The Connected Worker Movement: Inherent Inefficiencies in Frontline Operations
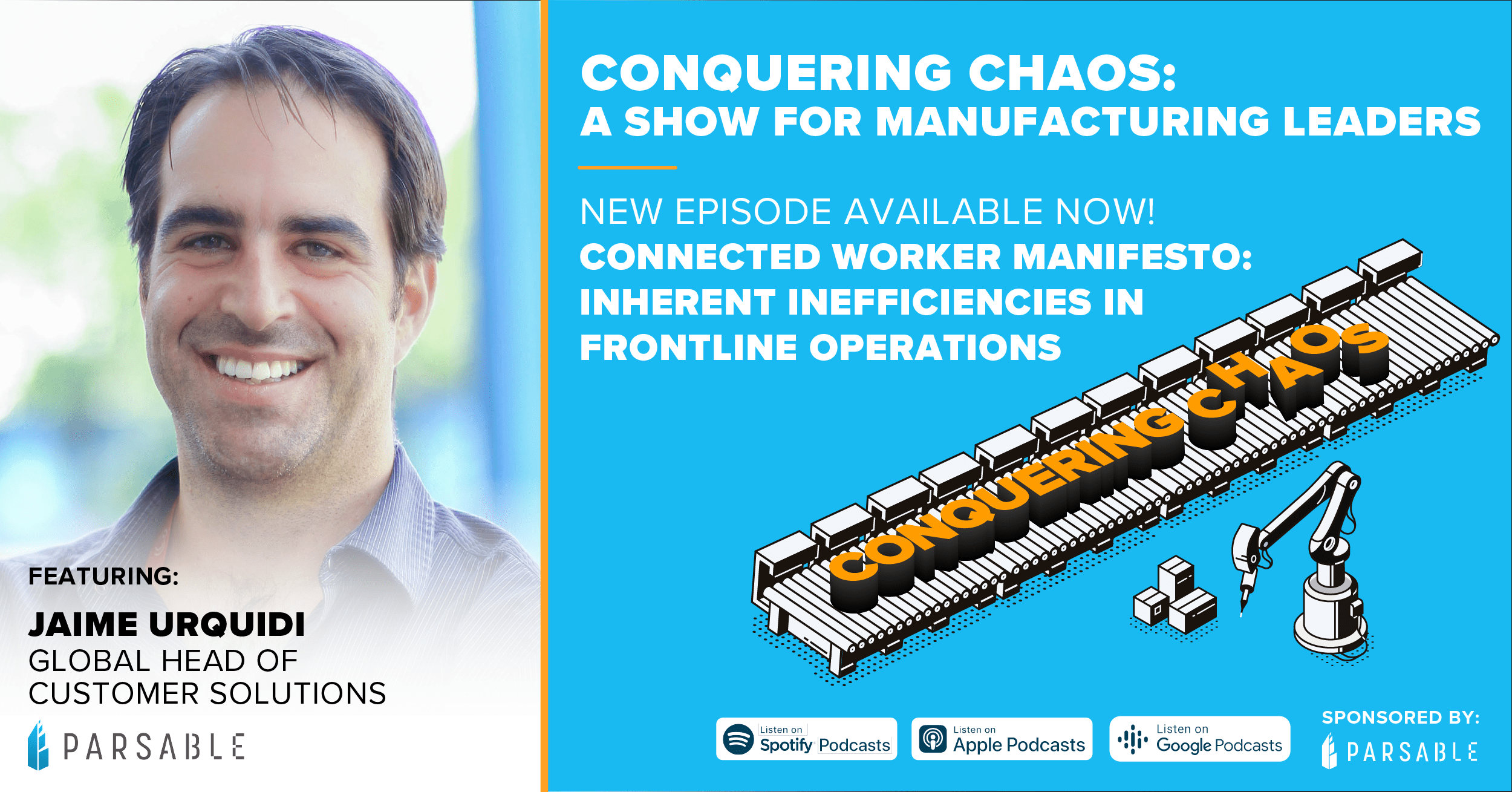
Join us on Conquering Chaos as we kick off a three-part series on the connected worker and workforce in manufacturing with our industry expert (back by popular demand) Jaime Urquidi, Global Head of Customer Solutions at Parsable.
In part 1, Jaime and Josh examine the most common inefficiencies that they’ve encountered while working with manufacturers to digitize frontline operations.. These inefficiencies are inherent within frontline workflows and processes and if left unchecked, they can significantly impact operational results.
Join as the two discuss the:
- 4 most common inefficiencies and what to do about them
- Cost of doing nothing
- Role of today’s frontline worker in solving inefficiencies
___________________________________________________________________________________
Experiencing disruption on the frontline? We can help. Request a demo today.

___________________________________________________________________________________
Check out the episode transcript below:
Josh Santo: Coming up on Conquering Chaos.
Jaime Urquidi: It’s very important that we are always questioning ourselves as manufacturing teams and as management teams. Are we creating a system that people need to work for the system, or the system works for the people to get the job done?
Josh: This episode is the first of a three-part mini-series in which Jaime and I will be examining in-depth connected worker and the connected workforce for manufacturers. In part one, Jaime and I talk about the most common inefficiencies that we see affecting manufacturers that we’ve worked with around the world. Now, there’s layers to these inefficiencies, so we get very specific and we even discuss common use cases suffering from these inherent inefficiencies.
We examine the impact of these inefficiencies, and then we examine the impact that these inefficiencies are having on manufacturers today. Now, in part two, we’ll deep dive and ask why more than five times to get to the root cause of these inefficiencies. In part three, we’ll explore the processes and technologies real manufacturers are using to combat inefficiency on the front lines. After this episode, go to the gemba and see if you can identify any of the inefficiencies we cover on today’s episode, and let me know if you do. With that, welcome to part one of our three-part miniseries on Connected Worker.
Jaime. Thanks once again for joining us in being a part of the Conquering Chaos Show.
Jaime: Thank you, Josh. It’s a pleasure again, to have a chance to speak to you and all the people that listened to the show. The first episode was a lot of fun and I see there’s a lot of traction on it so looking forward to keep the series evolving.
