The Connected Worker Movement: Digital Isolation of the Frontline Manufacturing Worker
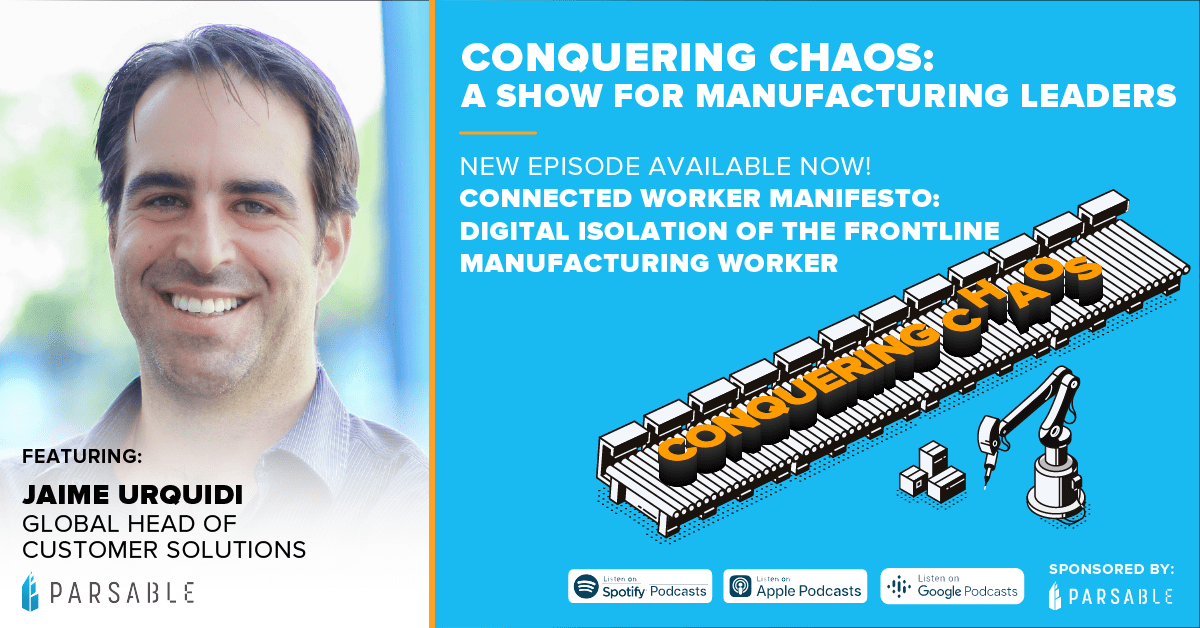
What if the tools you relied on every single day to get the job done were the reason you are experiencing inefficiency? How are you supposed to continuously improve when your options for implementing and sustaining change are limited?
In part two of our three-part series on the connected worker and workforce in manufacturing, we’re joined again by fan-favorite Jaime Urquidi, Global Head of Customer Solutions at Parsable
In this part, Jaime and Josh discuss the challenges ofsiloed solutions in the manufacturing industry. Jaime sheds light on the detrimental effects of relying on common siloed solutions, including the impact it can have on worker reliability and how it causes manufacturers to miss out on opportunities to improve. !
We also dive deeper into digital isolation, how it has affected manufacturing production, and why workers have been left behind in this process.
Join as the two discuss:
- A recap of the top takeaways of part 1
- How siloed solutions and lack of technology lead to digital isolation on the frontlines
- Digital isolation’s impact on manufacturing production and how workers got left behind
Catch the full article from the BBC on digital isolation here!
___________________________________________________________________________________
Experiencing disruption on the frontline? We can help. Request a demo today.

___________________________________________________________________________________
Check out the episode transcript below:
Josh: This is part two of our three-part series on Connected Worker. You’re going to hear me say this multiple times throughout the episode, but if you have not yet listened to part one, do so now. We cover in-depth details that we referenced throughout this episode. To ensure you’re getting the most out of this content, take a listen to part one. Now, in this episode, we examine the different types of siloed solutions we typically see in use on the front lines with manufacturers that we work with. Jaime does a great job of providing examples from his past to emphasize the topics that we cover and I do my best to keep up by sharing a few of my experiences working with manufacturers to improve workflows and processes. We also introduced digital isolation and discussed what it is and why it’s impacting frontline operations.
