Digital Twin to Win w/ Michael Pytel from Fulfilld
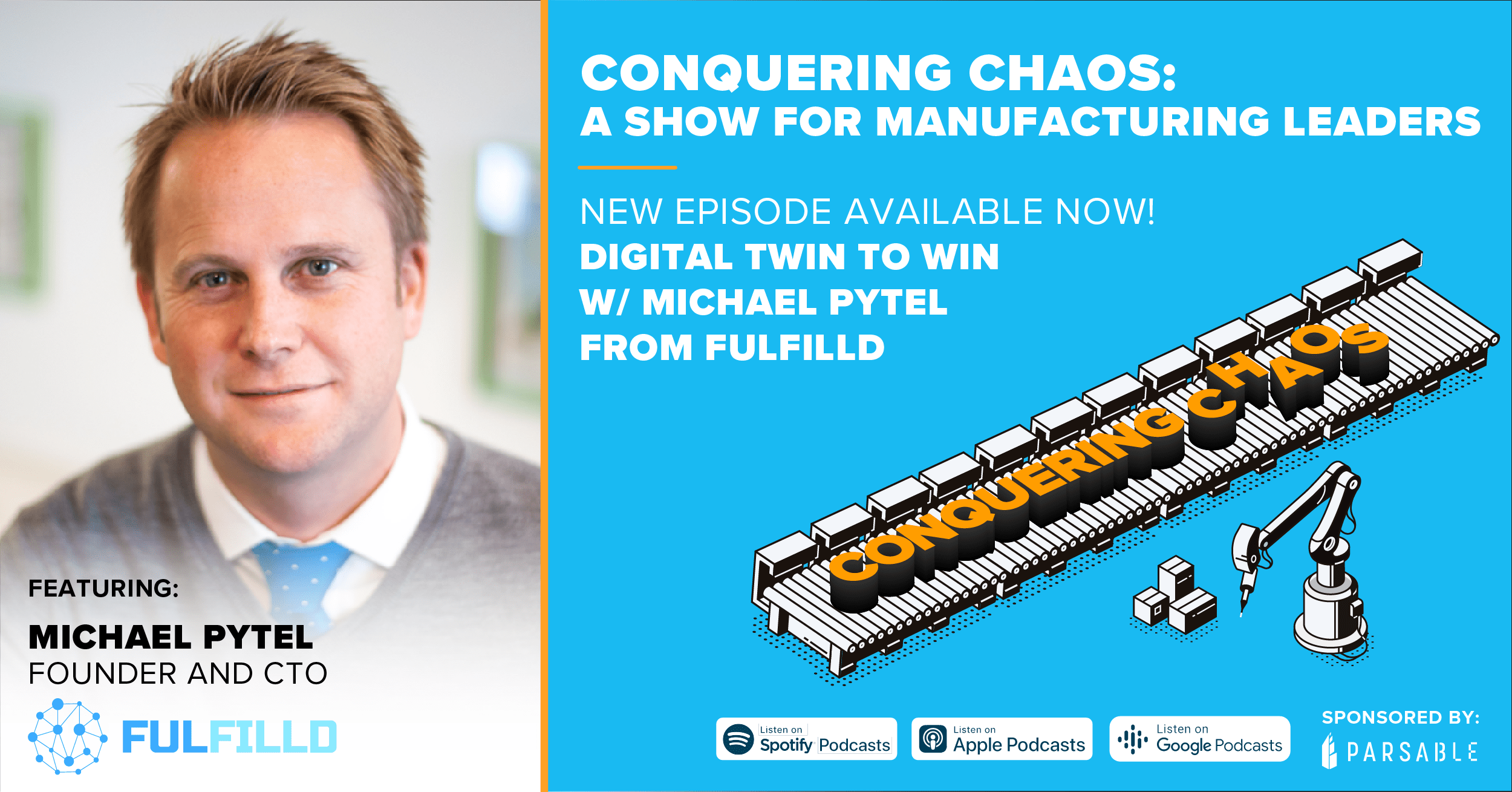
Digital Twin — hyped-up dud of an idea or critical component to the future of manufacturing (and the world)?
In this episode we’re examining fact and fiction when it comes to Digital Twin technology.
Our guest is Michael Pytel, Founder and CTO of Fulfilld. He discusses the implementation and reality of Digital Twins in the industry. Michael offers valuable insights on how digital twins have transformed the industry, and can transform logistic in particular, by providing real-time data and insights. He highlights the benefits of using digital twins, including increased efficiency, improved customer experience, and cost savings. He also shares the challenges that come with implementation and how to overcome them
Join as we discuss:
- Fact and fiction surrounding digital twin technology
- Benefits of using digital twin technology
- Overcoming implementation challenges.
- Key considerations for implementing digital twin technology
- How to start implementing digital twins
If you like what you heard, you can join Fulfilld and Michael at this year’s Promat Conference in March to continue the conversation!
And if you’re a fan of the show, please fill out this survey to help us improve it!
Conquering Chaos is hosted by Josh Santo, be sure to connect with him on LinkedIn!
P.S. Say “to win” fast and it sounds like”twin.” Is that a sign? Digital To Win, Digital Twin!
___________________________________________________________________________________
Experiencing disruption on the frontline? We can help. Request a demo today.

___________________________________________________________________________________
Check out the episode transcript below:
Josh: In this episode, I sit down with Michael Pytel, co-founder and Chief Technology Officer at Fulfilld, which offers the only intelligent warehouse management system with bundled hardware and software to seamlessly orchestrate warehouse operations and workflows. What I love most about this conversation with Michael is the grounded, realistic perspective. Michael shares about one of the most exciting emerging technologies in manufacturing, digital twins. Michael spent 15 plus years supporting large enterprise manufacturing in whole distribution organizations, developing quite the SAP expertise along the way.