Josh: Yes, people seem to really like what you have to say, which I can’t say that I’m surprised. I too am a fan of Jaime’s work. I’m actually pretty excited that we’ve been able to get you back on the show so quickly. This is the first part of a three-part series in which we’re focusing on this idea of connected worker.
For everyone listening, a lot of people have reached out over the course of the show so over the course of two years have ping me directly at josh@parsable.com and a couple of messages on LinkedIn as well, asking about this idea of connected worker, both from a product perspective as well as really a philosophy perspective since, Jaime, both you and I work for Parsable, which focuses on connecting workers within manufacturing operations.
I thought this could be a good opportunity to ride the coattails of your success so far, with the audience, and really dig into this idea of connected worker. To do that, really the focus of this conversation today is to highlight some of the background information that really sets up why this is such an important initiative, such an important movement within the manufacturing industry.
I think it’s important, Jaime, that we start with just providing some of our own background with how we are qualified to speak to this. Obviously, in the last episode, we talked about your 20-plus years in manufacturing, within all the lessons that you learned throughout your course of your career, from line manager all the way to factory director. You, obviously, have that expertise, but for the past, what, four or five years now you’ve been working here at Parsable, helping manufacturers implement connected worker technology across their front line in order to deal with some common problems that we’re going to talk about today?
Jaime: Yes, Josh, I think one of the most interesting things that my career has gone through in a way and just reflecting on the last four years, is that I’ve been able to bring all the things that I struggled with and that we talked about it a little bit on the previous episode, and how now with the new technologies available and what we’re doing here in Parsable and other things that we’ve seen in all the different customers that we work with, how we can really do a leapfrog change on how things are done leveraging the available technology here.
It’s not only, possibly of course, the central part of it, and that’s how we’ve been solving this together with our customers, but also, the other things that are available in the IoT world or in the ERPs or all in the information and data management, the capabilities that we have today for manufacturing. I think it’s just a very exciting time to see how all this world is just jumping very quickly to that futuristic world that we probably thought of in the ’90s and 2000s, so it’s very exciting.
Josh: It is. It’s always fun. Between the two of us, we’ve had to have visited and been onsite and helping implement this type of technology for hundreds of different manufacturers at this point. I’ve been all over the world which has been a lot of fun seeing the behind-the-scenes experiences of manufacturing, being able to tour factories and help the people that run these factories make the products that I grew up with. It’s super cool to be a part of this experience. It’s cool to see when you think about it, how frequently Parsable is used, across the world, its powering over a trillion dollars in production revenue at these major manufacturers of which the world relies on.
Through this connected worker approach and the problems that they’re solving and the gains and efficiencies that they are experiencing, they’re seeing some pretty impressive results. What comes to mind is OEE improvements. We’ve seen anywhere from 2%, 3% to 6%, which are massive improvements in OEE. We’ve also been able to work with customers who’ve experienced throughput increases, which is particularly important right now when people are struggling to meet production demand, being able to increase throughput in the case that I’m thinking of up to 12% is a pretty impactful change. What are some results that have stood out to you?
Jaime: I think that, just to echo on your first point, another thing that has been very interesting is that as we have visited sites all over the world, but in many different industries, that you could think that they don’t have anything to do with one with each other. We go from oil to construction and building materials to CPG to some aerospace customers that we’ve been exposed to and all that. The common problems that they’re trying to solve and how you can extract yourself and start looking at them from a different lens and then just see those common denominators that bring a lot of opportunity to impact their results.
The examples, for instance, in yield of materials utilized. We’ve had a customer that improves 2% on their yield of a specific process that gave them a lot of efficiency and better cost on their production floor rights which really impacted their bottom line. Those things are the things that really excite me on how we can come from the concept to using the technology, then seeing our customer use Parsable and then really change the way that they’re doing things so they can really impact the way that they’re performing.
Josh: You brought up such a good point. We work with manufacturers across different verticals of manufacturing. You mentioned CPG, we’ve worked with Health and Beauty, we’ve worked with Food and Beverage. In fact, some of our largest customers are in the food and beverage side, making the bread products that I know we all know and love, and some of the beer products as well.
I think you called out something that’s particularly important is we see and have these conversations in what some people might think of a totally different environment. Yes, it’s still manufacturing, but when you start to break up the different types of machinery, processes, challenges, et cetera, it does become significantly different. However, we started to see common themes pop up, conversations that weren’t really happening within a specific site. Let alone the entire company, let alone other companies that could all benefit from one another.
That really formed the background of the podcast is we wanted to promote these conversations with real people within the industry who are experiencing challenges or have a different perspective on a specific topic, so that as a whole we can grow together. Because really that’s what it’s all about, is how do we help not just move the industry forward, but how do we help really move humanity forward? That sounds so cheesy when I think of it but that’s really what we’re focused on and it’s exciting to see. Like you said, this is an exciting time to do it, for a couple of reasons.
Not only is there a lot of buzz around new technology and innovations that haven’t been around before, but look, it’s no secret that the industry is in experiencing significant disruption. There’s a lot of different disruptors to that some of the most common ones that stand out for the manufacturers that we have conversations with the workforce, retiring workers, the high amount of turnover. Retiring workforce is really top of mind for a lot of the manufacturers that we speak with as far as what is putting their production at risk and kind on a flipside of that and I separate these out for a reason. The lack of skilled labor/the lack of applicants to fill these roles that are being left open and vacant by veterans of the industry.
Jaime: Yes, and Josh, that point is super important, I mean, we see that probably manufacturing is not the first choice to all the people that are coming into the labor market. I think that leveraging on newer technology, cooler more technically and digitally enabled in work environments is something that is going to be very important, so we can attract that new generation of workers that will come and really make things happen. There’s always a debate.
When you work in a services industry and I can tell that from my experience and right now, I provide services and I used to manufacture things. The role of manufacturing is very important to keep our lifestyle moving. The type of work that manufacturing demands is a very relevant piece of our society. We need to make sure that we bring that digital world into that specific part of the workplace so that we can just make it more appealing and have more people wanting to make a difference in that world.