Back once again is Jaime Urquidi. Jaime, thanks so much for joining us once again for this part two of the three-part mini-series that we started on Connected Worker.
Jaime: Hi, Josh. It’s very exciting to be here again. It’s just another chance to continue talk about these things. Just thanks again for hosting me in the program.
Josh: Always excited to have you. You are clearly very popular. [chuckles] I’m a little jealous by how much engagement the episodes get whenever Jaime is on it. That includes both from listening to the episode, as well as people interacting on LinkedIn. If you don’t do it, make sure to follow us on LinkedIn, interact with us, let us know whether or not you like what we share, you don’t like it, if you’re a fan of Jaime, if you’re not a fan of Jaime. I am actively looking for some Jaime haters just to make myself feel better. I’m just kidding.
Jaime’s, great. He doesn’t have any haters.
This is, like I mentioned, part two of a three-part mini-series. If you didn’t catch our last episode in which we covered part one, stop right here and go and listen to it because we cover in detail the four most common inefficiencies that we consistently see across frontline workflows and processes. We’re going to recap those now, but I’m telling you, we go way more in-depth in part one. Make sure to listen to that if you haven’t already. To recap those inefficiencies, Jamie, why don’t you start us off? What’s the first one that you remember?
Jaime: Thanks, Josh. The slow-to-react topic is the first one that we talked about and the first symptom that we see is that you take a lot of time to identify issues and follow up on them. It’s very hard to just keep that cadence of continue addressing the issues that come today in that dynamic work environment that we have in manufacturing. Also, the other thing is that you just have to wait to get that information so you can react to it. Breakdowns and delays in workflows are also something that just gets embedded into the way of working. Also, very low ability or no ability to track trends on how things are moving. You need to act fast when you see some variables starting to move out of control and it’s very hard to do it if you don’t have a digital environment to really capture that data.
Josh: You’re absolutely right. With slow-to-react we’re really talking about can the right people get the information that’s needed so that they can take action because the longer you wait, the more likely there is to be some impact. The next one that we covered in the last episode is low to no compliance to process. Really what we’re talking about, if we break that down, it’s this idea of pencil whipping, as well as incomplete tasks. It’s deviations from standard procedure and it’s an inability to easily prove compliance. Really it’s these questions of is what’s supposed to be getting done, actually getting done the way it’s supposed to get done, and can you prove all of the above? That’s what we’re talking about with low to no compliance to process.
Jaime: That is very important because there’s like a black box. It’s a leap of faith between what you say that should be done in standard operating procedure and what actually happens on the floor. There are many reasons for that. The important thing is that with current technology, you cannot capture, you cannot see that. Now with new technology, you’re able to see that. The other one that we also talked about, Josh, were skills and expertise gaps. The expertise is always lying within the manufacturing floor.
Today with current technologies, it’s very hard to really capture and make sure that you have a democratized way of doing things. Just sharing that information and making sure that everybody has the same level of understanding on how things should be done and then new ways of doing things can be spread across the organization is very complex with current technologies. Just having people, having a vehicle to extract the people’s know-how to put it in the hands of more people is just a huge impact in the current operation.
Josh: Yes, because without doing some of those things you said you’re relying on tribal knowledge to get those things done. The problem with tribal knowledge, like we talked about in the last episode, is that it’s hard to scale, it’s hard to onboard off of that. It’s hard to make sure that people are doing the latest and greatest based off the improvements or the changes that come to procedures so huge inefficiency that causes complications within operations. Finally, we frequently see a lack of access to frontline data. In fact, whenever the data is captured, it’s typically captured on a piece of paper. Jaime, what happens to data captured on paper?
Jaime: Every time that you put a data point in paper, it dies.
Josh: It dies.
Jaime: Then you need to invest a lot of time and effort to bring it back to life and consuming.
Josh: To resurrect it. That’s right. The data dies on paper. On top of that, there are data points that are extremely invaluable for understanding opportunities to innovate or optimize processes that you’re just not able to capture with the tools that are currently available in most environments. Without that, it really impacts the ability to derive insights that lead to some sort of action and do that consistently across multiple sites, let alone a single site. That was a recap. Again, if you did not catch part one of this three-part series, go to the previous episode and check it out.
These inefficiencies are symptoms of a deeper issue. They are not the root cause. To get to the root cause we have to ask ourselves why are these inefficiencies happening? Why is it difficult to react quickly? Why can’t we eliminate pencil whipping? Why does onboarding take a lengthy amount of time or why is it difficult to locate and access data?