It’s through his career he discovered his passion for building and deploying digital twin technologies within these organizations. In fact, he worked on creating a digital twin of the San Francisco 49ers Stadium. Isn’t that crazy? Michael walks us through the basics of digital twins, what they are, what can be accomplished, and then examines the hype versus reality of digital twins. Listen to this episode to learn all you need to know about the basics of digital twins, including how to get started on Conquering Chaos.
Michael, welcome to Conquering Chaos. Thanks so much for being here today.
Michael: Fantastic, Josh. Thank you so much. It’s been a long time we’ve been speaking and excited to be here on the pod.
Josh: That is so true. It’s been a couple of months in the making in this episode. Our schedules weren’t lining up. When they finally did, I’m in Texas, the ice storm hit, the power went out, and, of course, the internet went out, so I had to reschedule. Everyone listening, it’s been a long time in the making. You were pretty busy last week anyway. You were at a conference, right?
Michael: Yes. My company is a young company and we had some sort of a coming-out party last week at a conference called Manifest. It’s titled as The Future of Logistics Conference and it was the who’s who of logistics in warehousing. You had DHL there, you had Meredith, you had some unicorns, some startup unicorns like Flock Freight was there, ZBOX was there, Uber Freight was there, Rail Providers.
It was everything logistics, everything supply chain. Robots were there. Boston Dynamics were there with their creepy dog there that was demoing how it could reach in and grab things, things like that. Great conference, great time. Happy to be here on the pod and talk about warehouses.
Josh: I am really excited about today’s topic because in today’s episode, we’re exploring the digital world. I’m not talking about the metaverse for everyone listening, although I will argue till I’m blue in the face that virtual reality is crazy, cool, and fun. If you don’t believe me, try out Beat Saber on the Quest. It is a fantastic game. It’s meditative.
Aside from that, we’re not talking about the metaphors. We’re talking about actual physical assets that are recreated in the digital world, digital twins, what they are and aren’t, and what you can do with them, and how you can get started with this inevitably essential technology. Michael, my first question to you, what’s a digital twin?
Michael: I’m sure there’s plenty of people out there on the pod that have a BMW or a Mercedes or a Toyota. When you pull up your My BMW app or even your Tesla app for your Tesla, you see a digital twin of your car. Are the windows up? Are the windows down? What’s the mileage? What do my tires look like? Do I have any service coming up? That’s a digital twin of your car when I pull the My BMW app and it tells me all about my car.
What I’m trying to create or what we’ve created is a digital twin of the warehouse. How big is that warehouse? How many people are in it? How many forklifts are running? Where is everybody? Where is the product? Creating that digital representation of a physical space or a physical thing, that’s the digital twin. I think digital twin first started with when the Germans created the concept of Industry 4.0 and the need for digital twins of manufacturing equipment.
My company and me, we’ve been extending that philosophy to different thing so in a prior life I helped create the digital twin in the San Francisco 49ers Stadium. Levi Stadium is headed by an organization of 49ers that is very innovative in the way that they approach the fan experience. We created a digital twin in the stadium for them a couple years ago, co-sponsored by SAP at the time, and it was built in SAP technologies where operators in the stadium could see a fan capacity at different gates, fan capacity at concession stands.
Honestly, that was a very fun project and really started my love of digital twin, and probably was the seedling of my current company, Fulfilld, and us wanting to create that digital twin in the warehouse.
Josh: I like how you started it out with an example of something that we might experience in our everyday life. I think that that’s pretty powerful. I’ve had people on the show talk about artificial intelligence and machine learning, and one of the things they called out is you are using this in your day-to-day lives and you may not realize it. I really appreciate the example of the car and the app, the car being the physical asset, the app being your gateway into the digital representation of that asset.
Really cool that you worked on the digital twin of the 49ers Stadium. I’m sure we could spend a whole episode talking about that, about lessons learned, about obstacles that you had to overcome, about goals, and what people are able to accomplish now. In order to not derail us, I do want to get some clarification for you on the way that you described digital twin. You said it is a digital representation.
When I hear the word representation, I can take that a couple of different ways. I’m wondering if you could get really crystal clear with us on what exactly a digital representation is because a photo digitally represents something, but we’re talking about something deeper here.
Michael: I think sometimes somebody will say, “We create the digital twin and it’s displayed in a tabular application like a grid row. This is a representation of all your orders in the queue.” “Is it a listing of orders that are on the manufacturing floor in the warehouse?” “Yes.” “Is that a digital twin?” I would say no. A digital twin needs to be a visual representation of that environment, of that asset, of that thing. I need to be able to see it digitally, but I also need to be able to interact with it.
When you talk about digital twin of a sports stadium, it’s being able to visually or digitally see what is the flow rate of people coming in and how long are the lines. I visually see the stadium. I visually see the four gates and I visually see a q length there. If I had a power BI report or a Tableau report, they just said the q length is 80 and it’s like a red bar. That’s not a digital twin. That’s analytics. I think analytics and digital twin, two different things all have their use cases.
A digital twin really enables the user to make decisions. For our space, for the warehouse, I need to digitally see a top-down or 3D, what is the warehouse? Where are people? Where are products, and where are the exceptions? Where’s the congestion? Where’s the issue? What can I solve?
That, to me, is what a digital twin helps you better understand, is what are the areas of concern? What do I need to be thinking about when it comes to whatever I’m working on? In my case, it’s a warehouse and I’ve got 50 employees in the warehouse. How do I see the exceptions and how do I really contextualize it to know where is it in the warehouse?
Josh: I think the keyword that you called out is this idea of interact. While you can interact with dashboards, I think you’re talking about something deeper. There’s more of an exploratory of almost putting yourself in the area without actually being in the area using data to get an understanding of what it’s like to be there or how this asset is performing compared to where it’s supposed to be.
