Digitize Your Forklift Inspections: Avoid Breakdowns and Accidents
An apple a day keeps the doctor away. In the case of manufacturing, an inspection a day keeps the penalties away. As corny as that may sound, it rings true. Workplace injuries are a common occurrence in manufacturing, especially when there’s heavy machinery in use.
One of the most common incidents on worksites and warehouses involves the use of powerful tools like forklifts, also known as powered industrial trucks. They’re an extremely important piece of machinery that helps keep your warehouses and worksites running efficiently and smoothly. Accidents are often the result of the machines not being properly maintained. Even if you’re a skilled operator, mishaps can still occur; machines can get damaged and things can spiral out of control if forklifts are poorly maintained.
Why Are Forklifts So Dangerous?
Forklifts are a piece of heavy machinery that are dangerous of a number of reasons; here are just a few:
- Forklifts are heavier in the rear to counterbalance heavy loads carried in the front, this uneven weight distribution can make it a difficult piece of equipment to handle.
- They weigh around 9,000 pounds, that’s three times heavier than most cars.
- Forklifts only have brakes in the front, which make it harder for them to stop.
- When loads are carried on a forklift they can often obstruct the view of the driver.
- Forklifts carry heavy loads to high places which is a dangerous combination.
- Forklifts are propelled by rear wheels which can cause the rear end to swing outward and increase the potential for tipping over during turns.
Forklift Accident Statistics and Why Your Team Should Operate With Caution
- On average 95 people are injured in a forklift accident every day and 1 person is killed in a forklift accident every 4 days in the U.S. (OSHA)
- 36% of forklift-related deaths are pedestrians (OSHA)
- Forklift overturns are the cause of about 25% of deaths (OSHA)
- In 2018 there were almost 8,000 forklift-related injuries, an increase of about 6% from the previous year (BLS)
- From 2011 to 2018, an average of 7.1% of workers missed work each year due to forklift-related injuries (BLS)
- The three leading injuries from forklift accidents were fractures (1,710), bruises contusions (1,570) and sprains/muscle tears (1,490) (BLS)
- Forklift accidents that result in serious injury total 34,900 annually (OSHA)
- Non-serious injuries related to forklift accidents reach 61,800 each year (OSHA)
Are Forklift Inspections Required?
Routine inspections and maintenance are required for heavy machinery and governed by the Occupational Health and Safety Administration (OSHA) 1910.178, which says forklift vehicles must be inspected at least daily prior to use at the beginning of each day or at the beginning of each shift, if it’s being used multiple times a day – to ensure there’s no mechanical breakdown or mishaps from one operator to next. During forklift inspections if a frontline worker finds that something is not working properly, they must notify their supervisor right away and lockout/tagout (LOTO) the forklift to make sure no one else uses the truck in the meantime.
Why Are Forklift Inspections Important?
Forklift inspection checklists are important for a number of reasons and can help avoid: accidents from occuring, mechanical breakdowns, operator injuries, incidents in the workplace by identifying and targeting defects and avoiding potential hazards.
Having a process in place where your frontline workers regularly use forklift inspection checklists is a great way to set safety standards among your team. Complying with these OSHA’s requirements is not only required, but it will help promote a safer and more productive work environment.
What Do Forklift Inspections Help Prevent?
Forklift inspections are intended to mitigate any potential safety issues from arising that could be caused by malfunctioning or damaged equipment – which could ultimately lead to a worker injury or fatality. For example, this includes things like hydraulic failure or stability issues that can cause the forklift to tip over. By conducting pre-shift inspections it ensures that your team can identify problem areas that need attention and forklift operators keep themselves and their teammates safe.
How Long Does It Take To Complete a Forklift Inspection?
It can take anywhere from five to fifteen minutes to complete a forklift inspection. Manufacturers should ensure their teams at worksites and warehouses have access to a digital checklist to guide them through the process. Completion of forklift inspections not only ensures your compliance with OSHA requirements, but it can also act as an audit tool.
What To Include on Your Forklift Inspection Checklist?