Josh: To your point, it’s this idea that there are multiple levers that can be pulled in order to address these types of situations, technology, certainly being one of them. We’ve done a good amount of research on this, the two research pieces that I can think of, we interviewed over 1400 frontline manufacturing workers across different types of manufacturing to get their perspectives on the industry, what they’re struggling with. What’s top of mind for them? What are the factors that keep them? What are the factors that make another opportunity more appealing?
We did the same focusing specifically on recent graduates in Generation Z to understand what are their perspectives on manufacturing. What we found was that there were a lot of different factors and thus, a lot of different levers that manufacturers could play with in order to make sure that they are competitive not just between other manufacturers but other industries as well that appeal to Gen Z and Millennials as well. Millennials are already well into their career I’ve stopped calling out Millennials because it’s really easy to focus on Gen Z, I know I’m one of them.
It doesn’t stop there. There’s also supply chain challenges. COVID really exacerbated, and essentially, was the straw that broke the camel’s back. There were all of these difficulties and opportunities for improvement existing beforehand but that was the final straw that broke everything, it shut everything down and we’re still recovering from it. That has led to conversations around how do we reshore, how do we nearshore which then ties back to some of the complications we just talked about of like, “Okay, well, if we’re going to reshore, how do we get people who are going to do it? Who going to help us get to it?”
It is compounding effects of this problem and then you lay on shifts in consumer demand, which has always been a thing. Demand is always shifting, that’s nothing new but it’s still this batch size one where products are becoming much more personalized, almost feeling custom to a specific consumer but you have to do that with the same equipment. Same materials that you’ve already had. Same processes. Same workforce that you’ve already had. How do you deliver what customers want when it’s becoming very niche as far as the product goes?
Then there’s the social side, the morality component, the environmental social governance side of things. How do you make sure that you’re producing products in a way that align with or reflect the values of your end consumers? Because that’s becoming a very important factor when considering what products should I give my business to. A very informed concerned consumer.
Jaime: Definitely, I mean, that impact not only on the environmental part but the whole impact of the audit stakeholders that are around, how you serve your market is becoming more and more important and being able to really address not only the environmental part, as we were saying but also the social part, that diversity and inclusion part of it, the equal opportunity, then on the governance and compliance and traceability on fair trade and all those things. The better that companies start tackling those new ways of working which are only pushing for a better society are the ones that are going to just maintain their competitive advantage. It’s something that is very important for this time.
Josh: There’s those two sides, you have to deliver not just what the customer wants but you have to see around those corners, where’s the trend going? What’s going to be the next big thing? Then there’s also on the flip side, you got to make sure that you’re able to make it which then takes us back to the workforce thing. Then you’re complicating all of that, you mentioned competitive advantages, what is the technology that’s going to ultimately help us really compensate for some of the problems that we might be experiencing? Whether that’s labor issues, whether that is complicated production plans because you have to deliver such custom products.
Technology is going to ultimately be the enabler of overcoming some of these gaps in order to deliver the right product to the customer right at the time that they show up at the store and go to the shelf and reach for the product. How do you make sure that that is there and it’s the exact thing that they want? Technology is going to be the great enabler, Digital Transformation, Industry 4.0. These are certainly buzzwords that we hear all the time and I’m sure you’ve gotten some eyes rolled at you whenever you’ve mentioned it but it really is a great description of the impact technology is having on the industry.
There’s a significant amount of disruption really coming to a head. I think if we take a step back and we look at these different points that you and I just went through, I think there’s a very prominent theme across all of those. What do you think?
Jaime: I think what is there and I think it’s there to stay is that people are central part of that.
Josh: Which people?
Jaime: The frontline workers, the frontline operators, and the people that actually put the product in the bag, that are actually making that happen. As they interact with all the requirements and governance needs. Talking back to how things are done that is becoming much and more important. Also, with the systems and all the complexity that’s coming from all this technology coming together like new machines, exoskeletons, these robots that you can teach someone how to do things and how people need to adapt to these new capabilities and then start using different skills.
Also, all the information that today we’re exposed to, how that is changing from 20, 30, 40 years ago, when you were a frontline worker and you were working on closing a box and putting tape on it. How that is really changing that landscape is just super interesting and how the role that frontline workers are taking into that, I really think that it’s not going to go away.
Josh: I’m in the same boat, I know that there is talk about what does the factory of the future look like? Is it a lights-out type of environment? I think one, it’s really going to depend on what is the product that you make and how do you make it. Even then people are still going to be responsible for the upkeep and the maintenance of the equipment that is running “lights out.” There would still have to be lights and they wouldn’t actually be lights out. It’ll be a very long time before robotics is able to successfully take over the role of people.
There’s that famous quote from Elon Musk, who is certainly making headlines all the time but this was a year, two years, maybe even three years ago where he tweeted out about “Tesla excessive automation was a mistake. Humans are underrated.” That is absolutely true. These disruptors that we talked about, that’s disruption that’s occurring on the front line. What we’re concerned about from a retiring and revolving workforce or a lack of skilled labor, that’s people on the front line, the supply chain challenges. Those struggles came from the difficulties that the workers on the frontline experienced and encountered.
Shifts in consumer demand are complicating how you manage the equipment, manage the production, it requires people and resources to really figure that out and handle it. When you think about this idea of factory of the future and this is something that Dr. Stefan Kozielski joined us to talk about, you have to focus on the frontline and by focusing on the frontline, we’re talking about their experience, we’re talking about workflows, we’re talking about rethinking processes that leverage technology to eliminate some non-value-added activities that are required all the time in order to successfully run a factory.
There’s so much non-value-added activity that has to happen these days. It’s a wonder to me sometimes that it’s not taken into consideration from a lean standpoint because there’s other non-value-added activities that are a little more obvious and that’s what we’re going to talk about. We’re going to talk about some of these non-value-added activities.
Jaime: Yes. You know what, Josh, the other very important thing of that role of the frontline workers is that, so creativity has always been sourced from the human experience. People actually doing the job are the ones that come up with ideas to solve those problems and then evolve. It’s almost, I would argue, impossible to lose that by experience you come up with the right solutions because the solutions don’t come necessarily from an outside entity that generates that change. It comes from actually leaving the problem and then getting help from other players in order to solve that problem. That cycle is very interesting and it’s always going to be there from my view.