That idea of a bidirectional layer of communication where data is feeding the digital representation whatever interaction you’re doing, what are the data sources are coming in, and it’s feeding back to that asset. I think that’s an interesting thing. How much with digital twins would simulations come into play in order to determine what might be the best decision in a given scenario?
Michael: Simulations with respect to digital twins is the next step of an evolution of digital twins. First step is creating digital twin. Creating that representation of the physical world inside an application. Next, we use machine learning, or specifically, something called a reinforced learning model where we can simulate environmental changes in that digital twin. In the case of a warehouse, a warehouse operator today uses their own experience, their own tribal knowledge to know, “You know what? I can’t have more than three forklifts operating.”
It’s their intuition that says that. They don’t have the ability to simulate that in their mind yet. They just feel it out. Whereas with a digital twin, with a reinforced learning model, I can digitally deploy 1, 2, 3, 4, 5 forklifts in a virtual world and simulate traffic inside of a warehouse to really find how much congestion is too much congestion? How many people is too many people? How many forklifts are too many forklifts before my efficiencies in the warehouse degrade?
Figuring out. If I had two more people like Bob in the warehouse and I hired two more people, what would my environment look like? That’s where that simulation comes into play, is now customers, once they first get their digital twin, then they can use machine learning to play different scenarios that in the end, are expensive decisions. Hiring two people is expensive, moving racks. Buying a forklift is a big capital expenditure, can I use digital twins to simulate and figure out, “Is this going to add value to my organization?”
Josh: I think that’s such a good question of, “Is this going to add value to my organization?” You’re talking about this specific action, maybe it’s a project, an initiative, just that ability to leverage tons and tons of data, leverage these digital assets, and compute faster than we can using data as opposed to, like you said, feeling it out or any gut-based decision making, turn it into a data-backed projected impact that we’d be having. I’d love to hear a little bit more about this idea of impact. What kind of impact can an operation have by leveraging digital twin technology?
Michael: Creating the digital twin creates a little bit more transparency into the operations of that machine, that building, that space or that asset. If you have a million-square-foot warehouse, you cannot be in all places at all times and can’t see all the inefficiencies. We have a customer in Tennessee, a million square feet, aisles are one way and workers are working on their tasks and forklift is waiting on another forklift to clear an aisle. A million-square-feet, unless I see it with my own two eyes, I’m not going to find that issue. That issue occurs multiple times per day.
In the business of warehousing and logistics, it is a low-margin business and volume is king. We need to keep our activities very quick and efficient. Without a digital twin, unless I’m physically on a scooter riding around looking and finding all these traffic jams, I’m not going to see that. A digital twin enables us to play back history and enables us to analyze history and find those conditions where we can further optimize our operations.
A digital twin of a machine that it’s stamping out metal components, same thing. I put sensors on it because I may not be able to watch it 24 hours a day and it may have some inefficiencies in its operation. I use sensors or create a digital twin in that machine to find those inefficiencies, predict when maintenance needs to happen. Same thing for managing people in the warehouse. We can use digital twin to look at that history.
Josh: It sounds like there is a bit of a limitation on your ability, not you Michael, but in general, in operation’s ability to really, truly maximize all of the efficiency gains they could possibly have because they don’t have a tool like this in place. No matter what efforts you put in there in order to find out and discover some of these problems, you’re looking at time and resource costs where you have someone whose sole job is looking at all these different things that in an instance, this digital representation could bring to light.
Essentially, some of the things I’m hearing is if you truly want to optimize your operation or optimize the performance of your warehouse, you have to embrace tools like these because you are simply capped by just human inability at that point.
Michael: That’s right. In the logistics space there’s a term called slotting. Slotting is if I’ve got a million square feet, how do I determine what product to put in this space versus that space? Do I keep it low and close or to keep it high and far? Slotting is done today through tribal knowledge, it’s done in Excel, it’s done through human beings.
Human beings take vacation, human beings turn over, and so when that slotting expert at your warehouse leaves to join another company, that experience of determining what to store where goes with the person or maybe it’s stuck at an Excel spreadsheet. Using machine learning, we can store all the human decisions that have ever been made and then improve upon them and reduce the risk of resource turnover in the future so that when that person leaves, their knowledge doesn’t leave with them. Their knowledge actually becomes part of the machine learning model because the machine is learning from the slotting decisions that that human being made.
Josh: Then the rest of the operation for the future will be able to benefit from that, especially as the algorithm continues to evolve.
Michael: Yes, absolutely.
Josh: A really interesting point. I’m curious when we think about this idea of digital representations of assets and areas and buildings and whatever you want to call it. Are there assets or are there things that will never have a digital twin or anything like that or can anything have its own digital twin?
Michael: Just thinking big, thinking cross-industry, thinking of what can’t have a digital twin is tough. Because I’ve worked alongside the agricultural industry and the agricultural industry being able to create a digital twin of a field by, A, understanding water usage in the field by having sensors in the ground measuring pH and measuring water contained in the soil, by using computer vision to identify the health of a crop by analyzing images of the crop. That’s agriculture.
If we look at the space industry, everybody knows that every part of that rocket is measured and monitored and there’s a digital twin of a rocket and the car. In short, I think we can create a digital twin. Apple Home is a digital twin at your home. You can interact with that digital twin by turning off and on your alarm, your lights, change the color of your lights, turn on your oven, change your thermostat. You’re interacting with the digital twin of your home.
I have a teenage daughter, that’s probably the one thing I couldn’t create a digital twin of. [laughs] That’s something that I can’t understand or communicate with. That’s probably the one thing I couldn’t create a digital twin of. [chuckles]
Josh: That’s a fair point. Teens are their own special unique challenge. I have one myself and I’m sure learned similar lessons that you have on that topic.