As your operators carry out their forklift inspections, they’ll want to make sure they check key components for signs of damage and/or excessive wear and tear. Some of the items that should be included in your forklift inspection checklist include:
- Fork condition, look for bending or signs of damage
- Chains for proper tension and greasing
- Carriage and load brackets for any signs of damage
- Check fluid levels: engine oil (dipstick), water level (electric forklift), hydraulic fluid (red cap, dipstick, the mast must be down, in neutral) and electrolyte levels (on electric forklifts)
- Inspect the mast chains and hydraulic hoses for leaks, cracks, and other visible damage
- Ensure that the load backrest extension is functioning properly
- Inspect the safety plates, labels, and warning decals
- Listen for any unexpected sounds like leaky hoses (hissing sounds) or other abnormal noises
- Any signs of visible fluid leaks from the engine or hydraulics
- Tire and wheel condition for chunking, tearing or damage
- Seatbelt for proper tension and performance
- Battery restraints
- Check all cables and connectors
- Test the truck brakes
- Cargo handling, inspect the forks, lift mechanism and tilt function
- Steering or control panel issues
- Ensure the operator manual is physically located on the truck and legible
How To Mitigate Risk and Promote a Culture of Safety With Connected Worker Technology
Forklifts should only be operated by experienced workers who are trained and certified. Injuries often occur because the forklift operator is not adequately trained, or they lack proper training on the specific model and type of forklift they’re using. Or, proper preventative steps like following forklift inspection checklists are not carried on a routine and regular basis. We can’t stress this enough, but it’s vital – and required – that forklift operators are trained according to employer and OSHA standards.
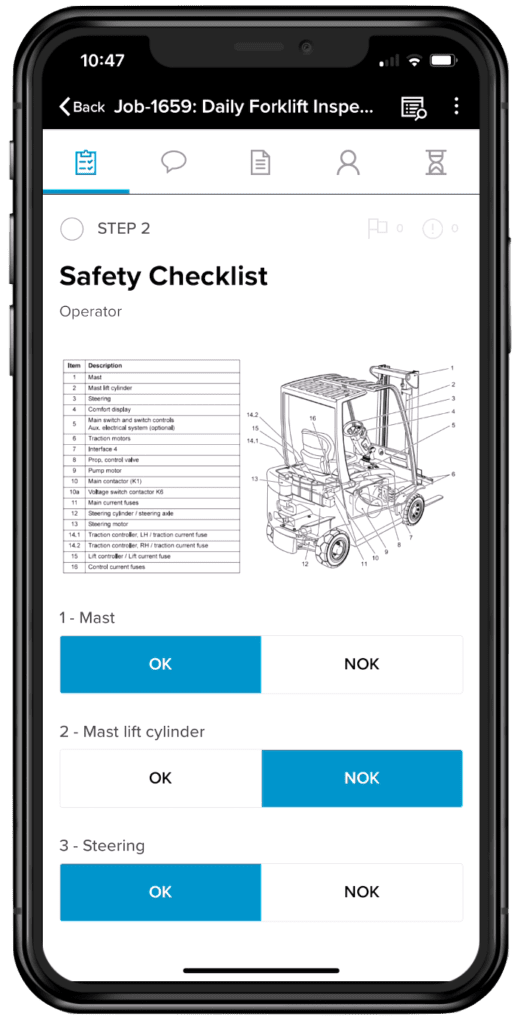
Your forklift checklist should guide you through what needs to be visually checked and what needs to be checked operationally. 81% of frontline manufacturing workers still rely on paper-based operating procedures to follow instructions and/or keep track of their work (check out our full research report here for more information). With that in mind, there’s a significant downside to relying on paper for a number of reasons: there’s room for human error, information gets lost, data isn’t accurately captured, pencil whipping occurs, and the list goes on.
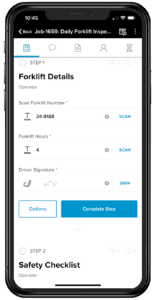
Adopting a digital forklift inspection checklist provides your team with step-by-step instructions so that nothing is skipped over – ensuring compliance. Workers can easily check off and capture data along the way creating a digital record, which is particularly handy if you undergo an audit.
Supervisors can stay up to date in real-time. If an operator runs into an issue during their inspection, they can make a note of it in the app and alert a supervisor right away. Connected Worker® by Parsable allows supervisors to view all operational inspections and report history in order to identify any concerning trends or forklift safety issues.
It’s critical to ensure your team is completing this process properly. Making sure they are adequately trained, and have access to the right tools and technology, can mean the difference between life and death.
Ready to revolutionize your operational workflows? Experience the power of Parsable’s Connected Worker® software firsthand and discover how our solution can streamline your operations by digitizing your frontline.