Josh: That was such a perfect call out because it ties a couple of things together. We just talked about– I brought up lean manufacturing and there’s camps of, is there seven waste? Is there eight waste with that eighth one being, are you leveraging the knowledge and experience, and talents of the people? When we think about one of the previous episodes that we had with Tom Shorma, he talked about one of the ways in which his company not just a part a particular site, but his entire company across multiple sites was able to increase throughput on average by 20% and it really all came down to listening to people’s ideas and implementing them. I think that’s such a great point in– Actually, let me ask you a question, Jaime. Are you in the camp of 7 wastes or 8 wastes?
Jaime: I think that lean is based on building a learning organization. All that knowledge is the key that will help you either solve the problem, understand the problem, and then solve it or develop technologies to find the solution for that problem. I’m in the camp of 8 because I think that knowledge and the way that you can generate an environment where people learn and the organization is a learning organization that is always coming up with new ways of doing things in a better and more productive way or more efficient way, then that’s where you start winning and that’s where lean manufacturing starts does start coming up.
I remember being in audits on WCM audits with Professor Yamashina, which is just like an authority in lean manufacturing. He would always come back to what is the learning, what is the organization learning? Are you really leveraging the know-how that you have and, and that you’re developing your organization? I think that really struck me and that really made me think of different ways of approaching things or approaching problems so that we could learn from it.
Josh: Yes, learn and continue progress because the second that you forget those learnings, you start repeating those mistakes and then you have to go through the process of learning it again. You’re not able to make and sustain progress. I think that’s such a great call out that idea of really focusing on learning and sharing that knowledge. Well, I want to address specifically– What are some of the inefficiencies that we see. We work with frontline operations all over the world.
We help them become more agile and adaptable through not just connected worker technology, but this philosophy of connected worker, connected workforce because it’s not just the frontline that sees a benefit from being connected, but to your point, you got to really define the problem, really define the problem and try to get to some of the root causes.
I want to cover that. I want to cover what are the problems that we typically see and what are some of the implications of that. At a high level, when we look at the ways in which connected worker is being consistently used in manufacturing sites around the world, I would argue that there are four very distinct categories of inefficiency that we see consistently.
I guarantee you if you’re listening to this and you go to the gemba and you just take a look around, you’ll start to see these exact things. I’m positive you will be able to relate to one or more of them as far as having experienced that firsthand.
Those four inefficiencies, the best way that I like to think about them is slow reaction times, an inability to react quickly. There’s low to no compliance to standard process. There’s skills and expertise gaps on the topic that you and I were just discussing. Then probably one of the most common ones is lack of access to data on frontline operations and frontline activity. I want to take some time and break each of those down. Let’s start first with the slow reaction times slow to react. I’m going to bring this up.
It’s that inability to respond quickly, but that’s the simplest way that I could put it. Now, this manifested a couple of different ways. This could be identifying issues and following up on those issues. Some of the examples I think about and this is a common one that I would see and it almost breaks my heart every single time. I can’t tell you, Jaime, how many times with some of the workers that I’ve worked with, some of the operators on the line that I’ve been able to have some really deep conversations with have mentioned this feeling of no one listens to me. I reported an issue and no one listens to me.
It just goes into a black hole and no one does anything about it. There’s a lot of complications that come from that. There’s not just the fact that you miss out on whatever that issue was and the complications, in that particular production run that day. There’s also that morale. That feeling of I’m not being heard, I’m not valued as an employee, why should I stay here? This issue identification and follow-up has a lot of complications to it. It really comes down to not being able to find out about issues. Some of that is not being able to effectively report issues and in general, respond to that. Can the right people find out about it and do something about it?
Jaime: Yes, definitely that’s something that the current, like the way that you can solve it is by either reporting it, like through the ranks, and then just everybody’s like super busy. The shopper, it’s so dynamic that it’s very hard to follow and it’s very hard to prioritize. Then on the other side, if you do it through paper, it’s also like another layer that you need to manage that with. It’s that dynamic or those technology restrictions in a way. They cause these things to get lost either in translation or in the process or in the big stack of all the things that we need to do in order to make these things. It extracts empowerment from the people that I can actually, if they get authorized, they can just go ahead and do it themselves.
Josh: Yes. I worked with a food manufacturer one time and we were specifically focusing on the relationship between the production line and the maintenance teams. Part of that was really trying to understand what was their current process for raising these issues and at their stations, they had a walkie-talkie, a radio. They would say to the radio, “Hey, this is me. Here’s where I’m located. I’m having this issue.” The person who was out on the floor representing the maintenance team at the time on that shift, they would receive that message and they would write it down on whatever sheet of paper they had handy, like, “Okay, I need to make sure to come back to this.”
Then put it in their pocket and go about whatever they were doing unless it was a super high-priority urgent item, but the problem with that is, that little piece of paper that he wrote it down, that got lost, so now this report just didn’t get captured at all. It can’t get followed up on. Actually, in that example, it led to frequent instances of downtime with their equipment. That was one of the reasons they were looking to explore what are the causes and what they can do about it. Now, identifying these issues and following up with them, that’s not the only way in which the manufacturers that we work with have found difficulties reacting quickly.
Sometimes it’s purely from a workflow standpoint, there’s just breakdowns and delays in workflows. Well, one example that I can think of, I worked with a food manufacturer of some of the best potato chips on the market. They were having a problem with their changeover. Well, I wouldn’t say they were having a problem. They noticed only after working with Parsable that, on average, they were seen about a 20 to 40-minute delay in the changeover that happened purely because the quality personnel who was responsible for performing a contaminants check to come and check the line to make sure that everything was good. I think they even did a swab test.
There was a delay in production notifying quality that it’s time to come and look at it. Then on the flip side, of quality notifying, “Hey, we did it. We’re good. You can proceed.” That alone was driving downtime. That was wait time from a lean manufacturing perspective that could be eliminated. It’s this inability to just share information and updates that cause these breakdowns and delays, ultimately wait time.
Jaime: Yes. That, Josh, it’s totally something that is super common. People are busy. People have a lot of things to do. It’s very hard to be working at capacity, or having some buffers to work on those things. You’re always running, especially in manufacturing and that dynamic place. Talking about that slow to react. I remember that in one of the companies that I worked for, we were performing hundreds and hundreds of safety behavior observations because we had a very strict program that everybody had to do one audit a day then cross audits between different departments and all that.