Michael: Another podcast.
Josh: Yes, another podcast.
Michael: [laughs]
Josh: Tech and parenting, anyway.
Michael: There you go.
Josh: [laughs] How to take your learnings and run your home with it. Although the more I study continuous improvement and learn from people and guests on the show, I’m often like, “I could use this at home. I can optimize home operations.” Then my wife tells me I use too much work talk, and I’m like, “Yes, I guess so.”
Another question that comes to my mind, Michael, about digital twins, it’s great to be able to talk with an expert like yourself on this subject because we can get clarity on a lot of different points behind it. I, by no means am an expert, but I’ve heard a lot of different, and sometimes, conflicting concepts about digital twins. I’m curious from your perspective, what do people in the industry commonly get wrong about digital twin technology?
Michael: They commonly confuse digital twin with machine learning, with AI. A digital twin is a data source for AI, a digital twin is not AI. Machine learning takes a series of events or conditions that happened in the past and makes recommendations of what should happen in the future. An AI is taking in more variables than just a machine learning model and making decisions for you automatically as opposed to you selecting from a pre-selected list of recommendations.
Creating the digital twin does not mean that you are using artificial intelligence. Again, I don’t see it confused that often, but that’s one area of misconception that digital twin does put you on your path to AI. I would argue that AI needs the data from a digital twin, specifically in the manufacturing, logistics, warehousing ecosystem. I can’t have AI without having a digital representation because that digital representation is all the data elements I would need for an AI to make a decision for me.
Josh: AI and machine learning require a ton of different data. Then I think to the point that we talked about earlier, not only when setting up a digital twin do you need to create that digital representation but you need to, as the second step, create that reinforced learning model. That idea of being able to simulate, that’s where I see the power of digital twin, and realizing its full potential is being able to have an accurate AI because there’s a qualifier there.
Is the AI to the point that it needs to be yet? Being able to have, at such quick speeds, something that can run these simulations, generate these data points, present projected outcomes, and either put into motion or make the recommendation to people. That saves time, that saves brain power, that moves from these opinion-based and intuition-based, and even experience-based decisions to a more just data-backed approach to managing any aspect of your operation.
Michael: Yes. Let’s talk about automotive manufacturer. Inside of their inbound receiving area, they have 10 doors. When a driver shows up, with a 52-foot trailer, he pulls up, he gets out of his truck and he walks inside and says, “Hey, what door do you want me at?”
The gentleman or girl at the dock will say, “Yes, door nine, pull to door nine.” Then the driver leaves. There was that interaction that driver spent 30 minutes there. For that driver, they’re not getting paid unless they’re on the road, so their motivations are to get in and out. For the person inside of the warehouse, they want you to pull up to the right doors so they can send the right team at the right tools to get the stuff off the truck.
Now, imagine a world where we use ChatGPT, AI for text creation, copywriting, we use a solution like Fulfilld for digital twin and digitally understanding what doors are consumed and then knowing what tools and equipment are behind that door. Now when the driver pulls up to the gate, there’s a big sign says, Texas number to get your door assignment. Rather than a human being get involved, Fulfilld knows what door we want them to pull up.
We call ChatGPT to write a nice human readable text message that’s sent to that driver and that driver now says, “I get a pleasant message from somebody named Doris.” That might just be the AI. Doris is saying, “Hey, Harry, welcome to such and such automotive. Please back up to door nine. Look out for that trashcan on the left.” Something that looks and reads really well, like a human being wrote it, but it was 100% done by AI.
That person didn’t get out of their cab, they didn’t waste time walking into the door, and the dock worker didn’t have to stop what they were doing to go to the door to talk to the driver. That’s a scenario where digital twin and AI work together to streamline an interaction.
Josh: I think that’s a powerful example. It’s a fun one. I’m so glad you brought up ChatGPT. It’s the first time on the show that it’s been brought up. I think we all know that it will become, not just an essential part of our lives, but a ruling part of our lives, whether or not we know it. One thing I couldn’t help but think about within your example is we’ve got the warehouse as a digital twin.
Like we talked about before, there’s really not a whole lot that can’t have a digital representation with the right sensors in place, connectivity, communications to backend systems, et cetera. Thinking about that image of the truck pulling up, the sensors that are no doubt attached to that truck as part of logistics tracking system or management system that’s in place, being able to share that information with the vendors or the customers so that they know this is the truck to expect as soon as it like pulls up onto the campus onto the facilities.
Having that trigger everything automatically, so now it’s not even a need for texting. You’re three minutes away and you get the notification, “Pull up to number nine.”
Michael: Exactly. Door scheduling sounds so simple. It sounds so simple like, “Just go to door 10,” but it’s like when you stand in the coffee lane and then you look behind you now there’s 15 people behind you, but 10 minutes earlier there was nobody there. It’s just funny how in logistics when you have 10 doors, of course 11 trucks are going to show up at the same time. The doors are going to have empty all morning long but everybody’s going to show up at the same time and that’s where it becomes a hassle and it’s time-consuming and people lose efficiencies.
Josh: I’m sure that is something that technology can help solve at some point. When thinking about these futuristic concepts, these all sound amazing, but I have to mitigate that with my own experience in the tech industry. I’ve seen certain examples that claim to be things that, in reality, they’re lacking a little bit.
I can’t help but keep that in mind when discussing things like digital twin because you can compare that with some major buzzwords that get thrown about often, like digital transformation, industry 4.0, you brought that up earlier, smart factories, factories of the future, et cetera. These are all exciting concepts. I love exploring the potential of them, but we both have to acknowledge that even the most reputable information on these topics still gets to be very hypothetical.