Jaime: Josh, just real quick to that point I remember when I was working with WCM, World Class Manufacturing, we used to have Professor Yamashina, which is one of my most valued teachers within the digital methodologies. He always said that in order to start scratching the surface of the root cause you need to have between four and seven levels of detail to really start digging in to what you’re doing. It’s about how you get better data and how you get more granular to really understand the phenomena that you’re trying to understand and then so you can put good actions that really attack that root cause.
Josh: Digging in deep to make sure the problem can be clearly defined so that any solution that you implement is more likely to succeed because it’s targeting the right problem at that point. I think that’s such a great call out. One of the things that we frequently see is that frontline operations don’t have the tools that they need to adapt quickly. This is not just frontline workers. I mean it does include the workers, but it also includes the managers and even the executives.
Each group is essentially relying on what we call siloed solutions that are ultimately isolating people from information that they need when they need it. We’re going to talk in this episode about the most common tools that we see that are leading to those inefficiencies that we discuss and spend much time really digging into. Jaime, look, you’re the one with the manufacturing experience. Talk to us about some of the common tools that you see that are driving some of the siloed isolated experience.
Jaime: Josh, we see a lot of paper. There has been a lot of effort to digitize the shop floor and start solving with more modern tools but we still rely a lot on paper. The paper-based solutions, we’ve been talking about that. Paper, I always say that paper is a great solution. It has solved for mankind since it was invented right by the Egyptians and now we still use so it’s been a great solution.
Today technology has given us more power. What we have to do today is to start eliminating that paper that really can help us look at the problem, see it in a different way, and then start tackling it differently. I remember when I was a process engineer, and as you were saying, that it’s not only for the frontline workers, but it’s for everybody, I was a process engineer in one part of my career and I used to do a lot of studies. I would gather a lot of information from the operators from the process so I could really dig into those levels of detail, so I can understand a problem that I was trying to solve to go and do it.
What I would do is I would just do a design of experiments and then create a couple of templates in an office software and then give it to the operators or just capture some data on my own and then give it to the operators so we could aggregate enough data so I could run those statistical models. The first thing that I had to do is I had to spend a couple of hours trying to just pass everything that I had captured in paper back into an Excel spreadsheet or to a statistic model at Minitab or whatever, and then start moving that data, that also created a lot of inefficiencies. I had to invest a lot of time in just capturing the data and putting it together instead of having the data readily available and then use that time and that effort to really dig in on understanding what’s a phenomenon and really interpret it.
Josh: There’s a lot of great points in what you brought up. You really emphasized in that story that idea that you brought up earlier, that data dies on paper and you have to go through so much work in order to resurrect it. Typically, if we really want to take this metaphor a little bit further, not only does it die on paper, it’s often buried in filing cabinets and that’s where you have to go essentially grave robbing in order to do that resurrection, but it’s true. I can’t tell you how many of Parsable customers that we’ve worked with that have rooms dedicated to filing cabinets or even sites or parts of their warehouse dedicated to the storing of this documentation just encased.
Jaime: Oh, there are businesses that run based on that, a lot of filing. Paper is still going to be needed and it’s still going to be used and it’s super good. It’s not a war on paper but we need to use it on the smartest way possible and that’s the whole point of this.
Josh: Well, yes, it’s really recognizing that it’s the fact that there is a better way, which we’ll get to in part three. It’s also recognizing that there’s trade-offs with the tools that you use. Relying on paper-based processes, it does come with these inefficiencies that we were talking about earlier. The term that you taught me with [chuckles] your background and introduced me to that idea of non-value added activities, everything that you scribed from going and hunting for that information, that data that you were looking for and putting it together in order to analyze it, that’s all non-value added activity that’s required right now. It’s necessary so that you can get to the insight and take the action but let’s make no mistake, it’s something that we can explore getting rid of to operate in a bit leaner manner. What’s another tool that comes to your mind?
Jaime: We talked a little bit about it in the opening, tribal knowledge. I cannot count the days or the examples that I have on this one. I remember just running a machine or just being in one of my shifts, I was a line supervisor or a line manager, and then the machine breaks down. We had a very efficient robot arm that used to help us to package some racks in a plant that I used to work at, but the worst thing that we could have is that the robot would break down and that it would lose its zero because only Johnny was the only one that could know it.