Then in my weekly meetings, I would ask for, “Hey, what are the things that happened last week?” We were generating that many behavior observation cards that the safety team was not able to keep up with putting all that together and categorize it so that we could review them on a weekly basis. They were always behind. I would review the information from two weeks or three weeks before.
I was like, “Hey, we cannot be proactive with that because the safety, I don’t want to describe it as it goes, but that safety risk is always moving depending on the decisions that are happening and the environmental conditions that are around it.” It’s very hard to effectively be able to change that trend if you cannot be ahead of the game or be faster to react.
When you have technologies available that can capture that information digitally, and then you can see, and you can actually, without the effort of the people of the safety department, to collect all the tags, then summarize them, put them on an Excel spreadsheet, and then drive the trends and look for the top three that happened in the last week. What if that information is captured and is readily available? Every shift you can have a conversation on what happened last shift, and then to specific reactions to change that trend or to address those situational environments or conditions that can provoke a risk.
Josh: What you’re really highlighting behind this idea of slow to react, it’s really coming down to are people able to access the information they need, get the information they need to react in a time effective way. To your point, you don’t want a month to go by for you to realize, oh, we’ve got these top three safety concerns from a behavioral perspective that we need to correct because within that month who knows what could have happened?
This is something you want to be as close to real-time and ideally proactive about. I think that’s such a great example that really brings in the fact that, like you called out, there really is with these delays in getting information, this is all– Then once you get that information going through it and trying to figure out what to do with that information, again, this is all non-value added activity that takes a significant amount of time that can be augmented with the right technology.
Now another one that we commonly see as far as inefficiency goes is low to no compliance to process. I feel like this might be a little bit of a controversial one because I’m going to talk about pencil whipping. I can’t tell you how many times when I sit down with some of the functional managers production managers in particular when we’re talking about autonomous maintenance there’s a concern that these tasks that are supposed to be getting done aren’t actually getting done.
However, if you check the paper trail it shows that everything was done on time when it was supposed to be every single time. I know that this is something that you’ve experienced in your career in manufacturing as well as just these the complications that come from these incomplete tasks.
Jaime: You know what Josh, just to be fair a lot of times us as organizations and as management teams, we generate a lot of that unconsciously because we put on a lot of requirements that from one point of view, they might be very important to do a check, but we really don’t– Everything just lands on the hands of the person that is executing that task.
If I’m a frontline worker that I need to run a machine, do quality checks, do safety checks, then do some maintenance reporting and then do some CIOs and all that. It’s not often that organizations go and look at, hey, is that we’re asking to the frontline worker feasible to be done in the eight hours that they have. Then, unconsciously, organizations as they put control boundaries and they put control systems and processes.
Which are very important. I’m not saying the other thing, they need to happen, but we need to think what is the best way to do it so that they are effective and we don’t create unwanted behavior unconsciously. I think that everybody goes to work, or I would argue that 99.9999% of the people that go to work go there to do a good job and do the best they can.
Now, a lot of times, and I don’t know if you’ve ever been exposed to, but hey, I need to do all these things and then I just don’t have time. It’s not feasible. The other thing that is important in that sense, and I was just talking about, it just struck my head, is that people decide to pencil with things that they don’t see nobody caring about. It’s not that they don’t care about that check.
It’s that I know that I put this in a sheet of paper and then that paper goes to a binder that binder goes into a box and that box goes to a warehouse and nobody looks at it unless there’s a recall. I need to get my job done. I need to get these things done. I need to get the line running. I need to fix and tweak all the dials. This thing is just going to have to wait, and then I’m just going to pencil with it.
It’s a natural prioritization and just doing the most important things that they think that they can be doing. Now in hindsight, on the other side, from the control perspective, the quality of the data that you’re basing your decisions on it’s not there. You have a system that is trying to make decisions based on information, but the reliability of that information is not great. How can we close that gap so that we have the right information at the right time in the right place for the right people to make the decisions that they’re supposed to be taking?
Josh: That’s such a fair call out. It’s easy to assume that it’s negligence and that it’s intentional, malicious, I don’t care about this job, whatever. That’s not the case at all. Oftentimes there is a gap between the expectation of how and what is supposed to get done and then what actually does because based off my experience these are the things that are most important.
These are the priorities. To your point, this thing never gets looked at. It never gets checked. It’s really not that high priority. I have to make these decisions very quickly. I’m slammed. People are quitting, there’s less of us working. That means I have to pick up the pace. It becomes a very complicated thing. Now, that doesn’t change that, that conversation needs to be forced because ultimately everything must add value provides some value, and people have to understand the why it’s important of that piece.
Jaime: Yes. Just to close that one out, but it’s very important that we are always questioning ourselves as manufacturing teams and as management teams. Are we creating a system that people need to work for the system, or the system works for the people to get the job done? I think that’s a very fair question to ask whatever you’re doing, because the important thing is that you have a system that enables people to get the job done right, with safety, with quality, and with productivity.
Josh: Yes. Now we’re talking about load to no compliance in the process we just talked about pencil whipping which is really around this idea of is what’s supposed to be getting done, actually getting done, but there’s another flavor of low compliance, and that comes from this idea of deviating from standard procedure. So, the thing got done, the activity was completed, but was it completed the way it’s supposed to get done? Was it done safely? Not just efficiently, but did everyone follow the appropriate safety behaviors that are coached on and established within that operation?
I just read an article about a very prominent bottler in Guam that OSHA is coming down hard on because people weren’t following safety protocols. Instead, they were prioritizing just quick reach in, and fix this little blocker until someone got injured and it was pretty bad, so there is an importance around not just if it’s getting done, but if it’s getting done the way that it’s supposed to get done.
Jaime: Yes. I described this or the way that I’ve thought about this is that, what you have in your procedure, is your best approach and the best to your knowledge, and you put your procedure in paper, in the instructions. Then there’s a leap of faith on people actually doing that way. Then when a new person comes into the front line, they get teamed up with somebody and then they pass that tribal knowledge. The process or the instruction is done by somebody that is not necessarily the people that are executing.
