Manufacturing Skills Gap: Changes in Industrial Leadership
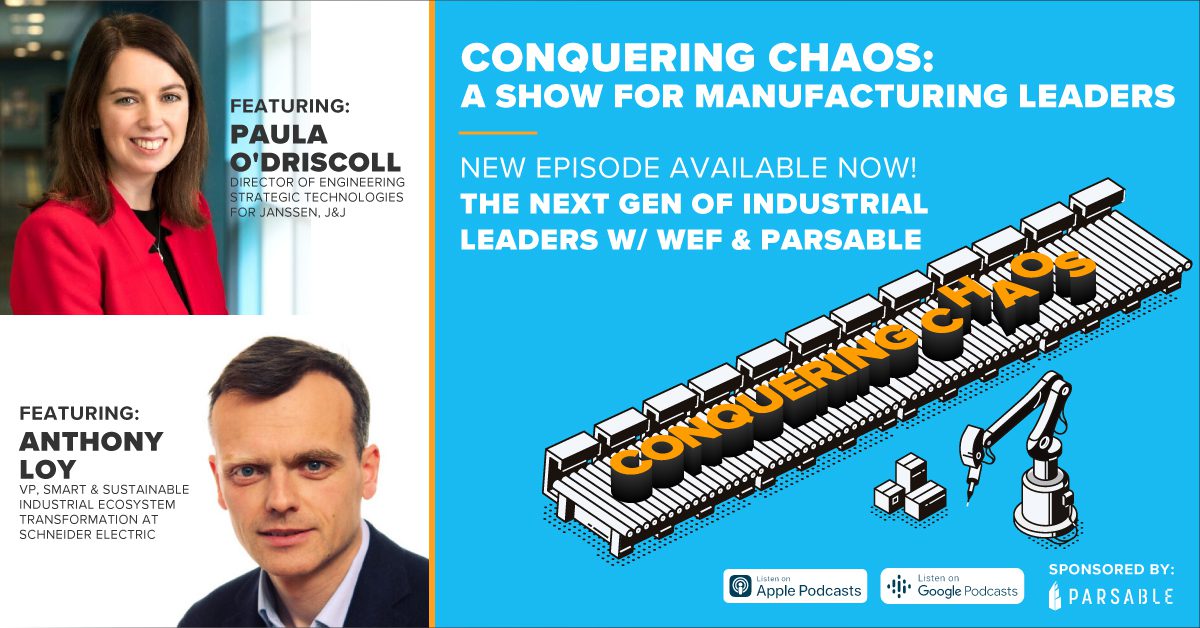
In our latest episode of “Conquering Chaos: A Show for Manufacturing Leaders,” Parsable’s connected work expert and podcast host, Josh Santo, speaks with Paula O’Driscoll, Director of Engineering Strategic Technologies for The Janssen Pharmaceutical Companies of Johnson & Johnson, and Anthony Loy, Smart and Sustainable Industrial Transformation at Schneider Electric, about building the next generation of industrial leaders.
Listen to the full podcast episode here.
Manufacturing Skills Gap: The Future Workforce
The skills gap is a prevalent topic in manufacturing along with the need to recruit and retain the next generation of workers, which includes: millennials, Gen Z and eventually Gen Alpha. Something in the industry needs to change, as current recruitment efforts are no longer effective. It’s not just about how companies recruit for new talent, but also the type of work experience they can provide their workers. People spend a big chunk of their day at work, and how they spend that time matters – especially to the younger generation of workers, who are the future of the manufacturing workforce. One of the first steps a company should take is to examine the current working environment and identify gaps, particularly related to digital transformation in Industry 4.0.
Evaluating The Manufacturing Skills Gap to Deliver Opportunities Afforded by Industry 4.0
It’s critical to understand the plan for Industry 4.0 deployments across the business, O’Driscoll explains. This could include advanced analytics, smart assets, artificial intelligence and the types of technical process or customer deployments that are planned. This provides directional context to identify what skills are needed, when and for how long. Then a company can then assess which people, skills and capabilities are already available and where gaps might exist. Different technologies are going to drive the need for specific skill sets.
