environment is somewhat riskier as hazards can cause fatality. There are many harmful materials that you need to avoid in a factory such as electricity, high-speed pressures, or chemical. Back to your question, the important thing is that employees need to be aware of risks. They must wear sufficient or personal protective equipment. Do not work in unsafe harsh conditions to mitigate hazards. The truth is that accidents are preventable when people have safe mindsets. When people have a good attitude to what is safe in their environments and their own risks are controlled.
[00:20:04] Josh: I completely agree with what you said. There are risks all around us and you’re right. I’ve got my– it’s a different type of safety glasses, but they’re my blue light blockers. For blocking the– to reduce eye strain so I don’t have headaches or dry eyes, I make sure to stand and walk around because it does play an impact if you’re sitting all day, if you’re an office worker and I think what you’re highlighting is correct, you have to be aware of those things, wherever you are, in whatever environment, what could impact your health. Manufacturing’s no different.
Now, like you called out, there is heavy machinery. There are chemicals in place. There are different ways of powering these machines that could be dangerous, if not handled with care. That’s the important part that you’re calling out in any situation. If it’s not handled with care, if you’re not aware, if I don’t do something about this cord, that’s plugged into my wall, I could trip fall and hurt myself just as easily as if I were in a factory. Right.
There’s still those risks, no matter where you go. I think it’s a good point to highlight that it’s not that it’s dangerous. It’s about the culture and the behavior that exists. People have to be aware and they have to take responsibility and they have to look out for each other, for everyone else. I think another perception that I’ve often heard is this, there’s usually a description of manufacturing of dark, dirty, dangerous. I think they’re called the three Ds.
I want to talk about that idea of dark, because typically when people refer to a dark, they think about the technology that’s being used or just whether or not manufacturing is in line with current day practices. For example, the use of digital technology and the way that we use and we’re communicating right now. Do you think that jobs in manufacturing, do you think that they’re routine that they’re, non-creative that they’re lacking in technology? What’s your experience?
[00:22:17] Tu: This is true that in some industries, types of machine and change for their case, and you can imagine that in industries of ground or coal mining, when a machine is worn out, they just replace a new one. Even though there is some update, but this is unremarkable and others are not, we have seen that in automobile, in industry automated robots, has been used since a long time ago.
Recently in packing light, robotic arms are used to pick the cotton boxes into pallets to reduce human efforts. That is highly invested infrastructure. We have another technology that is informatic. In this, more companies want to build a smart factory. Now the operational data will be transmitted from various machines in manufacturing, like to an Iott half. That one will trigger actions to those kinds of machines and efficiency will be boosted by the practical information tank.
[00:23:30] Josh: What is getting you excited in your manufacturing career?
[00:23:34] Tu: My Job gives me a feeling that every day is a new day and I should live a fully free moment. When I started my career, I thought that my duty was only working in the line to ensure production outputs, meet targets. I was in the mood for self-doubt as my technical knowledge and problem-solving skills are not as good as mature employees. It took time for me to solve a process improvement us by term, involving a myriad of jobs. My strength has been identified. As a young person, I have had adaptability to technologies and I have that driven mindset.
Last year, when the factory applied a new digital platform, I can explore features that to enhance open operational productivity and having a technical career, I still utilize the line, my right brain function, my creativity, and I have decided that desktop calendars and distribute them to oncologists in a factory over. I can make videos for the company communication campaign. In the company, I use this tripod here and gimble to improve the stability of my videos. Also, the knowledge learned from the factory, I can apply in my daily life, especially the safety knowledge. When I travel, when I’m walking in a shopping mall using the escalators, I need to identify the emergency buttons to avoid a chance.
[00:25:08] Josh: Think that’s great. I do the same thing whenever I’m making toast-
[00:25:12] Tu: Okay.
[00:25:12] Josh: -at my house. When I’m going to take the toast out, unplug the toaster. I isolate the energy right there. I’m not locking anything out. I’m not tagging anything out, but I am isolating the energy source at that point to make sure that I don’t get electrocuted when I’m getting my toast out of the toasters. I completely understand what you mean about safety. I love that you’re not just being able to lead some of these digital projects because those are critical, right? The industry as a whole is targeting, how do we digitally transform? There’s a lot of different ways in which things have to change. Digital tools have to be in place.
It’s great to hear that you’re able to work on digital projects that are going to have an impact like this. Then the creativity side is super important. You’re making videos. I think that that’s so fun, right? That’s more modern. I’ve even seen some people make Tik Toks help get people engaged at work. It’s great to see that there’s, not just that, those technical projects, but that creative side as well. You mentioned really learning and applying some of those safety practices in your everyday life. What else are you learning?