I remember a lot of times where we’re looking at a breakdown and then you hear in the background, a voice of somebody saying, “Oh, I wish Johnny was here. He knows how to reprogram the robot,” or, “He knows how to zero it,” and he was like, “All right, so let’s–” We started scrambling everybody and then just trying to find out if somebody had his phone, if we could wake him up at 3:00 AM in the morning, if he could come to the plant, or he could guide us by the phone to really get that robot or that equipment back up and running.
Tribal knowledge is super important and it’s something that we build through the years and through experience and really getting to know that granular in the maintenance, in the operation teams, and all that. Right now it’s very hard to bring that tribal knowledge into a brother, a crowd so that we together can lose or eliminate those dependencies on the Johnnys and Peters and experts in the world.
Josh: Yes, the information that’s needed is stuck in the minds of specific people and that’s the problem with tribal knowledge. I think you raised an interesting point that I’m going to call out explicitly, which is that tribal knowledge is something that is unavoidable. We’re people, as we build up experience and expertise we’re going to retain that and we’re going to stick to it and we’re going to get in our own habits and start to work that way.
That’s not necessarily a bad thing but what you called out is, it’s the fact that that can’t be easily shared, particularly with new individuals, which is a huge problem right now considering the workforce, the changing workforce, the retiring workforce and the need to quickly get not just new people in the door but get them operating at the same level as some of these veterans because, at the end of the day, many of these best practices live in the minds of these organizational veterans.
New workers are more likely to suffer as a result and they will rely on tribal knowledge, the tribal knowledge particularly of the people that they are shadowing or being mentored by or working with that day, which starts to introduce variations depending on who taught you how to do what, who does what process which way. Tt the end of the day these examples of tribal knowledge, there’s really no way to measure the impact of these internalized best practices and so that’s where some of the inefficiency sets in. You see variation in how people are completing tasks. You called this out earlier, Jaime, you see discrepancies in what is expected to get done and then the way in which it actually gets done, which, look, it could be more efficient to do it that way but it could also be risky. It could also open you up to some compliance concerns-
Jaime: Or safety complaints.
Josh: -or safety complaints. Absolutely.
Jaime: Safety problems, yes.
Josh: That’s such a fun example of Johnny that you provided because how often do you hear that? There’s really this hero culture that develops where you rely on one, two, three people to get something done in a very dramatic way. I know one of the customers that we worked with, I think I mentioned this on the show before, for their line startup process, I don’t remember the individual’s name, but if he was on shift, it was going to take 15 minutes to get that line up and running. If he wasn’t there, it was going to take an hour. There’s no reason why other people shouldn’t be able to do what he did and that’s similar to the point that you were raising with Johnny. You don’t want to rely on just one person and inconvenience them at 3:00 AM to come and fix things. I’m sure they’re happy to do so, don’t get me wrong, but, yes, let the guy sleep
Jaime: Then you can really elevate Johnny’s knowledge, because then he or she, they can transcend within the organization because they were able to not only know how to do it, but also make the whole organization go to the next level. We talked a little bit on the last episode about learning organizations, so that is a topic that we need to just bring those examples up, and, as you said, “Not have that many heroes, but have a lot of people that help us grow as that learning organization.”
Josh: Yes, everyone’s the hero in this case. You don’t have to have your own Justice League or Avengers team to get things done.
Jaime: They always come in handy and we still need them because then you have Thanos and then you have those attacks but, [laughs] really, it’s very important that we don’t rely that much to them, and then we can just make sure that we run steady. Another point that you brought up on the comment is that these things or these phenomena or these symptoms don’t happen in isolation. A lot of times they come all together, so it’s a mix between tribal knowledge and then non-connected legacy systems and all these things coming together that just evolve and just manifest in a way that create issues. It’s not that either you have one or two or three or four, it’s that all of them coming together in different shapes and forms, that’s when you create chaos. That’s what we’re trying to conquer.
Josh: Absolutely. That’s a fair point. We are examining what we typically see as some of the drivers of these inefficiencies. There’s definitely going to be more, and you’re going to experience different shades of them. Some might barely impact you and some might really impact you. I think there’s a fair point of it could be all, it could be one, it could be multiple working together, complicating one and another. That gets back to your point of making sure that you are digging in and understanding what the actual problem is so that whatever fix you implement is likely to stick. Now, you mentioned one that we haven’t covered yet, which was legacy systems. Talk to us about legacy systems.