There’s not as much of an implementation because no one has digitally transformed. Industry 4.0 is still in its infancy. It’s not necessarily new, but it’s still maturing as far as adoption go. Smart factories are by no means smart yet, factories of the future are still in the future, not in the present. I want to discuss, where does digital twin technology fall on this spectrum? What would you say is the hype versus the reality of what’s been implemented and accomplished?
Michael: I think that digital twin, if you look at, I think it’s Gartner that puts out that hype report that says what’s the [unintelligible 00:24:40]. [crosstalk]
Josh: Yes, the hype cycle.
Michael: The hype cycle. I think this is now beyond the hype cycle and it’s at implementation. Like I said, in the consumer world, we have the digital twin of our home in nest, our car in the BMW app, at work we are creating digital twin. Of course, I look at my competitors in this space, in the software logistics space. They’re doing it too, of course, I think I’m doing it better. It’s the next evolution of industry.
For me, digital twin is not science fiction. Having AR in the warehouse is still a little almost science fiction, but digital twin, I think, is implementable, it’s doable. There are many technologies out there to implement it with. I’m one of many. Customers, of course build, their own as well. The tools in the platform exist, the sensors exist.
I often say digital twin, I think, was thought of as a six-figure project. You’re not going to do it on the cheap. The answer is, it doesn’t need to be a six-figure project. Digital twins can be created within the logistics and manufacturing space very quickly and efficiently.
Josh: It’s mature enough to be implemented, for sure. From what you’re saying, there are certain components that have to come together, but it is doable, to what you said, and not even as expensive as you may think it is to actually get started and seeing some benefit from using digital twin. That makes me wonder about the adoption of the technology. It’s available, it’s usable, it doesn’t cost as much as you think. What have you seen as far as the state of adoption and implementation of digital twin technology?
Michael: Again, we all have our different perspectives in the different ecosystems that we work in. I don’t know the e-commerce fulfillment space. The Fulfilld by Amazons and those types of warehouses and the $10 million to $50 million revenue type warehouses, I don’t know that space and I don’t know the Shopify warehouse, so I can’t speak to that. What I can do is speak to what I am working in, which is large enterprise.
I mentioned automotive customer, Lucid Motors, big box retailers working in their warehouses, big CPGs working in their warehouses. Digital twin is in full adoption because large enterprise has seen it is more a line manager within the business can make a decision more quickly when seeing a digital representation of a business problem as opposed to seeing the green bar report and saying, “Oh, this is out of spec. We should have done five units per hour and the report says we did seven.”
When they’re looking at that tabular report in Excel, it’s difficult to pluck out the problems, but when looking at a digital twin and I see a red dot or a red light or a representation of objects backing up or a cue, a human being can look at that and make a decision very quickly and say, “That’s our problem area, that’s what I’m going to focus on.”
In large enterprise, in retail, in automotive, in manufacturing, digital twin implementation is well underway. I think that the warehouse is last. I think people immediately focused on digital twin of manufacturing equipment and machinery first. In fact, I worked on a digital twin project at Gates Corporation here in Colorado that won multiple awards. Would love to bring up that later. Manufacturing happened first and then, I think, warehouses is trailing and following along.
Josh: Is there a difference, or maybe I should ask, what are the differences between what it looks like for implementing on the manufacturing side versus the warehouse side? Or are there any differences?
Michael: I think people’s minds need to be opened up a little bit that the warehouse itself can be digitally represented. I think a lot of times people think digital twin manufacturing, they think of a pressing machine or some robotics or a paint booth, or something in the manufacturing floor where I can see I have a sensor here and a sensor there, and I have a PLC that controls it. They think of that as digital twin of that machine. Slowly through education, through information, people are now realizing a building can be a digital twin.
Josh: I agree that it needs to be a holistic approach to it. It’s just like when we talk about implementing lean as a methodology, that has to be a complete company approach, not just a specific department or a specific component of the operation because it does you no good if you’re lean in some areas and not lean in another. Same thing with a digital twin. You’re going to making bigger impact by having this connected experience, this consistent connected experience throughout.
Now, I wonder, there’s a lot of data that’s being generated by machines. Parts that are being produced, components that are being produced, some of the automatic quality detectors based off certain specs can identify what’s happening. If a machine stops for any reason, that gets logged as a data point. I would imagine these are all very fruitful data points for a digital twin technology to aggregate and to have, because it’s again, accurately representing what’s happening in the day-to-day.
What about, you mentioned your daughter earlier, not being able to turn her into a digital twin, but what about people in general, because that is a big component of operations today is what people are doing. What are your thoughts on not necessarily digital twins of people, but the type of data needed on the human aspect of the operation to truly paint the appropriate picture of what’s happening in the operation?
Michael: Great question. We started our organization thinking about having an individual carry or wear a tag. I knew where they were all the time. As they were scanning, I knew where the product was all the time. We slowly got rid of tracking of a human being. Because we can get enough the data we need to optimize the warehouse purely by understanding when was that task sent to the warehouse? Who started the task and capturing the data element, the timestamps in short, around when did it hit the handle? When did I start it? How long did it take me and when was it completed?
At the end of the day, a warehouse operator or a company, they’re looking at do I have enough people in the warehouse to fulfill the requirements of the warehouse? When I say fulfill the requirements of the warehouse, that could be supplying the manufacturing side of the business with the raw materials and the components needed to make things. Can I fulfill my responsibilities in the warehouse around fulfillment of orders and shipping, either B2B or B2C? What is the right number of warehouse workers, warehouse people I need at any given time to fulfill all of those responsibilities?
The people, and the resource planning side of the warehouse today is tribal knowledge based. It is typically not based on a number. I feel like I need nine people at all times. One person will call in sick and I need eight people to operate the warehouse. If we use machine learning and digital twin, the digital twin knows the distance between all bins in the warehouse, the shipping dock, the manufacturing for the receiving dock. We know all distances, we generally know how fast a human being can walk. We know how fast a forklift is.