Loy adds that there are three areas that companies should focus on in terms of skills: core digital skills, design thinking with an attitude of innovation and finally, a transformative approach. Core digital skills include the capacity to develop software, design architectures, networks, solution design, etc. As a layer on top of that, design thinking refers to the capacity to understand user needs, core needs, pain points, etc. Lastly, having a transformational approach means thinking about where you want to go and taking incremental steps to implement the transformation.
The manufacturing skills gap is only one piece of the equation when it comes to delivering on Industry 4.0. Companies need to have the right vision and the right people in place to be able to explore these opportunities in depth and encourage the curiosity that comes with the drive and attitude for innovation.
Addressing The Manufacturing Skills Gap
Loy mentions at Schneider Electric they started with a comprehensive self-assessment and a survey of its different populations. This included several thousand people, all in different functions in varying geographies to provide the right mapping in terms of where they were under-skilled. They then went on to create specific learning paths that were tailored for different job positions and these learning paths are still evolving today.
For Johnson & Johnson, O’Driscoll says that it can depend on different factors. She explains how closing the manufacturing skills gap can be built by your borrower or a contract decision, depending on the type of skill that’s needed, the urgency or the duration. It may be a talent acquisition play, where it’s to hire into the organization. In many cases, current employees will have the opportunity to upskill and reskill. She highlights how building skills right across the digital space, such as advanced process control and data analytics, is a major focus for Johnson & Johnson right now.
There is no right or wrong approach to addressing the gap. Companies should evaluate what they are able to do and make the decision that is best for their business.
Business Results From Upskilling and Reskilling Workforce
At Johnson & Johnson, O’Driscoll says people apply what they have learned across all targeted innovation areas and across multiple projects. While she mentions there is no direct causation to learning, one can correlate that upskilling or reskilling plays a major role in the on-time delivery of new technology or processes.
Loy explains how at Schneider Electric, they started a transformation program with 10 sites that created the first framework for their smart factories. They were able to duplicate from one site to another. Now they are deployed at 100 sites and have a core digital model that is accepted by workers because they invested in training and understanding the process.
Adapting Recruitment to Bridge the Manufacturing Skills Gap
Johnson & Johnson has made a major investment in talent acquisition for data and analytics to help with the need for Industry 4.0. The company is also upskilling current talent and growing partnerships with educational institutions to make sure the course curriculum meets their needs and accurately reflects the industry.
Loy echoed the same thoughts explaining how Schneider Electric is self-promoting the supply chain internally to attract people from other divisions. In their recruitment, they also put an emphasis on digital technology to show that manufacturing is not outdated as some believe it to be.
Building a Culture of Continuous Learning
At Johnson & Johnson, O’Driscoll explains building a culture of continuous learning is done in a few different ways. Leadership sets the example that learning is for everyone. They create learning journeys that help individuals see their path and how their learning is connected to business needs and delivering results.
“What did you learn today?” is the motto at Schneider Electric, Loy reveals. He goes on to say that every day employees should learn something. Decentralizing learning is crucial as well as making it available to everyone.
Sustainably Embedding Upskilling Within a Business
Sustainability is incredibly important. O’Driscoll highlights how the Johnson & Johnson team continuously scans its business to detect current and unmet needs. They keep learning connected to the business strategy and technology roadmaps. Johnson & Johnson also connects the self-reflection and self-assessment of skills required with the skills of its team members, to understand what skills are needed to do the work at hand. Having good internal processes and external partners will push the team beyond today’s knowledge and into the expertise that’s needed for the future.
Loy mentions how Schneider Electric has regular touch points between managers and employees to make sure they’re addressing any skills gap that might exist. They also have a “stem of reference” that shows what they expect from everyone in terms of skills and it is updated on a regular basis. If you’re interested in learning more, listen to the full podcast episode.