Welcome to the Next Generation of Manufacturing Allstars
According to a study by the Manufacturing Institute and Deloitte, 4.6 million jobs will need to be filled within the manufacturing sector by 2028 and 2.4 million jobs may be left open due to a lack of trained workers. The sector faces an immediate problem of a growing skills gap. And filling open jobs remains a top concern for many companies. The manufacturing industry struggles to recruit and retain a younger workforce with the technical skills, aptitude and willingness to learn new technology solutions.
The Current State of the Manufacturing Employment Gap
It should not come as a surprise that the Baby Boomer generation is retiring in droves; by 2030, all Boomers will have reached or surpassed the retirement age of 65. Since we can’t ignore the onset of the retiring workforce, there is little manufacturers can do now to stop their retirement.
Instead, companies must shift gears and focus on training new workers. This demands spending their time and energy into investing in technology solutions that will help with the advanced training needed to fill these highly skilled jobs.
This 2018 study by Deloitte and the Manufacturing Institute is the sixth survey in the last 30 years that has looked into the manufacturing job shortages and the inability of U.S. manufacturers to invest in the necessary advanced training that would work to solve the problem. The time is now to invest in advanced training.
In addition to attracting a new workforce, the work itself has become more difficult and requires a different skillset. The average CPG manufacturing floor looks a lot different than it did 30 years ago. Today, manufacturing is highly automated; all the highly repetitive and simple activities, previously completed by humans, can now be done by machines. But this doesn’t mean human workers are going away. Humans must be there to keep the machines running at peak efficiency or for highly intricate assembly processes. No matter how much high tech is incorporated into the shop floor, there will always be a need for humans in manufacturing.
The silver lining here is there is a way to both recruit and sustain the new incoming workforce, which many manufacturers have already embarked on by adopting a connected worker platform.
The Light at the End of the Tunnel – Humans and Technology
Not only is filling the employment gap a top concern for many manufacturers, but these companies also struggle with addressing the knowledge gap. Companies are trying to grapple with how to unlock the knowledge trapped inside the heads of the experienced, older generation of workers. And it’s not just extracting that knowledge, but how can you capture and digitize it for future employees?
Up until this year, many manufacturers have been so focused on building a strategy around equipment, IoT, eliminating downtime (check out these interesting stats on downtime) and improving operational efficiencies. And there is nothing wrong with that. However, if COVID-19 has taught us anything so far, it’s the importance of the role of humans in manufacturing. Knowledge and skills are starting to slowly disappear, as businesses work toward putting the right labor strategy in place. This is particularly true now, where we see that not all employees are physically present on the plant floor, staggering shifts, social distancing protocols, safety and risk mitigation – all becoming the norm.
Manufacturers are now looking to operators to do more, and to do more with less. According to a study by Axonify and Ipsos, nearly one-third of frontline employees do not receive any formal workplace training.
During my time at Parsable, I’ve asked manufacturers about their training program. I often get a bashful answer about following the most veteran employee around the plant for a week or digging up an old binder with paper work instructions.
This made me think back to a book called The Checklist Manifesto. The author, Atul Gawande, says, “The volume and complexity of what we know has exceeded our individual ability to deliver its benefits correctly, safely, or reliably. Knowledge has both saved us and burdened us.”
It’s unfair for us to expect so much from employees when we do not provide the building blocks for their success. The book highlights the importance of checklists in a number of manufacturing industries. Again and again, it states that if manufacturers provide workers with a simple and easy to comprehend checklist, they will increase their success rates. Connected Worker® by Parsable can help with that.
It is a simple and easy to use solution to help your frontline workers capture, digitize and make use of interactive, multimedia work procedures. We are seeing more and more companies investing in digital technology solutions to transform their workflows.
Leveraging Connected Work to Help Close the Gap
How do you create an environment that not only provides flexibility for your workforce, but promotes a culture of collaboration and knowledge sharing? So that, as the Baby Boomer generation slowly retires from the workforce, their tribal knowledge isn’t lost forever? With Connected Worker from Parsable, this knowledge is captured and documented within a digital solution available to all employees.
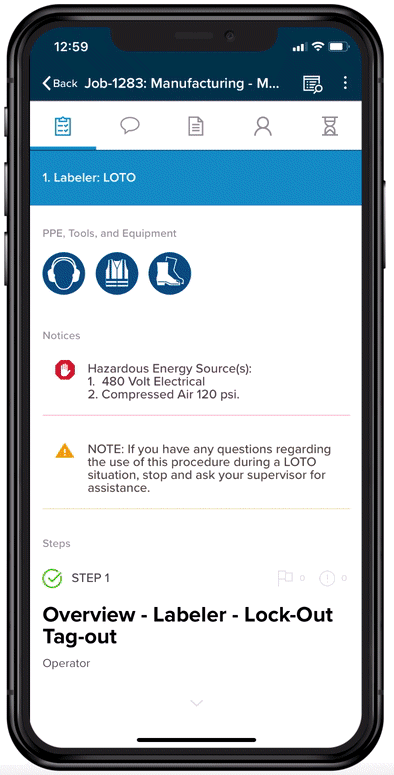
Parsable’s no-code authoring platform makes it easy to create digital instructions for tasks at hand. The question of who will create the digital work instructions is a very important one. An experienced operator is able to hone their skills over many years of practice. But, this kind of knowledge is difficult to transfer from one person to another. In fact, 57% of working Baby Boomers say they have shared half or less of the knowledge needed to perform their job responsibilities with those who will assume those responsibilities after they retire. Parsable’s digital work instructions are used to document tacit knowledge and eliminate the knowledge gap between your veterans and the incoming, younger generation of frontline employees.
Where will these highly skilled workers come from to teach the broader workforce? The answer to that is to look within your organization. Your team and internal experts can capture, digitize and author standard operating procedures (SOPs) in Parsable. The authoring platform also has revision history available. This allows your team to see recent changes that have been made and allows for you to revert back to older versions of a workflow. It also can’t hurt to get a second opinion on your work instructions. Parsable allows for teammates to comment and collaborate inside the authoring platform. We’ve seen this used across many of our clients’ locations to optimize the work instructions, while also standardizing processes across a number of locations.
It’s one thing to provide initial training, but even more worthwhile is to have the information readily available, in an easy to consume way, and when needed used to enforce procedural adherence among frontline workers. Parsable’s digital work instructions are used for “one point lessons.” One way to bridge the employment gap is to understand that Millennials and Gen Z are digital natives. The concept of giving them a 6-inch binder won’t work. Digitizing SOPs, replacing paper and analog-based printouts with smartphones and tablets, and training employees via in-the-moment collaboration and multimedia now serve as the tools of choice for the new industrial workforce. Parsable’s platform provides employees with photos, audio, links, GIFs and videos that can all be embedded within SOPs, to help workers learn on the fly. We have found video instructions placed within SOPs to be extremely useful among many of our customers, because they’re instructional and easy to follow along.
Parsable can be used to reduce procedural mistakes in situations where there are risky, unsafe or costly tasks that are frequently completed incorrectly. Our platform is here to provide the correct step-by-step information and collect data each step of the way.
Now is the time to build and sustain a highly efficient workforce for the years to come. Take the first step in investing in your workforce with Connected Worker by Parsable.