Now it’s a math problem that we can solve. Lots of people can solve a math problem that says, “If I have all of these tasks, the order fulfillment, the replenishment to manufacturing, the finished goods for manufacturing into the warehouse, I can now calculate exactly how many people I need.” I can move levers to say if I want it more things done more quickly, if I add two people what does that peak velocity or goods, movement velocity look like? If I take away two people, what does it look like?
Now, I have a data backed decision that I’m making inside of my organization rather than, “You know what, it’s the holiday season, there’s always people calling in sick, getting sick, cold and flu. I’m going to have 15 people knowing that based on my history, I know I need that much.”
We’re looking to use the digital twin data to make a fact-based decision around this is what the appropriate time to complete these tasks should be. Based on the number of people that I’m planning for, I should be able to complete my day in X efficiencies with the measurable efficiency.
Josh: That makes sense. The reason I ask is because one of the biggest variables in an operation is the people. Like you said, someone may not be there that day or that idea of tribal knowledge, that expertise, that’s certainly a pain point that we see a lot of manufacturers that we work with your Parsable is how do we make sure that people are pulling from the same source of knowledge and that they have access to this expertise that has been developed over decades in some cases. Because that all leads to variables in the actions that people take, which then have an impact on the operations as a whole.
That’s what got me thinking about this idea of, is it enough to have a digital twin, a digital representation of an asset or of an area? Or do we need to think about digital twins from the entire operations perspectives? A little bit to your point before, it’s not just the warehouse, it’s everything that comes together to make this product at this spec and get it out the door the right way, the right time, so the customer gets it right when they need it. What are your thoughts on that idea of should the focus be a digital representation of an asset or a digital representation of the operations?
Michael: It should be the latter, right? Digital representation of the operations. We were actually internally we were talking about changing our perspective. Because right now our perspective of when building our application has been of the warehouse worker and what do they need to do their job for the day. We tried to have a brainstorming session yesterday of, let’s take the perspective of I’m the product and I want to get out the door. What are my paths to get out the door?
What are the bottlenecks to me getting out the door and trying to using digital twin represent that I have these products on this shelf that need to get to door eight to be on the FedEx truck at nine? What are the impediments to that product being able to get out the door? It’s a little bit of a change in focus, but it aligns to what you talked about. The digital twin and a representation of the operations, like the orchestration of everybody and everything that needs to happen in order to get that product off the shelf and to door nine before 4:00 PM and FedEx shows up.
Josh: I love that idea that reframing of the perspective of the products because as soon as you said it, I had the life of a product flash through my head. This product that’s like, “I want to fulfill my purpose. I want to satisfy the customer. I want to be there and make sure that they’re able to use me for what I’ve been built for.”
I love flipping that switch of thinking about it, what’s everything that’s getting in that product’s way of getting to that person who showed up at the store, who’s walking to the aisle that they go to every few weeks to pick up the product, who’s going there. How can you make sure that that item is hanging from the little hook on in the retail store? I don’t know what the hook is called, but just hanging there. I love that.
Michael: I can’t take credit from that idea. That was my product owner Rick Fisher. I thought he was half crazy when he told me. I was like, “Wait a minute. What?”
Josh: That’s a great idea. I’m going to reach out to Rick. Maybe we can have a comic book series on this.
Michael: Basically, you using a digital twin to show the bottlenecks, the things that are preventing, is there anything preventing that product from getting there other than a human being going to it? I say human being, it could be a robot. We partner with automated forklift company where much like in the military, you have a drone pilot that’s sitting in a booth and he or she might be piloting two or three drones for automated forklifts. It’s the same scenario.
I have eight automated forklifts in the warehouse and I have a single operator sitting in an office. It’s only on the joystick when that forklift has an obstacle that it can’t figure out. In our platform, again, the Roomba creates the digital twin as a vacuum in your home. These automated forklifts, again, are part of that digital twin in your warehouse so that they can go out and receive move pallets around very safely and efficiently without a human being really be involved. They can be attached to it when necessary for exceptions.
Josh: I love this concept of digital twin. I think it’s something that is inevitable within the future scenario. That plus like the power of machine learning and AI plus the power of being able to automate and leverage robotics where appropriate. Having that ability to really take in all these data points, feed it to an individual who can make the best decision and put that decision in motion. Then over time, if we’re being honest, that’s going to continue to learn and eventually put things into motion on its own at that point.
I think that’s such an interesting concept, very futuristic. I can’t help but think of this movie I, Robot with Will Smith, where there’s this central artificial intelligence that’s controlling all the robots that are pervasive. I don’t expect the robot uprising to actually happen, but that’s the imagery that it starts to invoke in this guy’s mind. Each warehouse is unique and so we do believe that machine learning to make recommendations in the beginning, and then in two to five years, AI will essentially make decisions in collaboration with the human being.
In that, we at Fulfilld when our machine learning model makes a recommendation we track when you accepted our recommendation and when you didn’t, so that we’re laying the foundation for when AI will now make decisions like Frank did or like Fally did. When they’re approving those recommendations over and over let’s not ask for their approval anymore. They always approve those let AI decide and make decisions like that person would.
Josh: Now, when we get into topics like this where we talk about the ability to automatically make decisions looking far enough into the future having the technology put into motion action, having robots pick up the forklifts, drive outs wherever they need to go, things getting where they need to go without people taking that action, that starts to invoke fears of getting rid of people replacing or eliminating jobs at that point.
Michael, in your experience with digital twin technology, is this something that is going to eliminate jobs or is it going to open up jobs? Talk to us about what do you expect and what you’ve seen there?
Michael: I think it’s going to move the workforce in a different area, and those resources will be further optimized. We know today that unemployment’s at the lowest it’s ever been. We know that warehouse worker turnover is anywhere between 40% and 60% a year on average in the industry across the entire country. There are pockets where people stay at work for a very long time, but in general there’s a lot of resource turnover in the warehouse.