Jaime: I think that every system and every process that you put in your organization has a specific purpose. It comes to my mind a couple of examples. For instance, in one occasion we had a PLC that the mother board just got burned. We had to get a new mother board. We installed it, but we didn’t have the CD to upload the recipes back into that PLC. We had to scramble around and sometimes even fly people from outside of the country to help us put that back in.
Those legacy systems they’re important and they’re basic. In order to have control, just make sure that everything is in place, in control, and we have the right impact but I think that we need to find a happy medium and a way to really play with the flexibility that current technology provides and that autonomy that we give to the different levels of the organization and different teams in a plant, but also have that control that you rely on the deep expertise so we don’t create an unwanted error. Those things, the better that you can help your organization have an ecosystem that embraces legacy together with new systems that they can work together to create more value, that’s where the magic starts to happen.
Josh: In that, I want to double down on one of the points that you’ve raised, which was there is magic that can happen between– You have to have these systems in place. Your ERP, your CMMS, your MES, if you have one implemented, and others as well, you need those for effectively managing your operations. Really, the difficulty that you are describing there, Jaime, is the fact that those systems traditionally, don’t do a great job of sharing information between their own system and other critical systems. I think that’s a great example that you provided, but it’s also a bit of a terrible example to be held hostage by the fact that you’re not able to access the data that you needed when you need it because it wasn’t something that you were allowed to access, essentially.
Jaime: Yes, it was just not available. It has to be kept somewhere that is safe and then probably was kept so safe that nobody found it.
[laughter]
Josh: Very safe indeed. Another thing with these legacy systems, I think, that’s important to call out, is on the data side. A lot of data that is used in analysis within manufacturing, yes, there’s data that’s coming from the machines, you’ve got SCADA, you’ve got data from your legacy systems. One of the things that we typically see is that there are data points that are needed to understand some of the variables that would help explain operational results.
Legacy systems like an ERP or CMMS, they don’t usually generate this type of activity data, rather they focus more on result data, meaning, this thing started at this time, it’s ended at this time, and these things got done by this person on this asset, which is absolutely information that you need. What it doesn’t highlight is what are the differences between that particular instance of completion and another particular instance of completion. Are they exactly the same? If not, why not? Because the goal is to standardize, to bring order, and without the right data points, that’s just not something that’s going to be available. That’s another element of legacy systems that we typically see.
Jaime: Yes, and Josh, again, it’s not an absolute no or yes. All these legacy systems are moving in the right direction. They’re opening up, they’re starting to change, and all that. The trick comes on how can you use the right technology at the right time so you can really unlock the power of that data. One of the things that you have available to really accelerate and really just punch those small buttons that really open that flow of value that that you’re looking for.
Josh: Yes, you definitely see a lot of modernization of these solutions. There’s a big push to move to the cloud as opposed to on-prem is, which goes a long way with sharing information, making that information more accessible in the ways that we talked about. What’s another tool that comes to mind for you?
Jaime: I was thinking a little bit about this, but another one is that sometimes we’re trying to just tighten in a bolt with a screwdriver. We’re using Office designed for back office software in order to solve for shop floor problems. A typical example is Excel. We use Excel for everything, and it’s a super powerful tool. Everybody loves it and everybody has a very deep understanding. I’ve seen people with no technical and programming in software background create some macros and some databases that are incredibly powerful and super good.
Now, the thing here is that a lot of times as they are designed for backups and they have a specific purpose and we’re using them for something else, it doesn’t mean that you cannot get the job done, but it’s just not the best tool to solve it. As these new technologies come in, and are specifically designed for that, then you can have a replacement of that wrong tool or that have solution for those things to really have something that is really specific for that you’re trying to solve.
A lot of times with Excel, I’m going to go back to that, or Word, you create amazing procedures, but still, you have to print them, or those forms, you have to print them again and then just putting the same pain that you were trying to solve at the beginning. You still have to capture the data on paper, then it dies, and you need to revive it and then put it back so you can consume it and then get to the full round. Those kind of things are also another shape or form of symptoms that end up providing or developing or just creating those problems that we’ve been talking about during these two shows.