Then when the people go in and start executing, then they learn, they learn from somebody that it’s going to depend on if Joe, Peter, or John showed you how to do it, because one of them does step A123, the other one does 321, and the other one was 132. At the end, they all performed the whole process, but then the effect on the outcome of that might be very dependent on that sequence of events.
Josh: There’s such a big focus on standardization, and that means that people have to be doing things the same way so that you can reduce variability so in that example that you provided if you have these things happening in different ways, you’re most likely going to see inconsistent results depending on who’s the one operating and that’s not something that’s going to be ultimately efficient in the long run. Now, another flavor of this, so it’s not just is what’s supposed to get done actually getting done, it’s not just is it getting done the way it’s supposed to get done. The other part of that is can you prove that it got done. This idea of proving compliance.
There have been some manufacturers that we work with where there’s no instance of pencil whipping. People are doing what they’re supposed to do. They are very experienced in on the same page. They’ve got a very healthy bidirectional culture in which feedback is coming down and going up, and so they’re doing it the way that it’s expected to be done, but the problem is just in accessing the records to demonstrate that it was done the way it’s supposed to get done when it was supposed to get done so this is inability to prove compliance is another one.
Jaime: Yes. That’s just traceability in a nutshell. You have all these procedures because that way, by ensuring that it was done that way, the theory is that you’ll have like perfect safety, no waste, better quality, more productivity and all that. The thing is that it’s very hard to see if you actually did it, so technology today can give us that in a much better way. I mean just with a device and these technologies can give you a time stamp and offering stamp.
Then you can start building on how things were done without having somebody to do extra work to make sure that it happened at that moment, in that time, at that sequence.
Josh: Well, you brought up quality I know some of the conversations we have frequently about this surround quality. Do you have any thoughts on the impact of either not proving compliance or pencil whipping has for quality checks, for example?
Jaime: Yes, again, I’m going to just go back to the point of the quality of the data that you’re making decisions on. There are a lot of times where not only quality, let’s talk about quality you’re doing your quality checks, and everything is in compliance, everything is green, but still the market is identifying some– and you still have complaints, so there’s something that happened in between that you were not able to capture that defect that ended up being in the hands of the consumer and your quality system was broken.
Same thing with maintenance. You do your autonomous maintenance, and you do your everyday checks, and you make sure that everything is clean, inspected, and lubricated, so you can avoid breakdowns. You have a great record of CILs, but then you still have a large number of breakdowns, or your equipment keeps breaking. The day-to-day small things that you need to do or that you’re supposed to be doing, if you ensure or you can have a way to making sure that they’re happening, then it’ll help you in the wrong runs for them not to become bigger problems.
Josh: Absolutely. Adding to that idea is it getting done how it’s supposed to get done? That leads us to the flip side, which is our next inefficiency that we see. This idea of skills and expertise gaps, you called it out perfectly, which is when you’re not really sure if things are getting done the way they’re supposed to get done, and that turns into tribal knowledge, this is the way that we do things. Don’t worry about what this document says that hasn’t been updated in years at this point. I’ve been doing this, I know how to do it.
That really starts to drive even further gaps, and it makes it hard to scale that type of knowledge, so one of the other inefficiencies when we talk about skills and expertise gaps, it’s that over-reliance on tribal knowledge and tribal knowledge may or may not reflect the actual way, preferred way of something getting done. That over-reliance on tribal knowledge, it really drives some inconsistency in the way tasks are performed. Some of the best practices live within the minds of the people that have been doing it but if they’re not on the shift that becomes a problem. I know one customer that we worked with in particular, they were struggling with their line startups.
There was a specific individual, I cannot remember his name off the top of my head, but if he was on shift, it took 15 minutes to start the line. If he wasn’t there that day, it was going to take an hour. That’s a 45-minute difference in production, or we’re talking about a huge amount of units missed at that point.
Jaime: Yes, definitely, and that happens a lot and there’s always going to be experts and there’s always going to be people that know the process better because of experience, because of preparation, because of many different factors, but the way that we can generate, again, a learning organization and provide the systems and processes so that people can do their job in the best way that we know, then the better we’ll be. As you were talking, just two things came to my mind.
We were talking to a customer at another paving company, and the maintenance manager said, you know what, with this technology, the company can really capture the know-how of all the people that work here, and it’s not that we want to get rid of that. It’s that, they have other things to do and they have so much to provide to the organization that can be of benefit for everyone. That it was just, they saw possible as a great way to do that. The other part of it is that we’ve seen a lot of our customers that naturally are starting to use the capabilities that technology brings in order to help people do their job better.
In the middle of COVID in Germany, another customer, didn’t have people to do changeovers, so they would have to switch people around from line to line to prioritize which production line to be running. They were able to, through the use of the procedures and the technology that they had, some videos that they had embedded in the procedures impossible. They were able to actually execute a changeover from product A to product B. With people that had never done it.
Now, it didn’t take the standard time that it took because you need that skill. You need to build that and they’re people that are used to doing it, and somebody new was never going to do it at that level, but they were able to leverage that tribal knowledge that was captured in the system for them to be able to perform the changeover, which took three times more. At the end they were able to do it and reduce the downturn, be able to produce that new product that had to be done.
Josh: There’s really two things that I heard when you broke that down. First, back to the point that you made earlier about lean is about having a learning culture. That sharing of best practices, it’s so that people can build upon the progress that has been made. You don’t want people to have to make the same mistakes in order to come to the same conclusions and then make progress.
That idea of really making sure that people can learn from one another in a consistent and scalable way by sharing these best practices that are often locked up here is such an important part. Then furthermore and really to the next level of the inefficiency is this idea of, how can you onboard and upskill people quickly? To your point, you had people who had never performed this specific process on these lines from product A to product B, and they were able to do that safely and successfully.
Now, it didn’t go as fast as it usually does because there is always going to be a need to ramp somebody up and build that familiarity. The ability to do is the best learning experience, but to be able to shorten that time to understanding by providing in the moment educational material based on how the experts do it, the changeover got done. That’s a huge win. Now, another level of that, it’s not enough to just capture those updates, those processes, but it’s how do you consistently share it?