Automating some of the lower-end tasks is beneficial in that the human beings are able to focus on a higher level of thinking and problem-solving. Boston Dynamics has a warehouse robot, I believe it’s called Handle. This robot can unload a truck now on its own, unload the truck, meaning take boxes and put them on a conveyor belt, and then the conveyor belt takes them out of the truck.
When we think about Phoenix in August, what’s human being wants to be in a container truck when it’s 120 degrees outside unloading boxes, it’s basically a sauna. We can send Handle in there. It’s a little bit safer work environment. They’re not going to throw their back out. The human being can focus on the more important tasks of keeping inventory up to date, following up on urgent orders, fulfilling orders and helping the operations continue to flow very efficiently.
I don’t see it as a method of reducing the labor force. I think it is a means of optimizing the labor force and improving the quality of life of employees in the Warehouse.
Josh: I appreciate you sharing that. I think it’s always important whenever we’re talking about technology and the future of the technology to always bring it back to it’s there to serve the people. I really appreciate what you’ve laid out and that really matches a lot of what I’ve heard, which is the expectation that automation’s not necessarily eliminating your opportunity to work. It may in the need for certain positions, but those positions are typically unfilled at this point.
Like you said we’ve got extremely low unemployment although the tech industry is really taking a hit right now in that case. Regardless, like you said, it’s optimizing for a better working experience and a better ultimately living experience for the people as opposed to getting rid of people.
Michael: Yes, absolutely. In fact, there are different liberal laws in different countries. Our data around employee performance, we actually change the way the data shape is inside of France and Germany where we cannot report an individual performance at the task level inside of a warehouse. We actually abstract that. We don’t know that we aggregate the team’s performance and then we show average performance across a group of employees. For specific for the EU, specifically for France and Germany, we don’t highlight that Michael is the slowest picker and Rick is the fastest, we aggregate and anonymize.
Josh: I think that’s such an important concept that anonymizing understanding really the factors that lead to one person being a high performer versus a low performer. Because ultimately you want to create a standardized approach. Maybe it’s a training thing, an expertise thing, maybe it’s a process-related thing. There’s so many different variables that we don’t think about, or maybe we do, but we don’t have the data on to really make a data-back decision on how to fix it.
I think that’s a whole episode in itself in talking about that topic. It’s been a really interesting conversation so far, talking about what a digital twin is, what the state of the implementation of digital twin technology is. I’d love for us to talk about getting started with digital twin technology.
Now, I know this will take more than just a vision of the future, the vision that I keep talking about, but there are probably a lot of factors that have to be explored when trying to create this virtual representation of these assets and the operation. I’d love to hear from you, Michael, what are the technical requirements for implementing digital twin technology?
Michael: Digital twin for us within the warehouse and manufacturing sites it all starts with the CAD drawing. Before that, really what we like to do is take people in that environment, in that space, in that operation, and ask them what are the decisions that you make hourly, daily, monthly? What are the decisions that you make based on seeing something with your own two eyes?
Meaning I see that these shelves are full so I’m going to start queuing product to go to the secondary warehouse. That’s a decision a human being make based on them standing there and them seeing a shelf. What if I could digitally represent the shelf, know in advance when that shelf is going to be full? Because I understand product dimension and I understand shelf space. Instead of that product hitting the dock and then having it removed again, could I just have it delivered directly to the second warehouse by implementing a digital twin?
Focus on the decisions that are being made at an operational level, and then build a digital twin to answer those questions ahead of time or to support the decision-making being made by human beings in those environments.
Josh: Is there such thing as digital twin in a box where you can order something and attach some sensors to things, post some cameras up? I think you and I have talked about previously indoor positioning technology as well. Talk to us about some of the technical components that you may need to have when exploring this.
Michael: From a technology perspective, digital twin can mean lots things. Creating the visual representation is the first place. Having a technical drawing that you convert into adjacent object. At the San Francisco 49ers stadium, we had a whole drawing of the stadium that we converted into an object that could be represented digitally and that could be used a technology called D3, GeoJSON is another technology for visualizing things. There’s ways to visualize things in JSON and Python.
A front-end developer if you’re getting started that understands how to represent drawings in a digital way, it put me an analytics developer. A TAP low has a capability to do that. Power BI has a capability to do that. In my world, it was a React developer and a Python developer got together and they were able to take a CAD drawing and create adjacent object that we would put them in the app. That talks about people involved technically.
The other thing is just you need the data. In my case, my data comes from advanced shipment notifications, or EDI, my data comes from an ERP system, purchase orders, sales orders. What am I buying and bringing in? What am I selling and shipping out? My product master, what products do I have in the warehouse? Then that CAD drawing of the warehouse which shows not only my four walls of my building but my racks. Then I need the data around my racks. This is a 48-inch shelf, it’s 32 inches deep and it’s 48 inches high. I need those data elements.
When I stitch the map and the drawing and the metadata around product and purchase orders and sales orders altogether, I’m now at that stage work from the warehouse. I’ve created the digital twin of the warehouse.
Josh: We talked about some tactical items there of what it takes to implement the technology. Whenever I talk with leaders in manufacturing in some consultants as well a common theme with implementing new technologies is around this idea of not just piloting something. You should pilot something, but oftentimes the pilot is the end of the project and it never quite makes it outside of that pilot is that idea of pilot purgatory. The common advice is building your plan to scale.
Whatever you do in the pilot, how is it going to lead up into a full enterprise deployment? I’m curious we just talked about some of the tactical items. What strategic factors need to be considered for implementing digital twin technology?