Josh: Yes, back office software, there’s a lot of power enabled by those tools. Excel is such a great example because we see that in use all the time. Excel, being a spreadsheet tool, something that’s really looking at data and creating pivot tables so that you can analyze the data, building charts, et cetera, really about how can someone effectively interact with the data. We see it getting used for a lot of different things. One of the examples that comes to my mind is the common approach to tracking clean, inspect, lubricate activities. Using Excel spreadsheet to provide the standard work instruction, “Here’s what needs to get done. Here’s an image to help you understand how to do it. Here’s some callouts. Note this information, record this information here, and sign off here.”
One of the problems is the interaction with that Excel document then becomes, “Let me print it out so I can take it with me and go and do what I’m supposed to do and note that I’m doing what I’m supposed to do.” Then we just use paper. That data is dying and then it’s on someone to resuscitate it back into the Excel file. This is to your point that you made earlier where it’s just further compounding and complicating some of those processes.
On another side, I remember working with a customer of ours, on their behavior-based safety observations. They had a centralized program in which they wanted to make sure that all the sites under their purview were completing– I think each individual was required to complete one BVSO per quarter. It was a very low number like that. They were struggling to make that happen while they were struggling to prove that it was happening because the workers would fill out the information on paper, and then they would turn it in to the local safety manager who would then take all of those things, I think it was on a weekly, maybe even a monthly interval, and enter it all into a spreadsheet, and then send that spreadsheet to corporate.
One of the problems they had there was just the standardization of the reporting format, at that point, but you could see all of the breakdowns and all of these time-intensive and resource-intensive activities that went in to trying to get the information they need in a format that they could use using tools that were not really optimized for that particular process.
Jaime: You know what, Josh? Then at the end, the regional safety manager, director, or VP, ended up, Josh, they know of what happened, but then they could not do anything after that because it was too late. Then, what if you had a way to really get that data available on a more timely manner so that you can act instead of being so reactive?
Josh: Exactly. That’s why we started with an exploration of the common inefficiencies because that’s exactly what you’re describing is. This is an inefficient process and it is impacting your results. You mentioned in one of the previous episodes, particularly with safety, you can’t have that be lagging. You have to be on top of that. If it takes you a month to find out about a trending issue or behavior, what kind of risk do you have in that time in which that behavior is consistently occurring?
I think it’s such a great example of the slow-to-react side of things. I appreciate you taking us through that, Jaime, those different tools. Really, we can’t emphasize enough that these tools are failing to facilitate the sharing of information at the speed it’s needed. That’s the key here. If you put enough effort and resources and time into it, you can get the information that’s needed in the format that it’s needed and get it to where it needs to go but that is a very time-consuming, inefficient process. This is what makes these solutions siloed. This is why we call them siloed solutions. The information that is needed is siloed, it takes extra effort to get through those silos just to get information that’s needed, like I said, when it was needed in the format that it’s needed.
That’s a problem. It’s a problem because the name of the game right now is resiliency. Resiliency is really just about adapting quickly and sustaining those adaptations. To overcome inefficiency, to be a productive organization, to achieve resiliency, in this time of disruption, you have to get away from siloed approaches to operations.
Jaime: Definitely, Josh. It’s a super important point. The better that you can get to get that continuous flow of information and of data, then you will be able to really act faster and be ahead of the curve so that you can avoid those problems, those inefficiencies, those issues, those safety incidents, and those quality problems, or those losses in your production.
Josh: Now, one thing that you brought up a couple of times, Jaime, was this idea of new and emerging technologies that are, ultimately, opening us up to having these types of conversations. I would add to that, and say, further complicating these inefficiencies that we described, the status quo that we talked about, is the continued digitalization of these different systems and machines within manufacturing. It’s not that that’s, in itself, is a problem, it’s that as these critical pieces of infrastructure continue to be brought online and connected to one another, people are getting left behind. That’s really what we’re highlighting, that idea of you have to prioritize the frontline, their workflows, their processes, their experience in order to keep up with all of the other changes that are occurring.
Actually, this phenomenon that we described is referred to as digital isolation. It’s not just found in the manufacturing industry. Dr. Bibi Reisdorf, who is an assistant professor in communication studies at the University of North Carolina at Charlotte defines digital isolation as when people find themselves in a position where they can’t access the internet or digital media and devices as much as other people.
Now, why does that matter? Why do I bring it up? Well, what’s in an article published by the BBC titled Digital Isolation: The vulnerable people left behind, it examines the impacts that the lack of access to technology such as a mobile phone, or even an email address, technology that most of us now take for granted in our everyday lives, it examines the impact that lack of access to technology has on particular groups of people. In particular, this article examines the impact on people living in poverty. It actually prevents them from applying for jobs or signing up for available public services that are there to help them in particular, so they are getting left behind.