I had an example of– we were working with a particular manufacturer, this is again on the food manufacturing side. This individual that I was working with, he had just made some updates to the procedure, and he was going through trying to find each of the binders that he was going to put that in, because at this point in time, we were just observing what their current workflow was like. One of the maintenance guys in particular, pulled out the procedure and he had it folded up, had the piece of paper that he carried with them, but it was from three versions ago. It wasn’t up to date.
There’s this difficulty of making sure that the updated version is proliferated everywhere that it needs to be at that point. It’s not enough to capture and put this expertise in these points of knowledge into a digital format. It’s also, how do you distribute it and make sure that everyone gets it so that there’s no confusion in a more automatic way. That really helps us to overcome some of these skills and expertise gaps that we’ve seen.
Now, the final inefficiency that we most frequently see is this inability to access data on frontline work. We talked a little bit about it when we were talking about slow to react, because ultimately it does lead to delays in reacting quickly. You’ve got a very popular saying, you say it all the time. I think it’s absolutely true about this inability to access data and the impact that it has on the operation. What’s that saying?
Jaime: You’ve already heard me say 1000 and 1000 of times. It’s every time that you put a data point in a sheet of paper or in an analog system, that data point dies. Then you need to invest a lot of time, energy, and resources to bring it back to lives so that the people that have to consume it, are readily available to. We’ve been talking about this through the whole conversation. We’ve been touching about that.
It’s very important to realize that today, that paper has solved world history. It has taken us as humans to this level. Now, we have new technology that can really break those boundaries of paper, that sheet of paper to bring it and then enable us to have more data, better data on a more timely manner without all the effort that it requires today to bring it to the decision point.
Josh: That’s a fair call out. That paper itself is not a problem. It’s been one of the most effective tools for much of human history. It’s not that paper’s the problem, it’s the fact that the information on the paper stays on the paper, and the only way to transfer that is to transfer the paper and all the different hands that paper has to go through in order for someone to do something with that information that’s just ineffective. That leads to those delays that we were talking about before.
After the spiel that you gave me, the first time that you broke this down for me, and I was like, “Jaime, isn’t paper the problem?” You were like, “No, it’s because data dies on paper.” [chuckles] It was this idea that much products, data has a shelf life. The longer it takes for you to get to it, the more likely that data has expired, that data has died, so to speak. Because of that, you’re missing out on opportunities to either improve a process or optimize something or it ties back to some of these other problems inefficiencies that we talked about.
If that data’s dying on that piece of paper and that data reflects an issue that needs to be corrected, a trend that is occurring that you need to address, that’s going to have a further impact and it’s going to compound on those inefficiencies that we’ve covered already.
Jaime: Definitely. You know what Josh? You mentioned it, but I just want to stress it. It’s not that you have one of the issues isolated. They always come all together, and they have a big interaction. These are for problems that we see. You can stress the phenomena in different shapes and forms, but you have many of them coming together in what you’re seeing there. It’s just also important to just realize how they’re becoming, how they’re manifesting in a way, and then how you are approaching this. You can have an impact in all these different aspects of the whole problem that you’re trying to solve.
Josh: That’s why we’re spending so much time talking about these different problems and inefficiencies that we see so that people can start to recognize these specific ones, put a name to it so that they can dig into focus. Like, this is how, or this is what we need to solve and it’s causing this problem. Now another one that we see, and this one is a limitation of paper as well, is the type of data that you’re able to capture is ultimately limited.
We mentioned earlier about how technology is ultimately going to unlock the competitive advantage. It’s not just connected worker, it’s things like digital twin, artificial intelligence and machine learning, prescriptive algorithms, et cetera. There’s a lot that comes together. The thing that is frequently missing from a paper perspective is the specific type of data that you need to capture, that’s going to help you understand some of the nuances of the different points that we talked about earlier like, how is work actually getting done?
Paper doesn’t really reflect that. Whereas a digital tool can then capture the data that then says, at this time, this person did this thing. By the way, the contextual data, the metadata of this data point is that this person was working on this line for this product at this site. It really starts to set the foundation for being able to draw insights that you couldn’t get before. That’s something that we also see is there’s just a lack of the ability to generate and capture this type of data, which is ultimately going to unlock process optimization, innovation and other opportunities like that.
Jaime: We have a client from Germany, which he always says. You have paper, then a picture says the paper has words. A picture says more than 1000 words. A video tells more than 10,000 words. These types of technologies enable us as manufacturers to have all this additional information and additional context so that we can really understand in a better way the phenomena. I always talk about the granularity of the data that you can really capture today compared to what you were able to do before.
Then that is going back to the learning organization. It can help you to solve the problems in a much better way because you have more granular data that is more relevant to the phenomena so you can understand it, find the root cause, and then with that root cause, act on it, change the process, improve it, control it, and then maintain. All that continues improvement cycle that we’re talking about, lean and all that, with this data capability behind it becomes superpowered to help us do a better job.
Josh: That’s such a good way of thinking about it. These data points that can’t be captured today, that can only be generated with the right tool really help to highlight some of the variables that are impacting operational results. To your point, to really get to the root cause, you have to understand what are all the different variables that are coming together, leading to this particular result so that you can then effectively manage and do something about it, implement a change, and then sustain that change. At a high level, those are the four inefficiencies that we consistently see when we examine frontline workflows and processes. There’s just a recap slow reaction time so the inability to find out the information that you need to find out do something with that, the inability to react quickly.
Loaded note compliance to standard process, which is asking the questions is what’s supposed to get done actually getting done? Is it getting done the way it’s supposed to get done and can we prove that it got done the way that it was supposed to get done? There’s skills and expertise gaps and that really complicates the situation with tribal knowledge and lengthy onboarding times which are a struggle. Again, back to some of these disruptors that we talked about.
How do you reshore? How do you nearshore it? How do you bring in new people and get them up to speed quickly so that it doesn’t take them 20 to 30 years to build that expertise? Then finally, an inability to access frontline activity data or frontline operational data that really helps manufacturers understand what are these different variables that are impacting my results. Can I skip all of the manual work required in gathering data, entering it into a spreadsheet, turning that into a pivot table, reviewing it, because again, that all complicates some of the other inefficiencies that we had before.