Michael: From a strategic, in our minds, it’s assisting and enabling the line-level managers, the operational folks. You have to have their support or you have to be solving a problem for them. Creating a dashboard, putting it in the warehouse, and having it sit there and flash yellow and red lights as to the production status. That doesn’t help a line manager decide where to focus his or her energy to solve that problem.
For us from a strategy perspective, during a pilot is when we’re doing road shows to those line level operational level workers and getting buy-in or getting input from them on the decisions that you make day-to-day, how could we support those? How could we visually represent that to make your decision making even easier so that you can quickly identify the problem and solve it as opposed to you finding the problems?
Josh: This is an interesting point because I have to admit when we were discussing digital twin tech earlier on, the visions that I kept having were really, I guess would be more of managerial and above level as far as receiving an impact from it. You’re saying, there’s something in it for everyone on the digital twin side.
Michael: Yes. For the warehouse worker with regard to digital twin and machines recommending where to store a product, a lot of organizations we go to, its employee determines where to put it. Their knowledge over the next weeks, months, years, they know that, “You know what? This product’s probably going to get used next week, I’m going to keep it close. This product, we don’t sell a lot of this, so I’m going to keep it in the back.”
If you’re a brand-new employee and you put away something that you need tomorrow far away, you’re like, “Ah, that was stupid. Why did I do that?” Now, machine learning slotting, and when that employee scans that product, we recommend, keep this close, and then giving them a reason. You have this order tomorrow for it. I’ve made it their job better. I’ve made their work environment better through that digital twin, understanding physical space, understanding what’s coming tomorrow, and informing them in their decision-making or making recommendation that they can accept or not accept. That’s at the lowest level of the warehouse worker.
Josh: Which is such a point that we can’t hit on enough is that really like all of these problems that we’re talking about solving or these opportunities for improvement, this is all focused on the frontline, with everything that we’ve discussed. The product, going through its own story and reaching those bottlenecks that prevent it from getting out to the customer, that’s happening on the frontline.
You just mentioned these decisions that are made by people with experience, that’s happening on the frontline. Of course, the frontline workers must be actively part of the conversation for really not just digital twin technology, but any type of technology. We certainly see that a lot here at Parsable with our connected worker technology. That is also built four frontline workers and there’s impact up the chain there.
That brings another question to my mind, Michael, which is, who needs to be involved with an implementation like this? We mentioned frontline workers, but who typically gets involved in identifying digital twin technology, implementing it, getting it set up and getting it used?
Michael: For us right now, it’s typically the operational teams that are looking for ways to improve operations, improve visibility in the operations, improve the lives of the employees on the shop floor. Right now, this is where I love to be, I used to be in an area where I was majority working on IT-driven projects. I’m very happy today to be in Fulfilld, and working with operationally led projects where an operational leader says, “I need better visibility in my warehouse operations, and I need to give my line level resources decision-making capability or better decision-making capability.”
For us, it’s the operational team members. It’s the manager of a warehouse, the VP of supply chain, the warehouse supervisors wanting something different from their ERP or wanting something different from their WMS.
Josh: I love that you broke it down that there’s something in it for everyone, and even got specific as to who you typically work with. Because that ultimately indicates who’s seen a lot of the direct value, is those people that you’re talking with. Michael, I feel like I have learned a lot in our conversation today. I’m sure if anyone sees the video of this podcast, they’ll notice moments where I’m just stupified in understanding some of the things that you brought up.
I took a lot of notes. I wrote down that idea of the perspective of the product. That one just about blew my mind because it was such a different way of thinking about it. I loved it. I certainly appreciate you joining us and not only taking the audience through digital twin technology, but educating me and reframing some concepts within my own mind. As we wrap up, I would love to hear from you, how can Fulfilld help our listeners with digital twin technology in their warehouse operations?
Michael: Fulfilld is a cloud-based WMS. We are a warehouse management, inventory management platform, and we take warehouse-specific drawings and create a digital twin of your space. The premise is, is we want to create that citizen warehouse worker. Anybody should go and walk into that warehouse and be effective day one and not require the weeks and months of job shadowing to be effective. That’s how we help.
We are assistive, additive to ERP systems. We sit on top working in coordination and cooperation with, and our goal is to enlighten and delight that warehouse worker so that they feel good throughout their day. When a warehouse worker goes to the same area five times, they know in their mind like, “Wow, I’ve been here six times today. I wish I could have just done this task once.”
In addition to improving operations in the warehouse, we believe that we improve the warehouse workers day. Happy to share more with the listeners. That’s fulfilld.io. F-U-L-F-I-L-L-D.io is our website. We’ll be at ProMat this year as well, the logistics conference at the end of March. Excited to meet and talk to more people.
Josh: Now, you just dropped another one on me that made my mind blow for a second, which was enlight and delight. I love that. I love that it rhymes and I love the overall message and the concept behind it. Yet another one in this episode, Michael. I appreciate you calling out how our listeners can find out more about Fulfilld. If they want to connect with you or continue the conversation with you, what’s the best way to reach you?
Michael: LinkedIn, social media for business. LinkedIn/Michaelpytel. All one word. M-I-C-H-A-E-L-P-Y-T-E-L. LinkedIn, Michaelpytel, or drop me an email. michael@fulfilld.io.
Josh: Awesome. Michael, thank you so much.
Michael: Thank you so much, Josh. Wonderful discussion today.
Josh: Big thanks to Michael for joining Conquering Chaos, and educating our fellow conquerors of chaos. Digital twins are exciting and inevitably essential, but it’s still decently early in its maturity as well as adoption. That means that many solutions will fall short of expectations because they’re still being built and imagined to some degree. However, it’s better to be ahead of the curve than behind it. Digital twins require connectivity for seamless bidirectional data flow, thousands or even millions of data points and more.
Listen to find out the basics on Digital Twin technology and the impact manufacturers can have with this exciting emerging solution!