I highlight that because we see this in our day-to-day lives. We may not live this experience ourselves but what I mean by that is outside the world of work in people’s lives, there is this phenomenon of digital isolation. I call this out because this experience, this risk of being left behind is 100% prevalent within the manufacturing industry. This isolated experience is common on the frontlines of manufacturing, as well as other industries. I’m not trying to just pick on manufacturing, it’s what we talked about here, but it’s definitely something that we’ve seen in our work with oil and gas extraction companies, for example. You even see it with other services, other governmental services, as well. It’s all over the place but for the purposes of this conversation, we’re focusing on manufacturing.
It’s preventing people from accessing and sharing information that’s needed, when it’s needed. Something that, Jaime, I know, you and I have talked about a lot, is just that idea of being able to access the information that’s needed or automatically share the information that’s being generated or captured in a format that can be received.
Jaime: Yes, and it’s bringing technology that is available now to all of the different parts of the society. It’s just breaking those paradigms or breaking those preconceptions that technology cannot be used in certain environments. Now, we’ve proven that everybody in society can really leverage technology, and make sure that we go to the next level.
Josh: Yes, the point of that article is how tech has proliferated our lives in such a way that we rely on it in ways that we take for granted, and people, who are not able to access that digital world that we now rely on, are at a disadvantage. That is the same thing that we see as these systems, as these machines become increasingly digital-first and connected in nature, it’s not providing the people with a way of interacting with it. In fact, and I won’t go too much into this, but part of the difficulties is not even being able to use the right type of technology on the factory floor.
For example, when we talk about some of the options for frontline worker technologies in part three, we’re going to explore the power of mobile devices, and how that gives people a window into the digital world. This isolated experience, it is something that is, ultimately, driving those inefficiencies that we talked about earlier that’s getting to the root cause of it. The other element that I want to highlight is that you have to consider the disruption that is currently impacting manufacturers in this day and age.
Those who are able to overcome digital isolation on the frontlines, they will find a competitive advantage over others in their industry from producing goods at a lower cost to lower turnover, to having a higher likelihood of appealing to certain types of workers, who are looking for a more modern digital-first environment in which they work. These types of impacts will be undeniable and we’re already seeing it in the work that we do with other manufacturers.
Jaime: Definitely, Josh. I think the companies that really go after that transformation in any shape or form, they’re going to build a competitive advantage because the ones that move faster and really embed that into the way they think, the way they operate, the way they solve problems, I think they’re going to be better off than the ones that just take more time to go at it.
Josh: You called out the way they think. I think that’s a point that I should have emphasized earlier. This is not necessarily a problem of tools. It’s a problem of strategy and philosophy. Is your approach one that requires these siloed solutions or are you finding ways of making sure that people are able to get the information they need right when they need it in a way that they can consume it or can these systems get that same information?
I’m really excited with part three because in our next session, we will be exploring what solutions are available to help you overcome digital isolation across your frontline operations. Like always, Jaime, I really appreciate you stopping by the Conquering Chaos studios to talk with us about the different tools that are leading to this digitally isolating experience on frontline operations.
Jaime: Thank you very much, Josh. As always, it’s a pleasure to talk to you. I’ll see you on the next episode.
Josh: All right, [laughs] sounds good. Look at that. This is probably the shortest episode that we’ve ever recorded together.
Jaime: Yes, I guess we were able to pass the message in 40 minutes. That’s amazing. [laughs]
Josh: Yes, it is amazing because Jaime and I are talkers, and you’d know that if you listen to the previous episode. Once again, if you haven’t listened to part one make sure you do, and stay tuned for part three, which is coming up soon. Jaime, thanks again.
Jaime: Thank you very much, Josh.
Josh: Digital isolation, it’s an interesting phenomenon and a byproduct of our increasingly digital lives. With digital transformation Industry 4.0, it’s something that we are seeing in our work with manufacturers, people, the most valuable asset to manufacturers are getting left behind. In part three, we’re going to cover the different types of frontline worker technologies that are available to you to help you combat it and give people the tools they need to thrive in the factory of the future.
Take a listen to the only podcast miniseries dedicated to the who, what, where, when, and why of the connected frontline worker!