That inability to access frontline data quickly, easily, and the specific types of data points all drive inefficiencies that we see within frontline workflows and processes. Now, these inefficiencies, they’re not just a pain. They’re not just an inconvenience, they’re costly to manufacturers. I think we’ve mentioned a couple of them, but one of the ones Jaime, I remember you calling out was the downtime. If the CIL isn’t getting done consistently when it’s supposed to get done, that’s going to lead to unplanned stops, that’s going to lead to unplanned downtime.
According to Senseye, the average downtime cost is $532,000 per hour. Obviously, that changes depending on what you’re manufacturing, the volume, et cetera but we’re talking about big numbers and sometimes it’s 20 minutes of downtime. Sometimes 10 minutes of downtime, but regardless, even 10 minutes of that is what? Oh, I can’t do math that quickly. That would be $53,000 at least. I hope that’s correct.
Feel free to email me if not, but what I’m emphasizing is that these problems are costing organizations today.
Another one that comes to mind is, I read this on MODIS, which is correcting poor quality is often 100 times the initial price of the part being corrected. If it takes, I don’t know, $1 to create the part $10. I’m sorry, $100 to replace the part. I told you math is not my forte, that’s why I do a lot of talking but what are some other costs that you’ve seen?
Jaime: I just want to emphasize a couple of things here. That cost of rework. I’ve had customers talking about, “Hey, we don’t have any waste, because we rework everything, and then all the pieces even when they’re defective, we just sell them. We’re able to sell them,” but I mean, you’re missing on a very important part that is at least you’re putting double overhead into that part. You’re affecting your customer directly, but those are hidden losses that can arise if you really look at the problem in the right way.
As I said, at the beginning, I mean, the yield or the yield of ingredients and materials is something that can really heavily be impacted by doing the right things at the right time with the right settings, with the center lining and all those things. That you have the efficiency or the overfill on production lines, or the underfilled, which creates a compliance problem and then you can be fine. All those kinds of things are really things that affect that.
Another point that I wanted to make Josh, is that we agreed that organizations spend a lot of time managing and working on the data so it can be consumed. They spend a lot of time, a lot of resources, a lot of energy and all that. Imagine that you could use all the expertise, all the know-how, and all the brainpower of those people that are managing that data to just focus on the analysis and the solutions instead of managing the information and putting it in a consumable form. Then you could really excel on how these people are using that know-how, that expertise, and that experience to really impact how things are being done in your organization.
Josh: That’s such a good point. It’s really this idea of cost. Your costs are being impacted by these inefficiencies and especially when we start thinking about inflation, because I didn’t mention that before. I kind of looped that into supply chain because when we get into some of the root causes and all that it all ties back to the supply chain issues but inflation, one of the best ways to combat those increasing costs is efficiency. How do you reduce your cost per unit?
How do you reduce your labor cost, without necessarily reducing headcount at that point? How do you make them more efficient? How do you allow them to do instead of like you said, all of these activities, non-value added activities of compiling information, turning it into a consumable format, and then analyzing it and taking action? How do you reduce some of that burden, some of that workload for it? I think this was a great example of hard costs. There are also soft costs as well and one of the ones that comes top of mind back to that example that we provided earlier of people don’t listen to me, I’m not heard, I’m not valued, that leads to turnover.
I know turnover itself is a hard cost. What I mean is, it gets harder and harder to draw the inefficiency as the root cause to it. Turnover is certainly a hard cost, but in this case, I’m talking about the feelings that come from it in that case.
Jaime: It definitely impacts engagement. Engagement has been studied forever and engagement has a direct correlation on productivity and output, and efficiency and employee. I think it’s something that we need to really consider on how, as we build these learning organizations, we can put the systems and processes in place so that people’s voices can be heard, so that they have more pride and more ownership, and they feel the importance of the role that they’re playing within all these complex supply chain. That needs to happen like it’s a Swiss watch, in order to make sure that we are supplying the market.
Josh: The keyword is heard. That doesn’t necessarily mean that you implement that idea because they might not be the idea that’s best for the organization. It might be something that’s like that is a good idea, but not right now because it’s not the priority but that heard requires that response and that follow-up, “Hey, I heard you, I’m listening, I’m going to level with you. This is where our head’s at and why we’re going to do X, Y, or Z.”
Jaime: Let’s have the conversation.
Josh: Let’s have the conversation.
Jaime: That raises the conversation between all the different roles and layers within your team that can really drive productivity and engagement in your work environment.
Josh: That’s right. Well, I think this has been a great examination of the experience that we typically see and help manufacturers with regard to the inefficiencies that we have found working with these manufacturers across frontline workflows and processes. This is the first part of a three-part series in which we’re focusing on connected worker. We explored really the problems that need to be solved. What you’re going to see is they’re really the symptoms of the problems that need to be solved.
In our next session, we’re going to get down to the root cause, what is driving these inefficiencies, and then in the final section, we’ll talk about the different ways in which you can go about solving these particular problems. Jaime, as always, thanks so much for joining us today. I always love having conversations like this with you.
Jaime: Thank you very much, Josh, and looking forward to next episode, and I hope you find this conversation useful. Thank you very much.
Josh: I sure hope you enjoy conversations with Jaime as much as I do. I’m already looking forward to the next two parts of the miniseries. Now while these conversations might be fun, at least for me, the value is in the action that you take as a result. I encourage you to go to the Gemba, observe the workflows and processes conducted day in and day out at your factory and try to identify which of the inefficiencies we cover today are impacting your operation.
Let me know if you’d like any help doing just that. Now, if you like what you heard today, subscribe to Conquering Chaos in your podcast player of choice. Leave us a rating and a review to let us know that we’re on the right track in bringing you valuable insights from industry leaders. We’re active on LinkedIn. Check the show notes for a link to our company page and click the follow button to stay up to date with the latest from Conquering Chaos.
Also, just be sure to connect with me on LinkedIn or even send me an email josh@parsable.com. Let me know which episode you heard and what you think. Finally, if you have a moment, let us know which topics are top of mind for you via the survey found in the show notes. As always, thanks for listening.
Take a listen to the only podcast miniseries dedicated to the who, what, where, when, and why of the connected frontline worker!