[00:26:35] Tu: The most significant value is the ownership. When I’m assigned a task, I collect and analyze historical data. When a piece of data is met, I need to do trials to get it. Then I bring solutions by later driven approach. The presentation should not highly focus on technical aspects because it needs to be easily digested by top managers. In summary, I have full responsibility for the result of the task and keeping to that. The confidence has been boosted over time.
The second one is teamwork spirit. After years working in a factory, this one improved because when I work with mature colleagues, I use their experience because they have worked there for approximately 10 years. They have experience and I’m young. I have my database method. We work together and we achieve the main objectives.
[00:27:40] Josh: What advice do you have for people interested in a career in manufacturing?
[00:27:45] Tu: Yes, I would like to tell the young that if you have a technical background, for example, in the field of chemical or biotechnology and now you don’t know what to do. Just enrolling in the manufacturing sector is time, is the time for falling and getting up. Also if you want to develop in this sector, you need patience. There are some obstacles that await you such as the volume of knowledge in the factory, the physical energy spent, and the combination of various knowledge to solve a problem. After three or four years, it’s worthwhile.
[00:28:24] Josh: I think that’s a great expectation to set. If you have those interests, as you mentioned in chemical or biotechnology, this is a place where you can really explore those different topics in a way that you might not be able to elsewhere and be prepared to have to take some time to learn. That’s okay. Some things are going to just take some time for people to learn, understand, and get acquainted with. I think it’s important to emphasize that. Now, I would love to hear your perspective, just one final question, what do you think would help manufacturers recruit and retain younger workers?
[00:29:05] Tu: Yes. I will share this one from the point of view of a young that, if the leaders want to recruit and retain young workers, they should delegate jobs to the young and give them ownership. This will create the intrinsic motivation for the young to commit and achieve the target that you delegated, and at the same time leaders, because they have experience, should give the young directions. We can use a simple example is that when a leader asks the subordinate to climb to the ceiling and he gave a ladder, so he should direct his subordinate, which wall to lean the letter on that, to climb to the ceiling safely and fast. The last one is the succession plan because we are in a factory, there are many levels to be promoted. Then the leader should coach the young on how the leadership works and communicate with operators and how to understand the operation of the machines because, after five or six years, that young person will become middle-level managers.
[00:30:28] Josh: I think you’re absolutely right. That idea of ownership, that idea of focus on teaching skills, providing mentorship, and that last idea in particular, what is the path to go growth? What does a career look like? These are all concepts that if you look at some of the research that’s out there, big driving factors of how to engage the younger workforce when they are on the job, that ownership so that they can feel they are fulfilling a purpose, that mentorship so that they know that they are learning, and that progression path so that they understand and have appropriate expectations of what it would be like to grow in this career. I think you’re absolutely right and I think that’s in line with what we’re hearing. Look, Tu, I think this has been a really insightful common conversation. Are there any thoughts or comments that you’d like to share before we wrap up?
[00:31:28] Tu: This is a really great opportunity for me to hear and to talk to you, and to our audience about my experience, even though I’m still young and maybe my experience is minor, but I hope that it can help some young people to direct their career in manufacturing.
[00:31:52] Josh: Absolutely. I think it absolutely has. I appreciate your time. Thank you so much for joining us.
[00:31:57] Tu: Okay. Thanks, Josh. Have a nice day.
[00:32:00] Josh: You have a nice night.
[00:32:08] Walter: Hey all, is Walter. I’m another producer for Conquering Chaos. Before you go. If you’re not ready to try Parsable to help you get rid of paper, why not watch a quick video instead, check the show notes for a link to a demonstration Josh together to show frontline workers what it’s like to use a dynamic digital experience to get work done. In it, Josh shows you how using a modern-day app enables you to connect to people, information systems, and machines, just like the apps you use in your personal lives. Take a look and let us know what you think.
[00:32:42] Josh: That’s the show. Thank you so so much for joining us today. Conquering Chaos is brought to you by Parsable. If you’re a fan of these conversations, subscribe to the show and leave us a rating on Apple podcast. Just tap the number of stars you think the show deserves. As always, feel free to share what’s top of mind for you and who you think we should talk to next. Until then talk soon, take care, stay safe and bye-bye.
[00:33:38] [END OF AUDIO]
Listen to meet the next gen of manufacturers: Tu Cao